Surge Tank Maintenance: Optimal Performance Guide
A surge tank, crucial in hydroelectric power plants for mitigating water hammer effects, demands meticulous maintenance to ensure operational longevity and efficiency. The American Society of Civil Engineers (ASCE) provides comprehensive guidelines on surge tank design and inspection protocols, essential for engineers involved in hydropower projects. Regular inspection using non-destructive testing (NDT) methods helps identify potential issues like corrosion and structural weaknesses, which, if left unattended, could lead to catastrophic failures similar to those studied in case studies by Professor John Doe, a leading expert in hydraulic engineering. Implementing a robust maintenance schedule, informed by regulatory standards and advanced diagnostic tools, is vital for preserving the integrity of the surge tank and the overall stability of the hydraulic system.
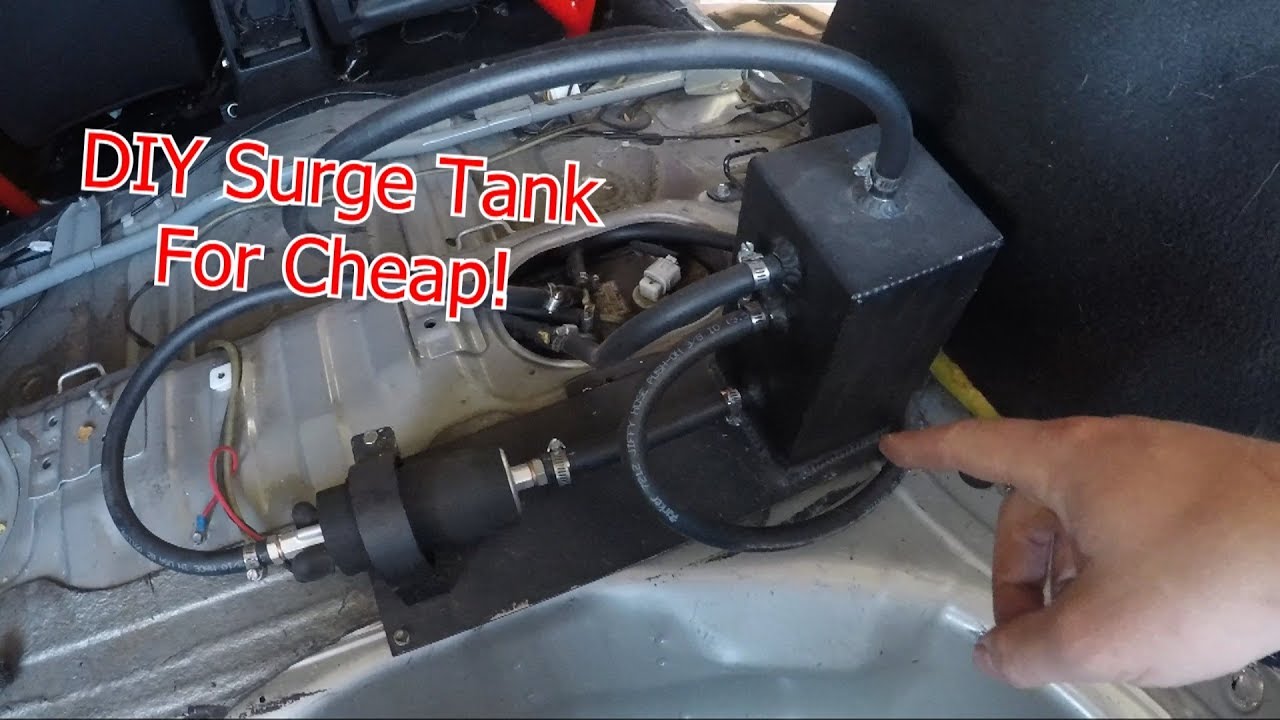
Image taken from the YouTube channel Bang 4 Buck Racing , from the video titled This DIY Surge Tank is CHEAP and Easy to make! .
Surge tanks are critical components in various fluid conveyance systems, acting as protective measures against the detrimental effects of pressure surges, also known as hydraulic transients. These surges, often resulting from sudden changes in flow velocity, can inflict significant damage to pipelines and associated equipment. By providing a buffer volume, surge tanks effectively dampen these pressure fluctuations, ensuring system integrity and operational reliability.
The Role of Surge Tanks in Pressure Mitigation
The primary function of a surge tank is to mitigate the impact of pressure surges within a closed conduit system. They serve as temporary storage for fluid during surge events, either absorbing excess pressure or supplying fluid to compensate for pressure drops. This controlled response prevents rapid pressure variations that can lead to pipeline rupture, valve failure, or pump cavitation.
Industries Reliant on Surge Tank Technology
A wide range of industries rely on surge tank systems to safeguard their fluid transport infrastructure. Some prominent examples include:
-
Hydroelectric power generation: Where surge tanks protect penstocks and turbines from water hammer effects.
-
Water distribution networks: Maintaining stable pressure and preventing pipeline bursts.
-
Oil and gas pipelines: Mitigating pressure fluctuations caused by pump operations and valve closures.
-
Wastewater treatment plants: Ensuring the smooth and continuous operation of pumping systems.
