Eutectic Point: Lowering Melting Temperatures Explained
The phenomenon of eutectic point, crucial in metallurgy and materials science, represents the specific composition at which a mixture of substances achieves its lowest possible melting temperature. Phase diagrams, essential tools for understanding material behavior, illustrate how the eutectic point defines a unique invariant reaction where a liquid transforms directly into two or more solid phases. Researchers at organizations such as ASM International extensively study eutectic alloys to leverage their enhanced properties and controlled solidification characteristics. Such understanding of the eutectic point is essential in diverse applications, ranging from soldering, where alloys like tin-lead are employed, to the creation of advanced composite materials with tailored thermal behaviors.
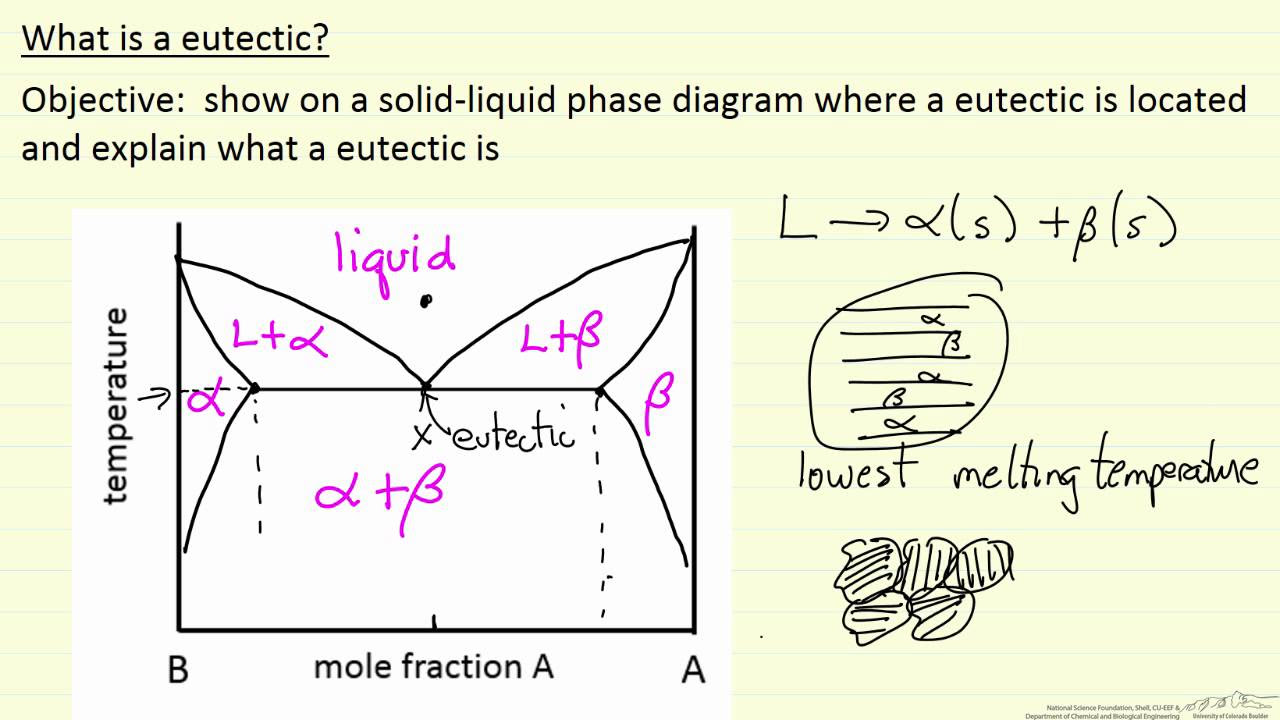
Image taken from the YouTube channel LearnChemE , from the video titled What is a Eutectic? .
Eutectic systems are pivotal in materials science and engineering, dictating the behavior of numerous alloys and composite materials. Understanding these systems is paramount for materials selection, optimizing processing techniques, and ultimately controlling the properties of the final product.
