Discharge Coefficient: The Ultimate Guide You Need to Know
The discharge coefficient, a dimensionless number, quantifies the reduction in flow caused by friction and contraction within flow passages. Orifice plates, commonly utilized in flow measurement, exhibit a discharge coefficient value directly impacting the calculated flow rate. Fluid mechanics, a fundamental engineering discipline, provides the theoretical framework for understanding the discharge coefficient and its behavior in various applications. ASME (American Society of Mechanical Engineers), a prominent standards organization, offers guidelines and methodologies for determining the discharge coefficient in specific flowmeter designs, ensuring accuracy and reliability.
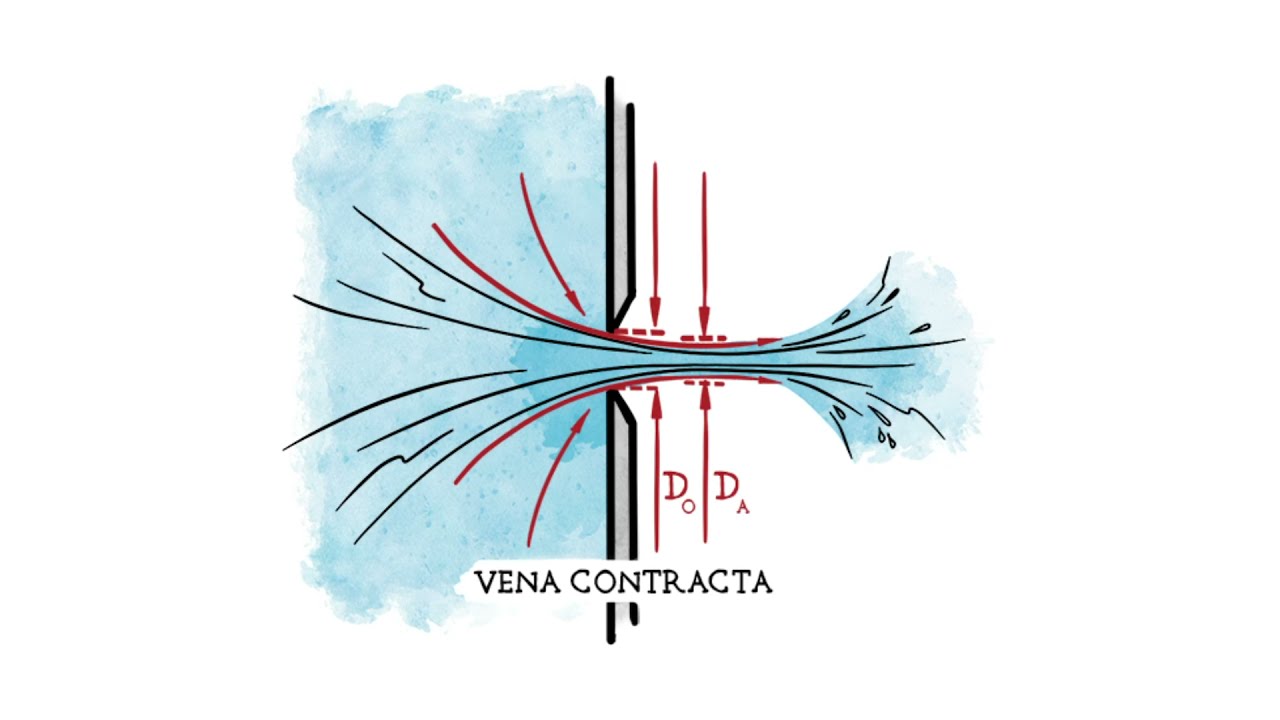
Image taken from the YouTube channel MeyerFire , from the video titled What is a Coefficient of Discharge? .
Accurate flow measurement forms the bedrock of countless engineering endeavors. From optimizing chemical processes to ensuring efficient water distribution, knowing precisely how much fluid is moving through a system is paramount. This is where the Discharge Coefficient (Cd) enters the picture.
