Stall Torque: DIY Guide for Mechanics
Understanding stall torque is essential for any mechanic working with automotive systems, especially when diagnosing issues within the powertrain. Torque wrenches, vital tools for achieving precise bolt tightening, become particularly critical when dealing with components affected by stall torque. Improper assessment of stall torque can lead to inefficiencies or failures in systems designed by companies such as Bosch, a leader in automotive technology, and can have implications on vehicle performance, as measured at locations like the dyno testing facilities at automotive research centers.
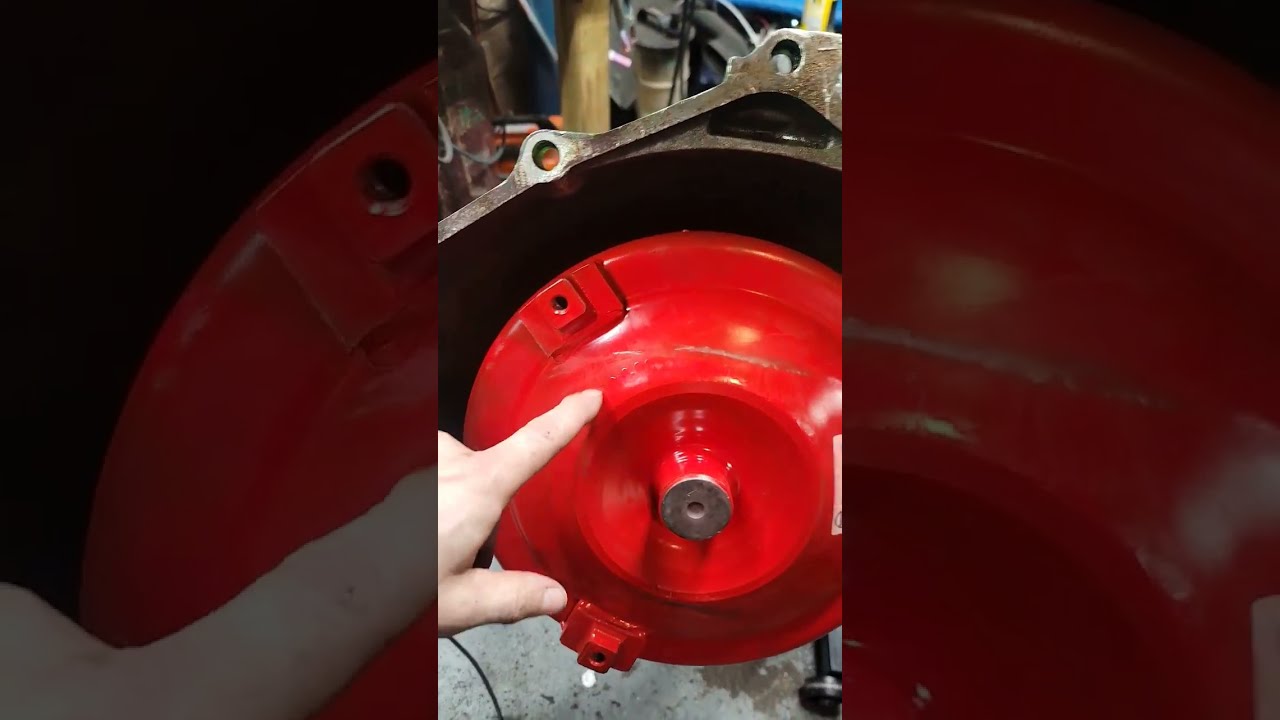
Image taken from the YouTube channel Southern Gearz , from the video titled Guess who makes Summit Racing Pro Ls Torque Converters! .
Demystifying Stall Torque: A Crucial Concept for Motor Applications
Stall torque: It’s a term often encountered when delving into the world of motors, but its true meaning and implications are not always immediately clear. Simply put, stall torque is the maximum torque a motor can produce when it is not rotating. It represents the point at which the motor's output force is exactly balanced by the load it's trying to move, resulting in a standstill. The motor is drawing maximum current, but it's not achieving any movement.
Why Stall Torque Matters
Understanding stall torque is paramount for anyone working with motors, regardless of their level of experience. Whether you're a hobbyist tinkering in a DIY workshop, a robotics enthusiast building intricate machines, or a professional designing electric power tools, stall torque knowledge is indispensable.
Practical Applications
The importance of stall torque becomes strikingly evident when considering real-world applications.
