Spring Constant Explained: Unlock the Secrets! [Guide]
The spring constant, a crucial parameter in understanding Hooke's Law, governs the relationship between force and displacement in elastic materials. Engineering design often depends on precisely calculating the spring constant to ensure structural integrity and functionality. The behavior of a helical coil spring, for example, is directly dictated by its spring constant. Researchers at the National Institute of Standards and Technology (NIST) continuously refine measurement techniques to accurately determine the spring constant of various materials. This guide unlocks the secrets behind the spring constant, offering a clear explanation of its underlying principles and practical applications.
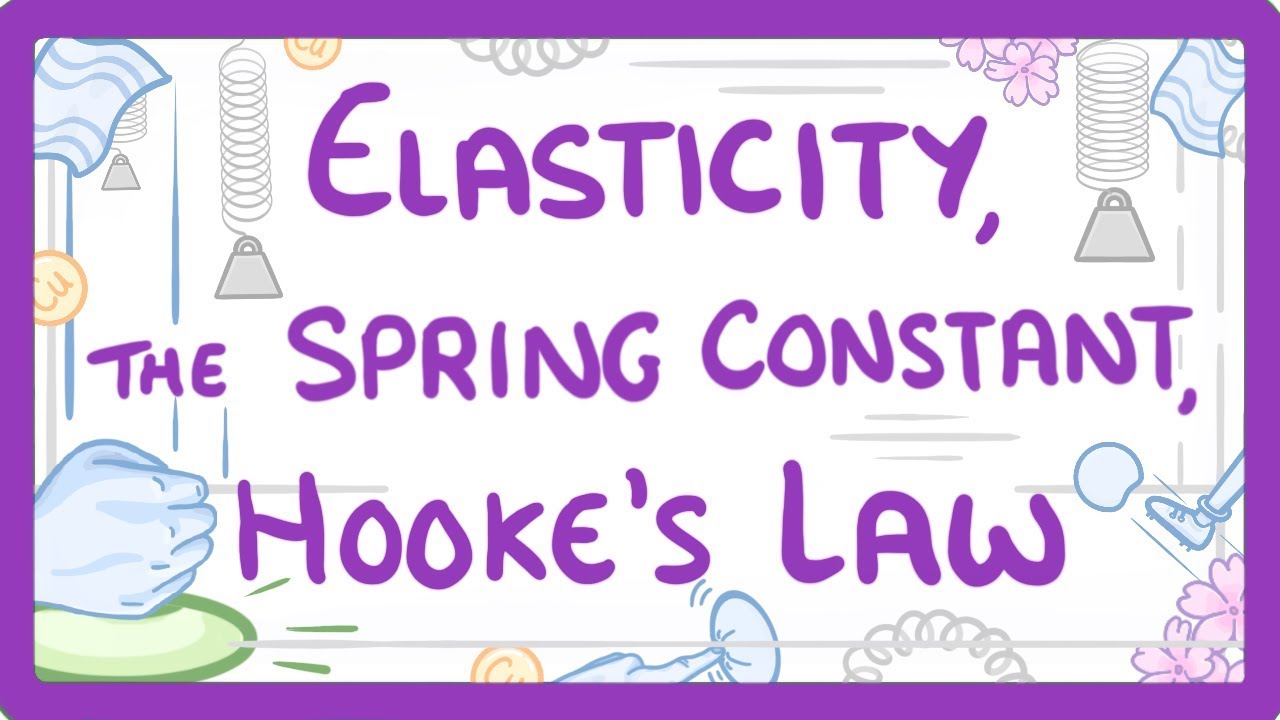
Image taken from the YouTube channel Cognito , from the video titled GCSE Physics - Elasticity, spring constant, and Hooke's Law .
The spring constant, often denoted as k, is a fundamental property in physics and engineering. It quantifies a spring's stiffness, defining the relationship between the force required to stretch or compress it and the resulting displacement. But its significance stretches far beyond simple coils.
From the precise mechanisms within medical devices to the robust suspension systems of vehicles, the spring constant plays a crucial, yet often unseen, role. Understanding this seemingly simple value unlocks insights into a wide array of mechanical behaviors and energy storage principles.
The Ubiquitous Nature of k
The spring constant is not confined to the realm of coiled metal. It appears in various contexts, often subtly:
-
Material Science: It reflects the inherent elasticity of materials, influencing their response to stress and strain.