It stands as a critical, yet often understated, parameter in the realm of flow measurement. Think of it as the correction factor that bridges the gap between theoretical calculations and messy reality. This guide aims to provide a comprehensive understanding of Cd, exploring its significance and diverse applications.
The Foundation: Flow Measurement & Its Significance
Flow measurement is the quantification of fluid movement through a defined space, typically a pipe or channel. Its importance spans numerous disciplines:
-
Chemical Engineering: Ensuring precise reactant ratios for optimal product yield.
-
Civil Engineering: Monitoring water distribution networks and wastewater treatment plants.
-
Mechanical Engineering: Optimizing the performance of engines and hydraulic systems.
-
Aerospace Engineering: Fuel flow management for aircraft and spacecraft.
Without accurate flow measurement, processes become inefficient, products become inconsistent, and systems become unreliable.
Defining the Discharge Coefficient (Cd)
The Discharge Coefficient (Cd) is a dimensionless number that represents the ratio of actual flow rate to the theoretical flow rate through a device like an orifice plate, nozzle, or venturi meter. In simpler terms, it accounts for the inevitable energy losses that occur in real-world flow scenarios.
These losses stem from friction, viscosity, and other non-ideal conditions that deviate from perfect theoretical models. Cd values typically range between 0 and 1, with higher values indicating less energy loss and closer agreement between actual and theoretical flow rates.
Purpose & Scope of This Guide
This guide is designed to be a comprehensive resource for anyone involved in flow measurement and fluid dynamics. Whether you're a seasoned engineer or a student just starting to learn, we aim to provide clarity and practical insights into the Discharge Coefficient.
We will explore the factors that influence Cd, examine its application in different flow measurement devices, discuss methods for determining its value, and highlight its real-world impact. By the end of this guide, you will have a solid understanding of Cd and its critical role in achieving accurate and reliable flow measurement.
Decoding the Discharge Coefficient: What It Is and Why It Matters
The Discharge Coefficient (Cd) might seem like an obscure technicality, but it is a vital link between theoretical fluid dynamics and the practical realities of engineering. It's the factor that acknowledges that pipes aren't perfectly smooth, fluids aren't perfectly ideal, and the world rarely adheres perfectly to our equations.
A Formal Definition
At its core, the Discharge Coefficient (Cd) is a dimensionless number that quantifies the efficiency of a flow device, such as an orifice plate, nozzle, or venturi meter. Specifically, it represents the ratio of the actual flow rate observed in a real-world setup to the theoretical flow rate predicted by idealized equations. This seemingly simple ratio encapsulates a wealth of information about the fluid's behavior and the device's performance.
Cd's Role: Accounting for Energy Losses
The significance of Cd stems from its ability to account for the inevitable energy losses that occur during fluid flow. In a perfect, theoretical world, fluid would flow unimpeded, with no friction or turbulence. However, real-world scenarios introduce complexities that diminish the flow rate.
These complexities include:
- Friction between the fluid and the pipe walls.
- Viscous effects within the fluid itself.
- The formation of eddies and turbulence downstream of flow constrictions.
Cd acts as a correction factor, essentially scaling down the theoretical flow rate to reflect the actual flow rate, considering these energy losses.
Ideal Flow vs. Real Flow: Bridging the Gap
The need for Cd arises from the fundamental difference between ideal and real fluid flow. Ideal flow is a theoretical construct, assuming:
- Inviscid fluid (no viscosity).
- Incompressible fluid (constant density).
- Steady flow (constant velocity over time).
- No energy losses due to friction or turbulence.
While ideal flow provides a useful starting point for analysis, it drastically simplifies reality. Real flow, on the other hand, is characterized by:
- Viscosity.
- Compressibility (in some cases).
- Unsteady flow (fluctuations in velocity).
- Significant energy losses.
Cd bridges the gap between these two paradigms, allowing engineers to apply theoretical principles to practical situations with greater accuracy. Without Cd, calculations would significantly overestimate the actual flow rate, leading to design flaws, inefficiencies, and even safety hazards.
