Plastic Melting Point: A Complete Guide You Need to Know
The type of polymer significantly influences the plastic melting point, with different compositions exhibiting varying thermal behaviors. Differential Scanning Calorimetry (DSC), a common analytical technique, provides precise measurements of the plastic melting point for materials. Understanding the properties of polyethylene, one of the most widely used plastics, requires careful consideration of its plastic melting point for successful applications. Material scientists continuously investigate methods to modify the plastic melting point of different plastics to enhance their performance and broaden their applicability across various industries.
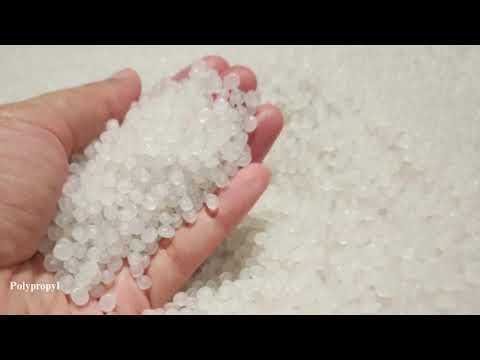
Image taken from the YouTube channel Gentle Packing , from the video titled What is polypropylene melting point? .
Plastics. They're everywhere. From the packaging that protects our food to the components that make up our cars and electronics, these synthetic materials have become an indispensable part of modern life. We often take their presence for granted, but a deeper look reveals a complex world of polymer chemistry and material science.
The Ubiquitous Nature of Plastics
Consider your immediate surroundings. The chances are high that you are within arm's reach of multiple plastic items. Perhaps it's the case of your phone, the frame of your glasses, or the keyboard you are using to read this article. This ubiquity underscores the versatility and adaptability of plastics.
They have replaced traditional materials like wood, metal, and glass in countless applications due to their properties like lightweight, durability, resistance to corrosion, and ease of manufacturing.
Why Melting Point Matters
But what makes one plastic suitable for a particular application while another fails? A crucial factor is the melting point, or more accurately, the thermal behavior of the plastic at elevated temperatures. Understanding the melting point of a plastic is essential for several reasons:
-
Material Selection: Different plastics have different melting points. Knowing these values allows engineers and designers to choose the right material for a specific application. For example, a container intended for use in a microwave oven needs to be made from a plastic with a high melting point to prevent deformation or melting.
-
Processing and Manufacturing: The melting point dictates the temperatures required for various manufacturing processes like injection molding, extrusion, and thermoforming. Incorrect temperatures can lead to defective products or damage to equipment.
-
Performance and Safety: The melting point also determines the upper limit of a plastic's service temperature. Exceeding this temperature can lead to softening, deformation, or even complete failure of the material, potentially creating safety hazards.
-
Recycling: Understanding the melting points of different plastics is crucial for effective recycling processes. Different plastics require different processing temperatures, and mixing incompatible materials can lead to poor-quality recycled products.
Guide Purpose and Scope
This guide aims to provide a comprehensive overview of plastic melting points. It will delve into the science behind melting, explore the melting points of common plastics, and discuss the factors that influence these temperatures.
By the end of this guide, you will have a solid understanding of why melting point is a critical property of plastics and how it impacts their selection, processing, and performance in various applications.
Plastics owe their versatility to their adaptability across a wide range of applications. The secret to their success lies in understanding how they behave under different conditions, especially when heated. But before we delve deeper into the specifics of different plastic types, it's essential to define what we mean by "melting point" and how it varies depending on the internal structure of the plastic itself.
Defining Melting Point: Crystalline vs. Amorphous Plastics
In the world of materials, the term "melting point" might seem straightforward, but its meaning becomes nuanced when applied to plastics. Plastics, being polymers, exhibit melting behaviors that depend heavily on their molecular arrangement. This section will clarify the definition of "melting point" in the context of plastics, distinguish between crystalline and amorphous structures, and explore the unique behavior of amorphous polymers through the concept of glass transition temperature.
What is Melting Point in Plastics?
