Scrap Causes ID: US Manufacturing Guide
In US manufacturing, waste reduction strategies are vital for maintaining competitiveness, and identification of causes in scrap plays a pivotal role. Lean manufacturing principles emphasize minimizing waste and maximizing efficiency, leading organizations like the National Association of Manufacturers to prioritize effective scrap management. Tools such as root cause analysis are frequently employed to systematically uncover the underlying reasons for material waste. Moreover, the implementation of Six Sigma methodologies, championed by figures like Bill Smith, drives continuous improvement in production processes by providing a structured approach to the identification of causes in scrap and the subsequent elimination of defects.
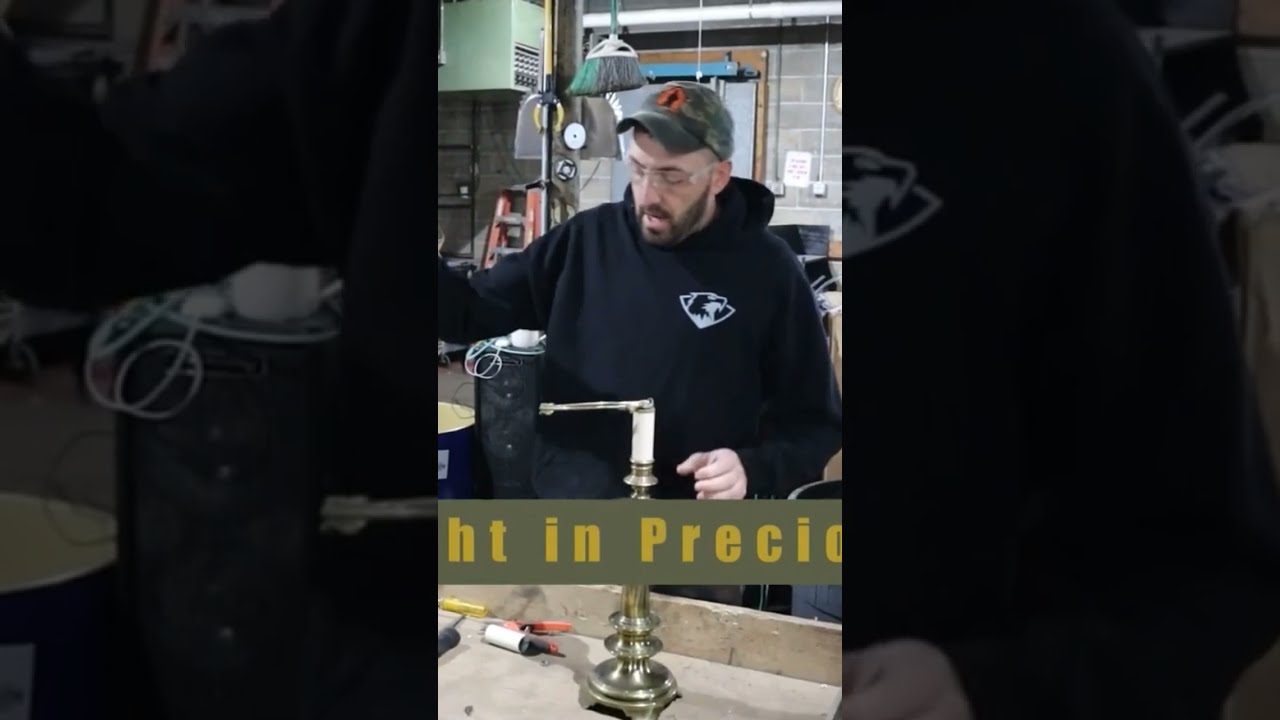
Image taken from the YouTube channel Andy Weins , from the video titled How to Identify what is worth scrapping $$$ .
Scrap in manufacturing, often relegated to the background, is a critical issue that demands the full attention of industry leaders. It is far more than just discarded material; it represents a significant drain on resources, profitability, and environmental well-being.
This section will unpack the definition of scrap, analyze its wide-ranging economic implications, and address the often-overlooked environmental consequences.
Defining "Scrap" in Manufacturing
Scrap, in its simplest form, refers to any material, component, or product that fails to meet required specifications and is deemed unusable for its intended purpose.
This definition encompasses a broad spectrum of waste, arising from diverse sources and manifesting in various forms.
It's crucial to differentiate between these types of scrap to implement effective reduction strategies:
-
Material Scrap: This includes raw materials or partially processed materials rendered unusable due to damage, contamination, or exceeding shelf life. Examples are metal offcuts, plastic trimmings, and spoiled chemicals.
-
Defective Parts: These are components or sub-assemblies that fail to meet quality standards due to manufacturing errors, dimensional inaccuracies, or material flaws.
-
Obsolete Inventory: Products or materials that are no longer needed or cannot be sold due to design changes, market shifts, or exceeding their usable lifespan.
-
Rejected Finished Goods: Completed products that fail final inspection and cannot be sold as intended.
