Thermal Shock Test: Methods, Applications, Standards
The integrity of materials under extreme temperature variations is rigorously evaluated through a thermal shock test, a procedure vital across numerous industries. The IPC (Association Connecting Electronics Industries), a leading organization, establishes standards that guide the execution and interpretation of these tests, ensuring reliability and consistency. Temperature cycling, a common method within thermal shock testing, exposes samples to alternating hot and cold environments to simulate real-world conditions. These tests find extensive application in sectors ranging from aerospace, where components must withstand rapid atmospheric changes, to semiconductor manufacturing, where microchips are subjected to intense thermal gradients during operation.
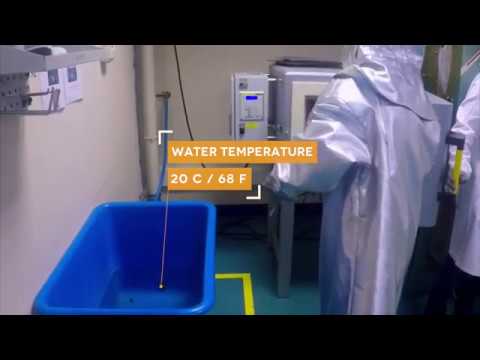
Image taken from the YouTube channel EuroKera. Transform the soul of your home. , from the video titled Thermal Shock Test .
Thermal shock, at its core, is the mechanical stress induced in a material due to rapid temperature changes.
This sudden shift creates non-uniform thermal expansion or contraction, leading to internal stresses that can exceed the material's tensile strength.
Ultimately, this can result in cracking or even catastrophic failure.
Defining Thermal Shock
Thermal shock occurs when a material experiences a rapid and significant change in temperature, causing differential expansion or contraction within its structure.
This rapid change creates internal stresses.
If these stresses surpass the material's tensile strength, cracks initiate and propagate, potentially leading to structural failure.
Consider a glass baking dish taken directly from a hot oven and placed on a cold countertop.
The sudden temperature difference between the hot glass and the cool surface induces stress.
If the stress exceeds the glass's capacity, it shatters. This is a classic example of thermal shock.
Another common instance is the cracking of ceramic engine components due to rapid heating and cooling cycles during operation.
The Significance of Thermal Shock Analysis
Thermal shock analysis plays a pivotal role in ensuring the reliability and durability of various products and structures across multiple engineering disciplines.
By predicting the susceptibility of a material or component to thermal shock, engineers can make informed decisions about material selection, design modifications, and operating conditions.
This proactive approach mitigates the risk of premature failure, reduces maintenance costs, and enhances the overall safety and performance of engineered systems.
For instance, in aerospace engineering, thermal shock analysis is crucial for designing turbine blades that can withstand the extreme temperature gradients within a jet engine.
Similarly, in the electronics industry, this analysis is essential for ensuring the longevity of electronic components subjected to thermal cycling during operation.
Key Material Properties Influencing Thermal Shock Resistance
Several material properties significantly influence a material's resistance to thermal shock.
Understanding these properties is crucial for selecting materials suitable for applications where thermal shock is a concern.
Thermal Conductivity
Thermal conductivity is a material's ability to conduct heat.
A higher thermal conductivity allows for more uniform temperature distribution, reducing thermal gradients and minimizing stress.
Thermal Expansion
The coefficient of thermal expansion measures how much a material expands or contracts with temperature changes.
Materials with low thermal expansion coefficients experience less dimensional change.
This, in turn, reduces the stress induced by thermal gradients.
Fracture Toughness
Fracture toughness quantifies a material's resistance to crack propagation.
A high fracture toughness implies that a material can withstand higher stresses before a crack initiates and grows, improving its thermal shock resistance.
Elastic Modulus
The Elastic Modulus or Young's Modulus is a measure of stiffness.
A lower elastic modulus indicates a more flexible material, which can deform more readily under stress without fracturing.
In summary, thermal shock is a critical consideration in materials science and engineering.
A comprehensive understanding of its underlying principles, coupled with careful material selection and rigorous testing, is essential for designing robust and reliable products that can withstand extreme thermal environments.
Theoretical Foundations of Thermal Shock
Thermal shock, at its core, is the mechanical stress induced in a material due to rapid temperature changes. This sudden shift creates non-uniform thermal expansion or contraction, leading to internal stresses that can exceed the material's tensile strength. Ultimately, this can result in cracking or even catastrophic failure. Defining Thermal Shock resistance relies on understanding the nuanced interplay of heat transfer, thermal gradients, material properties, and time-dependent factors.
Heat Transfer Mechanisms
The manner in which heat is transferred to or from a material undergoing thermal shock is paramount. There are three primary heat transfer mechanisms: conduction, convection, and radiation.
Conduction
Conduction refers to the transfer of heat through a material by direct contact. The efficiency of conduction depends on the material's thermal conductivity. Materials with high thermal conductivity, such as metals, can rapidly dissipate heat, reducing thermal gradients and minimizing stress.
Convection
Convection involves heat transfer through the movement of fluids (liquids or gases). Forced convection, where fluid movement is mechanically induced, is far more efficient than natural convection. The rate of convective heat transfer is influenced by the fluid's properties and the surface conditions of the material.
Radiation
Radiation is the transfer of heat through electromagnetic waves. This mechanism is particularly significant at high temperatures. A material's emissivity determines its ability to radiate heat. Coatings and surface treatments can alter emissivity, influencing the rate of radiative heat transfer.