The Formulaic Relationship
The relationship between actual flow rate (Qactual), theoretical flow rate (Qtheoretical), and the Discharge Coefficient (Cd) is expressed as a simple equation:
Cd = Qactual / Qtheoretical
This equation highlights the direct proportionality between Cd and the efficiency of the flow device. A Cd value close to 1 indicates minimal energy losses and a highly efficient device, while a lower Cd value suggests greater energy dissipation and a less efficient design. Understanding and applying this relationship is paramount for accurate flow measurement and control in any engineering application.
Key Influencers: Factors Affecting the Discharge Coefficient
Having defined the Discharge Coefficient (Cd) and established its significance in bridging the gap between ideal and real-world fluid flow, it's crucial to understand the factors that cause Cd to deviate from unity. These factors are interconnected and their influence on Cd can be complex, requiring careful consideration in flow measurement and control applications. Let's examine these key influencers.
The Reynolds Number (Re) and Flow Regime
The Reynolds Number (Re) is a dimensionless quantity that describes the ratio of inertial forces to viscous forces within a fluid. It is a primary indicator of the flow regime, determining whether the flow is laminar, transitional, or turbulent.
At low Reynolds numbers, viscous forces dominate, resulting in laminar flow characterized by smooth, orderly fluid motion. In this regime, the Discharge Coefficient tends to be more stable and predictable.
As the Reynolds number increases, inertial forces become more significant, leading to the formation of turbulence. Turbulent flow is characterized by chaotic, swirling eddies and increased energy dissipation. This, in turn, impacts the Cd value, generally decreasing it due to enhanced energy losses.
The relationship between Re and Cd is not always linear and can be influenced by other factors, but understanding the flow regime is crucial for selecting the appropriate Cd value or correlation.
Pressure Differential (ΔP)
The pressure differential (ΔP) across a flow restriction device, such as an orifice plate, is directly related to the flow rate. However, its impact on the Discharge Coefficient is somewhat more nuanced.
While ΔP itself doesn't directly alter the fluid properties, a higher ΔP can lead to increased flow velocities and potentially exacerbate the effects of turbulence and cavitation, especially in liquid flows.
Cavitation, the formation and subsequent collapse of vapor bubbles, can significantly reduce the Cd value and damage the flow device. Therefore, selecting a flow device and operating conditions that avoid cavitation is critical.
Furthermore, the accuracy of the pressure measurement itself can influence the calculated Cd value.
Small errors in ΔP measurement can translate into significant errors in the determined Cd, particularly at low flow rates.
Geometric Considerations
The physical dimensions and shape of the flow device and its surrounding piping significantly influence the Discharge Coefficient.
Orifice Plate Geometry
For orifice plates, the ratio of the orifice diameter to the pipe diameter (beta ratio) is a critical parameter. Different beta ratios result in varying flow patterns and energy losses, thus impacting the Cd value.
The thickness of the orifice plate also plays a role. A thicker plate can create a longer flow path, increasing friction and reducing the Cd. The sharpness of the orifice edge is also important; a sharp edge promotes a well-defined flow separation, which is essential for consistent Cd values.
Inlet and Outlet Pipe Geometry
The geometry of the upstream and downstream piping can affect the flow profile entering and exiting the flow device.
Straight pipe runs of sufficient length are typically required to ensure a fully developed flow profile and minimize disturbances that could affect the Cd. Bends, elbows, and other fittings near the flow device can create swirl and turbulence, leading to inaccurate flow measurements.
Fluid Properties: Viscosity and Density
Fluid properties, particularly viscosity and density, directly influence the fluid's behavior and its interaction with the flow device.
Viscosity is a measure of a fluid's resistance to flow. Higher viscosity fluids experience greater frictional losses, which can decrease the Cd value.
Density affects the fluid's inertia and its response to pressure gradients. Changes in density, particularly due to temperature variations, can also impact the Cd.
It's essential to consider the operating temperature and pressure conditions when selecting or calculating the Cd, as these factors can significantly affect fluid properties.
Surface Roughness
The roughness of the internal surfaces of the pipe and the flow device contributes to frictional losses and turbulence.