Economic Impact: The Hidden Costs of Waste
The financial repercussions of scrap are far-reaching, extending beyond the readily apparent cost of wasted materials. These costs ripple through the entire manufacturing process, eroding profitability and competitiveness.
Direct Costs
These are the most easily quantifiable costs associated with scrap:
-
Material Waste: The cost of raw materials that are ultimately discarded, including purchase price, transportation, and storage.
-
Labor Costs: The wages paid to workers who processed the scrap material, including time spent on production, inspection, and disposal.
-
Disposal Costs: Expenses associated with disposing of scrap material, including landfill fees, recycling costs, and transportation.
Indirect Costs
Often overlooked, these costs can significantly amplify the financial burden of scrap:
-
Rework and Repair: The cost of labor and materials required to correct defects and salvage non-conforming products.
-
Production Delays: Scrap can disrupt production schedules, leading to delays in delivery and potential penalties.
-
Increased Overhead: Higher scrap rates can necessitate increased inspection, quality control, and administrative overhead.
-
Lost Capacity: Manufacturing capacity wasted on producing scrap parts cannot be used for profitable production.
-
Damaged Reputation: High scrap rates can negatively impact a company's reputation, leading to decreased customer confidence and lost sales.
Environmental Impact: A Call for Sustainability
The environmental consequences of scrap extend beyond the confines of the factory floor, contributing to resource depletion, pollution, and greenhouse gas emissions.
A comprehensive approach to scrap reduction is essential for promoting sustainability and minimizing the environmental footprint of manufacturing operations.
-
Resource Depletion: Scrap represents a wasteful use of natural resources, including raw materials, energy, and water.
-
Pollution: The manufacturing and disposal of scrap can generate air and water pollution, harming ecosystems and human health.
-
Landfill Waste: Scrap sent to landfills contributes to the growing problem of waste disposal, consuming valuable land and potentially contaminating soil and groundwater.
-
Energy Consumption: The production of scrap consumes energy, contributing to greenhouse gas emissions and climate change.
Embracing sustainable manufacturing practices, including waste reduction, recycling, and the use of environmentally friendly materials, is crucial for minimizing the environmental impact of scrap and ensuring a more sustainable future.
By understanding the multifaceted implications of scrap, manufacturers can begin to implement effective strategies for minimizing waste, improving profitability, and promoting environmental responsibility.
Core Methodologies for Effective Scrap Reduction
Scrap in manufacturing, often relegated to the background, is a critical issue that demands the full attention of industry leaders. It is far more than just discarded material; it represents a significant drain on resources, profitability, and environmental well-being. This section will unpack the definition of scrap, analyze its wide-ranging economic and environmental implications, and then delve into the fundamental methodologies that form the bedrock of effective scrap reduction strategies.
Root Cause Analysis (RCA)
Root Cause Analysis (RCA) is a systematic approach to identifying the fundamental reasons why a problem occurred. Unlike addressing superficial symptoms, RCA aims to unearth the underlying causes that trigger a chain of events leading to scrap generation.
The RCA process typically involves:
- Defining the problem precisely.
- Gathering data and evidence.
- Identifying possible causal factors.
- Determining the root cause(s).
- Implementing corrective actions.
- Verifying the effectiveness of the solutions.
For example, if excessive porosity is observed in castings, RCA might reveal that inadequate degassing procedures or improper alloy composition are the root causes, rather than simply attributing it to "bad luck."
The "5 Whys" Technique
The "5 Whys" is a deceptively simple yet powerful technique for drilling down to the root cause of a problem. By repeatedly asking "why" (typically five times, though the number may vary), you can peel back layers of symptoms to expose the true underlying issue.
For example:
- Problem: High scrap rate in machining.
- Why? Tools are breaking frequently.
- Why? Tool feed rate is too high.
- Why? Operator is trying to increase throughput.
- Why? Operator is not adequately trained on optimal machining parameters.
- Why? There is a lack of sufficient training and updated standard operating procedures for machine operators.
This reveals that the root cause is a lack of sufficient training and updated standard operating procedures, not merely "broken tools."
Fishbone Diagram (Ishikawa Diagram)
The Fishbone diagram, also known as the Ishikawa diagram or cause-and-effect diagram, is a visual tool used for brainstorming and categorizing potential causes of a problem.
The diagram resembles a fish skeleton, with the problem (scrap generation) represented as the "head" and the potential causes branching off as "bones." Typical categories include:
- Man: Operator errors, training deficiencies.
- Machine: Equipment malfunctions, calibration issues.
- Method: Inadequate procedures, poor work instructions.
- Material: Defective raw materials, incorrect specifications.
- Measurement: Inaccurate inspection, faulty measuring tools.
- Environment: Temperature fluctuations, humidity.
By systematically exploring each category, the Fishbone diagram helps teams identify a comprehensive list of possible contributing factors to scrap.
Pareto Analysis
Pareto Analysis, based on the Pareto principle (the 80/20 rule), is a technique for prioritizing the most significant sources of scrap. It posits that roughly 80% of problems stem from 20% of the causes.