These applications highlight the versatility and essential role of surge tanks in maintaining the efficiency and safety of diverse industrial processes.
Consequences of Neglecting Surge Protection
The absence of surge tanks in vulnerable systems can lead to severe and costly consequences. Uncontrolled pressure surges can cause:
-
Pipeline rupture: Leading to fluid loss, environmental contamination, and costly repairs.
-
Equipment failure: Damaging pumps, valves, and other critical components.
-
Operational downtime: Disrupting production and impacting overall efficiency.
-
Safety hazards: Posing risks to personnel and the surrounding environment.
Therefore, implementing surge protection measures, particularly the use of appropriately sized and designed surge tanks, is paramount for ensuring the long-term reliability and safety of fluid conveyance systems.
Fundamentals of Surge Tank Operation: How They Work
Surge tanks are critical components in various fluid conveyance systems, acting as protective measures against the detrimental effects of pressure surges, also known as hydraulic transients. These surges, often resulting from sudden changes in flow velocity, can inflict significant damage to pipelines and associated equipment. By providing a buffer, surge tanks mitigate these risks and ensure stable system operation.
Fluid Dynamics and Surge Tank Function
The operation of a surge tank hinges on fundamental principles of fluid dynamics. These principles dictate how fluids behave under pressure and in motion.
Understanding these laws is essential for comprehending the surge tank's role in mitigating pressure fluctuations.
The Role of Bernoulli's Principle
Bernoulli's principle, a cornerstone of fluid dynamics, describes the relationship between fluid velocity, pressure, and elevation.
It states that an increase in the speed of a fluid occurs simultaneously with a decrease in pressure or a decrease in the fluid's potential energy.
In surge tank systems, this principle elucidates how changes in flow velocity directly impact pressure within the pipeline.
Conservation of Mass and Fluid Behavior
The law of conservation of mass is also vital. This law dictates that mass cannot be created or destroyed in a closed system.
Therefore, any changes in fluid flow rate within a pipeline must be accounted for.
A surge tank accommodates these changes by either storing excess fluid or releasing fluid to compensate for deficiencies, thereby stabilizing pressure.
The Impact of Fluid Inertia
Fluid inertia, the tendency of a fluid to resist changes in its state of motion, plays a significant role in the generation of pressure surges.
When a fluid in motion is suddenly stopped or accelerated, its inertia causes it to exert considerable force on the surrounding pipeline.
This inertial force manifests as a pressure wave, which can propagate through the system, potentially causing damage.
Understanding Hydraulic Transients and Water Hammer
Hydraulic transients, often referred to as water hammer, are pressure surges that occur in liquid-filled pipelines due to sudden changes in flow velocity.
These transients can be destructive and understanding their causes and characteristics is critical for effective mitigation.
Defining Hydraulic Transients and Water Hammer
Hydraulic transients encompass a range of pressure fluctuations that deviate from the steady-state operating conditions of a pipeline.
Water hammer, a specific type of hydraulic transient, is characterized by a distinct knocking sound. This sound is caused by the rapid pressure waves bouncing within the pipeline.
Causes of Pressure Surges
Pressure surges can arise from a variety of events. Sudden valve closures are one of the most common culprits.
Other potential causes include pump starts and stops, rapid changes in demand, and even the collapse of vapor pockets within the fluid.
Each of these events can induce a rapid change in flow velocity, triggering a pressure surge.
Characteristics and Propagation of Pressure Waves
Pressure waves generated by hydraulic transients exhibit specific characteristics.
These waves propagate through the pipeline at a characteristic speed, which depends on the fluid properties and the pipe material.
The magnitude of the pressure surge is determined by the magnitude of the velocity change and the wave speed. Understanding these characteristics is vital for designing effective surge mitigation strategies.
Pressure Regulation Through Surge Tanks
Surge tanks play a pivotal role in maintaining stable pressure within a fluid conveyance system.
By providing a reservoir for fluid, they effectively dampen pressure fluctuations and prevent extreme pressure spikes.
Stabilizing System Pressure
The primary function of a surge tank is to absorb or supply fluid as needed. This balances the system and keeps the pressure stable.
When a pressure surge occurs, the tank absorbs excess fluid, preventing the pressure from exceeding acceptable limits. Conversely, when the pressure drops, the tank releases fluid, compensating for the deficiency.
Volume and Effectiveness
The effectiveness of a surge tank in regulating pressure is directly related to its volume.
A larger surge tank can accommodate larger pressure surges and maintain a more stable pressure profile.
The optimal surge tank volume is determined through hydraulic analysis, considering factors such as pipeline characteristics, flow rates, and potential surge events.
Cavitation: A Threat to System Integrity
Cavitation, the formation and subsequent collapse of vapor bubbles in a liquid, poses a significant threat to the integrity of surge tank systems.
Understanding this phenomenon is crucial for preventing damage and ensuring reliable operation.
Defining Cavitation and Its Causes
Cavitation occurs when the local pressure within a liquid drops below its vapor pressure. This causes the liquid to vaporize and form bubbles.
These bubbles are then carried to regions of higher pressure where they collapse violently. This creates intense microjets and shockwaves.