Rougher surfaces create more friction, impeding flow and reducing the Cd value. This effect is more pronounced at higher flow rates and with more viscous fluids.
Regular inspection and maintenance of the flow device and piping are crucial to prevent excessive build-up of scale or corrosion, which can increase surface roughness and affect the accuracy of flow measurements.
Cd in Action: Discharge Coefficients in Different Flow Measurement Devices
Having established the importance of the Discharge Coefficient and explored the factors that influence its value, it's time to examine how it's applied in real-world flow measurement scenarios. Each type of flow measurement device possesses unique characteristics that affect the Discharge Coefficient. Let's delve into the specifics of how Cd is utilized in various devices, including orifice plates, venturi meters, flow nozzles, and control valves.
Orifice Plates: Cd in Sharp-Edged Simplicity
Orifice plates, known for their simple design and ease of installation, are a staple in flow measurement. But this simplicity comes with a trade-off: a relatively low Discharge Coefficient compared to other devices.
Cd Usage in Orifice Plate Calculations
The Discharge Coefficient (Cd) in orifice plate calculations serves as a correction factor in the flow rate equation. The ideal flow rate is multiplied by Cd to account for the energy losses caused by the flow contraction and subsequent expansion as the fluid passes through the orifice. Without Cd, the calculated flow rate would be significantly higher than the actual flow rate.
Typical Cd Values for Different Designs
Typical Cd values for orifice plates range from 0.60 to 0.85. This range can vary based on factors like the beta ratio (the ratio of the orifice diameter to the pipe diameter) and the Reynolds number. Different tapping arrangements (corner, flange, D-D/2) can also slightly influence the Cd value.
Influence of the Beta Ratio
The beta ratio is a critical design parameter for orifice plates. A lower beta ratio (smaller orifice) results in a higher pressure drop and a lower Cd. Conversely, a higher beta ratio (larger orifice) leads to a lower pressure drop and a higher Cd, approaching unity as the orifice diameter nears the pipe diameter. Selecting the appropriate beta ratio is essential for achieving accurate flow measurement.
Venturi Meters: Streamlined for High Efficiency
Venturi meters stand out due to their streamlined design. This design minimizes energy losses and results in a higher Discharge Coefficient compared to orifice plates.
Cd Usage in Venturi Meter Calculations
Like orifice plates, Cd in Venturi meter calculations corrects for deviations from ideal flow. However, because Venturi meters are designed to minimize turbulence and energy dissipation, the Cd value is closer to 1. This translates to more accurate flow measurements with lower unrecoverable pressure losses.
Typical Cd Values and Advantages
Venturi meters typically have Cd values ranging from 0.95 to 0.99. This high Cd value is a significant advantage, especially in applications where minimizing pressure loss is critical. For example, in pumping systems, reduced pressure loss translates directly into lower energy consumption.
High Cd Values Due to Streamlined Design
The streamlined design of the Venturi meter, with its converging inlet, throat, and diverging outlet, is the key to its high Cd value. This shape minimizes flow separation and turbulence, reducing energy losses and resulting in a more efficient flow measurement.
Flow Nozzles: Bridging the Gap
Flow nozzles offer a performance profile that falls between orifice plates and Venturi meters. They are characterized by a smooth, contoured inlet that gradually converges to a throat, followed by an abrupt expansion.
Cd Usage in Flow Nozzle Calculations
The Discharge Coefficient is used similarly in flow nozzle calculations to correct for non-ideal flow behavior. Flow Nozzles generate less permanent pressure loss when compared to Orifice Plates.
Typical Cd Values and Applications
Typical Cd values for flow nozzles generally range from 0.92 to 0.99, offering a balance between accuracy and pressure loss. They are frequently used in high-velocity flow applications, like steam flow measurement, where the erosion resistance of the nozzle's robust design is advantageous.
Flow Nozzles vs. Orifice Plates and Venturi Meters
Compared to orifice plates, flow nozzles offer a higher Cd and lower pressure loss, albeit at a higher cost. While they don't quite match the efficiency of Venturi meters, flow nozzles are more compact and easier to install, making them a suitable choice for applications where space is limited.