In its simplest form, the melting point of a substance is the temperature at which it transitions from a solid to a liquid state. However, for plastics, this transition is not always as sharp or well-defined as it is for pure crystalline substances like ice.
Instead, the "melting point" for a plastic is often considered the temperature range over which it softens to the point where it loses its structural integrity and can be easily deformed or shaped.
Crystalline vs. Amorphous Plastics: A Tale of Two Structures
The key to understanding the different melting behaviors of plastics lies in their molecular structure. Plastics can be broadly classified into two categories: crystalline and amorphous.
Crystalline Plastics
Crystalline plastics possess a highly ordered molecular structure. Their polymer chains are arranged in a regular, repeating pattern, forming tightly packed regions known as crystallites.
This ordered arrangement results in a relatively sharp and well-defined melting point. As the temperature increases, the crystalline regions maintain their structure until they reach a specific temperature range, at which point the polymer chains gain enough energy to overcome the intermolecular forces holding them together, and the material transitions to a more liquid-like state.
Examples of crystalline plastics include polyethylene (PE), polypropylene (PP), and polyethylene terephthalate (PET).
Amorphous Plastics
In contrast to crystalline plastics, amorphous plastics have a disordered molecular structure. Their polymer chains are randomly arranged, lacking the long-range order found in crystalline materials.
This disordered structure means that amorphous plastics do not exhibit a sharp melting point. Instead, they gradually soften over a broad temperature range as the polymer chains gain mobility.
As a result, amorphous plastics are characterized by a glass transition temperature (Tg) rather than a distinct melting point.
Glass Transition Temperature (Tg): The Amorphous Polymer's Defining Point
The glass transition temperature (Tg) is a critical property of amorphous polymers. It represents the temperature at which the material transitions from a hard, glassy state to a more rubbery, flexible state.
Below the Tg, the polymer chains are essentially frozen in place, and the material is rigid and brittle. Above the Tg, the polymer chains gain sufficient thermal energy to move more freely, allowing the material to become more pliable and deformable.
It's important to note that the glass transition is not a phase transition in the same sense as melting. The material remains in a solid state, but its mechanical properties change dramatically.
Examples of amorphous plastics include polystyrene (PS), polycarbonate (PC), and acrylic (PMMA). The Tg values of these materials are crucial for determining their suitability for various applications.
Understanding the difference between crystalline and amorphous structures, along with the concept of glass transition temperature, is fundamental to selecting the right plastic for a specific application.
Plastics owe their versatility to their adaptability across a wide range of applications. The secret to their success lies in understanding how they behave under different conditions, especially when heated. But before we delve deeper into the specifics of different plastic types, it's essential to define what we mean by "melting point" and how it varies depending on the internal structure of the plastic itself.
Melting Points of Common Plastics: A Detailed Overview
Having established a clear understanding of melting point in the context of both crystalline and amorphous plastics, we can now turn our attention to the specific melting behaviors of some of the most commonly used plastics. This section offers a detailed look at these materials, outlining their characteristic melting points and exploring the factors that can cause these temperatures to fluctuate.
Polyethylene (PE)
Polyethylene, one of the most ubiquitous plastics, is available in several forms, each with distinct properties and melting points. The two most common types are Low-Density Polyethylene (LDPE) and High-Density Polyethylene (HDPE).
LDPE (Low-Density Polyethylene)
LDPE is characterized by its branched molecular structure, which prevents the polymer chains from packing tightly together.
This results in a lower density and a lower melting point, typically ranging from 105°C to 115°C (221°F to 239°F).
LDPE is commonly used in applications like plastic bags, films, and flexible containers.
HDPE (High-Density Polyethylene)
In contrast to LDPE, HDPE has a linear molecular structure, allowing for tighter packing of the polymer chains.
This leads to a higher density and a higher melting point, generally between 120°C and 140°C (248°F to 284°F).
HDPE's higher melting point makes it suitable for more demanding applications, such as milk jugs, detergent bottles, and piping.