-
Mechanical Engineering: It governs the behavior of springs in countless machines, from simple latches to complex shock absorbers.
-
Civil Engineering: It informs the design of structures that can withstand dynamic loads, such as bridges and buildings.
-
Even at the Atomic Level: The concept of a "spring constant" is used to model the bonds between atoms within a molecule or crystal lattice, where it represents the stiffness of the bond.
Its broad applicability makes the spring constant an indispensable concept for anyone working with physical systems.
Why Understanding k Matters
The ability to accurately determine and apply the spring constant has practical implications that touch our daily lives.
Consider the design of a car's suspension system. The spring constant of the shock absorbers directly affects the ride quality and handling characteristics. A spring constant that is too low results in a "bouncy" ride, while a spring constant that is too high leads to a harsh and uncomfortable experience.
In the medical field, the spring constant is critical in designing precise instruments. Surgical tools, drug delivery systems, and even prosthetic limbs rely on carefully calibrated springs to function correctly. Miscalculating the spring constant can lead to inaccurate measurements, unreliable performance, or even patient harm.
These examples barely scratch the surface. A deep understanding of the spring constant enables engineers and scientists to design safer, more efficient, and more reliable systems across countless applications.
What This Guide Will Cover
This guide provides a comprehensive exploration of the spring constant, moving beyond a basic definition to examine its underlying principles, influencing factors, and real-world applications. We will delve into:
-
The formal definition of the spring constant and its relationship to stiffness.
-
Hooke's Law, the fundamental principle that governs spring behavior.
-
Factors that influence the spring constant, such as material properties and geometry.
-
The connection between the spring constant and potential energy storage.
-
The role of the spring constant in simple harmonic motion.
-
Methods for experimentally determining the spring constant.
-
Limitations of Hooke's Law and instances of non-linear spring behavior.
The ability to accurately determine and apply the spring constant has practical implications that touch our daily lives.
Consider the design of a car's suspension system. The spring constant of the shock absorbers directly affects the ride quality and handling.
From this example, it is clear why understanding the spring constant is important. We now need to formalize a definition of what k actually represents.
Defining the Spring Constant: Stiffness Quantified
At its core, the spring constant (k) is a measure of a spring's stiffness. It tells us how much force is required to deform the spring by a certain distance.
The Spring Constant as a Measure of Stiffness
Think of it this way: a spring with a high spring constant is very stiff and requires a large force to stretch or compress it.
Conversely, a spring with a low spring constant is easily deformed with only a small force.
This relationship makes the spring constant an invaluable tool for characterizing and predicting the behavior of springs under load.
Resistance to Deformation
The spring constant directly reflects a spring's resistance to deformation.
A higher k value indicates a greater resistance to being stretched or compressed, while a lower k value indicates less resistance.
This resistance stems from the material properties and geometry of the spring, factors we will explore later.
Units of Measurement: Newton per Meter (N/m)
The standard unit of measurement for the spring constant is Newton per meter (N/m) in the International System of Units (SI).
This unit directly reflects the definition of the spring constant as the force required per unit of displacement.
Understanding N/m
One N/m means that a force of one Newton is required to stretch or compress the spring by one meter.
Examples of Spring Constants
For example, a spring with a spring constant of 100 N/m requires a force of 100 Newtons to stretch it by one meter.
Similarly, a spring with a spring constant of 5 N/m only requires a force of 5 Newtons to achieve the same one-meter displacement.
In practical applications, displacements are often much smaller than one meter, and forces are adjusted accordingly. Spring constants can also be expressed in other units, such as pounds per inch (lb/in), but N/m is the standard in scientific and engineering contexts.
The spring constant provides a quantitative measure of stiffness, enabling us to predict how a spring will respond to applied forces. But to truly understand spring behavior, we need to delve into the fundamental law that governs their elasticity.
Hooke's Law: The Foundation of Spring Behavior
Hooke's Law stands as the cornerstone of understanding how springs behave under load.
It elegantly describes the linear relationship between the force applied to a spring and the resulting displacement. This law is not just a theoretical construct. It's a practical tool that allows engineers and scientists to design and analyze systems involving springs.
The Equation: F = -kx
The mathematical representation of Hooke's Law is deceptively simple:
F = -kx
This concise equation encapsulates the core principle of spring behavior. Let's break down each component:
-
F (Force): Represents the force applied to the spring, measured in Newtons (N). It's the external influence causing the spring to deform.