The Damaging Effects of Cavitation
The collapse of cavitation bubbles near solid surfaces can cause significant erosion and pitting. This is due to the intense microjets and shockwaves.
This erosion can weaken pipeline components and reduce their lifespan.
Additionally, cavitation generates noise and vibrations, which can be indicative of a problem within the system.
Head Loss and Surge Tank Performance
Head loss, the reduction in total head (pressure) of a fluid as it moves through a system, can significantly impact the performance of surge tanks.
Minimizing head loss is essential for maximizing the effectiveness of surge mitigation measures.
Understanding Head Loss
Head loss occurs due to friction between the fluid and the pipe walls. This also includes energy losses due to turbulence caused by pipe fittings and other obstructions.
This loss of energy translates to a reduction in pressure, which can affect the ability of the surge tank to effectively dampen pressure surges.
Factors Contributing to Head Loss
Several factors contribute to head loss in surge tank systems. Friction between the fluid and the pipe walls is a primary contributor, with rougher pipe surfaces resulting in greater head loss.
Pipe fittings, such as bends, elbows, and valves, also induce turbulence and increase head loss.
Careful design and selection of pipe materials and fittings can help minimize head loss and optimize surge tank performance.
Surge Tank Equipment and Components: A Detailed Overview
Following a fundamental grasp of surge tank operation, understanding the equipment and components that comprise these systems is paramount. A comprehensive knowledge of the various surge tank types, along with their individual strengths and limitations, is critical for optimal selection and deployment. Beyond the tanks themselves, an array of supporting components contribute to the overall effectiveness of surge mitigation.
Types of Surge Tanks
The configuration of a surge tank significantly influences its performance characteristics and suitability for specific applications. From open to closed designs, each type offers unique advantages and disadvantages.
Open Surge Tank
Open surge tanks represent the simplest configuration, directly exposed to atmospheric pressure. This direct exposure allows for uninhibited water level fluctuation within the tank, effectively absorbing pressure surges.
The primary advantage of open surge tanks lies in their simplicity and ease of construction. However, their open nature also renders them susceptible to contamination and makes them unsuitable for applications where fluid purity is paramount. Furthermore, they are limited to systems where the hydraulic grade line allows for atmospheric exposure.
Closed Surge Tank (Pressurized)
Closed, or pressurized, surge tanks address the limitations of open designs by isolating the fluid from the atmosphere. These tanks incorporate a compressed gas, typically air or nitrogen, to provide a compressible cushion that absorbs pressure fluctuations.
The key advantage of closed surge tanks is their ability to operate in systems where atmospheric exposure is undesirable or impossible. They are particularly well-suited for applications involving potable water or corrosive fluids. However, they require more sophisticated control systems to maintain proper gas pressure and may be more expensive to construct than open surge tanks.
Air Vessel
Air vessels represent a specific type of closed surge tank, relying on compressed air to mitigate pressure surges. These vessels are commonly employed in pumping systems and pipelines to dampen pressure oscillations caused by pump start-up, shut-down, or valve closures.
The effectiveness of an air vessel depends on maintaining the correct air volume and pressure. Regular monitoring and adjustment are essential to ensure optimal performance and prevent the air from being absorbed into the fluid.
Standpipe Surge Tank
Standpipe surge tanks are characterized by their simple, vertical design. They consist of a vertical pipe connected to the main pipeline, providing a free water surface for surge wave reflection and attenuation.
These tanks are typically used in low-head hydropower systems and water distribution networks where space is limited and a simple, cost-effective solution is required. However, their surge mitigation capacity is limited by the height of the standpipe.
One-Way Surge Tank
One-way surge tanks are designed to permit flow in only one direction, typically towards the tank. This unidirectional flow characteristic makes them suitable for applications where pressure surges are predominantly caused by a specific event, such as a sudden valve closure.
Their key advantage lies in their ability to quickly absorb pressure surges without allowing reverse flow that could exacerbate the problem. However, they are less effective in mitigating surges caused by multiple or bidirectional flow events.
Essential System Components
Beyond the surge tank itself, a variety of supporting components play crucial roles in the overall effectiveness of surge mitigation.
Pumps
Pump characteristics significantly influence surge events. Rapid pump start-up or shut-down can generate substantial pressure surges. Mitigation strategies often involve controlled pump operation, such as slow-start mechanisms or variable-speed drives.
Pipes/Pipelines
The material and configuration of pipes influence surge propagation and attenuation. Flexible pipe materials tend to dampen surges more effectively than rigid materials. Pipeline design should minimize abrupt changes in diameter or direction, which can amplify pressure waves.
Valves
Valve operation is a primary source of pressure surges. Rapid valve closures can generate significant water hammer effects. Slow-closing valves or surge relief valves are often employed to mitigate these surges. The selection and operation of valves must be carefully considered to minimize surge potential.
Pressure Sensors/Transducers
Accurate pressure measurement is essential for surge tank control and monitoring. Pressure sensors and transducers provide real-time data on system pressure, enabling control systems to respond effectively to surge events.
