SiO2 Dielectric Constant: Key Role in Electronics
Silicon dioxide (SiO2), recognized for its stable amorphous structure, serves as a foundational material in modern electronics due to its insulating properties. Its performance in integrated circuits is largely determined by the sio2 dielectric constant, which influences capacitance and signal propagation speed. The effectiveness of SiO2 is often evaluated using tools like Capacitance-Voltage (CV) measurements, which help determine the dielectric constant under various operating conditions. Research led by entities such as the Intel Corporation continues to optimize SiO2 properties to enhance the performance and reliability of microelectronic devices.
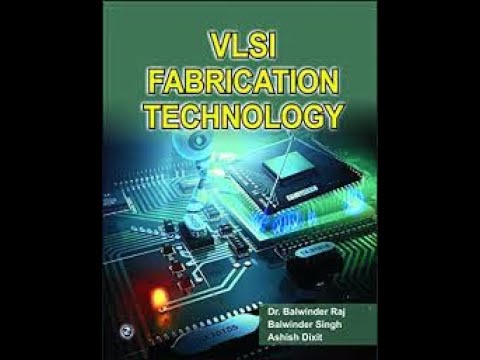
Image taken from the YouTube channel Dr.Karthikeyan A , from the video titled VLSI Fabrication and Oxidation .
Silicon dioxide (SiO2), commonly known as silica, stands as a cornerstone material in the vast landscape of microelectronics. Its ubiquitous presence within semiconductor devices is undeniable. From foundational elements to advanced architectures, SiO2 plays a crucial role.
Its widespread adoption stems from a unique combination of favorable electrical and physical properties. These characteristics enable the efficient and reliable operation of countless electronic systems. Understanding its role is paramount.
The Ubiquitous Nature of SiO2
SiO2 is predominantly utilized as an insulator or dielectric material. It is found in various components.
-
MOSFETs (Metal-Oxide-Semiconductor Field-Effect Transistors): Acts as the gate dielectric, controlling the flow of current.
-
Integrated Circuits (ICs): Provides electrical isolation between different circuit elements.
-
Memory Devices (DRAM and Flash): Serves as a charge storage medium or insulating layer.
Its versatility and ease of integration have cemented its position as a workhorse material.
Why Dielectric Properties Matter
The dielectric properties of SiO2 are paramount for optimizing semiconductor device performance.
A material's dielectric constant (εr or κ) dictates its ability to store electrical energy within an electric field. In devices like MOSFETs, a carefully chosen dielectric enables precise control over the transistor's switching behavior.
Furthermore, the dielectric strength of SiO2 determines its ability to withstand high voltages without breaking down. A high breakdown voltage ensures the reliability and longevity of electronic components. Understanding these aspects is key.
Article Scope: A Deep Dive into SiO2
This article embarks on a detailed exploration of silicon dioxide's dielectric properties and their significance in microelectronics. We will delve into:
- The fundamental characteristics that define SiO2 as a dielectric material.
- Its behavior under applied electric fields.
- Its critical applications in semiconductor devices.
- The fabrication techniques employed to create high-quality SiO2 films.
- The cutting-edge research focused on alternative dielectric materials.
By examining these facets, we aim to provide a comprehensive understanding of SiO2's role. Its lasting impact on the ever-evolving world of microelectronics will also be examined.
Dielectric Materials: A Foundation for Understanding SiO2
Silicon dioxide (SiO2), commonly known as silica, stands as a cornerstone material in the vast landscape of microelectronics. Its ubiquitous presence within semiconductor devices is undeniable. From foundational elements to advanced architectures, SiO2 plays a crucial role.
Its widespread adoption stems from a unique combination of favorable electrical properties, most notably its behavior as a dielectric. Before delving into the specifics of SiO2, it is essential to establish a solid foundation by defining dielectric materials and their key characteristics.
What are Dielectric Materials?