Thermal Gradients and Heat Flux
Rapid temperature changes induce thermal gradients within a material. A thermal gradient refers to the rate of change of temperature with respect to position. Steep thermal gradients lead to significant differences in thermal expansion or contraction across the material, generating high internal stresses.
Heat flux, which is the rate of heat transfer per unit area, dictates the severity of these gradients. High heat flux exacerbates thermal shock, while lower heat flux allows for more gradual temperature equalization and reduced stress.
Stress, Strain, and Temperature
The relationship between stress, strain, and temperature is central to understanding thermal shock. When a material is heated or cooled, it expands or contracts, respectively.
The extent of this expansion or contraction is governed by the material's thermal expansion coefficient. Materials with high thermal expansion coefficients experience greater dimensional changes for a given temperature change, leading to higher stresses if constrained.
Elastic Modulus and Poisson's Ratio
The elastic modulus (Young's modulus) quantifies a material's stiffness or resistance to deformation. A high elastic modulus indicates a stiffer material, which will experience higher stresses for a given strain. Poisson's ratio, on the other hand, describes the ratio of transverse strain to axial strain. This parameter influences the distribution of stresses within the material.
Fracture Mechanics Considerations
Fracture mechanics principles are crucial in predicting a material's response to thermal shock. Thermal shock can induce both crack initiation and crack propagation.
Crack Initiation
Crack initiation occurs when the stress at a point exceeds the material's local strength, often at pre-existing flaws or stress concentrators.
Crack Propagation
Crack propagation describes the growth of cracks under sustained stress. The rate of crack propagation depends on the material's fracture toughness, which is its resistance to crack growth. Materials with high fracture toughness are more resistant to thermal shock.
Influence of Time-Dependent Factors
Dwell time, transfer time, and ramp rate are critical time-dependent factors that significantly influence the magnitude of induced stresses during thermal shock.
Dwell Time
Dwell time refers to the duration a material is held at a specific temperature. Longer dwell times can allow for stress relaxation through creep or other mechanisms. Shorter dwell times intensify the effect of thermal gradients.
Transfer Time
Transfer time is the time taken to move a material between different temperature environments. Minimizing transfer time ensures the most rapid temperature change, often leading to the most severe thermal shock.
Ramp Rate
The ramp rate, or the rate of temperature change, directly affects the magnitude of thermal stresses. High ramp rates induce steeper thermal gradients and higher stresses, while lower ramp rates allow for more gradual temperature equalization.
Understanding these theoretical foundations is paramount for designing materials and structures that can withstand the rigors of thermal shock. By carefully considering heat transfer mechanisms, thermal gradients, material properties, and time-dependent factors, engineers can mitigate the risk of failure and ensure the long-term reliability of their designs.
Materials Prone to Thermal Shock: A Comparative Analysis
Theoretical Foundations of Thermal Shock Thermal shock, at its core, is the mechanical stress induced in a material due to rapid temperature changes. This sudden shift creates non-uniform thermal expansion or contraction, leading to internal stresses that can exceed the material's tensile strength. Ultimately, this can result in cracking or even catastrophic failure. Understanding which materials are most susceptible, and why, is crucial for informed design and material selection across diverse engineering applications. The following analysis examines the thermal shock behavior of several key material classes: ceramics, glass, metals and alloys, and polymers.
Thermal Shock in Ceramics
Ceramics are widely known for their high-temperature resistance and hardness, but their behavior under thermal shock conditions can be a significant limitation.
The inherent brittleness and relatively low thermal conductivity of many ceramics make them particularly vulnerable to cracking when subjected to rapid temperature variations.
Factors Influencing Ceramic Thermal Shock Resistance
Several factors play a pivotal role in a ceramic's ability to withstand thermal shock. Grain size is a critical microstructural feature; smaller grain sizes generally lead to higher strength and improved thermal shock resistance. Porosity, conversely, often reduces thermal conductivity, exacerbating thermal stress buildup.
However, controlled porosity can sometimes improve thermal shock resistance by providing sites for stress relief. The presence of secondary phases and the overall microstructure complexity also significantly influence a ceramic's performance under thermal stress.
Applications and Challenges
Ceramics are frequently used in high-temperature applications such as furnace linings, engine components, and thermal barrier coatings. However, these applications often involve extreme thermal cycling, pushing the limits of ceramic materials.
Advanced ceramics, such as silicon carbide (SiC) and silicon nitride (Si3N4), offer improved thermal shock resistance compared to traditional ceramics like alumina (Al2O3). The selection of appropriate ceramic materials and careful design considerations are essential to ensure reliability in demanding thermal environments.
Thermal Shock in Glass
Glass, like ceramics, is a brittle material and therefore susceptible to thermal shock. However, different types of glass exhibit varying degrees of resistance based on their composition and processing.
Types of Glass and Thermal Properties
Soda-lime glass, commonly used in windows and containers, has relatively poor thermal shock resistance due to its high thermal expansion coefficient and low thermal conductivity.
Borosilicate glass, such as Pyrex, contains boron oxide, which significantly reduces thermal expansion, making it much more resistant to thermal shock. Fused silica glass, composed almost entirely of silica, boasts exceptional thermal shock resistance due to its extremely low thermal expansion coefficient.
Common Applications
Borosilicate glass is widely used in laboratory glassware and cookware due to its ability to withstand rapid temperature changes without shattering. Fused silica finds applications in high-temperature crucibles, furnace components, and other demanding environments where thermal stability is paramount.
Thermal Shock in Metals and Alloys
Metals and alloys generally exhibit better thermal shock resistance than ceramics and glass due to their higher thermal conductivity and ductility.