By collecting data on scrap generation by type, source, or defect, a Pareto chart can be created to visually represent the relative contribution of each factor.
This allows manufacturers to focus their resources on addressing the "vital few" causes that have the greatest impact on reducing overall scrap.
For example, a Pareto analysis might reveal that a specific type of defect accounts for 70% of all scrap, prompting immediate investigation and corrective action targeting that particular issue.
Statistical Process Control (SPC)
Statistical Process Control (SPC) is a method of monitoring and controlling manufacturing processes using statistical techniques. By tracking key process variables (e.g., dimensions, temperature, pressure) over time, SPC charts can detect deviations from the expected range, signaling potential problems before they result in scrap.
SPC charts typically include a center line (representing the average value) and upper and lower control limits. When a process variable falls outside these limits, it indicates that the process is out of control and requires investigation and corrective action.
SPC enables proactive intervention, preventing defects and minimizing scrap through continuous monitoring and process adjustments.
Six Sigma
Six Sigma is a data-driven methodology focused on reducing variation and defects in manufacturing processes. It aims to achieve near-perfect quality by systematically identifying and eliminating the root causes of defects.
The core of Six Sigma is the DMAIC (Define, Measure, Analyze, Improve, Control) cycle:
- Define: Clearly define the problem and project goals.
- Measure: Collect data to quantify the problem and establish a baseline.
- Analyze: Analyze the data to identify the root causes of defects.
- Improve: Implement solutions to address the root causes and reduce variation.
- Control: Establish controls to maintain the improvements and prevent future defects.
Six Sigma projects often involve the use of statistical tools and techniques to analyze data, identify critical process variables, and optimize process parameters.
Lean Manufacturing
Lean Manufacturing is a philosophy focused on eliminating waste in all aspects of the manufacturing process. One of the key wastes targeted by Lean is defects, which directly contribute to scrap.
Lean principles and tools that are effective in reducing scrap include:
- Value Stream Mapping: Visualizing the entire production process to identify sources of waste.
- 5S (Sort, Set in Order, Shine, Standardize, Sustain): Creating a clean, organized, and efficient work environment.
- Poka-Yoke (Mistake-Proofing): Designing processes and equipment to prevent errors from occurring.
- Just-in-Time (JIT): Producing goods only when needed to minimize inventory and waste.
By implementing Lean principles, manufacturers can streamline their processes, reduce defects, and minimize scrap.
Failure Mode and Effects Analysis (FMEA)
Failure Mode and Effects Analysis (FMEA) is a proactive risk assessment technique used to identify potential failure modes in a product or process and to evaluate their potential effects.
FMEA involves systematically analyzing each component or step in a process to determine:
- How it could fail (failure mode).
- What the effects of that failure would be.
- How likely the failure is to occur (occurrence).
- How easily the failure can be detected (detection).
- The severity of the effects (severity).
Based on these assessments, a Risk Priority Number (RPN) is calculated (Occurrence x Severity x Detection). This helps prioritize actions to mitigate the most critical failure modes and prevent scrap.
Data Analytics/Data Mining
Data Analytics and Data Mining play an increasingly important role in scrap reduction efforts. By analyzing large datasets of production data, manufacturers can identify patterns and trends that are not readily apparent through traditional methods.
For instance, data mining might reveal a correlation between specific machine settings and increased scrap rates, or identify shifts or operators with higher defect rates. Advanced analytics can even predict potential failures before they occur, allowing for proactive maintenance and intervention.
By leveraging the power of data, manufacturers can gain valuable insights into the causes of scrap and develop targeted strategies to address them, leading to substantial improvements in efficiency and profitability.
Process-Specific Scrap Generation and Mitigation Strategies
Scrap in manufacturing, often relegated to the background, is a critical issue that demands the full attention of industry leaders. It is far more than just discarded material; it represents a significant drain on resources, profitability, and environmental well-being. This section will unpack the diverse ways in which scrap manifests across various manufacturing processes.
We will delve into specific causes and offer targeted mitigation strategies, providing a practical guide for minimizing waste and maximizing efficiency. The goal is to move beyond generic solutions and address the unique challenges presented by each process.
Machining: Precision and Waste Reduction
Machining operations, while essential for creating precise components, are inherently prone to generating scrap. Chips, swarf, and rejected parts contribute significantly to material waste. The key to minimizing this waste lies in optimizing several critical factors.
Cutting Parameter Optimization: Aggressive cutting parameters, while increasing production speed, often lead to increased tool wear, surface defects, and ultimately, more scrap. Carefully adjusting speed, feed, and depth of cut to match the material and tool is paramount.
Tool Maintenance: Worn or improperly sharpened cutting tools are a major source of defects. Implementing a rigorous tool maintenance program, including regular inspection, sharpening, and replacement, is crucial for maintaining part quality and minimizing scrap.
Material Selection: The choice of cutting fluid impacts both tool life and surface finish. Selecting the appropriate cutting fluid for the material being machined can significantly reduce friction, heat, and the likelihood of defects.