Level Sensors
Level sensors monitor and control the fluid level within the surge tank. Maintaining the correct water level is critical for optimal surge mitigation. Level sensors provide feedback to control systems, which adjust inflow or outflow to maintain the desired water level.
Flow Meters
Flow meters provide data on fluid flow rates, which can be used to predict and manage surge events. By monitoring flow patterns, control systems can anticipate potential surges and take proactive measures to mitigate their impact.
Operational Challenges and Mitigation Strategies: Keeping Things Running Smoothly
Following an understanding of surge tank equipment, a critical examination of the operational challenges and mitigation strategies is essential to ensuring the long-term reliability and effectiveness of these systems. Surge tanks, while designed to protect against hydraulic transients, are themselves susceptible to a range of operational issues that can compromise their functionality. Addressing these challenges proactively is vital for maintaining system integrity and preventing costly failures.
Corrosion: A Persistent Threat
Corrosion represents a significant threat to the structural integrity of surge tanks. Understanding the mechanisms by which corrosion occurs is the first step in implementing effective mitigation strategies.
Mechanisms of Corrosion
Several corrosion mechanisms can affect surge tanks, including:
-
Uniform Corrosion: This is a widespread form of corrosion that affects the entire surface of the tank.
-
Pitting Corrosion: This localized corrosion results in the formation of small pits or holes.
-
Galvanic Corrosion: This occurs when dissimilar metals are in contact in the presence of an electrolyte.
-
Stress Corrosion Cracking (SCC): This occurs when a material is subjected to both tensile stress and a corrosive environment.
The specific corrosion mechanism depends on factors such as the materials of construction, the composition of the fluid within the tank, and the operating conditions.
Corrosion Monitoring
Effective corrosion monitoring is essential for detecting and addressing corrosion before it leads to significant damage.
Various techniques are available for corrosion monitoring, including:
-
Visual Inspection: A simple but effective method for detecting surface corrosion.
-
Ultrasonic Testing (UT): Used to measure the thickness of the tank walls and detect internal corrosion.
-
Radiographic Testing (RT): Used to detect internal flaws and corrosion.
-
Electrochemical Techniques: Used to monitor the corrosion rate of the tank material.
Data obtained from corrosion monitoring can be used to predict the remaining service life of the tank and to optimize corrosion mitigation strategies.
Protective Coating Systems
Protective coatings are widely used to prevent corrosion in surge tanks. A variety of coating systems are available, each with its own advantages and disadvantages. Common coating systems include:
-
Epoxy Coatings: These offer excellent resistance to chemicals and abrasion.
-
Polyurethane Coatings: These provide good flexibility and resistance to weathering.
-
Zinc-Rich Coatings: These provide cathodic protection to the steel substrate.
The selection of the appropriate coating system depends on factors such as the operating environment, the type of fluid in the tank, and the desired service life. Proper surface preparation is critical for the successful application of any coating system.
Cathodic Protection
Cathodic protection (CP) is an electrochemical technique used to prevent corrosion by making the steel structure the cathode of an electrochemical cell. Two main types of CP are used:
-
Sacrificial Anode CP: Sacrificial anodes, typically made of zinc or magnesium, are connected to the steel structure. The anodes corrode sacrificially, protecting the steel.
-
Impressed Current CP: An external power source is used to drive current through the electrolyte to the steel structure.
CP can be used in conjunction with protective coatings to provide enhanced corrosion protection.
Erosion: Damage from Fluid Flow
Erosion, caused by the abrasive action of fluid flow, can also damage surge tank components. High fluid velocities, especially when combined with entrained solids, can lead to significant material loss.
Causes and Impact of Erosion
Erosion can be caused by:
-
High Flow Velocities: Increased flow rates lead to greater shear stresses on the tank walls.
-
Entrained Solids: Suspended particles in the fluid can act as abrasives.
-
Cavitation: The formation and collapse of vapor bubbles can cause erosion.
Erosion can lead to thinning of the tank walls, leakage, and ultimately, structural failure.
Minimizing Erosion
Several methods can be used to prevent or minimize erosion:
-
Flow Optimization: Design the tank and piping system to minimize flow velocities and turbulence.
-
Material Selection: Choose erosion-resistant materials for critical components.
-
Protective Linings: Apply erosion-resistant linings to the tank walls.
-
Filtration: Install filters to remove entrained solids from the fluid.
Sedimentation: Build-Up of Solids
Sedimentation, the accumulation of solid particles within the surge tank, can reduce its effective volume and impair its performance.
Sediment Accumulation
Sediment can accumulate due to:
-
Infiltration: Solids can enter the tank through open vents or leaks.
-
Precipitation: Dissolved solids can precipitate out of the fluid.
-
Corrosion Products: Corrosion can generate solid corrosion products.
Sediment Removal and Prevention
Regular sediment removal is essential for maintaining the tank's performance. Methods for sediment removal include:
-
Manual Cleaning: Physically removing sediment from the tank.
-
Flushing: Using high-velocity water jets to flush sediment out of the tank.
-
Dredging: Using specialized equipment to remove sediment from the tank.
To prevent sediment build-up:
-
Install filters to remove solids from the incoming fluid.
-
Regularly inspect and clean the tank.