In DIY workshops and garages, selecting the right motor for a project involving lifting or rotating heavy objects hinges on understanding its stall torque capacity.
Robotics applications demand precise movement and lifting capabilities. Ensuring a robot arm can reliably lift a specific weight without stalling requires careful consideration of the motor's stall torque.
Similarly, in electric power tools, such as drills and saws, the ability to overcome resistance and maintain rotation depends on the motor's stall torque. A drill with insufficient stall torque will struggle to bore through tough materials, leading to frustration and inefficiency.
Preventing Motor Damage and Ensuring Proper Selection
Beyond practical applications, understanding stall torque is crucial for preventing motor damage. Operating a motor continuously at or near its stall torque can lead to overheating and premature failure. The motor is drawing maximum current without any corresponding movement to dissipate the heat, leading to a rapid temperature increase.
Therefore, selecting a motor with an adequate stall torque for a given application is vital. This ensures that the motor can handle the expected load without being pushed to its absolute limit, which will extend the lifespan and reliability of the motor. By carefully considering stall torque during the motor selection process, both hobbyists and professionals can ensure the success and longevity of their projects.
Core Concepts: Building Blocks of Stall Torque
Now that we understand the basic definition of stall torque, let's dive deeper into the core principles that make it tick. A firm grasp of these concepts is essential for anyone looking to select the right motor or diagnose performance issues. Let's explore the key factors that determine stall torque, equipping you with the knowledge to optimize your motor applications.
Torque: The Rotational Force
At its core, torque is a rotational force. Think of it as the twisting effort that causes rotation around an axis.
It's measured in units like Newton-meters (Nm) or pound-feet (lb-ft). The higher the torque, the greater the motor's ability to turn a load.
Imagine tightening a bolt: the more force you apply to the wrench handle, the more torque you're applying to the bolt, allowing it to rotate further.
Similarly, in a motor, torque is what drives its shaft to rotate against a load.
Load: The Resistance to Rotation
Load refers to the resistance a motor must overcome. This resistance can take many forms.
Common examples include friction, gravity, or inertia. Understanding the load is crucial for selecting a motor with sufficient torque to start and maintain motion.
Types of Loads
- Frictional Load: This is the resistance caused by surfaces rubbing together. It's always present to some degree and can significantly impact the required torque.
- Inertial Load: This is the resistance to changes in motion. Objects with higher inertia require more torque to accelerate or decelerate.
- Gravitational Load: This is the force of gravity acting on an object. Lifting a weight requires overcoming gravitational load.
RPM (Revolutions Per Minute): The Speed of Rotation
RPM, or Revolutions Per Minute, measures a motor's rotational speed. It indicates how many complete rotations the motor's shaft makes in one minute.
It's a vital parameter for understanding motor performance. There's an inverse relationship between Torque and RPM. As the torque demand increases, the RPM tends to decrease, and vice versa.
A motor can spin quickly with little load. But the speed will drop when faced with higher resistance requiring more torque.
Motor Constant (Kt): The Torque-Current Relationship
The Motor Constant, denoted as Kt, describes how effectively a motor converts electrical current into torque.
It's expressed in units like Nm/Amp (Newton-meters per Ampere). A higher Kt value means the motor produces more torque for each unit of current it draws.
Essentially, Kt quantifies the motor's torque output per unit of current input. It's essential for predicting how much current a motor will draw under specific load conditions.
Gear Ratio: Adjusting Torque and Speed
A gear ratio is the ratio of the number of teeth on the driving gear to the number of teeth on the driven gear in a gearbox.
Gear Ratio significantly impacts torque output and speed. Using a gearbox allows you to trade speed for torque or vice versa.
By using a gearbox to reduce speed, you can proportionally increase the available torque. This is a common strategy for applications requiring high torque at lower speeds.
For example, a low-speed high-torque geared motor for an electric winch allows a smaller motor to lift heavy loads by trading off speed.
Back EMF (Electromotive Force): The Counter Voltage
Back EMF is a voltage generated by a rotating motor that opposes the applied voltage. It's proportional to the motor's speed.
As the motor approaches stall, Back EMF decreases, leading to increased current draw. This heightened current draw generates a significant amount of heat, which must be managed to prevent overheating.
Friction: An Ever-Present Load
Friction is a force that opposes motion, impacting stall torque. It's the resistance a motor must overcome to initiate and maintain rotation.
Reducing friction is crucial for improving efficiency and increasing the available torque for the desired application.
