Reed & Prince Screws: History & Where to Buy Them
Reed & Prince screws, a once-ubiquitous type of screw drive, feature a distinct pointed tip and cruciform recess, attributes distinguishing them from the more common Phillips head screws. Henry F. Phillips, while not the inventor, popularized a similar design through his company, Phillips Screw Company, leading to widespread confusion between the two drive types. The Reed & Prince Manufacturing Company, founded by Eugene Reed and Asa Prince, originally produced these screws, holding patents that predated Phillips' design. Despite their decline in mainstream applications, particularly with the advent of newer screw drives used by modern power tools, specialized fasteners using the Reed & Prince design are still available through select distributors and vintage hardware suppliers.
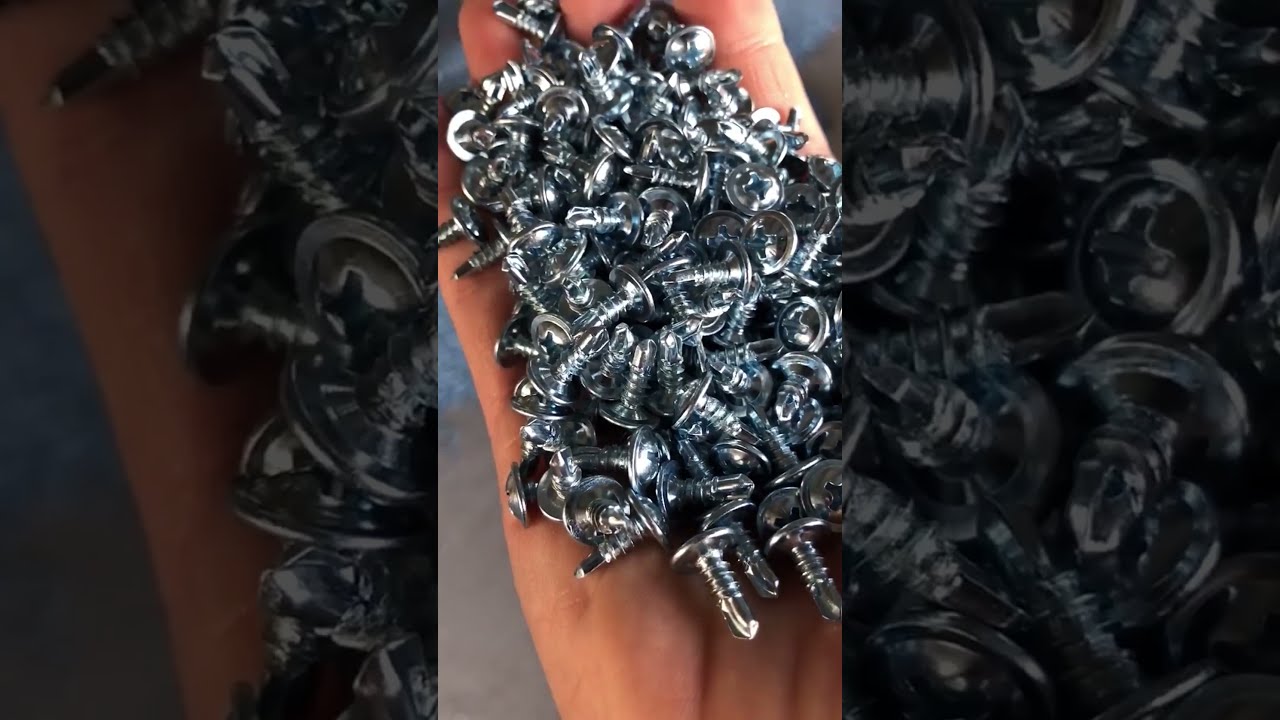
Image taken from the YouTube channel Prince Fastener , from the video titled Screws wholesale-Prince Fastener-Fastener manufacturer | self tapping screws | drywall screws .
Unearthing the Mystery of Reed & Prince Screws
Reed & Prince screws, a once-ubiquitous fastener, often escape the notice of the modern craftsman. Yet, their distinctive design and historical prevalence make them a subject worthy of examination. Understanding their characteristics is vital for anyone involved in restoration projects or seeking historical accuracy in their work.