A dielectric material, also known as an insulator, is a substance that does not conduct electricity easily. Instead, when subjected to an electric field, it becomes polarized.
This polarization is the key to its function. Dielectrics are employed in electrical devices to increase capacitance, isolate conductors, and prevent electrical breakdown.
Common examples include ceramics, polymers, and, of course, silicon dioxide.
Permittivity: Quantifying a Material's Ability to Store Electrical Energy
The ability of a dielectric material to store electrical energy in an electric field is quantified by a property called permittivity (ε). Permittivity essentially measures how much electric field (more correctly, flux) is 'generated' per unit charge. It is a crucial parameter in determining the behavior of capacitors and other electrical components.
Absolute Permittivity vs. Relative Dielectric Constant
It's important to distinguish between absolute permittivity (ε) and relative permittivity, also known as the dielectric constant (εr or κ).
Absolute permittivity (ε) is a measure of a material's ability to permit electric fields.
Relative permittivity (εr or κ), on the other hand, is a dimensionless quantity that represents the ratio of a material's absolute permittivity (ε) to the permittivity of free space (ε₀).
εr = ε / ε₀
The dielectric constant (εr or κ) provides a convenient way to compare the dielectric properties of different materials relative to a vacuum. Materials with higher dielectric constants can store more electrical energy for a given electric field.
The Relationship Between Dielectric Constant and Capacitance
The dielectric constant (εr or κ) has a direct impact on capacitance (C), a fundamental property in circuit design. Capacitance is the measure of a device's ability to store electrical charge for a given voltage.
The relationship is expressed by the following equation:
C = εr ε₀ (A / d)
Where:
- C is the capacitance
- εr is the dielectric constant
- ε₀ is the permittivity of free space
- A is the area of the capacitor plates
- d is the distance between the plates
This equation highlights that capacitance is directly proportional to the dielectric constant. By using a material with a higher dielectric constant as the dielectric in a capacitor, we can achieve a higher capacitance for the same physical dimensions.
This is particularly important in modern microelectronics. Miniaturization demands high capacitance in ever-smaller spaces.
The dielectric constant is therefore a critical parameter for engineers to consider when designing circuits and selecting materials. Understanding this relationship is vital for optimizing device performance and achieving desired circuit characteristics.
Silicon Dioxide (SiO2) as a Dielectric: Properties and Behavior
Building upon the foundational understanding of dielectric materials, we now turn our attention to silicon dioxide (SiO2) itself. Understanding the behavior of SiO2 under electrical stress is paramount. This enables effective utilization within diverse microelectronic applications. Let us delve into its specific dielectric properties and performance characteristics that dictate its widespread adoption.
SiO2 Under Electric Field: Polarization Mechanisms
When an electric field (E) is applied across SiO2, the material undergoes polarization. This polarization arises from the displacement of charged particles within the SiO2 structure. This phenomenon is crucial to its function as a dielectric.
The polarization in SiO2 is primarily electronic and ionic. Electronic polarization involves the displacement of electron clouds relative to the nucleus of silicon and oxygen atoms. Ionic polarization refers to the slight shift in the equilibrium positions of Si and O ions within the SiO2 lattice. These displacements create dipoles that align with the external electric field. The overall effect is a reduction of the electric field within the material.
The magnitude of polarization is directly proportional to the applied electric field. This relationship is characterized by the dielectric susceptibility, which is related to the dielectric constant. A higher dielectric constant indicates a greater ability of the material to polarize and store electrical energy.
Dielectric Loss: The Tangent Delta (tan δ)
While SiO2 is an excellent dielectric, it is not perfectly lossless. Dielectric loss refers to the energy dissipated within the material as heat when subjected to an alternating electric field. This energy dissipation is quantified by the dielectric loss tangent (tan δ).
Tan δ represents the ratio of energy lost per cycle to the energy stored per cycle. A lower tan δ value indicates a more efficient dielectric material with minimal energy dissipation. Several factors contribute to dielectric loss in SiO2. These include:
- Defects and impurities: Imperfections in the SiO2 structure or the presence of impurities can lead to energy absorption and dissipation.