Casting: Controlling Variables for Quality
Casting processes, involving the pouring of molten material into molds, are susceptible to a range of defects that lead to scrap.
Porosity, shrinkage, and incomplete filling are common issues that must be addressed through careful process control.
Temperature Management: Precise temperature control is vital at every stage of the casting process. Controlling the pouring temperature, mold temperature, and cooling rate can significantly reduce defects related to solidification and shrinkage.
Mold Design: The design of the mold plays a crucial role in preventing defects. Optimizing the gating system, runner design, and venting can ensure proper filling and minimize turbulence, leading to fewer casting flaws.
Material Quality: The quality of the molten material directly impacts the final casting. Ensuring that the metal is properly refined and free of impurities is essential for producing sound castings.
Forging: Achieving Consistency and Reducing Defects
Forging, a process that involves shaping metal through compressive forces, is prone to defects such as cracking, laps, and scale. Maintaining consistency and precision is key to minimizing scrap.
Die Maintenance: The dies used in forging are subjected to extreme forces and temperatures, leading to wear and tear. Regular die maintenance, including inspection, cleaning, and repair, is essential for preventing defects.
Temperature Control: Maintaining the correct temperature of both the dies and the workpiece is critical. Overheating can lead to grain growth and cracking, while insufficient heating can result in incomplete forging.
Lubrication: Proper lubrication reduces friction between the dies and the workpiece, preventing defects and extending die life. The type of lubricant used should be carefully selected based on the material and forging process.
Injection Molding: Precision Polymers
Injection molding, a widely used process for manufacturing plastic parts, faces challenges such as sink marks, warpage, and short shots. Addressing these issues requires careful control over mold design and process parameters.
Mold Design Optimization: A well-designed mold is essential for producing high-quality parts. Optimizing the gate location, runner design, and cooling channels can ensure proper filling, minimize warpage, and reduce sink marks.
Process Parameter Control: The injection molding process involves numerous parameters, including injection pressure, temperature, and cooling time. Optimizing these parameters for the specific material and part geometry is crucial for minimizing defects.
Material Handling: Proper handling and storage of the plastic resin are essential for preventing contamination and moisture absorption, both of which can lead to defects.
Stamping: Maximizing Material Utilization
Metal stamping, involving the use of dies to cut and form sheet metal, inevitably generates scrap in the form of skeleton scrap and rejected parts. Optimizing die design and material utilization are key to minimizing waste.
Die Design Optimization: Efficient die design can significantly reduce the amount of skeleton scrap generated. Optimizing the nesting of parts within the sheet metal can maximize material utilization.
Material Selection: Using the correct material grade and thickness can minimize the likelihood of tearing or cracking during stamping. Selecting materials with good formability can also reduce the number of rejected parts.
Lubrication: Proper lubrication reduces friction between the die and the sheet metal, preventing defects and extending die life.
Welding: Ensuring Joint Integrity and Reducing Spatter
Welding, a process that joins materials together using heat, can generate scrap in the form of spatter, porosity, and weld defects. Employing proper techniques and quality control measures are crucial.
Proper Gas Shielding: Using the correct shielding gas and maintaining proper gas flow is essential for preventing atmospheric contamination of the weld, which can lead to porosity and other defects.
Weld Parameter Optimization: Optimizing welding parameters, such as voltage, current, and travel speed, is crucial for achieving a sound weld with minimal spatter.
Joint Preparation: Properly preparing the joint surfaces, including cleaning and removing oxides, is essential for ensuring good weld fusion and preventing defects.
Electronics Manufacturing: Minimizing PCB Defects
Electronics manufacturing, particularly PCB fabrication and assembly, is incredibly complex, generating scrap through component misplacements, solder defects, and board contamination. Automated inspection and precision equipment are key.
Automated Optical Inspection (AOI): Implementing AOI systems can detect a wide range of defects, including component misplacements, solder bridges, and insufficient solder joints.
Component Placement Accuracy: Precise component placement is critical for ensuring proper functionality. Using automated pick-and-place machines with high accuracy can minimize the risk of misplacements.
Process Control: Closely monitoring and controlling process parameters, such as reflow temperature and soldering time, is essential for minimizing solder defects.
Textile Manufacturing: Optimizing Material Usage
Textile manufacturing, encompassing weaving and knitting, generates scrap primarily from edge trimmings, yarn breakage, and fabric defects. Efficient material utilization is vital.
Pattern Nesting Optimization: Efficiently nesting patterns during cutting can minimize the amount of edge trimming scrap.
Yarn Quality Control: Using high-quality yarn with consistent strength and thickness can reduce the likelihood of yarn breakage during weaving and knitting.
Machine Maintenance: Maintaining weaving and knitting machines in good working order can prevent fabric defects caused by mechanical problems.
Food Processing: Reducing Spoilage and Waste
Food processing, encompassing a wide range of operations, generates scrap primarily from spoilage, trim loss, and packaging defects. Optimizing processes and reducing spillage is essential.