-
k (Spring Constant): As we've established, this is the spring constant, measured in Newtons per meter (N/m). It quantifies the spring's stiffness.
-
x (Displacement): This denotes the displacement of the spring from its equilibrium position, measured in meters (m). It is the amount the spring stretches or compresses.
Unpacking the Variables
Understanding what each variable represents is crucial for applying Hooke's Law effectively.
Force is the external action, the spring constant is the inherent property of the spring, and displacement is the result of their interaction.
Think of it as a cause-and-effect relationship: the force causes a displacement that is mediated by the spring constant.
The Significance of the Negative Sign
The negative sign in Hooke's Law is not merely a mathematical detail; it carries profound physical meaning.
It indicates that the force exerted by the spring is always in the opposite direction to the displacement.
This is a manifestation of the spring's restoring force, its inherent tendency to return to its original, undeformed state.
If you stretch a spring to the right, the spring pulls back to the left. If you compress a spring, the spring pushes back outwards. This opposing force is what the negative sign captures.
Robert Hooke: A Pioneer of Elasticity
Hooke's Law is named after Robert Hooke, a 17th-century English scientist who made significant contributions to various fields, including physics, biology, and architecture.
Hooke's work on elasticity, published in 1676, laid the foundation for our understanding of how materials deform under stress.
His observation that the force required to extend a spring is proportional to the distance of that extension, provided the basis for the law that bears his name. Hooke's Law remains a vital tool in engineering and physics, a testament to his enduring legacy.
The relationship between force and displacement, as elegantly captured by Hooke's Law, provides a powerful tool for understanding spring behavior. However, the spring constant, k, isn't simply a fixed property etched into each spring. It’s a value that's subject to a number of influences.
These factors dictate how stiff or compliant a spring will be. Therefore, understanding these influences is crucial for designing and applying springs effectively in any system.
Factors Influencing the Spring Constant
The spring constant, while often treated as a characteristic property of a spring, is actually quite susceptible to various influences. These influences arise from the inherent nature of the spring itself. Its material composition, its physical dimensions, and the surrounding environmental conditions all play a role.
Material Properties: The Intrinsic Stiffness
The material from which a spring is made is arguably the most fundamental factor influencing its spring constant. Different materials possess varying degrees of inherent stiffness, quantified by their Young's modulus (E).
Young's modulus essentially describes a material's resistance to elastic deformation under tensile or compressive stress. A material with a high Young's modulus, like steel, will exhibit a higher spring constant compared to a material with a lower Young's modulus, like aluminum, assuming all other factors are equal.
The type of steel alloy used also matters significantly.
For example, spring steel alloys are specifically designed to withstand high stresses and repeated deformations without permanent damage, leading to a more consistent and predictable spring constant over its lifespan.
Geometric Considerations: Shape and Size Matter
The geometry of a spring—its shape and dimensions—plays a critical role in determining its spring constant. These geometric factors influence how the material deforms under load. Key geometric parameters include wire thickness (d), coil diameter (D), and the number of active coils (N).
Wire Thickness
A thicker wire provides a greater cross-sectional area to resist deformation. This leads to a stiffer spring and, consequently, a higher spring constant. The relationship is generally proportional to the fourth power of the wire diameter (d⁴). This means a small increase in wire thickness can dramatically increase the spring constant.
Coil Diameter
A larger coil diameter generally results in a lower spring constant. This is because the force applied is distributed over a larger area. The stress on the material is reduced. The relationship is typically inverse to the cube of the coil diameter (D³).
Number of Active Coils
The number of active coils refers to the coils that are free to deform under load. A spring with more active coils will generally have a lower spring constant.
This is because the total displacement is distributed across a greater number of coils. Each individual coil contributes less to the overall stiffness.
The formula for the spring constant of a helical spring reflects these geometric relationships:
k = (G d⁴) / (8 D³ * N)
where G is the shear modulus of the spring material. This equation highlights the interplay between material properties and geometry in determining the spring constant.
Temperature Effects: A Subtle Influence
Temperature can also influence the spring constant, although often to a lesser extent than material properties or geometry. As temperature changes, the material properties of the spring itself can change.