However, repeated thermal cycling can still lead to fatigue failure, especially at high temperatures.
Influence of Alloying Elements
The addition of alloying elements can significantly influence the thermal shock resistance of metals. For example, adding chromium to steel improves its high-temperature oxidation resistance and thermal fatigue life.
Nickel-based superalloys, containing elements like chromium, aluminum, and titanium, are designed for extreme high-temperature applications and offer excellent thermal shock resistance.
Applications Under Thermal Stress
Metals and alloys are used in a wide range of applications involving thermal cycling, including engine blocks, turbine blades, and heat exchangers. Careful material selection and design optimization are crucial to ensure the long-term reliability of these components.
Thermal Shock in Polymers
Polymers typically have the lowest thermal shock resistance compared to ceramics, glass, and metals.
Their low thermal conductivity, high thermal expansion coefficient, and relatively low glass transition temperatures make them particularly vulnerable to thermal stress.
Specific Properties
The glass transition temperature (Tg) is a critical parameter for polymers; above Tg, the material becomes much softer and more susceptible to deformation and failure. Polymers with higher thermal stability and lower thermal expansion coefficients, such as some engineering plastics and composites, offer improved thermal shock resistance.
Application Considerations
Polymers are generally not suitable for applications involving large temperature fluctuations or high-temperature environments. However, they can be used in specific applications where the thermal stresses are relatively low or where they are protected by other materials. For example, polymers can be used as coatings or insulators in certain electronic applications, but careful consideration must be given to their thermal properties and operating conditions.
Thermal Shock Testing Methodologies: A Comprehensive Overview
Theoretical foundations of thermal shock provide the necessary understanding, but the practical assessment of a material's resistance necessitates standardized testing methodologies. Several techniques exist to simulate thermal shock conditions, each with its strengths and weaknesses. Selecting the appropriate method depends on the intended application and the material properties under investigation.
Liquid-to-Liquid Thermal Shock Testing
Procedure
The liquid-to-liquid method involves rapidly transferring a sample between two liquid baths maintained at different temperatures. This is typically achieved using automated transfer systems to ensure quick and consistent transitions. The sample is held at each temperature for a predetermined dwell time, allowing it to reach thermal equilibrium before the next transfer.
Advantages
This method offers excellent heat transfer rates, facilitating rapid temperature changes. The liquid medium ensures uniform temperature distribution across the sample surface, minimizing thermal gradients within the material. It’s also relatively straightforward to implement.
Disadvantages
The choice of liquid is limited by its boiling and freezing points, restricting the temperature range achievable. Some liquids may also react with the test material, leading to inaccurate results or sample degradation. Contamination of the liquid baths is another potential concern. The method also presents significant thermal gradients.
Air-to-Air Thermal Shock Testing
Procedure
In air-to-air thermal shock testing, the sample is rapidly moved between two chambers, each maintained at a distinct temperature. As with liquid-to-liquid testing, automated transfer systems are typically employed. The dwell time in each chamber allows the sample to reach thermal equilibrium.
Advantages
This method offers a wider temperature range compared to liquid-to-liquid testing, as air does not have the same boiling or freezing point limitations. It avoids the risk of chemical reactions between the test material and the surrounding medium. It has greater ability to handle complex geometries.
Disadvantages
Heat transfer rates are lower than in liquid-to-liquid testing due to the lower thermal conductivity of air. This can result in slower temperature changes and potentially less severe thermal shock. Temperature gradients within the sample may also be more pronounced. Air uniformity can also be an issue with some setups.
Fluidized Bed Thermal Shock Testing
Procedure
The fluidized bed method utilizes a bed of solid particles (e.g., alumina) that are suspended in a stream of gas, typically air. The gas is heated or cooled to the desired temperature, and the sample is immersed in the fluidized bed. This provides a relatively uniform and rapid temperature change.
Advantages
This method offers a good compromise between heat transfer rate and temperature range. The fluidized bed provides a more uniform temperature distribution than air-to-air testing. It provides an alternative between air and liquid.
Disadvantages
The complexity of the setup is higher than other methods. Maintaining a stable and uniform fluidized bed can be challenging. The particles may also cause surface abrasion or contamination of the test material.
Oven Testing
Procedure
Oven testing, sometimes called thermal cycling, involves placing the sample in an oven and cycling the temperature between specified high and low limits. The temperature ramp rate and dwell time at each temperature are carefully controlled.
Advantages
This method is relatively simple and inexpensive to implement. It allows for long-term testing and can simulate gradual temperature changes that occur in real-world applications.
Disadvantages
Temperature change rates are slower compared to other methods. This may not accurately represent rapid thermal shock conditions. Temperature uniformity within the oven may also be a concern, especially for large samples.
Non-Destructive Testing (NDT) for Assessing Thermal Shock Damage
While the previously mentioned tests induce thermal shock, Non-Destructive Testing (NDT) methods are employed to evaluate the resulting damage without compromising the integrity of the sample. These techniques are crucial for identifying cracks, delaminations, and other defects caused by thermal stress.
Methods
Several NDT methods are commonly used:
-
Ultrasonic Testing (UT): Uses sound waves to detect internal flaws and measure material thickness. Changes in the ultrasonic signal can indicate the presence of cracks or voids.
-
Radiographic Testing (RT): Employs X-rays or gamma rays to create an image of the sample's internal structure. It helps reveal subsurface defects such as cracks and porosity.