- Frequency dependence: Dielectric loss typically increases with the frequency of the applied electric field.
- Temperature dependence: Temperature can also influence dielectric loss, with higher temperatures generally leading to increased losses.
Excessive dielectric loss can lead to device heating. This reduces efficiency and potentially compromising long-term reliability.
Breakdown Voltage: The Limit of Insulation
Breakdown voltage is a critical parameter for any dielectric material. It represents the maximum electric field that the material can withstand before undergoing catastrophic failure. This results in a sudden surge of current. When the applied electric field exceeds the breakdown voltage, the SiO2 film can no longer effectively insulate. This leads to irreversible damage and device malfunction.
The breakdown voltage of SiO2 depends on several factors. Key factors include:
- Film thickness: Thinner films generally have lower breakdown voltages.
- Film quality: Defects and impurities within the film reduce breakdown strength.
- Temperature: Higher temperatures can lower the breakdown voltage.
Ensuring that the operating electric field remains well below the breakdown voltage is critical for ensuring device reliability and preventing catastrophic failures. Rigorous quality control measures are implemented during manufacturing. These measures ensure the SiO2 films meet the required breakdown voltage specifications for their intended applications.
SiO2 in Action: Applications in Semiconductor Devices
[Silicon Dioxide (SiO2) as a Dielectric: Properties and Behavior Building upon the foundational understanding of dielectric materials, we now turn our attention to silicon dioxide (SiO2) itself. Understanding the behavior of SiO2 under electrical stress is paramount. This enables effective utilization within diverse microelectronic applications. Let...]
Silicon dioxide's exceptional qualities have cemented its place as a cornerstone material in modern semiconductor devices.
Its versatile applications span across a multitude of technologies, including MOSFETs, CMOS circuits, and diverse memory devices. Each application exploits the unique dielectric properties of SiO2 in distinct ways.
The Indispensable Role of SiO2 in MOSFETs
The Metal-Oxide-Semiconductor Field-Effect Transistor (MOSFET) is arguably where SiO2 shines brightest. As the gate dielectric, it meticulously isolates the gate electrode from the underlying silicon channel.
This insulation is critical for controlling the flow of current between the source and drain.
The quality of the SiO2 layer directly impacts key MOSFET characteristics. These include threshold voltage, transconductance, and overall device reliability.
A thinner, high-quality SiO2 layer generally leads to improved performance, enabling faster switching speeds and reduced power consumption.
SiO2 in CMOS Technology: The Backbone of Integrated Circuits
Complementary Metal-Oxide-Semiconductor (CMOS) technology forms the backbone of most digital integrated circuits (ICs) today. SiO2 plays a fundamental role in CMOS.
It provides the necessary insulation and isolation between the n-channel and p-channel MOSFETs that comprise the CMOS logic gates.
The reliability of SiO2 within these ICs is paramount, as its failure can lead to catastrophic circuit malfunction.
The continuous miniaturization of CMOS technology demands increasingly thinner and higher-quality SiO2 films.
This pursuit drives ongoing research into alternative dielectric materials with superior properties.
SiO2 in Memory Devices: DRAM and Flash
SiO2 finds extensive use in memory devices, including Dynamic Random-Access Memory (DRAM) and Flash memory. In DRAM, SiO2 is utilized as the dielectric material in the storage capacitor.
Its ability to store electrical charge is essential for representing binary data.
In Flash memory, SiO2 is used in the gate oxide of the floating-gate transistor. This enables non-volatile storage of data.
The performance and reliability of both DRAM and Flash memory are heavily dependent on the quality and integrity of the SiO2 layers.
The Impact of Film Thickness on Device Characteristics
The thickness of the SiO2 film is a crucial parameter that significantly influences device characteristics.