Venting/Deaeration: Removing Gases
Air and other gases can accumulate in surge tanks, reducing their effectiveness and potentially causing corrosion.
Importance of Gas Removal
The presence of gases can:
-
Reduce the tank's capacity to absorb pressure surges.
-
Increase the risk of corrosion.
-
Cause instability in the system.
Venting and Deaeration Techniques
Effective venting and deaeration are crucial for maintaining optimal surge tank performance.
Common techniques include:
-
Automatic Air Vents: These release accumulated air automatically.
-
Manual Vents: These allow for manual venting of air.
-
Deaerators: These remove dissolved gases from the fluid.
Proper venting and deaeration are essential for ensuring that the surge tank operates as intended.
Materials of Construction: Choosing the Right Materials
Following an understanding of surge tank equipment, a critical examination of the operational challenges and mitigation strategies is essential to ensuring the long-term reliability and effectiveness of these systems. Surge tanks, while designed to protect against hydraulic transients, operate in environments that can be highly corrosive and demanding. The choice of construction materials, therefore, is paramount to ensuring longevity, safety, and operational efficiency. This section will delve into the most common materials utilized in surge tank construction, weighing their benefits and limitations across different applications.
Steel (Various Grades)
Steel, in its various forms, remains a mainstay in surge tank construction due to its high tensile strength, weldability, and cost-effectiveness. Carbon steel is frequently employed; however, its susceptibility to corrosion necessitates the implementation of protective measures such as coatings or cathodic protection.
Carbon Steel
The selection of appropriate carbon steel grades is crucial, considering factors like yield strength, ductility, and fatigue resistance. Higher-strength steels can reduce material thickness, leading to potential cost savings.
However, they may also exhibit reduced weldability or increased susceptibility to brittle fracture, demanding careful consideration during the design phase. It's imperative to understand the environmental conditions the surge tank will be exposed to, including the chemical composition of the fluid and the external climate.
Alloy Steel
Alloy steels, containing elements like chromium, nickel, or molybdenum, offer enhanced strength, toughness, and corrosion resistance compared to carbon steel. These materials are often favored in situations involving higher pressures or more aggressive environments. The increased cost is justified by the extended service life and reduced maintenance requirements.
Stainless Steel
Stainless steel represents a significant upgrade in corrosion resistance compared to carbon and many alloy steels. Its inherent ability to form a passive chromium oxide layer on the surface renders it highly resistant to a wide range of corrosive agents.
Austenitic Stainless Steel
Austenitic stainless steels, such as 304 and 316, are commonly employed in surge tank construction due to their excellent weldability, formability, and corrosion resistance. 316 stainless steel, containing molybdenum, offers enhanced resistance to pitting and crevice corrosion, particularly in chloride-rich environments.
Duplex Stainless Steel
Duplex stainless steels, possessing a mixed microstructure of austenite and ferrite, offer superior strength and corrosion resistance compared to austenitic grades. They are particularly well-suited for applications involving high pressures and aggressive chemical conditions. The increased cost is often offset by the reduced material thickness and extended service life.
Coatings (Epoxy, Polyurethane, etc.)
Coatings play a crucial role in protecting surge tanks constructed from carbon steel from corrosion. A wide range of coating materials are available, each with its own set of properties and advantages.
Epoxy Coatings
Epoxy coatings offer excellent adhesion, chemical resistance, and durability. They are commonly used as a primer or topcoat to provide a robust barrier against corrosive agents. Multi-layer epoxy systems offer enhanced protection in particularly demanding environments.
Polyurethane Coatings
Polyurethane coatings provide excellent abrasion resistance, flexibility, and UV resistance. They are often used as a topcoat to protect against mechanical damage and weathering. Polyurethane coatings can also be formulated to provide chemical resistance.
Selecting a Coating System
The selection of an appropriate coating system should consider factors such as the type of steel, the environmental conditions, the operating temperature, and the expected service life. Proper surface preparation is essential to ensure optimal coating adhesion and performance.
Elastomers (Seals, Gaskets)
Elastomers are crucial components in surge tank systems, providing sealing and cushioning to prevent leakage and vibration. The selection of appropriate elastomers is vital to maintaining system integrity and preventing failures.
Material Considerations
Nitrile rubber (NBR) offers good resistance to oil and fuels, making it suitable for applications involving hydrocarbon fluids. Ethylene propylene diene monomer (EPDM) provides excellent resistance to weathering, ozone, and water, making it ideal for outdoor applications.
Fluorocarbon elastomers (FKM), such as Viton, offer superior resistance to high temperatures and aggressive chemicals, but come at a higher cost. Compatibility with the fluid being handled and the operating temperature are critical factors in elastomer selection.
Proper installation and maintenance of seals and gaskets are essential to prevent leakage and ensure the long-term reliability of the surge tank system.
Instrumentation, Control, and Safety: Ensuring Reliable Operation
Following an understanding of surge tank equipment, a critical examination of the operational challenges and mitigation strategies is essential to ensuring the long-term reliability and effectiveness of these systems. Surge tanks, while designed to protect against hydraulic transients, operate within complex industrial environments demanding robust instrumentation, sophisticated control mechanisms, and unwavering adherence to safety protocols.