Optimized Cutting Techniques: Implementing efficient cutting techniques can minimize trim loss during processing.
Reduced Spillage: Minimizing spillage during handling and processing reduces waste and prevents contamination.
Proper Storage: Storing raw materials and finished products under the correct conditions is essential for preventing spoilage and extending shelf life.
Identifying and Addressing Different Types and Sources of Scrap
Scrap in manufacturing, often relegated to the background, is a critical issue that demands the full attention of industry leaders. It is far more than just discarded material; it represents a significant drain on resources, profitability, and environmental well-being. This section will unravel the intricate web of scrap origins and provide targeted strategies for each specific type.
Understanding the multifaceted nature of scrap is the first step towards effective mitigation. Scrap can arise from a variety of sources, ranging from inherent material imperfections to systemic design flaws. A comprehensive approach requires a meticulous categorization of these sources and the development of corresponding countermeasures.
Material Defects: The Foundation of Quality Control
Material defects represent a foundational challenge in manufacturing. Imperfections in raw materials, often undetectable without rigorous inspection, can propagate through the entire production process, leading to substantial scrap generation.
The effectiveness of supplier quality control is paramount in minimizing material-related scrap. Implementing robust inspection protocols at the point of material entry is crucial for identifying and isolating substandard materials before they enter the production stream.
This may include:
- Advanced testing methods: Employing non-destructive testing (NDT) techniques such as ultrasonic testing and radiographic inspection.
- Statistical sampling: Conducting rigorous statistical sampling to assess the overall quality of material batches.
- Supplier audits: Performing regular audits of supplier facilities to ensure adherence to established quality standards.
Process Defects: Optimizing the Manufacturing Flow
Process defects are the bane of efficient manufacturing. Errors occurring during the manufacturing process, often stemming from inadequate process control or poorly trained operators, can lead to significant scrap rates.
Effective mitigation of process defects requires a multifaceted approach centered on process optimization and continuous operator training.
This involves:
- Standardized work instructions: Establishing clearly defined work instructions and standard operating procedures (SOPs) to minimize variability.
- Statistical process control (SPC): Implementing SPC techniques to monitor process parameters and detect deviations from established norms.
- Regular operator training: Providing regular training and skill development opportunities for operators to enhance their proficiency and reduce errors.
Equipment Malfunctions: The Price of Neglect
Equipment malfunctions pose a significant threat to manufacturing efficiency and product quality. Unexpected breakdowns and performance deviations can result in substantial scrap, production delays, and costly repairs.
Preventive maintenance and equipment calibration are crucial to mitigate the risks associated with equipment malfunctions. A proactive maintenance strategy reduces the likelihood of unexpected breakdowns and ensures optimal equipment performance.
Key elements of such a strategy should include:
- Scheduled maintenance: Implementing a comprehensive schedule of routine maintenance tasks, including cleaning, lubrication, and component replacement.
- Predictive maintenance: Utilizing sensor technology and data analytics to monitor equipment performance and predict potential failures before they occur.
- Regular calibration: Ensuring that all measuring instruments and equipment are calibrated regularly to maintain accuracy and reliability.
Operator Error: The Human Element
Operator error, an inevitable aspect of manufacturing, can be a significant source of scrap. Mistakes made by workers, stemming from inadequate training or a lack of attention to detail, can lead to defective products and material waste.
Minimizing operator error requires a dual approach that focuses on improved training and enhanced process monitoring.
This entails:
- Comprehensive training programs: Developing comprehensive training programs that cover all aspects of the manufacturing process.
- Clear work instructions: Providing clear, concise, and easily understandable work instructions to minimize ambiguity and confusion.
- Effective process monitoring: Implementing effective process monitoring systems to detect and correct errors in real-time. This can include automated inspection systems, visual aids, and regular quality checks.
Design Flaws: Addressing the Root Cause
Design flaws, often overlooked as a source of scrap, can have a profound impact on manufacturing efficiency and product quality. Problems with product design, such as inadequate tolerances or difficult-to-manufacture features, can lead to persistent scrap issues throughout the production process.
Addressing design flaws requires a proactive approach that emphasizes design for manufacturability (DFM) and thorough design reviews.
This includes:
- DFM principles: Incorporating DFM principles into the product design process to ensure that products are designed for efficient and cost-effective manufacturing.
- Cross-functional collaboration: Fostering collaboration between design engineers, manufacturing engineers, and quality control personnel to identify potential design-related issues early in the development process.
- Thorough design reviews: Conducting thorough design reviews to identify and address potential design flaws before production begins.
Tooling Issues: Precision and Durability
Tooling issues, encompassing problems with cutting tools, molds, and dies, can significantly impact manufacturing quality and efficiency. Worn, damaged, or improperly designed tooling can lead to defective parts, increased scrap rates, and production downtime.
Mitigating tooling issues requires a comprehensive approach that addresses tool maintenance, design, and material selection.
This strategy should include:
- Regular maintenance: Implementing a regular maintenance schedule for all tooling, including cleaning, sharpening, and repair.