Thinner films generally lead to higher capacitance, enabling faster switching speeds and improved performance.
However, excessively thin films can compromise the dielectric strength, leading to increased leakage current and reduced reliability.
A delicate balance must therefore be struck when determining the optimal SiO2 film thickness. The goal is to maximize performance while maintaining acceptable reliability.
Interface Traps: The Achilles Heel
The interface between the SiO2 layer and the silicon substrate is a critical region. Interface traps can significantly affect device performance.
These traps, arising from imperfections and dangling bonds at the interface, can capture charge carriers, leading to threshold voltage instability and reduced carrier mobility.
Careful control of the fabrication process is necessary to minimize the formation of interface traps.
Techniques such as annealing in hydrogen-rich atmospheres are commonly employed to passivate these traps and improve device performance.
Beyond SiO2: The Rise of High-k and Low-k Dielectrics
Building upon the foundational understanding of silicon dioxide's properties and applications, we now broaden our perspective to explore alternative dielectric materials. The relentless pursuit of miniaturization and performance enhancement in microelectronics has driven the exploration of dielectrics beyond traditional SiO2. This section will delve into the world of high-k and low-k materials, examining their potential benefits and drawbacks compared to SiO2, particularly within the context of Very-Large-Scale Integration (VLSI) technology.
The Need for Alternative Dielectrics
As semiconductor devices shrink, the thickness of the SiO2 gate dielectric must also decrease to maintain adequate gate control. However, scaling SiO2 indefinitely leads to several problems:
-
Increased Gate Leakage Current: Thin SiO2 layers exhibit significant quantum tunneling of electrons, leading to increased power consumption and reduced device reliability.
-
Reliability Concerns: Extremely thin SiO2 films are more susceptible to breakdown and other reliability issues.
To overcome these limitations, researchers have turned to alternative dielectric materials with higher or lower dielectric constants than SiO2.
High-k Dielectrics: Boosting Capacitance
High-k dielectrics are materials with a significantly higher dielectric constant (κ) than SiO2 (κ ≈ 3.9). The primary goal of using high-k materials is to achieve the same capacitance as a thinner SiO2 layer, but with a physically thicker layer of high-k material. This thicker layer reduces gate leakage current.
Common High-k Materials
Several high-k materials are under investigation or already in use in commercial devices. Some prominent examples include:
-
Hafnium Oxide (HfO2): One of the most widely adopted high-k dielectrics, offering a good balance of dielectric constant, thermal stability, and interface quality.
-
Zirconium Oxide (ZrO2): Another promising candidate with a high dielectric constant and good compatibility with silicon.
-
Aluminum Oxide (Al2O3): While its dielectric constant is not as high as HfO2 or ZrO2, Al2O3 offers excellent thermal stability and is often used as an interfacial layer.
Advantages of High-k Materials
The key advantages of using high-k dielectrics are:
-
Reduced Gate Leakage: Allows for physically thicker dielectric layers while maintaining capacitance, reducing leakage.
-
Improved Device Performance: Enables higher drive currents and faster switching speeds.
Challenges of High-k Materials
Despite their advantages, high-k materials also present several challenges:
-
Interface Issues: High-k materials can react with the silicon substrate, forming interfacial layers with undesirable electrical properties.
-
Mobility Degradation: The presence of high-k materials can sometimes lead to a reduction in carrier mobility in the channel.
-
Material Integration: Integrating high-k materials into existing manufacturing processes can be complex and costly.
Low-k Dielectrics: Minimizing Capacitance
In contrast to high-k dielectrics, low-k materials have a lower dielectric constant than SiO2. They are primarily used as inter-metal dielectrics (IMD) in integrated circuits to reduce parasitic capacitance between metal interconnects.
Why Low-k Materials?
As device dimensions shrink and the number of interconnect layers increases, parasitic capacitance becomes a major bottleneck, leading to:
-
Increased Signal Delay: Higher capacitance slows down signal propagation.