-
Dye Penetrant Testing (DPT): Involves applying a dye to the sample surface, which penetrates any surface-breaking cracks. Excess dye is removed, and a developer is applied to draw the dye out of the cracks, making them visible.
-
Thermography: Measures the surface temperature distribution of the sample. Areas with defects may exhibit different thermal behavior, allowing for their detection.
Applications
NDT methods are essential for:
- Early detection of thermal shock damage: Identifying defects before they lead to catastrophic failure.
- Monitoring crack growth: Tracking the propagation of cracks during thermal cycling.
- Validating thermal shock models: Comparing predicted damage patterns with experimental results.
- Quality control: Ensuring that components meet specified thermal shock resistance requirements.
Ultimately, the selection of the most appropriate thermal shock testing methodology and NDT techniques should be based on a thorough understanding of the material's properties, the intended application, and the specific failure modes of concern.
Experimental Setup and Instrumentation for Thermal Shock Testing
Thermal shock testing methodologies, once selected, necessitate careful attention to the experimental setup. Precise and reliable instrumentation is paramount to obtaining meaningful and accurate results. This section outlines the crucial equipment and instrumentation required for conducting thermal shock tests, encompassing thermal shock chambers, data loggers, thermocouples, and strain gauges. A detailed discussion of their types, features, and applications follows, highlighting the importance of proper test fixture design.
Thermal Shock Chambers: Controlled Environments for Stress
Thermal shock chambers are the core of thermal shock testing, providing the controlled environment needed to induce rapid temperature changes. These chambers are designed to quickly transfer samples between extreme temperatures, thereby simulating real-world thermal stresses.
Types of Thermal Shock Chambers
Several types of thermal shock chambers exist, each tailored to specific testing needs:
-
Single-zone chambers typically involve manually moving the test specimen between hot and cold zones. They offer a basic but less automated solution.
-
Multi-zone chambers, on the other hand, automate this transfer process. They utilize baskets or elevators to rapidly move samples between independently controlled hot and cold zones. These chambers allow for precise control over dwell times and transfer rates.
-
Liquid-to-liquid chambers involve immersion in temperature-controlled fluids. This method is excellent for achieving extremely rapid temperature transitions.
Key Features of Thermal Shock Chambers
The choice of thermal shock chamber depends on the specific requirements of the test:
-
Temperature Range: This is a critical specification, as the chamber must be capable of reaching and maintaining the extreme temperatures dictated by the testing standard or application.
-
Cooling/Heating Rates: Rapid temperature transitions are essential for inducing thermal shock. Chambers with high cooling and heating rates are preferred.
-
Control Systems: Precise control over temperature, dwell time, and transfer time is crucial for repeatable and reliable results. Sophisticated control systems are essential for achieving this.
Data Loggers: Capturing the Thermal Response
Data loggers play a vital role in capturing and recording the thermal response of the test specimen during thermal shock testing. These devices allow for continuous monitoring of temperature, strain, and other relevant parameters.
Types of Data Loggers
Various types of data loggers are available, each suited to different measurement needs:
-
Temperature data loggers are used to record temperature variations over time.
-
Strain data loggers capture strain measurements, providing insights into the stress experienced by the material.
Critical Specifications
When selecting a data logger, several specifications are paramount:
-
Sampling Rate: This refers to the number of measurements taken per unit of time. A higher sampling rate is necessary to capture rapid temperature changes accurately.
-
Accuracy: The accuracy of the data logger directly impacts the reliability of the test results.
-
Storage Capacity: Sufficient storage capacity is essential to accommodate the large volume of data generated during prolonged thermal shock testing.
Data Acquisition and Analysis
Advanced data acquisition systems often include software for real-time monitoring and analysis. These tools facilitate the identification of critical events and trends during the testing process. Data analysis techniques, such as Fast Fourier Transforms (FFT), can be used to identify resonant frequencies.
Thermocouples: Precise Temperature Measurement
Thermocouples are indispensable for accurate temperature measurement during thermal shock testing. They are relatively inexpensive and reliable sensors that convert temperature differences into electrical voltage.
Thermocouple Types
Several types of thermocouples exist, each with a specific temperature range and accuracy. Common types include:
-
K-type thermocouples are versatile and widely used due to their broad temperature range and relatively low cost.
-
J-type thermocouples are suitable for lower temperature applications.
-
T-type thermocouples are accurate and stable, particularly at cryogenic temperatures.
Calibration is Critical
Proper calibration is essential to ensure the accuracy of thermocouple readings. Calibration involves comparing the thermocouple's output to a known temperature standard.
Placement for Accurate Readings
The placement of thermocouples is crucial for obtaining accurate temperature readings. Thermocouples should be placed in direct contact with the test specimen at critical locations. Adequate thermal contact is essential to minimize measurement errors.
Strain Gauges: Measuring Stress and Strain
Strain gauges are used to measure the stress and strain experienced by the test specimen during thermal shock. These sensors are bonded to the surface of the material and deform along with it, changing their electrical resistance.
Types of Strain Gauges
Different types of strain gauges are available:
-
Foil gauges are the most common type, consisting of a thin metallic foil grid bonded to a flexible backing.
-
Semiconductor gauges offer higher sensitivity but are more temperature-dependent.
Application Techniques
Proper application of strain gauges is critical for accurate measurements. The surface must be clean and smooth, and the gauge must be carefully aligned. Specialized adhesives are used to bond the gauge to the test specimen.
Data Interpretation
Interpreting strain gauge data requires careful consideration of the gauge factor and the material properties. Stress levels can be calculated from strain measurements using Hooke's Law.