Defining the Reed & Prince Screw
Unlike the more common Phillips or slotted screws, the Reed & Prince screw features a distinctive pointed tip and a 45-degree flank angle. This design differs significantly from the blunter tip and shallower angle of a Phillips head.
This unique geometry demands a specific driver, and using the wrong one can lead to damage and frustration.
A Glimpse into the Past
The Reed & Prince screw enjoyed its heyday in the mid-20th century, particularly in the post-World War II era. It was a staple in American manufacturing, finding widespread use in everything from automobiles to appliances.
Its prevalence during this period makes it a common sight in vintage machinery and structures. Recognizing this screw type can unlock valuable insights into the age and origin of an artifact.
Unique Design Features
Several key features set Reed & Prince screws apart from their contemporaries. The aforementioned pointed tip aids in self-centering and starting the screw, while the 45-degree flank angle provides a secure grip for the driver.
However, this angle also contributes to a tendency for the driver to cam-out, a phenomenon where the driver slips out of the screw head under high torque. This characteristic, while sometimes frustrating, is a key identifier.
Why Study Them Today?
While less common in modern manufacturing, Reed & Prince screws remain relevant for several reasons.
Restoration and Preservation
Perhaps the most significant reason to understand these screws is their presence in vintage items. Restoring a classic car, antique radio, or mid-century modern furniture often requires working with original components. Using the correct type of screw is essential for maintaining historical accuracy and preventing damage to delicate materials.
Historical Accuracy
Beyond restoration, understanding Reed & Prince screws provides valuable context for historical research. The type of fastener used can offer clues about the manufacturing processes and technological capabilities of a particular era. It allows for a deeper understanding of the material culture of the 20th century.
Avoiding Damage
Finally, knowing how to identify a Reed & Prince screw helps prevent damage. Attempting to drive one with a Phillips head screwdriver can strip the head, making removal difficult and potentially harming the surrounding material. Recognizing the difference is crucial for responsible handling and preservation.
The Reed & Prince Manufacturing Company: A Worcester Legacy
Unearthing the Mystery of Reed & Prince Screws Reed & Prince screws, a once-ubiquitous fastener, often escape the notice of the modern craftsman. Yet, their distinctive design and historical prevalence make them a subject worthy of examination. Understanding their characteristics is vital for anyone involved in restoration projects or seeking historical accuracy in their work. The story of Reed & Prince isn't merely about a screw; it's a tale of industrial innovation, family legacy, and a manufacturing powerhouse rooted in Worcester, Massachusetts.
Roots in Worcester: The Founding and Initial Purpose
The Reed & Prince Manufacturing Company's origins trace back to the mid-19th century in Worcester, a city then burgeoning as a major industrial center. The company was officially incorporated in 1887, but its roots extend to an earlier business established by Elon Reed.
Initially, the company focused on producing a variety of hardware items, gradually specializing in fasteners. This specialization proved to be a strategic move, aligning with the increasing demand for standardized and reliable fastening solutions driven by the rapid industrialization of the era.
The initial purpose of Reed & Prince was to capitalize on the growing need for mass-produced hardware, but they soon found a niche in screws.
Growth, Expansion, and Technological Advancements
The late 19th and early 20th centuries marked a period of significant growth and expansion for Reed & Prince. Demand for their fasteners increased steadily as industries like automotive, manufacturing, and construction expanded.
The company embraced innovation, investing in new machinery and manufacturing processes to improve efficiency and product quality. This commitment to technological advancement enabled Reed & Prince to stay competitive and meet the evolving needs of their customers.
One key aspect of their growth was the development and patenting of specialized screw designs, most notably the Reed & Prince screw drive itself. This differentiated their products from competitors.
Key Milestones: Patents and Market Penetration
Reed & Prince achieved several key milestones throughout its history. Patenting the Reed & Prince screw drive was a pivotal moment, establishing a unique product offering and solidifying their market position.
The company’s success extended beyond the United States, achieving significant market penetration internationally. Their screws were used in various industries globally, contributing to their reputation as a leading fastener manufacturer.
Their ability to consistently produce high-quality screws at scale allowed them to secure contracts with major manufacturers across multiple industries.
The Reed & Prince Family: Influence and Legacy
The Reed & Prince family played a central role in the company's success. Their leadership and vision guided the company through periods of growth, innovation, and market challenges.