-
Increased Power Consumption: Charging and discharging parasitic capacitances consume significant power.
Low-k dielectrics reduce these parasitic capacitances, improving performance and reducing power consumption.
Common Low-k Materials
Examples of low-k materials include:
-
Fluorinated Silicon Dioxide (FSG): Achieved by incorporating fluorine into SiO2.
-
Organic Polymers: Materials such as polyimides and parylenes.
-
Porous Materials: SiO2-based materials with controlled porosity to reduce the dielectric constant.
Challenges of Low-k Materials
Low-k materials also face several challenges:
-
Mechanical Strength: Many low-k materials are mechanically weak and susceptible to damage during manufacturing.
-
Thermal Stability: Some low-k materials degrade at high temperatures.
-
Integration Issues: Integrating low-k materials into existing processes can be challenging, particularly with regards to compatibility with other materials and process steps.
VLSI and the Dielectric Landscape
In the context of Very-Large-Scale Integration (VLSI), the choice of dielectric materials is critical for achieving optimal performance, power efficiency, and reliability. The trend towards smaller feature sizes necessitates the use of both high-k gate dielectrics and low-k inter-metal dielectrics.
Co-optimization is Key
The successful implementation of advanced VLSI technologies relies on the co-optimization of all materials and processes, including the selection and integration of appropriate dielectric materials. This requires a deep understanding of the trade-offs between different materials and the ability to tailor them to specific device requirements. Continued innovation in dielectric materials will be essential for pushing the boundaries of microelectronics and enabling the next generation of high-performance, low-power devices.
From Sand to Silicon: Fabrication and Processing of SiO2 Films
Having established the critical role of silicon dioxide (SiO2) as a dielectric material in microelectronics, it is crucial to examine the methods by which these SiO2 films are created. The journey from raw materials to functional components is a complex and tightly controlled process, and understanding the fabrication techniques is key to appreciating the performance and reliability of modern semiconductor devices.
This section delves into the core fabrication processes employed to deposit SiO2 thin films, with a focus on Plasma Enhanced Chemical Vapor Deposition (PECVD) and Thermal Oxidation. We will also explore the critical role of semiconductor fabrication facilities (fabs) and the factors that influence the quality of the final SiO2 film.
Thin Film Deposition Techniques
The deposition of SiO2 thin films is a cornerstone of semiconductor manufacturing. Two dominant techniques, Plasma Enhanced Chemical Vapor Deposition (PECVD) and Thermal Oxidation, offer distinct advantages depending on the specific application.
Plasma Enhanced Chemical Vapor Deposition (PECVD)
PECVD involves the use of plasma to enhance chemical reactions between precursor gases, enabling deposition at lower temperatures compared to traditional CVD methods. This is particularly important when working with temperature-sensitive materials or when precise control over film composition is required.
In a typical PECVD process, gases such as silane (SiH4) and nitrous oxide (N2O) or oxygen (O2) are introduced into a reaction chamber and exposed to radio frequency (RF) energy. The plasma ignites these gases, creating reactive species that deposit SiO2 onto the substrate.
PECVD offers versatility in controlling film properties, such as density, stress, and stoichiometry, by adjusting parameters like gas flow rates, pressure, temperature, and RF power. This flexibility makes PECVD a workhorse in many semiconductor manufacturing processes.
Thermal Oxidation
Thermal oxidation involves growing a layer of SiO2 directly on the silicon substrate by exposing it to an oxidizing environment at high temperatures. This can be achieved using dry oxygen (O2) or steam (H2O) as the oxidizing agent.
Dry oxidation produces high-quality SiO2 films with excellent dielectric properties and low interface trap density. However, it is a slower process compared to oxidation in steam. Steam oxidation, while faster, can result in films with slightly lower quality and higher defect densities.
Thermal oxidation is particularly attractive because it creates a nearly perfect interface between the SiO2 and the silicon substrate. This pristine interface is essential for the performance and reliability of many semiconductor devices, especially MOSFETs.