Test Fixture Design: Ensuring Accurate and Reliable Results
The design of the test fixture plays a crucial role in ensuring accurate and reliable thermal shock testing. The fixture must securely hold the test specimen while allowing for unrestrained thermal expansion and contraction. The fixture material should have a low thermal expansion coefficient to minimize its impact on the test results. The design must also ensure uniform temperature distribution across the specimen. Finite Element Analysis (FEA) can be a valuable tool in optimizing test fixture design to minimize stress concentrations and ensure accurate and reliable results.
Key Influencing Factors in Thermal Shock Performance
Thermal shock testing methodologies, once selected, necessitate careful attention to the experimental setup. Precise and reliable instrumentation is paramount to obtaining meaningful and accurate results. This section outlines the crucial equipment and instrumentation required for conducting thermal shock tests.
The efficacy of thermal shock testing hinges not only on the method employed, but also on a meticulous understanding of the factors influencing material performance under extreme temperature fluctuations. These factors, including the number of thermal cycles, dwell time, transfer time, and ramp rate, directly impact the severity of the induced stresses and the likelihood of material failure. Ignoring these parameters can lead to inaccurate test results and flawed predictions regarding product reliability.
The Cumulative Effect of Thermal Cycling on Fatigue Life
Materials subjected to repeated temperature variations experience cyclic stresses, which can lead to fatigue failure even if the stress levels are below the material's yield strength. Each thermal cycle introduces microstructural changes and accumulates damage, progressively weakening the material.
Damage Accumulation
The number of thermal cycles directly correlates with the extent of fatigue damage. As the cycle count increases, the material's ability to withstand stress diminishes, eventually leading to crack initiation and propagation.
Modeling Cyclic Behavior
Predicting the fatigue life of materials under thermal shock conditions requires sophisticated modeling techniques. These models typically incorporate material properties, stress amplitude, and the number of cycles to failure. Accurate material characterization and a deep understanding of fatigue mechanisms are essential for reliable predictions.
The Significance of Dwell Time at Extreme Temperatures
Dwell time refers to the duration for which a material is held at a specific high or low temperature during a thermal shock test. It plays a crucial role in determining the extent of thermal stress relaxation or creep that occurs within the material.
Extended dwell times at elevated temperatures can induce creep, a time-dependent deformation under sustained stress. Conversely, prolonged exposure to low temperatures can cause embrittlement, reducing the material's ductility and increasing its susceptibility to fracture. Precise control and monitoring of dwell time are essential for accurately simulating real-world conditions.
Impact of Transfer Time Between Thermal Environments
The transfer time, the duration it takes to move a sample from one temperature extreme to another, profoundly influences the severity of thermal shock. A longer transfer time allows for more gradual temperature changes, reducing the thermal gradients and associated stresses within the material.
Rapid transfer times, on the other hand, induce steep temperature gradients, leading to higher thermal stresses and increasing the risk of cracking or failure. Minimizing transfer time is crucial when simulating rapid temperature fluctuations experienced in certain applications.
The Role of Ramp Rate in Generating Thermal Stresses
Ramp rate, the rate at which the temperature changes, dictates the magnitude of thermal stresses induced within the material. Higher ramp rates lead to more significant temperature differentials between the surface and the core, resulting in elevated stress levels.
Controlling the ramp rate is essential for simulating specific operational conditions and assessing a material's ability to withstand rapid temperature variations. Slower ramp rates may provide a more gradual and controlled assessment of material behavior.
Real-World Applications of Thermal Shock Testing
Thermal shock testing methodologies, once selected, necessitate careful attention to the experimental setup. Precise and reliable instrumentation is paramount to obtaining meaningful and accurate results. This section outlines the crucial equipment and instrumentation required for conducting thermal shock tests across various industries.
The capacity of a material or component to withstand rapid temperature changes is paramount across a spectrum of industries. Thermal shock testing is not merely an academic exercise but a critical gatekeeper for product reliability and safety in real-world applications.
Electronics and Semiconductors: Ensuring Component Reliability
In the realm of electronics and semiconductors, components are subjected to rigorous thermal cycling to assess their ability to withstand temperature fluctuations encountered during operation. Electronic devices generate heat during use, and their operational environments can vary widely, making them susceptible to thermal stress.
Thermal shock testing identifies potential failure points such as solder joint cracking, delamination of packaging materials, and changes in electrical performance. These tests are crucial for ensuring the longevity and reliability of electronic devices in demanding applications.
Relevant Standards and Regulations
Several standards and regulations govern thermal shock testing of electronics, including JEDEC standards (Joint Electron Device Engineering Council) and IEC standards (International Electrotechnical Commission). These standards specify the testing parameters, acceptance criteria, and documentation requirements for electronic components. Compliance with these standards is often a prerequisite for product certification and market access.
Aerospace: Rigorous Thermal Cycling for Aircraft Components
The aerospace industry demands unparalleled reliability from its components due to the extreme conditions encountered during flight. Aircraft experience significant temperature variations during ascent, cruising, and descent, subjecting critical components to repeated thermal stress.
Thermal cycling tests simulate these conditions, assessing the performance of materials, structures, and systems under extreme temperature gradients. These tests ensure the structural integrity of aircraft components, preventing failures that could have catastrophic consequences.
Stringent Reliability Requirements
Aerospace applications are governed by stringent reliability requirements and regulations, such as those outlined by the Federal Aviation Administration (FAA). These requirements mandate rigorous testing and qualification procedures to ensure the safety and performance of aircraft. Thermal shock testing plays a vital role in meeting these requirements and guaranteeing the airworthiness of aircraft.