This introductory section lays the groundwork for a comprehensive exploration of eutectic transformations. We will delve into the fundamental concepts that define these systems, providing the essential context for appreciating their practical significance.
Defining Eutectic Systems and Their Significance
A eutectic system refers to a mixture of two or more components that solidifies at a lower temperature than any other composition of the same components. This specific composition, known as the eutectic composition, transforms directly from a liquid to a solid mixture of phases at a constant temperature – the eutectic temperature.
The importance of eutectic systems stems from their ability to tailor material properties. For instance, the sharp melting point of eutectic alloys can be exploited for applications like soldering, where precise temperature control is crucial.
Furthermore, the microstructure resulting from eutectic solidification often exhibits enhanced mechanical properties. These properties can include increased strength, ductility, or even improved corrosion resistance.
Examples highlighting the importance of eutectic behavior abound in various industries. Consider the aluminum-silicon alloys used extensively in the automotive industry for engine blocks.
The eutectic composition of this system offers superior castability, allowing for intricate shapes to be manufactured with ease. The properties of the resulting alloy after proper heat treatment are beneficial for the intended application.
Phase Diagrams: A Visual Guide to Material Behavior
Phase diagrams are indispensable tools for materials scientists and engineers. They serve as visual roadmaps illustrating the relationships between temperature, composition, and the phases present in a material system under equilibrium conditions.
These diagrams enable us to predict the phases that will form, their compositions, and their relative amounts at a given temperature and composition.
A simple binary phase diagram, depicting a system with two components, typically plots temperature on the vertical axis and composition on the horizontal axis. Regions within the diagram represent single-phase fields, where only one phase is stable.
Boundaries between these regions indicate phase transformations, such as melting or solidification. By carefully analyzing a phase diagram, one can determine the optimal processing conditions to achieve desired microstructures and properties.
Phase Equilibrium: The Foundation of Phase Stability
Phase equilibrium is the cornerstone of understanding phase transformations, including eutectic reactions. It defines the state where the chemical potential of each component in the system is the same in all phases.
In simpler terms, at equilibrium, there is no net driving force for a component to move from one phase to another. This state is governed by thermodynamic principles, specifically the minimization of the Gibbs free energy of the system.
The Gibbs free energy considers both the enthalpy (heat content) and entropy (disorder) of the system, dictating which phases are stable under given conditions of temperature and pressure. Understanding these principles allows for predicting the stability of different phases and the driving forces for phase transformations.
The Eutectic Point: The Lowest Melting Point
The eutectic point represents a singular location on a phase diagram where the liquid phase transforms directly into two or more solid phases simultaneously.
This point corresponds to the lowest melting temperature within the alloy system. At this precise composition and temperature, the liquid solidifies into a characteristic microstructure, often exhibiting a fine, intermixed arrangement of the constituent phases.
The eutectic point is strategically significant in material design. By utilizing eutectic compositions, it becomes possible to achieve lower processing temperatures, reducing energy consumption and minimizing thermal stresses during manufacturing.
Moreover, materials designed around the eutectic composition can exhibit improved castability, allowing for the creation of complex shapes with greater ease and precision.
Key Concepts Governing Eutectic Transformations
Eutectic systems are pivotal in materials science and engineering, dictating the behavior of numerous alloys and composite materials. Understanding these systems is paramount for materials selection, optimizing processing techniques, and ultimately controlling the properties of the final product. This introductory section lays the groundwork for a deep dive into the core principles governing eutectic transformations, illuminating the mechanisms that drive their behavior and influence the resulting material characteristics.
Liquidus and Solidus Lines: Defining the State of Matter
The liquidus and solidus lines are fundamental boundaries on a phase diagram, demarcating the temperature ranges within which a substance exists in either a completely liquid, completely solid, or a mixed state.
The liquidus line represents the temperature above which the alloy is entirely liquid. Crossing this line from a higher temperature initiates the solidification process.
Conversely, the solidus line signifies the temperature below which the alloy is entirely solid.