Friction can be minimized through proper lubrication and the use of bearings or bushings to reduce surface contact.
Measuring Stall Torque: Tools and Techniques
Now that we understand the basic definition of stall torque, let's dive deeper into the core principles that make it tick. A firm grasp of these concepts is essential for anyone looking to select the right motor or diagnose performance issues. Let's explore the key factors that determine stall torque.
The Critical Need for Accurate Measurement
Achieving project success hinges on the precision of your measurements. Accurate stall torque measurement is paramount for selecting the right motor and gearbox combination. Inaccurate data leads to underpowered or overpowered systems.
This results in project failure, inefficiency, or even damage. Knowing the precise stall torque allows for informed decisions. Ultimately leading to optimized performance and longevity of your mechanical systems.
Essential Tools and Equipment for Stall Torque Measurement
Measuring stall torque requires specialized tools that provide accurate and reliable data. Let's examine some of the most important equipment. Understanding their function is crucial for anyone undertaking motor performance testing.
Dynamometers (Dynos): Precision Torque Measurement
A dynamometer, or dyno, is the gold standard for measuring torque and speed. It applies a controlled load to the motor. This allows you to measure the motor's output across a range of operating conditions.
Dynos provide precise measurements. They are capable of simulating real-world conditions with high accuracy. This makes them invaluable for optimizing motor performance. Dynos are also great for identifying potential issues.
Ammeters: Measuring Current Draw at Stall
An ammeter is essential for measuring the current drawn by the motor when it is stalled. This measurement is directly related to stall torque through the motor constant (Kt). Knowing the current draw at stall helps estimate the torque output.
This is based on the motor's inherent characteristics. This enables you to calculate the stall torque indirectly. An ammeter is a cost-effective tool that provides valuable insights.
Voltmeters: Ensuring Stable Voltage
Maintaining a stable voltage supply is critical for accurate measurements. A voltmeter is used to monitor the voltage during testing. Voltage fluctuations can significantly impact the motor's performance.
Fluctuations ultimately affecting stall torque. A voltmeter ensures that the power supply is consistent. It provides reliable conditions for measurement. Stable voltage leads to more accurate and repeatable test results.
Power Supply: The Foundation of Reliable Testing
A stable and reliable power supply is the backbone of accurate stall torque measurement. The power supply needs to deliver a consistent voltage and current. This ensures the motor performs predictably under test conditions.
Inconsistent power can skew results and lead to incorrect conclusions. Invest in a quality power supply. Doing so will provide a solid foundation for any motor testing endeavor. It ensures reliability.
Motor Types: Stall Torque Characteristics
After measuring stall torque using various tools and techniques, the next critical step is understanding how stall torque differs across various motor types. This knowledge is essential for selecting the optimal motor for your specific application. Understanding the nuances of each motor type allows you to make informed decisions, balancing performance, efficiency, and cost.
DC Motors (Brushed vs. Brushless): A Stall Torque Showdown
DC motors, the workhorses of countless applications, come in two primary flavors: brushed and brushless. Each presents a unique stall torque profile, influenced by its construction and control mechanism.
Brushed DC Motors
Brushed DC motors are characterized by their simple design and ease of control. Their stall torque is relatively straightforward to predict and manage, making them suitable for basic applications. However, the friction caused by the brushes limits their efficiency and lifespan, particularly under high-torque conditions. This friction also contributes to a lower overall stall torque compared to similarly sized brushless motors.
Brushless DC Motors
Brushless DC motors (BLDC) offer significant advantages in terms of efficiency, durability, and control. Their stall torque characteristics are often superior, thanks to their more efficient design and electronic commutation. The absence of brushes means less friction, resulting in higher torque output and a longer operational life. BLDC motors are the go-to choice for demanding applications where performance and reliability are paramount. However, they require more sophisticated electronic control, which can increase the overall system cost.
Gear Motors: Multiplying Torque at the Expense of Speed
Gear motors combine a motor with a gearbox, providing a simple and effective way to increase stall torque. The gearbox reduces the output speed while simultaneously multiplying the torque.
The Trade-Off: Speed vs. Torque
The fundamental principle behind gear motors is the inverse relationship between speed and torque. By sacrificing speed, you gain a significant boost in torque, allowing a smaller motor to handle heavier loads. This makes gear motors ideal for applications such as robotics, electric vehicles, and industrial machinery, where high torque is essential for overcoming inertia and resistance.