Automotive: Withstanding Extreme Temperatures in Engine and Exhaust Systems
The automotive industry faces unique challenges in managing thermal stress, particularly in engine and exhaust systems. Engines generate high temperatures during combustion, while exhaust systems are exposed to extreme heat from exhaust gases.
Thermal shock testing is employed to evaluate the durability of materials and components used in these systems, ensuring they can withstand the rapid temperature changes encountered during vehicle operation. This testing is critical for preventing failures such as cracking, warping, and degradation of materials.
Material Selection Considerations
The selection of appropriate materials is paramount in automotive applications. Materials must possess high thermal conductivity, low thermal expansion coefficients, and excellent resistance to thermal fatigue. Thermal shock testing helps identify materials that meet these requirements, ensuring the long-term reliability of automotive components.
Medical Devices: Maintaining Integrity During Sterilization
Medical devices are subjected to various sterilization processes, including autoclaving, which involves exposing the devices to high temperatures and pressures. Thermal shock testing ensures that medical devices can withstand these sterilization processes without compromising their integrity.
This testing is critical for preventing failures such as cracking, deformation, and degradation of materials, ensuring that medical devices remain safe and effective for their intended use.
Additive Manufacturing (3D Printing): Ensuring Part Integrity
Additive manufacturing, commonly known as 3D printing, is revolutionizing manufacturing across various industries. However, 3D-printed parts can be susceptible to thermal stress due to the layer-by-layer manufacturing process and inherent material properties.
Thermal shock testing is employed to evaluate the thermal shock resistance of 3D-printed parts, ensuring they can withstand the temperature fluctuations encountered during their intended applications. This testing helps identify potential weaknesses and optimize manufacturing processes to improve part quality and reliability.
Failure Analysis of Thermal Shock-Induced Failures
Thermal shock testing methodologies, once selected, necessitate careful attention to the experimental setup. Precise and reliable instrumentation is paramount to obtaining meaningful and accurate results. This section outlines the crucial equipment and instrumentation required for conducting thermal shock tests, and subsequently, analyzing failures. Understanding the methodology behind assessing failures is critical to validating the experiment.
When a component or material fails under thermal shock conditions, a thorough failure analysis is crucial. This analysis goes beyond simply observing the damage; it aims to identify the underlying root cause of the failure. Only through a comprehensive understanding of the failure mechanism can effective preventative measures be implemented, ensuring the reliability and longevity of future designs.
Microscopy Techniques for Failure Analysis
Microscopy plays a vital role in characterizing the microstructural features associated with thermal shock failures. Both optical and electron microscopy techniques offer valuable insights into crack initiation, propagation, and fracture morphology.
Optical Microscopy
Optical microscopy provides a relatively quick and cost-effective method for initial examination. At lower magnifications, optical microscopy can reveal the overall crack patterns and surface features of the fractured component.
It's particularly useful for identifying:
- Crack initiation sites: These are often located at stress concentrators, such as sharp corners, surface defects, or grain boundaries.
- Crack propagation paths: The direction and morphology of cracks can provide clues about the stress state and material behavior during thermal shock.
- Surface oxidation or corrosion: These phenomena can weaken the material and contribute to failure.
Electron Microscopy
Electron microscopy, including Scanning Electron Microscopy (SEM) and Transmission Electron Microscopy (TEM), offers much higher magnification and resolution capabilities compared to optical microscopy.
SEM is invaluable for examining the fracture surface topography. It can reveal:
- Fracture mode: Identifying whether the failure was brittle, ductile, or a combination of both.
- Microstructural features: Observing features such as grain size, grain boundary phases, and the presence of microcracks.
- Foreign particles: Detecting contaminants or inclusions that may have acted as stress concentrators.
TEM is used for high-resolution imaging of the material's microstructure. This helps to identify:
- Defects: Dislocations, voids, and other imperfections.
- Grain boundary composition: Analyzing the chemical composition of grain boundaries, which can affect material strength and fracture resistance.
Spectroscopic Analysis
Spectroscopic techniques provide information about the chemical composition and elemental distribution within the material. Two commonly used methods are Energy-Dispersive X-ray Spectroscopy (EDS) and X-ray Photoelectron Spectroscopy (XPS).
Energy-Dispersive X-ray Spectroscopy (EDS)
EDS is typically used in conjunction with SEM. It allows for the identification and quantification of the elemental composition of the material at specific locations. In failure analysis, EDS can be used to:
- Identify contaminants: Detect the presence of foreign elements that may have contributed to the failure.
- Analyze corrosion products: Determine the composition of corrosion layers on the fracture surface.
- Map elemental distribution: Create elemental maps to visualize the distribution of different elements within the material.
X-ray Photoelectron Spectroscopy (XPS)
XPS is a surface-sensitive technique that provides information about the chemical state of the elements present on the material's surface. It can be used to:
- Identify surface oxidation states: Determine the oxidation state of elements on the surface, which can affect the material's corrosion resistance.
- Analyze surface contamination: Identify organic or inorganic contaminants on the surface.
- Study surface chemical reactions: Investigate the chemical reactions occurring on the surface during thermal shock.
Mechanical Testing for Failure Characterization
Mechanical testing provides quantitative information about the material's mechanical properties, such as fracture toughness and fatigue resistance.
Fracture Toughness Testing
Fracture toughness is a measure of a material's resistance to crack propagation. Determining the fracture toughness of a material after thermal shock can help assess the extent of damage and predict its remaining service life.