The region nestled between these two lines represents a coexistence zone, where both liquid and solid phases are present in equilibrium. The proportions of each phase within this region are dictated by the temperature and overall composition of the alloy, a principle quantified by the lever rule. Understanding the relationship of temperature to the liquidus and solidus lines is paramount to controlling alloy solidification.
Lamellar Structure: The Signature of Eutectic Solidification
A distinguishing feature of eutectic solidification is the formation of a lamellar structure. This characteristic microstructure is comprised of fine, alternating layers of the two solid phases that emerge simultaneously at the eutectic point.
The formation mechanism is driven by the need to minimize the diffusion distances of the constituent elements as they transition from the liquid to the solid phases. As the liquid cools to the eutectic temperature, nucleation of both phases occurs concurrently. The cooperative growth of these nuclei results in the formation of the intertwined lamellae.
The spacing between the lamellae plays a critical role in determining the mechanical properties of the alloy. Finer lamellar spacing generally leads to increased strength and hardness. This is because the interfaces between the lamellae act as obstacles to dislocation motion, hindering plastic deformation.
Control over lamellar spacing can be achieved through manipulation of cooling rates, with faster cooling promoting finer structures.
Microstructure Evolution: Shaping Material Properties
The microstructure of a material, which encompasses the size, shape, and distribution of its constituent phases, profoundly influences its properties. Eutectic transformations serve as a powerful tool for manipulating the final microstructure of an alloy.
The specific path of the transformation, influenced by factors such as cooling rate and alloy composition, dictates the resulting microstructure. This, in turn, governs crucial material attributes like strength, ductility, corrosion resistance, and thermal conductivity.
For instance, rapid solidification can lead to the formation of metastable microstructures with enhanced properties. In contrast, slow cooling allows for the development of equilibrium microstructures with potentially different characteristics.
Eutectic transformations offer a versatile means of tailoring the properties of a material to meet specific application requirements. Microstructural analysis tools, such as optical microscopy and scanning electron microscopy, are crucial for visualizing and characterizing these microstructures.
Solid Solution Formation: Modifying Alloy Properties
Solid solutions are formed when one or more elements dissolve in a crystalline solid, creating a homogenous mixture at the atomic level. In eutectic systems, solid solution formation can significantly modify the properties of the resulting alloy.
The introduction of solute atoms into the solvent lattice can induce lattice strain, which strengthens the material by impeding dislocation movement. This phenomenon, known as solid solution strengthening, is a widely used technique for enhancing the mechanical properties of alloys.
The extent of solid solution formation is governed by the solubility limits of the elements involved, as dictated by the phase diagram. Factors such as atomic size, electronegativity, and crystal structure influence the degree of solid solubility.
For example, the addition of zinc to copper in brass alloys results in a solid solution, leading to increased strength and improved corrosion resistance compared to pure copper. Therefore, controlling solid solution formation is critical to engineering desirable alloy properties.
Eutectic Alloys: Composition, Microstructure, and Applications
Eutectic systems are pivotal in materials science and engineering, dictating the behavior of numerous alloys and composite materials. Understanding these systems is paramount for materials selection, optimizing processing techniques, and ultimately controlling the properties of the final product. This section delves into the specifics of eutectic alloys, exploring how compositional variations and the resulting microstructures dictate their applications.
Defining Alloys: A Symphony of Elements
At its core, an alloy is a metallic substance composed of two or more elements combined, where at least one of these elements is a metal.
This strategic blending of elements is undertaken to achieve properties that are superior or more desirable than those of the individual constituent metals.
Alloys can be broadly classified into two primary categories based on how the constituent atoms interact: substitutional and interstitial.
-
In substitutional alloys, atoms of one element replace atoms of another in the crystal lattice. This usually happens when the atom sizes and chemical properties are similar.
-
Interstitial alloys, on the other hand, involve smaller atoms fitting into the spaces between the larger atoms in the lattice.
Hypoeutectic and Hypereutectic Compositions: A Tale of Two Microstructures
The eutectic point represents a specific composition where an alloy solidifies directly from a liquid into a mixture of two or more solid phases simultaneously at a single temperature.
However, alloys rarely exist precisely at the eutectic composition. They often deviate, leading to the formation of either hypoeutectic or hypereutectic microstructures.