- Optimized design: Designing tooling to minimize stress and wear, and to facilitate efficient manufacturing processes.
- Appropriate material selection: Selecting tooling materials that are appropriate for the application and that can withstand the rigors of the manufacturing process.
By addressing the various types and sources of scrap in a targeted and systematic manner, manufacturers can significantly reduce waste, improve efficiency, and enhance profitability. The strategies outlined in this section offer a roadmap for implementing a comprehensive scrap reduction program that addresses the root causes of waste and promotes a culture of continuous improvement.
Leveraging Technology for Scrap Reduction: Key Tools and Techniques
The relentless pursuit of scrap reduction in manufacturing is significantly enhanced by the strategic implementation of technology. The utilization of advanced technological tools and techniques is no longer optional but a necessity for companies aiming to optimize production processes, minimize waste, and enhance overall efficiency. These tools enable manufacturers to identify, analyze, and address sources of scrap with unprecedented precision and speed.
Coordinate Measuring Machines (CMMs)
Coordinate Measuring Machines (CMMs) play a crucial role in ensuring dimensional accuracy and conformity to design specifications. CMMs are sophisticated instruments that use precise probes to measure the physical geometry of an object.
These measurements are then compared against CAD models or engineering drawings to identify deviations, which can lead to scrap. By identifying these deviations early in the production cycle, manufacturers can take corrective actions.
These proactive measures prevent the production of defective parts. The precision and reliability of CMMs make them an indispensable tool in industries where dimensional accuracy is paramount.
Vision Systems
Automated vision systems provide a powerful method for inspecting parts at high speeds. Vision systems utilize cameras, optics, and image processing algorithms to detect defects, dimensional variations, and surface imperfections.
These systems can be integrated directly into production lines. Allowing for real-time monitoring and immediate detection of anomalies.
Their ability to perform complex inspections with minimal human intervention ensures consistent quality control and rapid identification of potential scrap-generating issues. Vision systems can also be programmed to identify specific types of defects, such as cracks, scratches, or missing features. The versatility and speed of vision systems make them essential for high-volume manufacturing operations.
Non-Destructive Testing (NDT)
Non-Destructive Testing (NDT) encompasses a range of techniques used to evaluate the integrity of materials and components without causing damage. These methods are critical for identifying internal defects that are not visible through visual inspection.
Common NDT Methods
Common NDT methods include:
- Ultrasonic Testing: Uses high-frequency sound waves to detect internal flaws such as cracks, voids, and inclusions.
- Radiography (X-ray): Employs X-rays to create images of the internal structure of a component, revealing defects and variations in density.
- Magnetic Particle Testing: Detects surface and near-surface flaws in ferromagnetic materials by applying magnetic fields and observing the accumulation of magnetic particles.
- Liquid Penetrant Testing: Identifies surface cracks and discontinuities by applying a liquid penetrant that seeps into the flaws and then is made visible under ultraviolet light.
NDT techniques are essential in industries such as aerospace, automotive, and energy, where component reliability is critical. By identifying and eliminating defective parts before they enter service, NDT helps to prevent catastrophic failures and reduces the risk of costly recalls or warranty claims.
Statistical Software and Statistical Process Control (SPC)
Statistical software plays a vital role in analyzing production data and identifying trends that may lead to scrap. These software packages provide a range of statistical tools and techniques, including:
- Control Charts: Monitor process variation over time and identify when a process is out of control.
- Histograms: Visualize the distribution of data and identify potential outliers or deviations from the norm.
- Regression Analysis: Determines the relationship between different variables and identifies factors that contribute to scrap.
- Analysis of Variance (ANOVA): Compares the means of different groups to identify significant differences and potential sources of variation.
By using statistical software to analyze production data, manufacturers can gain valuable insights into the factors that contribute to scrap. This enables them to implement targeted interventions and improve process control.
Statistical Process Control (SPC) is a method of quality control which employs statistical methods to monitor and control a process. SPC uses control charts to track key process parameters over time, identifying deviations from the expected range.
When a process deviates from its control limits, it indicates a problem that needs to be addressed. SPC helps manufacturers maintain process stability, reduce variation, and prevent defects before they occur, thereby minimizing scrap and improving overall product quality.
Key Roles and Responsibilities in Scrap Reduction Initiatives
Leveraging Technology for Scrap Reduction: Key Tools and Techniques
The relentless pursuit of scrap reduction in manufacturing is significantly enhanced by the strategic implementation of technology. The utilization of advanced technological tools and techniques is no longer optional but a necessity for companies aiming to optimize production processes. A successful scrap reduction program, however, hinges not only on technology but also on the coordinated efforts of various personnel within the organization. Clearly defined roles and responsibilities are paramount to achieving meaningful and sustainable improvements in minimizing waste.
The Collaborative Ecosystem of Scrap Reduction
Scrap reduction is not the sole responsibility of a single department or individual. It requires a concerted effort from a diverse team, each contributing their unique expertise and perspective. By fostering a culture of collaboration and shared accountability, organizations can create a powerful synergy that drives down scrap rates and enhances overall efficiency.