Gear Ratio: The Key to Torque Multiplication
The gear ratio determines the extent to which torque is increased and speed is reduced. A higher gear ratio results in higher torque but lower speed. Careful selection of the gear ratio is crucial to match the motor's capabilities to the specific application's requirements.
Servo Motors: Precision and Controlled Torque
Servo motors are designed for precise position control and are commonly used in robotics, automation, and other applications that require accurate movements. While their primary focus isn't solely on maximizing stall torque, they offer precise torque control within their operational range.
Torque Control: The Key to Servo Performance
Servo motors typically employ feedback mechanisms to ensure precise torque delivery and positioning. This allows them to maintain a desired position or follow a predetermined trajectory with great accuracy, even under varying load conditions.
Stall Torque in Servo Applications
While servo motors can deliver significant torque, their stall torque is often limited by their control system and thermal considerations. Exceeding the stall torque for prolonged periods can lead to overheating and damage. Therefore, selecting a servo motor with adequate torque capacity and implementing proper control strategies are crucial for ensuring reliable operation.
Practical Applications: Stall Torque in Action
After exploring the core concepts and measurement techniques related to stall torque, it’s time to examine its real-world significance. Understanding stall torque isn't just about theoretical knowledge; it's about applying that understanding to ensure successful outcomes in diverse projects and applications. This section will showcase some tangible examples where stall torque plays a pivotal role.
Robotics: Precision Movement and Lifting Capacity
In the realm of robotics, stall torque is paramount. It directly impacts a robot's ability to move precisely, lift objects effectively, and manipulate its environment with accuracy. Whether it's a complex industrial robot or a simple educational bot, the right amount of stall torque is essential.
A robot arm designed to lift heavy components on an assembly line requires motors with high stall torque. Insufficient torque leads to failed lifts, imprecise movements, and potential damage to both the robot and the objects it handles. Conversely, excessive torque can result in jerky, uncontrolled motions, jeopardizing the robot's accuracy and safety.
Therefore, careful calculation and selection of motors based on stall torque specifications are critical. This ensures the robot's ability to perform its intended tasks efficiently and reliably.
Hobby Robotics: Custom Builds and DIY Ingenuity
The world of hobby robotics provides fertile ground for applying stall torque knowledge. From custom-built robots to intricate 3D-printed mechanisms and remote-controlled vehicles, understanding stall torque is key to achieving desired functionality.
Consider a small, autonomous rover designed to navigate uneven terrain. If the rover's drive motors lack sufficient stall torque, it may struggle to climb inclines or overcome obstacles. This can lead to frustrating operational limitations and project setbacks.
Similarly, a 3D-printed robotic arm designed for delicate tasks requires precise motor control. A motor with inadequate stall torque might fail to hold its position under load. This results in inaccurate movements and compromised performance.
By carefully considering stall torque requirements during the design and construction phases, hobbyists can overcome these challenges. They can build robots that are both functional and reliable. Experimentation and iterative design are often crucial to fine-tuning motor selection for optimal performance.
Electric Power Tools: Ensuring Consistent Performance Under Load
Electric power tools, from drills to saws and grinders, rely heavily on stall torque. This torque enables them to perform demanding tasks without stalling under load. A drill's ability to bore through tough materials, or a saw's capacity to cut through thick wood, hinges on the motor's ability to maintain sufficient torque.
Imagine a drill struggling to penetrate a dense hardwood. If the motor's stall torque is insufficient, the drill bit will stop turning, interrupting the task and potentially damaging the tool or the workpiece.
Similarly, a grinder used to smooth welds requires consistent power to remove material effectively. A low stall torque motor might bog down under pressure. This resulting in uneven finishes and increased project time.
Manufacturers of electric power tools carefully select motors with appropriate stall torque characteristics. This ensures their tools deliver consistent performance and reliability. This meets the demands of various applications. For users, understanding the tool's intended use and torque rating helps prevent overloading and extends the tool's lifespan.
Related Areas: Deepening Your Understanding
After exploring the core concepts and measurement techniques related to stall torque, it’s time to examine its real-world significance. Understanding stall torque isn't just about theoretical knowledge; it's about applying that understanding to ensure successful outcomes in diverse projects and applications. This section delves into interconnected concepts that further illuminate the significance of stall torque, solidifying your foundation for effective motor usage and design.