Fatigue Testing
Thermal shock often induces cyclic stresses in the material. Fatigue testing simulates these cyclic stresses to evaluate the material's resistance to fatigue crack growth. This is particularly important for components that are subjected to repeated thermal shocks during their service life.
Determining the Root Cause
The ultimate goal of failure analysis is to identify the root cause of the failure. This requires a systematic and thorough investigation, combining the information obtained from microscopy, spectroscopy, and mechanical testing.
Common root causes of thermal shock failures include:
- Material defects: Inclusions, voids, and other imperfections that act as stress concentrators.
- Design flaws: Sharp corners, inadequate fillets, and other geometric features that increase stress concentrations.
- Improper material selection: Using a material with insufficient thermal shock resistance for the application.
- Manufacturing defects: Residual stresses, surface damage, and other defects introduced during manufacturing.
- Operating conditions: Exposure to temperatures or temperature gradients exceeding the material's capabilities.
By accurately identifying the root cause, engineers can implement effective preventative measures. These preventative measures may include:
- Improving material selection: Choosing materials with higher thermal shock resistance.
- Optimizing component design: Reducing stress concentrations by modifying the geometry of the component.
- Improving manufacturing processes: Minimizing the introduction of defects during manufacturing.
- Adjusting operating conditions: Reducing the severity of thermal shock by controlling temperature gradients and exposure times.
- Implementing quality control measures: Ensuring that materials and components meet required specifications.
In conclusion, a comprehensive failure analysis is essential for understanding the mechanisms behind thermal shock failures. By combining advanced microscopy, spectroscopy, and mechanical testing techniques, along with a systematic approach to root cause determination, engineers can effectively prevent future failures and enhance the reliability of their designs.
Regulatory Standards for Thermal Shock Testing
Failure Analysis of Thermal Shock-Induced Failures Thermal shock testing methodologies, once selected, necessitate careful attention to the experimental setup. Precise and reliable instrumentation is paramount to obtaining meaningful and accurate results. This section outlines the crucial equipment and instrumentation required for conducting thermal shock tests, while this section shifts focus to a crucial aspect of ensuring validity and comparability in thermal shock testing. Regulatory standards provide a framework for consistent and reliable evaluation of material and component performance under thermal stress. These standards are critical for ensuring product safety, reliability, and compliance across various industries.
The Importance of Standardized Testing
Adherence to regulatory standards in thermal shock testing is paramount for several reasons.
Firstly, it ensures that tests are conducted in a consistent manner, allowing for meaningful comparisons between different materials or products.
Secondly, it provides a baseline for assessing whether a product meets the minimum requirements for its intended application.
Finally, standards facilitate communication and collaboration between manufacturers, suppliers, and regulatory agencies.
International Electrotechnical Commission (IEC)
The International Electrotechnical Commission (IEC) plays a vital role in developing international standards for electrical, electronic, and related technologies. IEC standards related to environmental testing, including thermal shock, are widely recognized and adopted globally.
Key IEC Standards for Thermal Shock
Several IEC standards are particularly relevant to thermal shock testing.
IEC 60068, Environmental testing, is a series of standards that specifies methods for assessing the ability of components, equipment, and other products to withstand various environmental conditions, including rapid temperature changes.
Specifically, IEC 60068-2-14 outlines test methods for temperature change, including thermal shock. It provides detailed procedures for conducting thermal shock tests using various methods such as liquid-to-liquid and air-to-air thermal shock.
Application of IEC Standards
IEC standards are applied in a wide range of industries, including electronics, telecommunications, and automotive.
For example, electronic components used in automotive applications must meet specific IEC standards for thermal shock to ensure their reliability under harsh operating conditions.
Military Standards (MIL-STD)
Military Standards (MIL-STD) are a set of standards issued by the U.S. Department of Defense to ensure the performance and reliability of military equipment. MIL-STD standards are known for their stringent requirements and rigorous testing procedures.
MIL-STD-810: Environmental Engineering Considerations and Laboratory Tests
MIL-STD-810 is a comprehensive standard that covers a wide range of environmental tests, including thermal shock.
MIL-STD-810G and its successor MIL-STD-810H, outlines test methods for evaluating the effects of temperature shock on materials and equipment.
The standard provides guidance on selecting appropriate test parameters based on the expected operating environment and performance requirements.
Application of MIL-STD Standards
MIL-STD standards are primarily used for military applications, but they are also adopted by other industries that require high levels of reliability and durability.
Aerospace, defense contractors, and manufacturers of critical infrastructure components often rely on MIL-STD standards to ensure the quality and performance of their products.
ASTM International
ASTM International, formerly known as the American Society for Testing and Materials, is a globally recognized organization that develops voluntary consensus standards for a wide range of materials, products, systems, and services.
ASTM Standards for Thermal Shock Testing
ASTM standards related to thermal shock testing cover various materials, including ceramics, glass, and metals.
ASTM C1525, Standard Test Method for Determination of Thermal Shock Resistance for Advanced Ceramics by Water Quenching, provides a method for evaluating the thermal shock resistance of advanced ceramics by quenching samples in water.
ASTM E113, Standard Test Method for Ultrasonic Examination of Metal Pipe and Tubing, may be used to detect thermal shock related damage.
The Consensus-Based Approach of ASTM
ASTM standards are developed through a consensus-based process that involves participation from a wide range of stakeholders, including manufacturers, users, government agencies, and academia.
This process ensures that ASTM standards are technically sound, relevant to industry needs, and widely accepted.