Control Valves: Cd as a Valve Performance Metric
While not strictly a "flow measurement" device, Control Valves rely on a Discharge Coefficient (often referred to as a flow coefficient or Cv) to quantify their flow capacity and ensure proper sizing.
Cd in Sizing Control Valves
In control valve sizing, Cd (or Cv) is crucial for determining the valve's ability to pass a required flow rate at a given pressure drop. A valve with a higher Cd can pass more fluid at the same pressure drop compared to a valve with a lower Cd.
Valve Designs and Flow Characteristics
Different valve designs (globe, ball, butterfly, etc.) exhibit varying Cd values and flow characteristics. Globe valves, known for precise control, generally have lower Cd values than ball valves, which offer higher flow capacity. Understanding these characteristics is critical for selecting the right valve for a specific application.
Unlocking Cd: Methods for Determination
The Discharge Coefficient, Cd, is not a fixed property etched in stone. Its value fluctuates based on various factors. Understanding how to determine Cd is just as crucial as understanding what it represents. Thankfully, we have several methods at our disposal.
These range from hands-on experimentation to sophisticated computational modeling. Each approach offers unique advantages and limitations. The selection depends on the required accuracy, available resources, and complexity of the flow system.
Calibration: The Gold Standard of Experimental Cd Determination
Calibration represents the most direct, and often most accurate, method for determining the Discharge Coefficient. It involves physically measuring the actual flow rate through a device under controlled conditions. This is then compared against the theoretical flow rate, calculated using idealized equations.
The ratio of these two values yields the experimental Cd.
The Calibration Process: A Step-by-Step Approach
The basic calibration setup includes the flow device being tested, a well-defined fluid supply, accurate pressure and temperature sensors, and a reliable flow measurement system.
The process typically involves:
- Establishing a steady flow through the device.
- Measuring the pressure differential across the device.
- Simultaneously measuring the actual flow rate using a calibrated flow meter or weighing tank.
- Calculating the theoretical flow rate based on the measured pressure differential and device geometry.
- Calculating the Cd value as the ratio of the actual flow rate to the theoretical flow rate.
This process is repeated for a range of flow rates to generate a Cd curve.
Advantages and Disadvantages of Calibration
Advantages: High accuracy, direct measurement of Cd under specific operating conditions, and the ability to account for complex flow phenomena.
Disadvantages: Can be expensive and time-consuming, requires specialized equipment and expertise, and the Cd value is only valid for the specific conditions under which the calibration was performed.
Empirical Correlations: Estimating Cd with Equations
Empirical correlations offer a convenient way to estimate Cd values. These are equations derived from experimental data.
They relate Cd to various dimensionless parameters, such as the Reynolds number, beta ratio (for orifice plates), and geometric parameters. These correlations are specific to the type of flow device.
The Appeal of Empirical Correlations
Empirical correlations provide a quick and cost-effective means of estimating Cd. They eliminate the need for physical calibration. However, it's crucial to understand the limitations of these correlations.
Limitations of Empirical Correlations
- Accuracy depends on the quality and range of the experimental data used to develop the correlation.
- Extrapolation beyond the validated range can lead to significant errors.
- They may not accurately capture complex flow phenomena or device-specific variations.
- Always check the validity range of the correlation before using it.
CFD Simulations: Predicting Cd with Computational Fluid Dynamics
Computational Fluid Dynamics (CFD) offers a powerful alternative for determining Cd values. CFD uses numerical methods to solve the governing equations of fluid flow.
This simulates the flow field within the device.
Harnessing the Power of Simulation
By simulating the flow, engineers can predict the pressure drop and flow rate. This allows for the calculation of Cd. CFD simulations can handle complex geometries and flow conditions.
It provides detailed insights into the flow behavior.
Advantages and Disadvantages of CFD
Advantages: Ability to analyze complex geometries and flow conditions, provides detailed flow field information, and allows for virtual prototyping and optimization.