The Imperative of Motor Sizing: Matching Torque to Task
Motor sizing stands as a cornerstone of electromechanical design. It's more than simply choosing a motor that "fits"; it's about selecting a motor whose torque capabilities align precisely with the demands of the application. Stall torque becomes a critical parameter in this equation.
The consequences of inadequate motor sizing are far-reaching.
An undersized motor, one that cannot meet the peak load requirements, will struggle, stall, and potentially suffer irreversible damage.
On the other hand, an oversized motor leads to wasted energy, increased cost, and a bulkier, less efficient system.
Therefore, understanding the application's peak torque requirements and selecting a motor with a stall torque that comfortably exceeds those requirements—while considering efficiency at normal operating loads—is crucial for reliable performance and longevity.
Navigating the Perils of Overloading
Pushing a motor beyond its limits—overloading it—is a recipe for disaster.
Exceeding the motor's stall torque represents a critical threshold, triggering a cascade of detrimental effects.
Overheating emerges as a primary concern. As the motor strains against an excessive load, current draw skyrockets, leading to a rapid increase in internal temperature. This intense heat degrades insulation, weakens components, and significantly shortens the motor's lifespan.
Ultimately, chronic overloading leads to premature failure, resulting in costly replacements and project downtime. Preventing overloading through proper motor sizing and load management is essential for ensuring the long-term health and reliability of the system.
Mastering Heat Dissipation: Keeping Motors Cool Under Pressure
Heat, the insidious byproduct of electrical resistance, poses a significant challenge to motor performance and longevity, particularly when operating near stall torque.
As a motor approaches its stall point, the current flowing through its windings increases dramatically. This increased current generates more heat due to the resistance within the motor's coils.
If this heat isn't effectively dissipated, the motor's temperature rises, potentially causing damage to the insulation and other critical components.
Effective heat dissipation strategies are therefore essential for maintaining optimal operating temperatures and preventing premature failure.
These strategies include:
- Heat Sinks: Metal components designed to draw heat away from the motor's surface.
- Fans: Used to circulate air around the motor, enhancing convective cooling.
- Material Selection: Choosing materials with high thermal conductivity to facilitate heat transfer.
By proactively managing heat, you can ensure that your motors operate reliably, even under demanding conditions.
Gearboxes and Speed Reducers: Leveraging Leverage for Increased Torque
Gearboxes, also known as speed reducers, offer a powerful mechanism for manipulating the relationship between speed and torque in electromechanical systems.
These devices essentially trade rotational speed for increased torque. By reducing the output speed of a motor, a gearbox multiplies the available torque, enabling a smaller, less powerful motor to handle significantly heavier loads.
This is particularly useful in applications where high torque is required but space and weight are limited.
For example, a small robot arm lifting a heavy object might rely on a gearbox to amplify the motor's torque output.
The gear ratio of a gearbox determines the extent of this torque multiplication. A higher gear ratio results in a greater increase in torque but a corresponding decrease in output speed.
Careful consideration of the gear ratio is crucial to ensure that the desired torque and speed characteristics are achieved.
Gearboxes are not without trade-offs. They introduce mechanical complexity, potential sources of friction and wear, and, in some cases, increased size and weight.
However, in many applications, the benefits of increased torque outweigh these drawbacks, making gearboxes an indispensable tool for optimizing motor performance.
Video: Stall Torque: DIY Guide for Mechanics
FAQs: Stall Torque - DIY Guide for Mechanics
What does "stall torque" actually mean in practical terms?
Stall torque is the maximum torque a motor can produce when it's completely stopped (stalled) but still receiving power. Think of it as the absolute peak force it can exert before it gives up and stops rotating.
Why is understanding stall torque important for mechanics?
Knowing the stall torque of a motor helps in selecting the right motor for a specific application. If the load exceeds the stall torque, the motor won't be able to start or function properly, leading to premature wear or failure.
How can I estimate the stall torque of a motor without specialized equipment?
While not perfectly accurate, you can often find the stall torque specified in the motor's datasheet. Otherwise, estimating it requires specialized equipment that is beyond the scope of a typical DIY setup. Look for readily available specifications from the motor manufacturer.
What factors can affect a motor's stall torque?
Several factors impact stall torque, including voltage, motor design, winding configuration, and even temperature. Higher voltage generally leads to higher stall torque, but exceeding the motor's rated voltage can cause damage.
So, there you have it! Hopefully, this DIY guide gives you a better understanding of stall torque and how to troubleshoot issues related to it. Remember to always prioritize safety and consult your vehicle's manual. Now get out there and get wrenching!