Most metals experience a decrease in Young's modulus with increasing temperature. This results in a slightly lower spring constant at higher temperatures. The effect is usually more pronounced at extreme temperatures.
In applications requiring high precision, thermal compensation techniques or specialized materials with minimal thermal expansion coefficients might be necessary to maintain a consistent spring constant across a range of operating temperatures.
Spring Constant and Potential Energy: Stored Energy Explained
Having explored the factors that determine the spring constant, it’s time to investigate how this fundamental property relates to a spring's ability to store energy.
This section will examine the intimate connection between the spring constant and the potential energy accumulated within a spring as it's stretched or compressed.
We'll delve into the equation that governs this relationship and see how it connects to the overarching principle of energy conservation.
The Spring Constant as a Measure of Energy Storage Capacity
The spring constant, k, not only defines a spring’s stiffness but also its capacity to store potential energy.
A spring with a high k value requires more force to achieve a given displacement and, consequently, stores more energy when compressed or extended to that same displacement.
Think of it this way: stiffer springs "fight back" harder when deformed, and that resistance translates directly into a greater amount of stored energy.
Calculating Potential Energy in a Spring
The potential energy (PE) stored in a spring is directly related to its spring constant (k) and the square of its displacement (x) from its equilibrium position.
The formula for calculating potential energy is:
PE = (1/2) k x2
Where:
- PE is the potential energy, typically measured in Joules (J).
- k is the spring constant, typically measured in Newtons per meter (N/m).
- x is the displacement from the equilibrium position, typically measured in meters (m).
This equation reveals that the energy stored increases quadratically with displacement.
Doubling the displacement results in four times the stored potential energy, highlighting the significant impact of deformation on energy storage.
A Practical Example
Imagine a spring with a spring constant of 100 N/m compressed by 0.1 meters.
The potential energy stored would be:
PE = (1/2) 100 N/m (0.1 m)2 = 0.5 Joules.
This seemingly small amount of energy can be harnessed to perform work when the spring is released.
Connection to Energy Conservation
The potential energy stored in a spring is a manifestation of the broader principle of energy conservation.
When a spring is compressed or stretched, work is done on it, and that work is converted into potential energy stored within the spring's deformation.
When the spring is released, this potential energy can be converted back into kinetic energy, performing work on an object, or dissipated as heat due to internal friction within the spring.
In an ideal system (without friction or other energy losses), the total energy remains constant.
The energy transforms between potential and kinetic forms, demonstrating the fundamental principle of energy conservation.
For instance, consider a mass attached to a horizontal spring on a frictionless surface.
When the spring is compressed and released, the potential energy stored in the spring is converted into the kinetic energy of the mass, causing it to oscillate back and forth.
At the maximum displacement, all the energy is potential, and at the equilibrium position, all the energy is kinetic.
The continuous exchange between potential and kinetic energy exemplifies the conservation of energy within the system.
Having explored the factors that determine the spring constant, it’s time to investigate how this fundamental property relates to a spring's ability to store energy. The preceding sections established that a higher spring constant corresponds to a greater capacity for energy storage, but what happens when that stored energy is released? It's this release that sets the stage for understanding the intimate connection between the spring constant and the mesmerizing world of oscillations, specifically simple harmonic motion.
Spring Constant and Simple Harmonic Motion: Oscillations Demystified
Simple harmonic motion (SHM) describes the periodic motion of an object where the restoring force is directly proportional to the displacement and acts in the opposite direction. A classic example of SHM is the oscillation of a mass attached to a spring. The spring constant, in this context, plays a pivotal role in defining the characteristics of this oscillatory motion.
The Spring Constant as a Determinant of Oscillatory Behavior
The spring constant (k) dictates how readily a spring returns to its equilibrium position after being disturbed.
In the realm of simple harmonic motion, this translates directly into the speed and manner in which the mass oscillates.
A stiffer spring (higher k value) exerts a greater restoring force, causing the mass to accelerate more rapidly toward equilibrium.
Conversely, a weaker spring (lower k value) results in a gentler restoring force and a slower return to equilibrium.
Deriving the Equations for Period and Frequency
To quantify the relationship between the spring constant and SHM, let's examine the equations for the period (T) and frequency (f) of oscillation in a spring-mass system.
The period is the time it takes for one complete oscillation, while the frequency is the number of oscillations per unit time.