Hypoeutectic compositions are those that lie to the left of the eutectic point on the phase diagram. These alloys will initially solidify with a primary phase separating out from the liquid before the remaining liquid reaches the eutectic temperature.
As the temperature cools further, the remaining liquid transforms into the characteristic eutectic structure surrounding the primary phase.
Conversely, hypereutectic compositions are those that lie to the right of the eutectic point. In this case, the solidification process starts with the formation of a different primary phase compared to hypoeutectic alloys. Again, this initial solidification occurs before the system reaches the eutectic temperature.
The remaining liquid then solidifies into the eutectic structure, encasing the primary phase.
Understanding the influence of alloy composition on the resulting microstructure is crucial. The proportion and morphology of the primary phase and the eutectic structure significantly impact the mechanical properties, corrosion resistance, and overall performance of the alloy.
Visualizing Microstructural Differences
The following diagram illustrates the distinct microstructures formed in hypoeutectic, eutectic, and hypereutectic alloys:
[Note: Insert diagram here showing microstructures of hypoeutectic (α + eutectic), eutectic, and hypereutectic (β + eutectic) alloys]
-
Hypoeutectic: Notice the large grains of the alpha (α) phase surrounded by the finer eutectic structure.
-
Eutectic: Observe the fine, evenly distributed mixture of α and beta (β) phases.
-
Hypereutectic: Here, the beta (β) phase forms the larger grains embedded in the eutectic mixture.
Common Eutectic Alloy Systems: Real-World Examples
Eutectic alloys are not merely theoretical constructs; they are ubiquitous in everyday applications. Their specific properties, derived from their unique microstructures, make them indispensable in various industries.
Solder: The Joining Master
Eutectic solder alloys are characterized by their low melting temperatures, a direct consequence of their eutectic composition.
This property is critical in electronics assembly, where it minimizes the risk of damaging sensitive components during soldering processes.
Traditional lead-tin solders, such as the 63Sn/37Pb eutectic alloy, have been widely used, although lead-free alternatives are increasingly preferred due to environmental concerns.
Bronze (Copper-Tin Alloys): A Legacy of Craftsmanship
Bronze, a copper-tin alloy, exemplifies the importance of understanding phase diagrams in controlling material properties.
While not all bronze alloys are eutectic, manipulating the composition to approach a eutectic point can influence castability and strength.
The historical significance of bronze in toolmaking and artistry underscores the enduring relevance of eutectic principles.
Cast Iron (Iron-Carbon Alloys): Strength in Simplicity
Cast iron, an iron-carbon alloy with a carbon content exceeding 2%, utilizes the eutectic transformation extensively in casting processes.
The eutectic point in the iron-carbon system allows for the creation of alloys with excellent fluidity and castability, enabling the production of complex shapes with relative ease. Different types of cast iron, such as gray iron and ductile iron, rely on manipulating the microstructure through compositional control and heat treatment.
Aluminum Alloys: Lightweight Champions
Eutectic behavior plays a significant role in the design and processing of aluminum alloys.
Many aluminum alloys are designed to have compositions near a eutectic point. Doing this enhances their castability and can improve mechanical properties such as strength and ductility.
Aluminum-silicon alloys, for example, take advantage of the eutectic transformation to create lightweight components with good thermal conductivity, ideal for automotive and aerospace applications.
Experimental Techniques for Studying Eutectic Transformations
Eutectic systems are pivotal in materials science and engineering, dictating the behavior of numerous alloys and composite materials. Understanding these systems is paramount for materials selection, optimizing processing techniques, and ultimately controlling the properties of the final product. This requires a multifaceted approach, employing a range of experimental techniques to probe the intricacies of eutectic phase transformations.
Cooling Curve Analysis: Unveiling the Thermal Signature
Cooling curve analysis stands as a fundamental technique for experimentally determining the eutectic point. This method involves monitoring the temperature of a material as it cools from a liquid state, plotting the temperature as a function of time.
The resulting cooling curve provides a thermal signature of the solidification process.