The Vital Role of Semiconductor Fabrication Facilities (Fabs)
Semiconductor fabrication facilities, commonly known as fabs, are highly specialized and sophisticated manufacturing plants where integrated circuits (ICs) are built. These facilities represent a massive capital investment, requiring billions of dollars to construct and equip.
Fabs incorporate a wide array of advanced equipment, including deposition systems, lithography tools, etching machines, and metrology instruments. These tools work in concert to precisely pattern and process silicon wafers, layer by layer, to create complex microelectronic devices.
The environment within a fab is meticulously controlled to minimize contamination. Cleanrooms maintain extremely low levels of particulate matter, temperature, humidity, and vibration. Workers wear specialized suits to prevent the introduction of contaminants that could compromise device performance.
Factors Influencing the Quality of SiO2 Films
The quality of the deposited SiO2 film is paramount to the performance and reliability of the final semiconductor device. Several factors can significantly impact the film's properties:
- Deposition Temperature: Temperature influences the reaction kinetics and film density. Higher temperatures generally lead to denser films but may also induce unwanted diffusion or stress.
- Gas Flow Rates: Precisely controlling the flow rates of precursor gases is critical for achieving the desired stoichiometry and uniformity of the SiO2 film.
- Chamber Pressure: Pressure affects the plasma characteristics in PECVD and the oxidation rate in thermal oxidation.
- Substrate Cleaning: A clean substrate surface is essential for good adhesion and uniform film growth. Contaminants can lead to defects and poor electrical properties.
- Post-Deposition Annealing: Annealing can improve the film's density, reduce stress, and passivate interface traps, enhancing overall performance.
Careful control and optimization of these factors are crucial for producing high-quality SiO2 films that meet the stringent requirements of modern microelectronics. The continuous refinement of fabrication processes remains a key area of research and development in the semiconductor industry.
Quality Control: Characterizing SiO2 Dielectric Properties
From Sand to Silicon: Fabrication and Processing of SiO2 Films Having established the critical role of silicon dioxide (SiO2) as a dielectric material in microelectronics, it is crucial to examine the methods by which these SiO2 films are created. The journey from raw materials to functional components is a complex and tightly controlled process, a...
...and it's the characterization of the resulting SiO2 films that ensures optimal performance and reliability of semiconductor devices. Several techniques are employed to assess the dielectric properties of these films, each providing unique insights into their quality. This section will delve into the most prominent of these characterization methods, namely Capacitance-Voltage (C-V) measurement and Ellipsometry, elucidating their underlying principles and their significance in quality control.
Capacitance-Voltage (C-V) Measurement
Capacitance-Voltage (C-V) measurement is a fundamental technique used to characterize the electrical properties of dielectric materials. It involves applying a varying voltage to a capacitor structure, typically a Metal-Oxide-Semiconductor (MOS) capacitor, and measuring the resulting capacitance.
The MOS capacitor consists of a metal gate electrode, an oxide layer (in this case, SiO2), and a semiconductor substrate. By analyzing the C-V curve, valuable information about the SiO2 film can be extracted. This includes:
- Oxide Thickness: The oxide thickness (Tox) is directly related to the capacitance in the accumulation region. An accurate Tox value is crucial for device modeling and performance prediction.
- Doping Concentration: The doping concentration of the semiconductor substrate can be determined from the depletion region of the C-V curve.
- Interface Trap Density: Interface traps at the SiO2-semiconductor interface can significantly impact device performance. C-V measurements can reveal the presence and density of these traps.
- Flatband Voltage: The flatband voltage (Vfb) is a key parameter that indicates the presence of fixed charges in the oxide or at the interface. Variations in Vfb can affect device threshold voltage and stability.
Interpreting C-V Curves
The shape of the C-V curve provides valuable clues about the quality of the SiO2 film. An ideal C-V curve exhibits distinct regions corresponding to accumulation, depletion, and inversion.