Disadvantages: Requires specialized software and expertise, computationally intensive, and the accuracy of the results depends on the quality of the mesh, turbulence model, and boundary conditions used in the simulation.
The accuracy of CFD simulations must be validated against experimental data.
Real-World Impact: Practical Applications of the Discharge Coefficient
Having explored the intricacies of determining Cd, it's time to shift our focus to the tangible benefits that a solid understanding of this coefficient brings to various engineering applications. The Discharge Coefficient isn't just a theoretical value; it's a critical parameter that directly influences the accuracy, efficiency, and cost-effectiveness of numerous systems.
The Ubiquitous Role of Cd in Flow Metering
Flow metering stands as a cornerstone of countless industrial processes. From monitoring the flow of crude oil in pipelines to regulating the supply of natural gas to homes, accurate flow measurement is indispensable. In these scenarios, the Discharge Coefficient plays a pivotal role.
By accurately accounting for the deviations from ideal flow conditions, Cd ensures that flow meters provide reliable and precise readings.
This accuracy directly translates into better inventory management, optimized resource allocation, and improved process control. Inaccurate flow measurement, stemming from an incorrect Cd, can lead to significant financial losses or even compromise safety.
Process Control Optimization: Refining Efficiency with Cd
In complex process industries like chemical plants and refineries, maintaining precise control over fluid flows is paramount. Control valves, guided by sophisticated control loops, regulate these flows to ensure optimal operating conditions.
The Discharge Coefficient is crucial in selecting and sizing these control valves. A valve with an inappropriately chosen Cd can lead to instability in the control loop, resulting in oscillations, overshooting, or sluggish response.
This translates to inefficiencies, increased energy consumption, and potentially, off-spec product. Accurate Cd values allow for optimized control loop tuning, leading to smoother, more efficient, and more responsive process control. This translates directly into higher product quality, reduced waste, and enhanced profitability.
Hydraulic Design: Minimizing Losses and Maximizing Efficiency
The design of efficient piping systems hinges on a thorough understanding of fluid dynamics. Engineers strive to minimize energy losses due to friction, turbulence, and other non-ideal flow phenomena.
The Discharge Coefficient is instrumental in predicting these losses and optimizing the system design. By accurately estimating the pressure drop across various components, such as valves, fittings, and orifices, engineers can select appropriate pipe sizes, pump capacities, and other system parameters.
This results in reduced energy consumption, lower operating costs, and improved system reliability. A well-designed piping system, informed by accurate Cd values, minimizes pumping power requirements, thus contributing to significant cost savings over the system's lifespan.
The Bottom Line: Cost Savings and Efficiency Gains
The correct understanding and application of the Discharge Coefficient have a cascading effect on cost savings and efficiency improvements. From reducing raw material waste in manufacturing processes to minimizing energy consumption in fluid transport systems, the benefits are substantial and far-reaching.
By investing in accurate Cd determination and incorporating it into design and operational practices, organizations can unlock significant economic advantages and enhance their overall performance. The key is recognizing that Cd is not merely a correction factor, but a vital parameter for optimizing fluid flow systems and achieving operational excellence.
Real-world applications underscore the significance of a well-understood Discharge Coefficient, but even with the best intentions, pitfalls can occur. Mistakes in using and interpreting Cd values can lead to inaccurate flow measurements, inefficient processes, and increased operational costs. Understanding these common errors and implementing best practices are crucial for harnessing the full potential of Cd in fluid flow management.
Avoiding Pitfalls: Common Mistakes and Best Practices
Several critical errors frequently undermine the accurate application of the Discharge Coefficient. Recognizing these pitfalls is the first step in ensuring reliable flow measurement and control.
The Perils of Ignoring Reynolds Number
The Reynolds Number (Re) is a dimensionless quantity that describes the flow regime of a fluid. It's a ratio of inertial forces to viscous forces. Many engineers fail to adequately consider how the Reynolds Number impacts the Cd.
Changes in the flow regime (laminar, transitional, turbulent) significantly affect the velocity profile and energy losses within a flow meter or control valve. A Cd value valid for a specific Reynolds Number may be entirely inaccurate at a different Re.