Family members held key leadership positions, actively participating in strategic decision-making and shaping the company's culture. The family's commitment to quality and innovation contributed to the company's reputation and long-term success.
The family's stewardship extended beyond mere profit; they fostered a culture of innovation and community engagement in Worcester.
Factory Locations in Worcester: A Physical Presence
Reed & Prince's physical presence in Worcester was substantial, with multiple factory buildings and facilities located throughout the city. These factories served as the hub of their manufacturing operations.
Key locations included large complexes on Duncan Avenue and Gold Street, which housed their manufacturing equipment, warehousing, and administrative offices. These buildings were significant employers in Worcester, contributing to the city's economic vitality.
Today, the legacy of Reed & Prince is still visible in some of these buildings, serving as reminders of Worcester's industrial past and the company's important role in it. These historical sites serve as a tangible link to the company's history.
Technical Deep Dive: Sizes, Materials, and the Dedicated Screwdriver
Reed & Prince screws, a once-ubiquitous fastener, often escape the notice of the modern craftsman. Yet, their distinctive design and historical prevalence make them a subject worthy of examination. Understanding their characteristics is vital for anyone engaged in restoration projects or seeking a deeper appreciation of historical manufacturing practices.
This section delves into the technical specifications that define Reed & Prince screws. We will dissect their sizes, the materials from which they were made, and the specialized screwdrivers required for their effective use. This exploration will provide a comprehensive understanding of the technical aspects of these fasteners.
Size and Dimensional Specifications
Reed & Prince screws, like other screw types, were manufactured in a range of sizes to suit various applications. Understanding these sizes is crucial for proper identification and replacement.
The sizing system, while seemingly similar to other numbering conventions, possesses unique characteristics. A comprehensive chart detailing screw length, thread pitch, and head diameter is essential for accurate identification.
These screws are generally measured by their length (in inches) and a numerical size designation that corresponds to the screw's diameter and thread pitch. This numbering system does not directly correlate to standard fractional inch measurements, making accurate identification reliant on reference charts or specialized gauges.
Materials of Construction
The materials used in manufacturing Reed & Prince screws played a critical role in their strength, durability, and resistance to corrosion. Common materials included various grades of steel, each offering different properties.
Common Steel Alloys
Carbon steel was a frequently used material, often surface-treated with finishes like bluing or zinc plating to enhance corrosion resistance. The specific steel alloy used would influence the screw's tensile strength and shear strength, dictating its suitability for different applications.
Alloy steels, incorporating elements like chromium or nickel, were also employed to provide enhanced strength and corrosion resistance. These alloys were particularly valuable in applications where screws were exposed to harsh environments.
Material Impact on Performance
The choice of material directly impacted the screw's performance characteristics. Higher-strength alloys were essential for applications requiring resistance to high loads or stress. Conversely, more ductile materials might have been preferred in situations where the screw needed to withstand bending or deformation.
The Reed & Prince Screwdriver: A Specialized Tool
One of the defining characteristics of Reed & Prince screws is the requirement for a matching, dedicated screwdriver. Unlike the more versatile Phillips head, the Reed & Prince design necessitates a driver with a precisely shaped tip to engage properly with the screw's recesses.
Unique Tip Geometry
The Reed & Prince screwdriver features a distinctively pointed tip and a 45-degree flank angle, differing from the more rounded tip of a Phillips screwdriver. This geometry allows for a more secure engagement and reduces the risk of cam-out when properly used.
Handle Design and Ergonomics
Reed & Prince screwdrivers were manufactured with a variety of handle designs, ranging from traditional wooden handles to more modern plastic or composite grips. Ergonomics played a crucial role in ensuring comfortable and efficient use, especially in production environments where workers would use these tools for extended periods.
The Importance of Using the Correct Screwdriver
Using the wrong screwdriver with a Reed & Prince screw can lead to significant problems. The head can be easily damaged, making removal extremely difficult, and the driver tip can be worn down.
Preventing Screw Head Damage
Attempting to drive a Reed & Prince screw with a Phillips screwdriver, or vice versa, will almost certainly result in damage. The improper fit leads to slippage and deformation of the screw head's delicate recesses.