Navigating the Landscape of Regulatory Standards
Selecting the appropriate regulatory standard for thermal shock testing depends on several factors, including the type of material or product being tested, the intended application, and any specific regulatory requirements.
Consulting with experts in the field and carefully reviewing the requirements of each standard is essential for ensuring compliance and obtaining meaningful test results. Understanding the nuances of IEC, MIL-STD, and ASTM standards is vital for manufacturers seeking to validate the resilience of their products in thermally challenging environments.
Key Players in Thermal Shock Testing and Equipment Manufacturing
Thermal shock testing methodologies, once selected, necessitate careful attention to the experimental setup. Precise and reliable instrumentation is paramount to obtaining meaningful and accurate results. This section outlines the crucial equipment and services, and the companies that provide them, essential for conducting effective thermal shock tests. Selecting the right partners can significantly impact the accuracy and reliability of your testing program.
Manufacturers of Thermal Shock Chambers
The heart of thermal shock testing lies in the thermal shock chamber itself. These chambers must be capable of delivering rapid and controlled temperature transitions. A number of manufacturers specialize in these sophisticated pieces of equipment.
-
Thermotron: A recognized leader in environmental simulation equipment, Thermotron offers a wide range of thermal shock chambers. Their chambers are known for their precision, reliability, and advanced control systems. They offer both vertical and horizontal thermal shock chambers to suit various testing needs.
-
ESPEC: ESPEC is another major player in the environmental test equipment market. They provide thermal shock chambers with features such as programmable controllers. They emphasize energy efficiency and ease of use. ESPEC's equipment is widely used in electronics, automotive, and aerospace industries.
-
Cincinnati Sub-Zero (CSZ): CSZ is a well-established manufacturer with a reputation for durable and customizable thermal shock chambers. They offer solutions for diverse applications, from small-scale component testing to large-scale product evaluation. CSZ also provides comprehensive support and service options.
-
Tenney (Lunaire Environmental): As part of Lunaire Environmental, Tenney offers a range of thermal cycling and thermal shock chambers. Their chambers are designed for performance and reliability. Tenney focuses on providing solutions that meet stringent industry standards.
-
Weiss Technik: Weiss Technik is a global company offering advanced environmental simulation solutions. They specialize in thermal shock chambers with innovative features. Weiss Technik emphasizes precision, energy efficiency, and user-friendly interfaces.
When selecting a chamber manufacturer, carefully consider factors such as temperature range, transition time, chamber size, and control system capabilities. Assess the manufacturer's reputation for reliability, service, and support. This ensures the long-term value of your investment.
Reputable Testing Laboratories Offering Thermal Shock Testing Services
For organizations that prefer to outsource thermal shock testing, numerous reputable laboratories offer comprehensive testing services. These labs possess the expertise, equipment, and accreditation to conduct tests according to industry standards.
-
Element Materials Technology: Element is a leading global provider of testing, inspection, and certification services. They offer comprehensive thermal shock testing capabilities across a wide range of industries. Element’s expertise extends to failure analysis and materials characterization.
-
Intertek: Intertek is a well-known global testing and certification company. They have extensive experience in thermal shock testing. Their services cater to industries such as electronics, automotive, and aerospace. Intertek's global network offers convenient access to testing facilities.
-
SGS: SGS is another prominent global testing and certification organization. They provide a comprehensive suite of thermal shock testing services. SGS focuses on ensuring product compliance with regulatory standards and industry requirements.
-
TÜV SÜD: TÜV SÜD is a respected provider of testing, certification, and auditing services. They offer thermal shock testing services with a focus on quality and reliability. TÜV SÜD helps organizations ensure their products meet the highest safety and performance standards.
-
DNB: DNB provides comprehensive testing, inspection, and certification services, including thermal shock testing for various industries. They offer high-quality testing solutions tailored to meet specific needs and regulatory compliance.
When selecting a testing laboratory, it is crucial to verify their accreditation, experience, and adherence to relevant industry standards. Look for laboratories with a proven track record of accurate and reliable testing. This ensures the integrity of your test results.
Choosing the right thermal shock testing services or equipment can be a significant investment. Diligent research and a focus on quality are essential for ensuring accurate and dependable results. These are key to the reliability and longevity of your products.
Video: Thermal Shock Test: Methods, Applications, Standards
FAQs: Thermal Shock Test
What's the primary goal of a thermal shock test?
The primary goal of a thermal shock test is to evaluate a product's ability to withstand rapid temperature changes. It identifies potential weaknesses like cracking, delamination, or failures in seals caused by these extreme temperature fluctuations.
What are the common methods used in a thermal shock test?
Common methods include liquid-to-liquid testing, where a product is rapidly transferred between hot and cold liquid baths, and air-to-air testing. Air-to-air involves moving the product between hot and cold air chambers. Each method exposes the test items to a sudden thermal shock.
Where are thermal shock tests typically applied?
Thermal shock tests are widely applied in industries such as electronics, automotive, aerospace, and telecommunications. They are critical for assessing the reliability of components and products exposed to varying environmental conditions in their expected service life.
What standards govern thermal shock test procedures?
Standards such as MIL-STD-810, IEC 60068-2-14, and JESD22-A104 outline the recommended practices and requirements for performing a thermal shock test. These standards ensure consistent and reliable results across different testing facilities and applications.
So, there you have it – a glimpse into the world of thermal shock tests. Hopefully, this has given you a better understanding of the methods, applications, and standards involved. Whether you're designing electronics, working with ceramics, or simply curious, understanding the principles behind a thermal shock test can be incredibly valuable!