Core Roles in Scrap Reduction
Each role within the organization plays a critical part in the scrap reduction strategy. Understanding the responsibilities and how they intertwine is paramount for a robust process.
Quality Engineers: Guardians of Product Excellence
Quality Engineers are at the forefront of ensuring product quality and minimizing defects. Their role extends beyond simply inspecting finished goods; they are deeply involved in preventing defects from occurring in the first place.
Key Responsibilities include:
- Developing and implementing quality control procedures.
- Identifying and analyzing the root causes of defects.
- Implementing corrective and preventative actions (CAPA).
- Conducting statistical process control (SPC) to monitor process performance.
- Collaborating with other departments to improve product design and manufacturing processes.
Their analytical skills, combined with a strong understanding of quality management principles, make them invaluable assets in the fight against scrap.
Manufacturing Engineers: Architects of Efficient Processes
Manufacturing Engineers are responsible for designing and optimizing manufacturing processes to minimize waste and maximize efficiency. Their expertise lies in creating streamlined workflows, selecting appropriate equipment, and implementing best practices.
Key Responsibilities include:
- Developing and implementing manufacturing processes.
- Identifying and eliminating sources of waste (including scrap).
- Optimizing process parameters to improve product quality and reduce defects.
- Designing and implementing tooling and fixtures.
- Collaborating with other departments to improve product design and manufacturability.
By applying their engineering knowledge and problem-solving skills, manufacturing engineers play a crucial role in creating robust and efficient processes that minimize scrap generation.
Process Engineers: Fine-Tuning for Optimal Performance
Process Engineers focus on optimizing specific manufacturing processes to improve efficiency and reduce scrap. They possess in-depth knowledge of particular processes and are skilled at identifying and implementing improvements.
Key Responsibilities include:
- Analyzing process data to identify areas for improvement.
- Conducting experiments to optimize process parameters.
- Implementing process improvements to reduce scrap and improve efficiency.
- Developing and maintaining process documentation.
- Training operators on best practices.
Their meticulous attention to detail and process expertise contribute significantly to minimizing scrap and improving overall manufacturing performance.
Maintenance Technicians: Preserving Equipment Integrity
Maintenance Technicians are vital for ensuring that equipment operates reliably and efficiently. Their proactive maintenance efforts prevent breakdowns and malfunctions that can lead to scrap.
Key Responsibilities include:
- Performing regular maintenance on equipment.
- Troubleshooting and repairing equipment malfunctions.
- Implementing preventive maintenance programs.
- Ensuring that equipment is properly calibrated.
- Identifying and addressing potential equipment problems before they lead to breakdowns.
By maintaining equipment in optimal condition, maintenance technicians minimize downtime and reduce the risk of scrap resulting from equipment failures.
Production Supervisors: Frontline Observers and Problem Solvers
Production Supervisors play a crucial role in overseeing production and identifying potential problems that could lead to scrap. They are on the front lines, observing processes firsthand and interacting with operators.
Key Responsibilities include:
- Monitoring production processes to ensure they are operating correctly.
- Identifying and addressing potential problems that could lead to scrap.
- Supervising and training production operators.
- Enforcing quality control procedures.
- Communicating process issues to the appropriate departments.
Their vigilance and ability to identify and resolve problems quickly are essential for preventing scrap and maintaining smooth production operations.
Metrologists: Ensuring Measurement Accuracy
Metrologists are responsible for ensuring the accuracy of measurements throughout the manufacturing process. Their expertise in measurement and calibration is crucial for maintaining product quality and preventing defects.
Key Responsibilities include:
- Calibrating measuring instruments and equipment.
- Developing and implementing measurement procedures.
- Analyzing measurement data to identify potential problems.
- Ensuring that measurements are traceable to national standards.
- Training personnel on proper measurement techniques.
Accurate measurements are fundamental to quality control, and the expertise of metrologists ensures that products meet the required specifications and that scrap is minimized.
Data Scientists/Analysts: Uncovering Insights Through Data
Data Scientists and Analysts play a critical role in identifying scrap-related trends and patterns using data analysis techniques.
Key Responsibilities include:
- Collecting and analyzing data from various manufacturing processes.
- Identifying trends and patterns related to scrap generation.
- Developing statistical models to predict scrap rates.
- Creating reports and visualizations to communicate findings to stakeholders.
- Working with other departments to implement data-driven solutions to reduce scrap.
By leveraging their analytical skills, data scientists and analysts can provide valuable insights that inform scrap reduction efforts and drive continuous improvement. They transform raw data into actionable intelligence, empowering the organization to make informed decisions and optimize its processes.
Professional Organizations and Their Role in Promoting Best Practices
The relentless pursuit of scrap reduction in manufacturing is significantly enhanced by the strategic implementation of technology. The utilization of advanced technological tools and techniques is no longer optional but essential for maintaining competitiveness and achieving operational excellence. However, even with cutting-edge tools, the importance of continuous learning and adherence to established industry standards cannot be overstated. This is where professional organizations play a crucial role, providing a platform for knowledge sharing, skill development, and the dissemination of best practices.