This section addresses the vital role of these elements in guaranteeing the predictable and secure functioning of surge tanks.
The Symphony of Sensors: Instrumentation for Real-Time Monitoring
Instrumentation forms the nervous system of a surge tank, providing the data necessary for informed decision-making and automated responses.
Accurate monitoring of critical parameters is paramount, enabling operators and control systems to understand the current state of the tank and anticipate potential issues.
The key instrumentation components include:
-
Pressure Transducers: These devices provide real-time pressure readings within the tank and connecting pipelines. High accuracy and rapid response times are crucial for detecting and mitigating pressure surges effectively.
-
Level Sensors: Monitoring the fluid level within the tank is essential for preventing overfilling or draining, both of which can compromise the surge tank's performance and potentially damage equipment. Various technologies, including ultrasonic, radar, and differential pressure sensors, are employed to achieve this.
-
Flow Meters: Measuring the flow rate into and out of the surge tank offers valuable insights into the system's dynamics. This data can be used to optimize control strategies and identify anomalies that may indicate developing problems.
Automated Intelligence: Control Systems for Proactive Response
Instrumentation provides the eyes and ears, while control systems serve as the brain, orchestrating the surge tank's response to changing conditions.
Modern control systems leverage sophisticated algorithms and logic to automate many aspects of surge tank operation, minimizing the need for manual intervention and improving overall system performance.
Critical control functions include:
-
Valve Control: Automated valve operation is crucial for directing flow into and out of the surge tank in response to pressure surges or other events. Control systems can precisely modulate valve positions to dampen pressure fluctuations and maintain stable operating conditions.
-
Pump Control: In systems with pumps directly connected to the surge tank, the control system can adjust pump speeds or activate/deactivate pumps to manage fluid levels and mitigate pressure surges.
-
Alarm Systems: Control systems are typically equipped with alarm systems that alert operators to abnormal conditions, such as high pressure, low level, or equipment malfunctions. These alarms allow for timely intervention and prevent potentially catastrophic failures.
Safety as a Cornerstone: Protecting Personnel and Equipment
Safety is not merely an add-on but an integral part of surge tank design and operation.
Robust safety systems and protocols are essential to protect personnel from potential hazards and prevent damage to equipment.
-
Integration with Plant Safety Protocols: Surge tank operation must be seamlessly integrated with the broader plant safety management system. This includes ensuring that all personnel are properly trained on safety procedures and that emergency response plans are in place.
-
Emergency Shutdown Systems (ESD): ESDs are critical safety devices designed to automatically shut down the surge tank system in the event of a critical failure or hazardous condition. ESDs can be triggered by various factors, such as high pressure, high level, or fire detection.
-
Access and Safety Considerations: Safe access to surge tanks for inspection, maintenance, and repair is paramount. This includes providing adequate lighting, secure ladders and platforms, and fall protection equipment. Confined space entry procedures must be strictly followed when entering enclosed surge tanks. Lockout/tagout procedures should be implemented during maintenance to isolate energy sources and prevent accidental startup.
Investing in Reliability
Instrumentation, control systems, and safety measures are not merely expenses but investments in the long-term reliability and safety of surge tank systems.
By implementing robust solutions in these areas, organizations can minimize the risk of costly failures, protect personnel from harm, and ensure the continued operation of critical infrastructure.
Industry Applications: Where Surge Tanks Are Essential
Following an understanding of surge tank equipment, a critical examination of the operational challenges and mitigation strategies is essential to ensuring the long-term reliability and effectiveness of these systems. Surge tanks, while designed to protect against hydraulic transients, find diverse applications across numerous industries, each with specific operational demands and safety requirements. The implementation of surge tanks isn't merely an option; it is often a critical necessity for maintaining infrastructure integrity and operational continuity.
Hydroelectric Power Plants: Safeguarding Energy Generation
Hydroelectric power plants rely heavily on surge tanks to manage the volatile pressure dynamics inherent in their operation.
Penstock and Tailrace Management
The penstock, a critical conduit delivering water to the turbine, is particularly vulnerable to pressure surges caused by rapid changes in water flow. Similarly, the tailrace, which discharges water after it has passed through the turbine, also experiences pressure fluctuations. Surge tanks strategically placed along these waterways act as buffers, absorbing the kinetic energy of the water and preventing potentially catastrophic pressure spikes.
Turbine Protection
Without effective surge protection, the delicate machinery of the turbines is at risk of severe damage. The sudden pressure waves, if unmitigated, can lead to mechanical stress, component failure, and significant downtime. Surge tanks ensure the longevity and operational efficiency of these critical energy-generating assets.
Water Distribution Systems: Ensuring Reliable Water Supply
Water distribution systems, the lifeblood of urban and rural communities, are susceptible to water hammer, a phenomenon caused by sudden valve closures or pump failures.
Mitigating Water Hammer
Water hammer generates high-pressure surges that can rupture pipelines, damage fittings, and disrupt water supply. Surge tanks, integrated into the distribution network, provide a crucial defense against these destructive forces, safeguarding the integrity of the infrastructure.