Deviations from this ideal behavior can indicate the presence of defects or impurities in the oxide. For instance, a stretch-out of the C-V curve suggests the presence of interface traps. A shift in the flatband voltage indicates the presence of fixed charges.
Ellipsometry
Ellipsometry is an optical technique used to characterize thin films based on the change in polarization of light upon reflection from the sample surface. It is a non-destructive method, meaning it does not damage the sample during measurement.
The technique measures two parameters, Ψ (Psi) and Δ (Delta), which are related to the amplitude ratio and phase difference of the reflected light. These parameters are then used to determine the thickness and refractive index of the SiO2 film.
Information Extracted from Ellipsometry
Ellipsometry provides crucial information about the SiO2 film:
- Film Thickness: Ellipsometry is highly accurate in determining the thickness of thin films, even down to the nanometer scale.
- Refractive Index: The refractive index is a material property that indicates how light propagates through the film. Variations in the refractive index can indicate changes in film density or composition.
- Film Uniformity: By mapping the thickness and refractive index across the surface of the sample, ellipsometry can assess the uniformity of the SiO2 film.
- Surface Roughness: Ellipsometry can also provide information about the surface roughness of the film, which can affect its electrical properties.
Advantages of Ellipsometry
Ellipsometry offers several advantages over other characterization techniques:
- Non-Destructive: As mentioned earlier, ellipsometry is a non-destructive technique. This makes it suitable for characterizing sensitive samples without damaging them.
- High Accuracy: Ellipsometry can provide highly accurate measurements of film thickness and refractive index.
- Versatility: Ellipsometry can be used to characterize a wide range of materials, including metals, semiconductors, and dielectrics.
- Speed: Ellipsometry measurements can be performed relatively quickly, making it suitable for high-throughput quality control.
Importance for Quality Control and Process Optimization
The characterization of SiO2 dielectric properties is essential for ensuring the reliability and performance of semiconductor devices. By monitoring parameters such as oxide thickness, interface trap density, and refractive index, process engineers can optimize fabrication processes to produce high-quality SiO2 films.
These measurements are crucial for:
- Identifying and correcting process deviations: By tracking key parameters over time, engineers can identify deviations from the target values and take corrective action to maintain process control.
- Improving device performance: By optimizing the properties of the SiO2 film, engineers can improve the performance of semiconductor devices, such as increasing transistor speed or reducing leakage current.
- Ensuring device reliability: High-quality SiO2 films are essential for ensuring the long-term reliability of semiconductor devices. By monitoring the dielectric properties of the film, engineers can identify potential failure mechanisms and take steps to prevent them.
In summary, Capacitance-Voltage measurements and Ellipsometry are two crucial techniques in the characterization arsenal for SiO2 dielectric films. They provide essential information about the electrical and optical properties of these films, enabling process optimization and ensuring the reliability of semiconductor devices.
The Future of Dielectrics: Research and Development
Having established the critical role of characterizing the dielectric properties of SiO2 films, it is imperative to look toward the future of dielectric materials research and development. This section acknowledges the relentless efforts dedicated to improving these materials, highlighting the key players and their contributions.
Key Contributors to Dielectric Material Advancement
The advancement of dielectric materials is not the product of a vacuum; rather, it is driven by the collective efforts of individuals, research teams, and institutions pushing the boundaries of materials science and engineering.
Key scientists and engineers are at the forefront, investigating novel materials and innovative techniques to enhance dielectric properties and performance. Their research forms the foundation upon which future microelectronic devices will be built.
Equally important are the dedicated research teams within major semiconductor companies. These teams are tasked with translating fundamental research into practical applications, optimizing dielectric materials for specific device requirements, and addressing the challenges associated with integrating new materials into existing manufacturing processes.
The Pivotal Role of Semiconductor Manufacturers
Semiconductor manufacturers play a crucial role in driving innovation in dielectric materials. These companies invest heavily in research and development, collaborating with universities and research institutions to explore new materials and technologies.