Polypropylene (PP)
Polypropylene (PP) is another widely used plastic known for its excellent chemical resistance and relatively high melting point.
PP typically melts between 130°C and 171°C (266°F and 340°F), making it suitable for applications requiring heat resistance, such as food containers, automotive parts, and textiles.
The specific melting point can vary depending on the tacticity of the polymer (the arrangement of methyl groups along the polymer chain).
Polyvinyl Chloride (PVC)
Polyvinyl Chloride (PVC) is a versatile plastic known for its rigidity and durability, especially in its unplasticized form (uPVC).
PVC does not have a distinct melting point like crystalline plastics.
Instead, it softens over a range of temperatures, generally starting around 80°C (176°F), and begins to decompose before reaching a true melting point.
The addition of plasticizers can significantly lower the softening temperature of PVC, making it more flexible.
Polyethylene Terephthalate (PET)
Polyethylene Terephthalate (PET) is a strong and lightweight plastic commonly used in beverage bottles and food packaging.
PET has a melting point ranging from 250°C to 260°C (482°F to 500°F), contributing to its suitability for containing hot-filled products.
PET's high melting point also makes it a good candidate for recycling, as it can be easily melted and reprocessed.
Polystyrene (PS)
Polystyrene (PS) is an amorphous thermoplastic that is available in two main forms: general-purpose polystyrene (GPPS) and high-impact polystyrene (HIPS).
PS has a glass transition temperature (Tg) around 100°C (212°F), above which it becomes soft and pliable.
It doesn't have a sharp melting point.
GPPS is brittle and transparent, while HIPS contains added rubber to improve its impact resistance.
Acrylonitrile Butadiene Styrene (ABS)
Acrylonitrile Butadiene Styrene (ABS) is a terpolymer made by polymerizing styrene and acrylonitrile in the presence of polybutadiene.
ABS doesn't have a distinct melting point.
Instead, it softens over a range of temperatures, typically starting around 105°C (221°F).
It is known for its toughness, impact resistance, and rigidity.
Acrylic (PMMA)
Acrylic, also known as Poly(methyl methacrylate) (PMMA), is a transparent thermoplastic often used as a lightweight alternative to glass.
PMMA has a glass transition temperature (Tg) of around 105°C (221°F).
Like other amorphous polymers, it does not have a sharp melting point.
Factors Affecting Melting Point
Several factors can influence the melting point of plastics.
-
Molecular weight plays a significant role, with higher molecular weights generally leading to higher melting points due to increased intermolecular forces.
-
Additives, such as plasticizers, can lower the melting point by increasing the space between polymer chains, reducing intermolecular forces.
-
The degree of crystallinity also affects melting point, as highly crystalline polymers have sharper and higher melting points compared to amorphous polymers.
-
External pressure can also influence the melting point, though to a lesser extent in most common applications.
Understanding the melting points of common plastics and the factors that influence them is crucial for selecting the right material for a specific application and for optimizing processing conditions.
Having established a clear understanding of melting point in the context of both crystalline and amorphous plastics, we can now turn our attention to the specific melting behaviors of some of the most commonly used plastics. This section offers a detailed look at these materials, outlining their characteristic melting points and exploring the factors that can cause these temperatures to fluctuate.
The Science Behind Melting: Polymer Chemistry Explained
The melting point of a plastic is not simply a matter of temperature; it's a direct consequence of its underlying polymer chemistry. To truly understand why different plastics melt at different temperatures, we need to explore the fundamental principles governing the behavior of these long-chain molecules. This involves examining the forces that hold these chains together and how their structure influences their thermal properties.
The Basics of Polymer Structure
Polymers, at their core, are large molecules (macromolecules) composed of repeating structural units called monomers. These monomers are linked together through covalent bonds, forming long chains.
The type of monomer and the way they are linked dictates the chemical properties of the resulting polymer. These chains can arrange themselves in various ways, influencing the physical properties, including the melting point.