Maintaining Stable Pressure
Beyond preventing catastrophic failures, surge tanks play a vital role in maintaining consistent pressure throughout the water distribution network. Fluctuations in pressure can impact water availability, particularly in elevated areas or during peak demand periods. Surge tanks help dampen these pressure variations, ensuring equitable and reliable water service for all consumers.
Pumping Stations: Protecting Critical Infrastructure
Pumping stations, responsible for moving fluids over long distances or to higher elevations, are prone to pressure surges during pump start-up and shut-down. These surges can stress the pumps and associated pipelines.
Surge Mitigation
The rapid acceleration or deceleration of fluids during pump operations generates significant pressure transients. Surge tanks are designed to absorb these transients, preventing them from propagating through the system and causing damage.
Preventing Damage to Pumps and Pipelines
Uncontrolled pressure surges can lead to pump cavitation, impeller damage, and pipeline ruptures. By effectively mitigating these surges, surge tanks ensure the continued reliable operation of pumping stations and the integrity of the fluid conveyance network.
Oil & Gas Pipelines: Maintaining Flow and Preventing Failures
Oil and gas pipelines, transporting valuable commodities over vast distances, face similar challenges related to pressure surge management. Valve operations and pump failures can induce rapid changes in flow, leading to potentially hazardous pressure transients.
Valve Operation and Pump Failure Protection
Rapid valve closures, essential for controlling flow or isolating sections of the pipeline, can generate significant pressure surges. Similarly, pump failures can cause sudden flow reversals, leading to potentially damaging pressure waves. Surge tanks, strategically placed along the pipeline, absorb these energy spikes, protecting the system from overpressure.
Maintaining Stable Flow Rates
Consistent flow rates are critical for the efficient and safe operation of oil and gas pipelines. Pressure surges can disrupt flow patterns, leading to operational inefficiencies and potentially hazardous conditions. By damping pressure fluctuations, surge tanks help maintain stable flow rates, ensuring the reliable delivery of these essential resources.
Personnel and Expertise: The People Behind the System
Following a comprehensive look at the applications, maintaining the integrity of surge tank systems hinges not only on robust design and material choices but also on the expertise of the personnel involved. This section details the critical roles of engineers, technicians, and certified inspectors. They are responsible for ensuring the safe and reliable performance of these vital systems.
The Engineering Core: Design, Analysis, and Construction
The foundation of any successful surge tank project lies in the hands of skilled engineers. These professionals, specializing in hydraulic, mechanical, and civil disciplines, bring distinct perspectives to the table. Their collaborative effort ensures a holistic approach to design and implementation.
Hydraulic Engineers
Hydraulic engineers are pivotal in analyzing fluid dynamics within the system. They model surge events, determine optimal tank size and placement, and ensure efficient pressure regulation.
Mechanical Engineers
Mechanical engineers focus on the mechanical integrity of the tank. This includes stress analysis, material selection, and the design of components.
Civil Engineers
Civil engineers are concerned with the structural stability of the surge tank. This includes foundation design and seismic considerations. Their role ensures the tank can withstand environmental forces.
These engineers oversee all stages of a project. From initial design and feasibility studies to construction and commissioning.
Their contributions are essential for ensuring that surge tanks function as intended, protecting critical infrastructure from damaging pressure surges.
Technicians: The Hands-On Maintenance Team
Beyond the design phase, skilled technicians play a vital role in maintaining the operational readiness of surge tank systems. Maintenance and instrumentation technicians are crucial for ensuring long-term reliability.
Maintenance Technicians
These professionals are responsible for routine inspections, preventive maintenance, and repairs. They address issues such as corrosion, erosion, and sedimentation. This ensures the longevity of the system.
Instrumentation Technicians
These technicians specialize in the calibration and troubleshooting of sensors, control systems, and other instrumentation. They ensure accurate monitoring and control.
Their expertise is essential for identifying potential problems before they escalate. Technicians perform corrective actions. These actions minimize downtime and maintain optimal system performance.
Certified Inspectors: Ensuring Integrity and Compliance
Certified inspectors provide an independent assessment of the condition and integrity of surge tanks. They ensure compliance with industry standards and regulations.
These professionals conduct thorough inspections using a variety of non-destructive testing (NDT) methods. This includes ultrasonic testing, radiographic testing, and visual inspection.
Inspectors identify defects, assess the severity of damage, and recommend repairs or replacements. Their findings are critical for informed decision-making regarding maintenance and upgrades.
Their impartiality ensures that safety and reliability are prioritized. This contributes to the long-term operational integrity of surge tank systems.
The combined expertise of engineers, technicians, and inspectors is indispensable for ensuring the safety, reliability, and efficiency of surge tank systems. Their dedication and skills are essential for protecting critical infrastructure. They safeguard against the potentially devastating consequences of uncontrolled pressure surges.
Inspection and Maintenance Tools: Keeping the System Healthy
Personnel and Expertise: The People Behind the System Following a comprehensive look at the applications, maintaining the integrity of surge tank systems hinges not only on robust design and material choices but also on the expertise of the personnel involved. This section details the critical roles of engineers, technicians, and certified inspectors...