Ensuring Proper Torque and Engagement
Using the correct screwdriver ensures that the torque is applied evenly across the screw head, maximizing the driving force and minimizing the risk of stripping the threads. Proper engagement prevents the driver from slipping out of the recess, which can mar the surrounding material and damage the screw head.
Applications in Action: Where Reed & Prince Screws Found Their Niche
Reed & Prince screws, a once-ubiquitous fastener, often escape the notice of the modern craftsman. Yet, their distinctive design and historical prevalence make them a subject worthy of examination. Understanding their characteristics is vital for anyone engaged in restoration, historical preservation, or simply seeking to appreciate the evolution of fastening technology. But where exactly did these screws excel, and why were they the preferred choice in certain applications?
This section explores the diverse range of industries and specific contexts where Reed & Prince screws found their niche, illuminating the reasons behind their selection and highlighting their unique contributions.
Automotive, Manufacturing, and Construction: A Workhorse Fastener
Reed & Prince screws found substantial use in the automotive, manufacturing, and construction industries during their peak. Their pointed tip and ability to self-center made them particularly useful in assembly line settings, where speed and accuracy were paramount.
In automotive manufacturing, they were employed in securing interior trim, dashboard components, and various other non-structural elements. The ease of use and reliable grip offered by the Reed & Prince design contributed to efficient assembly processes.
Similarly, in general manufacturing, these screws were used across a wide array of products, from appliances to machinery. Their versatility and availability made them a staple fastener.
Even in construction, while not as prevalent as in other sectors, Reed & Prince screws found applications in cabinetry, woodworking, and light-duty fastening tasks.
Aerospace Applications: Precision and Reliability Aloft
The aerospace industry demands fasteners that meet stringent requirements for strength, reliability, and precision. Reed & Prince screws, while perhaps not as widely known in this context as other specialized aerospace fasteners, did find a specific niche.
They were sometimes used in aircraft assembly and maintenance for non-critical applications where a flush or countersunk head was desired. Their ability to provide a secure hold without excessive torque made them suitable for working with delicate or thin materials.
The pointed tip of Reed & Prince screws also aided in precise alignment during assembly, which was crucial in aircraft manufacturing.
Electronics Applications: Connecting the Circuitry
In the realm of electronics, the small size and ease of use of Reed & Prince screws made them a viable option for certain applications.
They were used in securing components to circuit boards, assembling electronic enclosures, and fastening connectors. The availability of Reed & Prince screws in smaller sizes allowed for their integration into compact electronic devices.
The ability to achieve a tight and reliable connection was particularly important in electronics, where loose fasteners could lead to electrical malfunctions.
Specific Examples: Illuminating Use Cases
To further illustrate the applications of Reed & Prince screws, considering specific examples can be helpful:
-
Vintage Appliances: Many vintage appliances, such as toasters, radios, and mixers, were assembled using Reed & Prince screws. Restoring these appliances often requires sourcing the correct screws to maintain historical accuracy.
-
Classic Automobiles: Certain classic car models utilized Reed & Prince screws extensively in their interiors and trim. Automotive restoration projects often involve locating and using these screws to preserve the original aesthetic.
-
Early Electronics: Early electronic devices, such as tube amplifiers and radios, frequently employed Reed & Prince screws in their construction. These screws played a crucial role in securing components and ensuring proper electrical connections.
By examining these diverse applications, it becomes clear that Reed & Prince screws were a versatile and widely used fastener in their time. Their unique design characteristics and availability made them a practical choice for a variety of industries and projects.
The Sunset Years: Decline and the Rise of Phillips
Reed & Prince screws, a once-ubiquitous fastener, often escape the notice of the modern craftsman. Yet, their distinctive design and historical prevalence make them a subject worthy of examination. Understanding their characteristics is vital for anyone engaged in restoration, historical preservation, or simply seeking to appreciate the evolution of fastening technology. The shift away from Reed & Prince represents a fascinating case study in how technical advancements and market forces can lead to the obsolescence of even well-established products.
Factors Contributing to the Decline
Several converging factors led to the decline in the popularity of Reed & Prince screws. These can be broadly categorized into manufacturing challenges, performance limitations, and the rise of more efficient alternatives.
Manufacturing Costs: One significant aspect was the cost of manufacturing. Reed & Prince screw heads, with their more sharply pointed recess, required more precise tooling and tighter tolerances during production. This translated to higher manufacturing costs compared to other screw types, making them less attractive to manufacturers seeking to optimize expenses.