For a mass (m) attached to a spring with a spring constant (k), the period is given by:
T = 2π√(m/k)
And the frequency is given by:
f = 1/T = (1/2π)√(k/m)
Interpreting the Equations
These equations reveal a crucial insight: the period of oscillation is inversely proportional to the square root of the spring constant.
This means that a stiffer spring (higher k) results in a shorter period and, therefore, a higher frequency. The mass oscillates more rapidly.
Conversely, a weaker spring (lower k) leads to a longer period and lower frequency. The mass oscillates more slowly.
Furthermore, the equations show that the period is directly proportional to the square root of the mass. A larger mass will oscillate more slowly.
Examples Illustrating the Spring Constant's Influence
Consider two identical masses attached to springs with different spring constants.
If spring A has a spring constant twice that of spring B (kA = 2kB), then the frequency of oscillation for mass A will be √2 times greater than that of mass B.
This means that mass A will oscillate approximately 41% faster than mass B.
Another example is comparing two systems with identical springs but different masses.
If mass C is four times heavier than mass D (mC = 4mD), the period of oscillation for mass C will be twice that of mass D.
The heavier mass will oscillate with a period twice as long as that of the lighter mass.
These examples highlight the tangible impact of the spring constant on the dynamics of oscillatory systems. It's not just a theoretical value but a practical determinant of motion.
Having explored the factors that determine the spring constant, it’s time to investigate how this fundamental property relates to a spring's ability to store energy. The preceding sections established that a higher spring constant corresponds to a greater capacity for energy storage, but what happens when that stored energy is released? It's this release that sets the stage for understanding the intimate connection between the spring constant and the mesmerizing world of oscillations, specifically simple harmonic motion.
Real-World Applications: Where the Spring Constant Matters
The spring constant isn't just an abstract concept confined to textbooks and laboratories. It’s a critical parameter that governs the behavior of countless devices and systems we encounter every day. From ensuring a smooth ride in our cars to enabling precise drug delivery in medical devices, the spring constant plays a vital role in engineering design and functionality.
Understanding its implications is essential for engineers, designers, and anyone interested in the mechanics of the world around them.
Automotive Engineering: The Suspension System
One of the most prominent applications of springs, and therefore the spring constant, is in vehicle suspension systems. These systems are designed to absorb shocks and vibrations from the road, providing a comfortable and stable ride for passengers.
The spring constant of the suspension springs directly affects the vehicle's handling characteristics. A higher spring constant results in a stiffer suspension, which can improve handling and reduce body roll during cornering. However, it can also lead to a harsher ride.
Conversely, a lower spring constant provides a softer, more comfortable ride but may compromise handling performance.
Engineers carefully select the spring constant to achieve the optimal balance between ride comfort and handling based on the vehicle type and intended use. Advanced suspension systems may even incorporate variable spring rates to adapt to changing road conditions.
Medical Devices: Precision and Control
The spring constant is equally important in the design of many medical devices where precision and controlled motion are paramount.
Syringes, for example, rely on springs to deliver medication at a consistent rate. The spring constant of the syringe plunger determines the force required to depress it, which directly affects the injection speed and dosage accuracy.
Similarly, surgical instruments such as forceps and clamps use springs to provide controlled gripping force. A well-defined spring constant ensures that these instruments apply the appropriate amount of pressure without causing damage to delicate tissues.
In sophisticated drug delivery systems, micro-springs with precisely calibrated spring constants are used to regulate the flow of medication. These springs enable controlled and sustained release of drugs, improving therapeutic outcomes.
Mechanical Systems: From Clocks to Construction
Beyond automotive and medical applications, the spring constant is a fundamental consideration in a wide range of mechanical systems.
Consider mechanical clocks and watches. The balance spring, also known as a hairspring, oscillates at a precise frequency, regulating the timekeeping mechanism. The spring constant of the balance spring directly determines its oscillation frequency, and therefore the accuracy of the clock or watch.
In construction and manufacturing, springs are used in various machines and equipment, such as vibration isolators and load-bearing structures. The spring constant of these springs is critical for ensuring stability, reducing noise and vibration, and preventing structural damage.
From simple tools to complex machinery, the spring constant is a key design parameter that influences performance, reliability, and safety.
Consumer Products: Everyday Applications
We also find springs, and thus, applications dependent on the spring constant, in everyday consumer products.