Their expertise in device fabrication and integration allows them to assess the feasibility and scalability of new dielectric materials, ensuring that innovations can be translated into high-volume manufacturing.
The relentless pursuit of smaller, faster, and more energy-efficient devices necessitates a continuous exploration of advanced dielectric materials, and semiconductor manufacturers are at the forefront of this endeavor.
The Importance of Research Institutions
Materials science research labs and microelectronics research centers are indispensable for the advancement of dielectric materials. These institutions provide a collaborative environment where researchers from diverse backgrounds can come together to tackle complex challenges.
Equipped with state-of-the-art facilities and expertise, these centers foster innovation through fundamental research, materials characterization, and device prototyping.
They serve as hubs for knowledge dissemination, training the next generation of scientists and engineers who will shape the future of microelectronics. This interdisciplinary approach is essential for accelerating the discovery and development of novel dielectric materials.
Navigating the Landscape of Advanced Dielectric Research
Several key areas dominate the current research landscape:
-
High-κ Dielectrics: Continued exploration of high-κ materials beyond hafnium-based oxides is paramount. The goal is to achieve higher dielectric constants while maintaining excellent interface quality and thermal stability. Research focuses on materials such as lanthanum oxide and other rare-earth oxides, as well as novel deposition techniques to minimize interface defects.
-
Low-κ Dielectrics: As device dimensions shrink, reducing parasitic capacitance becomes increasingly critical. Research into low-κ dielectrics focuses on developing materials with ultra-low dielectric constants and improved mechanical strength. This includes exploring porous materials, organic polymers, and aerogels.
-
2D Materials: Two-dimensional (2D) materials, such as graphene and hexagonal boron nitride (hBN), are emerging as potential candidates for ultra-thin dielectrics in future devices. Their atomic-scale thickness and unique electrical properties offer new possibilities for device miniaturization and performance enhancement.
-
Ferroelectric Materials: The integration of ferroelectric materials into memory devices and other applications is gaining momentum. Research focuses on developing ferroelectric thin films with high polarization, low coercive fields, and excellent endurance.
-
Atomic Layer Deposition (ALD): ALD is a critical technique for depositing thin, conformal dielectric films with precise control over thickness and composition. Research focuses on developing new ALD precursors and processes to improve film quality and deposition rates.
The synergistic collaboration between researchers, manufacturers, and research institutions is essential for navigating the complexities of advanced dielectric research and for ensuring that innovations translate into tangible advancements in microelectronics.
Video: SiO2 Dielectric Constant: Key Role in Electronics
FAQs: SiO2 Dielectric Constant in Electronics
Why is the dielectric constant of SiO2 important in electronics?
The sio2 dielectric constant is crucial because it directly impacts the performance of components like transistors and capacitors. A higher dielectric constant allows for greater charge storage in capacitors and can affect transistor switching speed, impacting overall circuit performance.
How does the sio2 dielectric constant affect capacitance?
The sio2 dielectric constant directly influences capacitance. A higher sio2 dielectric constant value allows a capacitor to store more electrical charge for a given size and voltage. This makes components smaller and more efficient.
What factors influence the sio2 dielectric constant?
While silicon dioxide has a generally consistent sio2 dielectric constant, slight variations can occur due to manufacturing processes, impurities, and temperature. These factors can cause minor deviations from the standard value.
How is SiO2's dielectric constant used in MOSFETs?
In MOSFETs (Metal-Oxide-Semiconductor Field-Effect Transistors), SiO2 typically forms the gate dielectric layer. The sio2 dielectric constant is essential for determining the gate capacitance, which controls the transistor's switching speed and current carrying capacity.
So, the next time you're marveling at your phone or computer, remember the unsung hero, SiO2. Its dielectric constant might seem like a small detail, but it's fundamentally enabling the electronics we rely on every single day. Pretty cool, huh?