Driver Cam-Out Issues: Another drawback was the tendency for drivers to cam-out, or slip out of the screw head, under high torque. While the pointed design provided a secure initial grip, it also created concentrated stress points. This could lead to damage to the screw head or the surrounding material, especially when using power tools. This contrasts with designs specifically engineered to mitigate cam-out.
Changing Industry Standards: As industries evolved, there was a growing need for standardization of tools and fasteners. The proliferation of different screw types created logistical challenges for manufacturers and consumers alike. This standardization trend ultimately favored more versatile and readily available options, like Phillips.
The Ascent of Phillips: Innovation and Market Dominance
The Phillips screw, patented by Henry F. Phillips, presented a significant advancement in screw technology. Its design incorporated several key features that addressed the limitations of earlier screw types, including Reed & Prince.
Engineered Cam-Out: Ironically, one of the defining features of the Phillips screw was its intentional cam-out. Instead of preventing cam-out entirely, the Phillips design allowed the driver to slip out at a predetermined torque level. This prevented over-tightening and damage to the screw or the surrounding material, particularly in mass production settings.
Self-Centering Driver: The Phillips head also featured a self-centering design that made it easier to align the driver with the screw head. This increased efficiency and reduced the risk of slippage, especially when using power tools.
Licensing and Standardization: Crucially, Phillips made his design available for licensing to multiple manufacturers. This fostered widespread adoption and ultimately established the Phillips screw as the industry standard.
The Impact of Standardization on Specialized Screw Types
The move towards standardization had a profound impact on specialized screw types like Reed & Prince. While these screws may have offered certain advantages in specific applications, their limited availability and higher cost made them less competitive in the broader market.
Versatility Versus Specialization: Standardization favored screw designs that could be used across a wide range of applications. The Phillips screw, with its ability to handle various materials and torque levels, fit this requirement perfectly. Specialized screws like Reed & Prince, which were often preferred for their initial grip, lost ground as manufacturers sought to simplify their operations and reduce inventory costs.
Reed & Prince vs. Phillips: A Comparative Analysis
To fully understand the transition, it's essential to compare the relative advantages and disadvantages of each screw type.
Feature | Reed & Prince | Phillips |
---|---|---|
Head Design | Sharply pointed recess, symmetrical | Rounded recess, symmetrical |
Initial Grip | Excellent | Good |
Cam-Out Resistance | Low (prone to cam-out) | Moderate (engineered cam-out to prevent overtightening) |
Manufacturing Cost | Higher | Lower |
Availability | Limited | Widespread |
Torque Application | Less suitable for high-torque applications | More suitable for high-torque applications |
In conclusion, the decline of the Reed & Prince screw was not due to a single factor, but rather a combination of economic, technical, and market forces. The rise of the Phillips screw, with its superior performance and widespread availability, ultimately eclipsed the Reed & Prince, marking a significant shift in the evolution of fastening technology.
Reed & Prince Today: Finding Needles in a Haystack
Reed & Prince screws, a once-ubiquitous fastener, often escape the notice of the modern craftsman. Yet, their distinctive design and historical prevalence make them a subject worthy of examination. Understanding their characteristics is vital for anyone engaged in restoration, historical preservation, or simply appreciating the evolution of fastener technology. But where does one find these specialized screws today, and what considerations should guide their acquisition?
The Quest for Authentic Reed & Prince Fasteners
The unfortunate reality is that widespread modern manufacturing of Reed & Prince screws is limited. Unlike their Phillips counterparts, which still enjoy mass production, these screws have largely faded from contemporary catalogs.
However, hope remains for those seeking authentic replacements. The first step is to determine if any manufacturers still produce them.
Modern Production: A Rare Find
Genuine, newly manufactured Reed & Prince screws are exceptionally rare. Dedicated research may uncover niche manufacturers or specialized suppliers catering to specific industries, such as vintage aircraft restoration.
These sources often involve custom orders and higher costs, reflecting the specialized nature of the product. Extensive searching and contacting fastener specialists may be necessary to verify the authenticity and quality of any purported new-production Reed & Prince screws.