Think of retractable pens. The small spring inside allows for easy extension and retraction of the pen tip. The spring constant dictates the force needed to click the pen.
Similarly, springs are used in furniture, appliances, and even toys. The correct spring constant ensures functionality, comfort, and durability of these products.
Experimental Determination: Measuring the Spring Constant
While the theoretical underpinnings of the spring constant, rooted in material properties and geometry, provide a valuable framework, practical applications often demand empirical verification. Determining the spring constant experimentally allows for accounting of real-world imperfections and validating theoretical calculations.
This section will outline the standard methodology for experimentally determining the spring constant using readily available equipment and fundamental principles, highlighting the critical aspects of accurate measurement and error mitigation.
The Static Method: Applying Hooke's Law
The most common and straightforward method for experimentally determining the spring constant relies directly on Hooke's Law (F = -kx). This static method involves applying known forces (weights) to the spring and measuring the resulting displacement.
Procedure
-
Setup: Secure the spring vertically from a fixed support. Ensure a stable and vibration-free environment. A simple clamp stand works well.
-
Initial Measurement: Measure the initial length of the spring with no load applied. This will serve as your reference point. Use a ruler or, for greater accuracy, a Vernier caliper.
-
Applying Known Weights: Gradually apply known weights to the spring, recording the mass of each weight. Convert mass to force using F = mg (where g is the acceleration due to gravity, approximately 9.81 m/s²).
-
Measuring Displacement: After each weight is added, carefully measure the new length of the spring. Calculate the displacement (x) by subtracting the initial length from the new length. Ensure that you are measuring the change in length accurately.
-
Data Collection: Record the applied force (F) and corresponding displacement (x) for each weight. Aim for at least five to ten data points to improve accuracy.
-
Calculating the Spring Constant: Plot the applied force (F) on the y-axis and the displacement (x) on the x-axis. The resulting graph should be a straight line. The spring constant (k) is the slope of this line. You can determine the slope by selecting two points on the line and calculating the rise over run (ΔF/Δx).
Example Calculation
Let's say you apply a force of 1 N and the spring stretches by 0.02 meters. Then, the spring constant (k) is:
k = F/x = 1 N / 0.02 m = 50 N/m
Importance of Accurate Measurements
The accuracy of the experimentally determined spring constant hinges directly on the precision of your measurements.
-
Length Measurements: Use a high-resolution measuring device (e.g., Vernier caliper) to minimize uncertainty in length measurements. Ensure consistent alignment and avoid parallax errors.
-
Weight Calibration: Use calibrated weights to ensure the applied force is known accurately. Cheap weight sets are often inaccurate.
-
Stable Setup: Minimize vibrations and external disturbances that could affect the spring's equilibrium position.
Minimizing Errors
Several factors can introduce errors in the experimental determination of the spring constant. Addressing these potential sources of error is crucial for obtaining reliable results.
-
Elastic Limit: Ensure that you do not exceed the spring's elastic limit. Beyond this point, the spring will deform permanently, and Hooke's Law no longer applies. Gradually increase the load and observe if the spring returns to its original length when the weight is removed.
-
Hysteresis: Springs can exhibit hysteresis, where the loading and unloading curves are slightly different. To minimize this effect, cycle the spring several times before taking measurements.
-
Friction: Friction in the support system or between the spring coils can introduce errors. Ensure that the spring moves freely without any obstruction.
-
Parallax Error: Always view the measuring scale directly to avoid parallax errors.
-
Zero Error: Check measuring instruments for zero errors and correct them before taking measurements.
Data Analysis and Interpretation
Once you have collected the data, careful analysis is essential.
-
Linearity Check: Visually inspect the force-displacement graph. If the data points deviate significantly from a straight line, it may indicate that you have exceeded the elastic limit or that there are other sources of error.
-
Linear Regression: Perform a linear regression analysis on the data to obtain a more accurate value for the spring constant (slope of the line). This statistical technique provides the best-fit line through your data points, minimizing the impact of random errors.
-
Uncertainty Analysis: Estimate the uncertainty in your measurements (e.g., using the standard deviation of the slope from the linear regression). This will provide a range within which the true value of the spring constant is likely to lie.
By meticulously following these procedures and carefully addressing potential sources of error, you can accurately determine the spring constant experimentally, providing valuable insights into the behavior of springs in real-world applications.