During the solidification of a pure metal, the cooling curve exhibits a distinct plateau at the freezing temperature. This plateau signifies the release of latent heat as the material undergoes a phase change from liquid to solid.
Eutectic solidification exhibits a similar, though often less pronounced, plateau at the eutectic temperature.
This plateau occurs because the simultaneous solidification of the two (or more) phases releases heat. The presence and temperature of this plateau are key indicators of the eutectic point. Deviations from ideal behavior can occur due to factors such as cooling rate and alloy purity.
Interpreting Cooling Curves
Careful analysis of the cooling curve is required. The precise onset and duration of the eutectic plateau provides valuable data on the eutectic temperature and the kinetics of the transformation. More sophisticated analyses can also extract information about the degree of undercooling and the rate of nucleation.
The Lever Rule: Quantifying Phase Fractions
The lever rule is an indispensable tool for determining the relative amounts of each phase present in a two-phase region of a phase diagram at a given temperature and composition. This rule is particularly relevant in eutectic systems, where understanding the phase fractions is critical for predicting material properties.
The lever rule utilizes the principle of mass balance to calculate the proportion of each phase. It is based on the tie line, which is a horizontal line drawn across the two-phase region at the temperature of interest.
The lever rule states that the fraction of one phase is proportional to the length of the tie line segment opposite that phase, divided by the total length of the tie line.
Applying the Lever Rule
To apply the lever rule effectively, an accurate phase diagram is required. The overall alloy composition and the compositions of the individual phases at the temperature of interest must be known.
By performing these calculations at various temperatures, one can develop a comprehensive understanding of the phase evolution during cooling or heating.
Undercooling, Nucleation, and Crystal Growth: Solidification Dynamics
The solidification process in eutectic systems is governed by the interplay of undercooling, nucleation, and crystal growth. Undercooling refers to the phenomenon where a liquid cools below its equilibrium freezing temperature without solidifying. This is a prerequisite for nucleation, the formation of tiny, stable nuclei of the solid phases within the liquid.
The extent of undercooling dictates the driving force for nucleation. A greater degree of undercooling generally leads to a higher nucleation rate.
Following nucleation, the nuclei grow into larger crystals, a process known as crystal growth.
Microstructural Consequences
The interplay of these three factors determines the final microstructure of the eutectic alloy. High nucleation rates coupled with slow growth rates result in fine, dispersed microstructures. Conversely, low nucleation rates and fast growth rates lead to coarser microstructures.
The control of these parameters through techniques such as melt superheating, inoculation, and rapid solidification allows for precise tailoring of alloy properties. This is because the microstructure of the eutectic alloys strongly impacts their properties.
Video: Eutectic Point: Lowering Melting Temperatures Explained
Frequently Asked Questions
How does the eutectic point lower melting temperatures?
The eutectic point represents a specific mixture of two or more substances that melts at the lowest possible temperature compared to any other mixture ratio. This lowered melting temperature occurs because the presence of the other components disrupts the crystal lattice structure of each individual component, making it easier to break down and melt.
Why is the eutectic point important in soldering?
Soldering often utilizes eutectic alloys because their low melting point facilitates easier and more reliable joining of metals. At the eutectic point, the solder melts completely at a single temperature, ensuring a strong and consistent bond without a pasty melting range.
What happens if the mixture is not at the exact eutectic point?
If the mixture deviates from the precise composition defining the eutectic point, the melting behavior changes. One component will start to melt at a higher temperature, resulting in a two-phase region where both solid and liquid coexist over a range of temperatures before the remaining mixture melts completely.
Can the eutectic point be predicted accurately?
While thermodynamic models and phase diagrams can help predict the eutectic point, experimental verification is usually necessary. Factors like impurities and non-equilibrium conditions can influence the actual eutectic point observed in practice, requiring adjustments to theoretical calculations.
So, next time you're wondering how seemingly incompatible materials can melt together at a surprisingly low temperature, remember the eutectic point! It's a nifty little phenomenon that's constantly being leveraged to create new materials and improve existing processes. Pretty cool, right?