Sourcing from the Secondary Market
The most common avenues for obtaining Reed & Prince screws lie within the secondary market. Online marketplaces, like eBay, and specialized vintage hardware suppliers are key resources.
Navigating Online Marketplaces and Specialty Suppliers
eBay and similar platforms host a fluctuating inventory of used and potentially new-old-stock Reed & Prince screws. Careful examination of listings is paramount, scrutinizing photographs and descriptions for telltale signs of authenticity.
Vintage hardware suppliers, often catering to antique furniture or classic car restoration, may also stock these screws. Their expertise can be invaluable in identifying genuine articles, but prices may reflect their specialized knowledge and curated inventory.
Identifying Genuine Reed & Prince Screws
Distinguishing authentic Reed & Prince screws from similar-looking fasteners, or outright imitations, requires a discerning eye. The crucial element is the tip of the driver bit, which is sharply pointed compared to other screw types, such as Phillips.
Key Identification Tips
- Pointed Tip: The most distinctive characteristic is the sharply pointed tip of the screw recess. This contrasts with the blunter tip of a Phillips screw.
- Flank Angle: Reed & Prince screws have a 45-degree flank angle, differing from Phillips screws.
- Head Markings: Original screws may exhibit manufacturer markings, though these can be faint or absent on older examples. The letters "RP" might be visible with magnification.
- Material and Finish: Inspect the material and finish for consistency with the era of manufacture. Anachronistic finishes (e.g., bright zinc plating on screws from the 1930s) are red flags.
Cost and Availability Considerations
Due to their scarcity, Reed & Prince screws command a premium compared to modern fasteners. Prices can vary significantly depending on size, material, condition, and source.
Expect to pay several times more for a Reed & Prince screw than for a comparable Phillips screw. Availability can also be unpredictable, requiring patience and persistence in the search. Purchasing large lots of reclaimed screws might be economical, but requires careful sorting and inspection.
Alternative Screw Types
When authentic Reed & Prince screws are unavailable or cost-prohibitive, consider alternative screw types that preserve the aesthetic and functionality of the original design.
Substitution Strategies
-
Slotted Screws: In some applications, slotted screws offer a visually similar alternative, particularly when the screw head is partially concealed.
-
Modified Phillips Screws: Carefully filing or grinding the tip of a Phillips screwdriver can yield a closer fit with a Reed & Prince screw, though this is not ideal.
-
Cosmetic Solutions: For purely cosmetic applications, consider using modern screws and covering the heads with decorative caps or faux Reed & Prince heads.
Ultimately, the choice of replacement screws depends on the specific project requirements, budget constraints, and the desired level of historical accuracy. While the quest for genuine Reed & Prince screws can be challenging, the satisfaction of restoring a piece of history with appropriate fasteners is often well worth the effort.
Video: Reed & Prince Screws: History & Where to Buy Them
FAQs: Reed & Prince Screws
What is the difference between Reed & Prince and Phillips head screws?
Reed & Prince screws and Phillips head screws appear similar, but are not interchangeable. Reed & Prince has a sharper, more pointed 45-degree point, while Phillips has a more rounded 68-degree point. Trying to use a Phillips screwdriver on reed & prince screws will often result in stripping the head.
Why were Reed & Prince screws invented?
The reed & prince screws design aimed to improve upon earlier screw designs by offering a more secure drive, reducing cam-out (slipping of the screwdriver), and ultimately speeding up assembly line processes, particularly in industries like aircraft manufacturing where precision and speed were critical.
Are reed & prince screws still commonly used today?
While not as ubiquitous as Phillips or slotted screws, reed & prince screws are still encountered, particularly in older equipment, boats, and classic cars. You may also find them in restoration projects where maintaining historical accuracy is important.
Where can I buy reed & prince screws and screwdrivers?
Finding reed & prince screws and screwdrivers can be challenging. Specialist fastener suppliers, online marketplaces like eBay or Amazon (search for "reed and prince"), and antique tool dealers are your best bets. Be sure to verify the driver type matches the reed & prince screws you're purchasing.
So, whether you're restoring a vintage radio or just appreciate the finer points of obscure fasteners, hopefully, this has shed some light on the world of Reed & Prince screws. They might be a bit harder to find than your standard Phillips head, but the hunt can be part of the fun – happy screwing!