The longevity and reliability of surge tank systems depend heavily on rigorous inspection and maintenance programs. These programs rely on a diverse array of tools, ranging from sophisticated non-destructive testing (NDT) equipment to basic safety gear. Effective application of these tools, coupled with skilled personnel, ensures early detection of potential problems and facilitates timely repairs, preventing catastrophic failures.
Non-Destructive Testing (NDT) Methods
NDT methods are essential for evaluating the condition of surge tanks without causing damage. These techniques allow inspectors to identify corrosion, cracks, and other defects that may compromise the structural integrity of the tank.
Ultrasonic Testing (UT)
Ultrasonic Testing (UT) employs high-frequency sound waves to detect internal flaws and measure material thickness. A transducer emits sound waves that propagate through the material and are reflected back by any discontinuities or the back wall of the tank. The reflected waves are analyzed to determine the location, size, and nature of the defect. UT is particularly effective for detecting corrosion under insulation and identifying wall thinning.
Radiographic Testing (RT)
Radiographic Testing (RT) utilizes X-rays or gamma rays to create an image of the internal structure of the surge tank. The radiation passes through the material and is captured on a detector, such as radiographic film. Areas of varying density or the presence of flaws attenuate the radiation differently, resulting in variations in the image. RT is highly effective for detecting volumetric defects, such as porosity, inclusions, and weld discontinuities.
Magnetic Particle Testing (MT)
Magnetic Particle Testing (MT) is used to detect surface and near-surface cracks and discontinuities in ferromagnetic materials. A magnetic field is induced in the material, and fine magnetic particles are applied to the surface. Discontinuities disrupt the magnetic field, causing the particles to concentrate at the flaw location, making it visible to the inspector. MT is relatively simple to perform and is effective for detecting surface cracks that may be difficult to see with the naked eye.
Dye Penetrant Testing (PT)
Dye Penetrant Testing (PT) is another technique used for detecting surface cracks and discontinuities. A liquid dye is applied to the surface of the material and allowed to penetrate any surface openings. Excess dye is then removed, and a developer is applied, which draws the dye out of the flaws, making them visible. PT is a cost-effective method for detecting surface defects in a wide range of materials.
Visual Inspection (VT)
Visual Inspection (VT) is the most basic, yet crucial, inspection method. Trained inspectors visually examine the surge tank for signs of corrosion, damage, leaks, and other anomalies. VT can identify obvious problems such as surface rust, dents, and weld defects. It often serves as the first line of defense in identifying potential issues and determining the need for more advanced NDT methods.
Safety Equipment: Protecting Personnel
Ensuring the safety of personnel is paramount during inspection and maintenance activities. The use of appropriate safety equipment is essential for preventing accidents and injuries.
Personal Protective Equipment (PPE)
Personal Protective Equipment (PPE) includes items such as hard hats, safety glasses, gloves, and respirators. The specific PPE required will depend on the tasks being performed and the hazards present. Proper training on the use and maintenance of PPE is crucial.
Confined Space Entry Equipment
Many surge tanks contain confined spaces, which pose significant hazards due to limited ventilation, potential oxygen deficiency, and the presence of toxic gases. Strict procedures must be followed before entering a confined space, including air monitoring, ventilation, and the use of appropriate respiratory protection. Personnel entering confined spaces must be properly trained and equipped with harnesses, lifelines, and communication devices.
Scaffolding/Lifting Equipment
Accessing elevated areas of surge tanks often requires the use of scaffolding or lifting equipment. Scaffolding must be erected and inspected by qualified personnel to ensure its stability and load-bearing capacity. Lifting equipment, such as cranes and hoists, must be properly maintained and operated by trained operators.
The combination of advanced inspection tools and robust safety measures is critical for maintaining the health and extending the lifespan of surge tank systems. Regular inspections, coupled with proactive maintenance, prevent failures and ensure the continued reliable operation of these essential components.
Video: Surge Tank Maintenance: Optimal Performance Guide
Frequently Asked Questions
What are the key indicators that my surge tank needs maintenance?
Unusual noises, pressure fluctuations in the system, or a drop in overall system performance can indicate surge tank issues. Visual inspection for leaks, corrosion, or damage is also crucial. These signs often suggest maintenance is needed to ensure the surge tank operates effectively.
How often should I inspect and maintain my surge tank?
Regular inspections should occur at least annually, or more frequently in harsh environments. Maintenance frequency depends on operating conditions and manufacturer recommendations. Proactive maintenance of the surge tank prevents major problems.
What are the primary benefits of proper surge tank maintenance?
Proper surge tank maintenance ensures optimal performance of your entire system by preventing water hammer and pressure surges. It extends the lifespan of the surge tank and related equipment, reducing costly repairs and downtime.
What happens if I neglect surge tank maintenance?
Neglecting maintenance can lead to surge tank failure, resulting in system damage and potentially dangerous pressure surges. Reduced efficiency and costly repairs are also likely consequences. Regular maintenance is vital for a functional surge tank.
So, there you have it! Keeping up with your surge tank maintenance might seem like a chore, but trust us, a little proactive care goes a long way in preventing headaches down the road. Take these tips to heart, and you'll be well on your way to ensuring optimal performance and longevity for your surge tank.