The Significance of Industry Associations
Industry associations serve as invaluable resources for manufacturers seeking to optimize their processes and minimize scrap. These organizations act as central hubs for the aggregation and distribution of expertise, facilitating collaboration and driving innovation across the sector.
By providing access to training programs, certification courses, and industry-specific research, these associations empower manufacturers to enhance their capabilities and implement effective scrap reduction strategies.
Moreover, they foster a culture of continuous improvement by promoting the adoption of standardized methodologies and benchmarks.
American Society for Quality (ASQ)
The American Society for Quality (ASQ) stands as a preeminent organization dedicated to advancing quality principles and practices across diverse industries.
ASQ offers a wide array of resources specifically tailored to assist manufacturing professionals in their scrap reduction endeavors.
ASQ's Role in Quality Assurance
ASQ provides comprehensive training programs that cover various aspects of quality management, including statistical process control (SPC), root cause analysis, and lean manufacturing principles. These programs equip individuals with the knowledge and skills necessary to identify, analyze, and address the underlying causes of scrap generation.
Furthermore, ASQ offers professional certifications, such as the Certified Quality Engineer (CQE) and Certified Six Sigma Black Belt (CSSBB), which validate an individual's expertise in quality management methodologies.
Holding an ASQ certification demonstrates a commitment to quality and enhances an individual's credibility within the manufacturing sector.
Resources and Tools for Scrap Reduction
Beyond training and certification, ASQ provides a wealth of resources, including publications, webinars, and conferences, that focus on best practices for scrap reduction. These resources offer practical guidance and real-world examples of how manufacturers have successfully implemented scrap reduction initiatives.
ASQ's online community forums also provide a valuable platform for professionals to connect, share insights, and seek advice from peers.
Society of Manufacturing Engineers (SME)
The Society of Manufacturing Engineers (SME) is another leading professional organization that plays a critical role in advancing manufacturing technologies and practices.
SME's focus is on promoting innovation and excellence in manufacturing processes, making it a valuable resource for professionals seeking to optimize their operations and minimize scrap.
SME's Contribution to Manufacturing Excellence
SME provides extensive training and educational programs designed to enhance the skills and knowledge of manufacturing engineers and technicians. These programs cover a wide range of topics, including process optimization, automation, and advanced manufacturing technologies.
By equipping professionals with the latest knowledge and skills, SME empowers them to implement effective scrap reduction strategies and improve overall manufacturing efficiency.
Networking and Knowledge Sharing
SME facilitates networking and knowledge sharing through conferences, workshops, and online communities.
These events provide opportunities for professionals to connect with peers, learn about emerging technologies, and share best practices for scrap reduction.
SME also publishes a variety of technical journals and publications that provide in-depth information on manufacturing processes and technologies.
These resources serve as valuable tools for staying abreast of the latest advancements and implementing innovative solutions to minimize scrap.
Advocacy and Standards
In addition to its educational and networking activities, SME advocates for policies and standards that promote manufacturing excellence.
By working with government agencies and industry stakeholders, SME helps to create a supportive environment for manufacturers to thrive and contribute to economic growth.
SME’s commitment to promoting best practices and fostering innovation makes it an indispensable resource for manufacturing professionals seeking to minimize scrap and achieve operational excellence.
Video: Scrap Causes ID: US Manufacturing Guide
FAQs: Scrap Causes ID: US Manufacturing Guide
What is the main purpose of the "Scrap Causes ID: US Manufacturing Guide"?
The guide provides a structured approach to identify the root causes of scrap in US manufacturing environments. It helps teams systematically analyze production processes and determine the underlying reasons for material wastage. The goal is to reduce scrap, improve efficiency, and lower production costs by enabling thorough identification of causes in scrap.
Who benefits most from using this guide?
Manufacturing engineers, quality control personnel, production managers, and process improvement teams will find this guide most valuable. Anyone involved in reducing waste, improving product quality, or optimizing manufacturing processes can use it to streamline identification of causes in scrap.
What types of scrap causes does the guide cover?
The guide covers a wide range of potential scrap causes, including material defects, machine malfunctions, operator errors, design flaws, and process variations. It offers a comprehensive framework for understanding and categorizing different factors contributing to scrap generation, aiding in accurate identification of causes in scrap.
How does the guide help with implementing corrective actions?
By providing a structured process for identifying the root causes of scrap, the guide lays the foundation for effective corrective actions. Once the causes are understood, targeted solutions can be implemented to prevent recurrence, improving overall manufacturing efficiency and decreasing scrap rates by focusing on the identification of causes in scrap.
So, there you have it! Hopefully, this guide sheds some light on the most common culprits behind your scrap issues. Remember, diligent investigation and a proactive approach to identification of causes in scrap are key to minimizing waste and maximizing profits. Good luck optimizing your manufacturing processes!