Therefore, always ensure that the Cd value used is appropriate for the actual operating Reynolds Number. Consult calibration curves or empirical correlations that explicitly account for Re.
The Pitfalls of Generic Cd Values
Another common mistake is relying on generic, "rule-of-thumb" Cd values without considering the specific characteristics of the device in question. While textbook values can offer a starting point, they often fail to capture the nuances of individual flow meters or valves.
Manufacturing tolerances, surface finish, and subtle variations in geometry can all influence the actual Cd value. A generalized Cd, without any careful consideration, could result in substantial errors.
The Consequences of Neglecting Proper Installation and Maintenance
Even with a theoretically perfect Cd value, inaccurate flow measurement can arise from improper installation and inadequate maintenance. This is an aspect that's often overlooked.
Upstream obstructions, such as partially closed valves or pipe bends, can distort the flow profile and introduce swirl, thereby altering the effective Cd. Similarly, the gradual buildup of deposits or corrosion on the internal surfaces of a flow meter can change its hydraulic characteristics over time, affecting the actual Cd.
Regular inspections, cleaning, and recalibration are essential to maintain the accuracy of flow measurement devices. Adhering to manufacturer's recommendations for installation, including straight pipe run requirements, is critical.
Best Practices for Accurate Flow Measurement and Control
To mitigate these risks, adopt a proactive approach to Cd selection and application. The following practices will help ensure optimal performance and accuracy:
- Prioritize Device-Specific Calibration: Whenever possible, obtain a calibration certificate from the manufacturer that provides Cd values for the specific flow meter or control valve under your operating conditions.
- Consult Empirical Correlations Carefully: When relying on empirical correlations to estimate Cd, ensure that the correlation is appropriate for the device type, geometry, and flow regime. Pay close attention to the correlation's limitations and range of applicability.
- Consider CFD Modeling: For critical applications or complex geometries, consider using Computational Fluid Dynamics (CFD) simulations to predict Cd values. CFD can provide valuable insights into the flow behavior within the device and help optimize its design.
- Implement Regular Maintenance: Establish a regular maintenance schedule for flow measurement devices, including inspections, cleaning, and recalibration. Document all maintenance activities and track changes in Cd values over time.
- Ensure Proper Installation: Strictly adhere to manufacturer's recommendations for installation, including straight pipe run requirements and proper orientation. Minimize upstream disturbances that could distort the flow profile.
- Monitor Performance and Validate Results: Continuously monitor the performance of flow measurement systems and validate results against independent measurements or process data. Investigate any discrepancies and take corrective action promptly.
By understanding the common pitfalls and implementing these best practices, engineers can significantly enhance the accuracy and reliability of flow measurement and control systems. This will result in improved process efficiency, reduced operational costs, and enhanced overall performance.
Video: Discharge Coefficient: The Ultimate Guide You Need to Know
FAQs: Understanding the Discharge Coefficient
This section answers common questions regarding the discharge coefficient, helping you grasp its significance and application.
What exactly is the discharge coefficient?
The discharge coefficient is a dimensionless number used in fluid dynamics to relate the actual flow rate of a fluid through an opening (like an orifice or nozzle) to the theoretical flow rate. It accounts for losses due to friction and flow contraction. A value of 1.0 represents ideal flow with no losses.
Why is the discharge coefficient important?
It's crucial because it allows us to accurately predict flow rates in real-world scenarios. Theoretical calculations often overestimate the actual flow. The discharge coefficient corrects for this, providing a more realistic estimation for design and analysis.
How is the discharge coefficient determined?
The discharge coefficient is typically determined experimentally. It depends on various factors, including the geometry of the opening, the fluid properties (like viscosity), and the Reynolds number of the flow. You can find these values in handbooks or through specific tests.
What factors affect the discharge coefficient?
Several factors can influence the discharge coefficient. These include the shape and sharpness of the inlet to the opening, the surface roughness, and the degree of turbulence in the flow. Also, changes in fluid properties like temperature, viscosity, or density can affect the discharge coefficient.