Limitations and Non-Linear Behavior
The experimental determination of the spring constant, as valuable as it is, often operates under the assumption that Hooke's Law holds true. This assumption works well within certain limits, but it's crucial to acknowledge that springs, like all physical systems, exhibit more complex behaviors when pushed beyond those boundaries. Understanding these limitations and the resulting non-linearities is essential for a complete grasp of spring mechanics.
The Elastic Limit: Where Hooke's Law Breaks Down
Hooke's Law, the bedrock of our understanding of spring behavior, posits a linear relationship between the applied force and the resulting displacement. However, this linearity is not infinite. Every spring has an elastic limit, a point beyond which the material undergoes permanent deformation.
Once this limit is exceeded, the spring will no longer return to its original shape upon removal of the load. This is because the material has begun to yield, experiencing plastic deformation. The relationship between force and displacement becomes non-linear, and Hooke's Law ceases to accurately predict the spring's behavior.
Understanding Plastic Deformation
Plastic deformation is a permanent change in the shape of a solid object due to the application of sustained stress. Unlike elastic deformation, where the object returns to its original shape when the stress is removed, plastic deformation results in a lasting alteration.
Think of bending a paperclip: initially, it springs back (elastic deformation), but if you bend it far enough, it stays bent (plastic deformation). Springs exceeding their elastic limit behave similarly.
Non-Linear Spring Behavior: Beyond the Straight Line
Even before reaching the point of permanent deformation, a spring's behavior can deviate from the linear relationship described by Hooke's Law. This non-linear behavior can manifest in several ways.
For instance, the spring constant itself might change with increasing displacement. This can occur due to complex interactions within the spring material or changes in the spring's geometry under high loads.
In these scenarios, the spring constant is not truly constant anymore. Instead, it becomes a variable that depends on the amount of deformation.
Factors Contributing to Non-Linearity
Several factors can contribute to non-linear spring behavior:
- Material Properties: The inherent properties of the spring material itself can introduce non-linearities, especially at higher stress levels.
- Geometric Effects: As a spring is compressed or extended, its geometry changes. These changes, such as coil binding in compression springs, can alter the spring constant.
- Large Deflections: Hooke's Law is most accurate for small deflections. When a spring undergoes large deflections, the linear approximation becomes less valid.
Implications for Design and Application
The limitations of Hooke's Law and the potential for non-linear behavior have significant implications for the design and application of springs. Engineers must carefully consider the expected range of motion and the potential for exceeding the elastic limit.
When designing systems that rely on springs, it’s important to:
- Select materials with appropriate elastic properties.
- Choose spring geometries that minimize stress concentrations.
- Account for potential non-linearities in the design calculations.
Ignoring these factors can lead to inaccurate predictions, system failures, and compromised performance.
Modeling Non-Linear Spring Behavior
While Hooke's Law provides a simple and useful approximation, more sophisticated models are needed to accurately describe non-linear spring behavior. These models often involve complex mathematical equations and numerical simulations.
Finite element analysis (FEA), for example, can be used to simulate the behavior of springs under various loading conditions, taking into account material non-linearities and geometric effects.
These advanced techniques allow engineers to design and optimize spring systems for applications where linear approximations are insufficient.
Video: Spring Constant Explained: Unlock the Secrets! [Guide]
FAQs About Spring Constant
This FAQ section answers common questions about the spring constant, clarifying concepts discussed in our guide. We aim to provide helpful information to deepen your understanding.
What exactly does the spring constant tell you?
The spring constant, often denoted as k, indicates the stiffness of a spring. It represents the force required to stretch or compress the spring by one unit of length. A higher spring constant means a stiffer spring.
How is the spring constant related to Hooke's Law?
Hooke's Law (F = -kx) directly incorporates the spring constant. The formula shows that the force exerted by a spring is proportional to the displacement from its equilibrium position, with the spring constant acting as the constant of proportionality. The spring constant is a central part of Hooke's law.
What are the common units for the spring constant?
The spring constant is typically measured in Newtons per meter (N/m) in the International System of Units (SI). It can also be expressed in other units, like pounds per inch (lb/in), but N/m is the most standard representation.
Can the spring constant be negative?
While the force exerted by a spring can be negative (indicating a restoring force), the spring constant itself is generally considered a positive value. The negative sign in Hooke's Law accounts for the direction of the force relative to the displacement. The spring constant represents the stiffness magnitude.