Intermolecular Forces: The Glue That Binds
While covalent bonds hold the monomers together within the polymer chain, intermolecular forces are responsible for the attraction between different polymer chains. These forces, though weaker than covalent bonds, play a crucial role in determining a plastic's melting point.
The stronger these intermolecular forces, the more energy (heat) is required to overcome them and allow the polymer chains to move freely, resulting in a higher melting point.
Types of Intermolecular Forces
Several types of intermolecular forces are relevant in polymer chemistry:
-
Van der Waals forces: These are weak, short-range forces arising from temporary fluctuations in electron distribution. They are present in all polymers, but their strength depends on the shape and size of the molecules.
-
Dipole-dipole interactions: These occur between polar molecules that have a permanent dipole moment due to uneven electron sharing.
-
Hydrogen bonding: This is a particularly strong type of dipole-dipole interaction that occurs when a hydrogen atom is bonded to a highly electronegative atom like oxygen, nitrogen, or fluorine. Polymers containing these groups, such as polyamides (nylon), can form strong hydrogen bonds, leading to higher melting points.
Molecular Weight and Melting Point
The molecular weight of a polymer, which is essentially the length of the polymer chain, also significantly impacts its melting point.
Longer chains have more opportunities for intermolecular interactions, leading to stronger overall attraction and, consequently, a higher melting point. Generally, as molecular weight increases, the melting point also increases, up to a certain point where the effect plateaus.
Chain Structure and Branching
The structure of the polymer chain itself – whether it's linear, branched, or cross-linked – profoundly affects its melting behavior.
-
Linear polymers: These polymers consist of long, straight chains that can pack closely together, leading to stronger intermolecular forces and higher melting points.
-
Branched polymers: Branches disrupt the close packing of the chains, reducing intermolecular forces and lowering the melting point. The more branching, the lower the melting point tends to be.
Think of it like packing spaghetti versus a pile of tangled noodles: the tangled noodles (branched polymers) take up more space and have weaker interactions.
In summary, the melting point of a plastic is a complex interplay of polymer chemistry principles. Understanding the type of monomers, the intermolecular forces between chains, the molecular weight, and the chain structure is crucial for predicting and controlling the thermal behavior of different plastics.
Having explored the theoretical underpinnings of melting behavior, and identified melting points for commonly used plastics, it is crucial to understand how these thermal properties are actually quantified and measured. The accuracy of these measurements is paramount for effective material selection and processing, ensuring optimal performance in various applications.
Measuring Melting Point: Techniques and Tools
Determining the melting point of a plastic material is essential for quality control, material characterization, and predicting its behavior during processing and end-use. Several techniques exist to measure this crucial property, but Differential Scanning Calorimetry (DSC) stands out as the most widely used and accurate method.
Differential Scanning Calorimetry (DSC): The Gold Standard
DSC is a thermoanalytical technique that measures the amount of heat required to increase the temperature of a sample and a reference, both of which are maintained at nearly the same temperature throughout the experiment.
The basic principle of DSC involves monitoring the difference in heat flow between the sample and a reference material as they are subjected to a controlled temperature program. This difference in heat flow provides quantitative information about the thermal transitions occurring within the sample, including melting, crystallization, and glass transitions.
Principles Behind DSC
At its core, DSC relies on the principle of heat flow measurement. The instrument consists of two pans: one containing the sample of interest, and the other containing an inert reference material. Both pans are heated or cooled at a controlled rate.
When the sample undergoes a thermal transition, such as melting, it will absorb or release heat. To maintain the sample and reference at the same temperature, the DSC instrument must adjust the heat flow to either the sample or the reference pan. This difference in heat flow is then recorded as a function of temperature or time, generating a DSC curve.
The area under the peak on the DSC curve corresponds to the enthalpy change (ΔH) associated with the thermal transition. The onset and peak temperatures of the curve indicate the beginning and the maximum rate of the transition, respectively.
Determining Melting Points with DSC
The melting point is identified on the DSC curve as an endothermic peak, which represents the heat absorbed by the sample as it transitions from a solid to a liquid state. The peak temperature of this endotherm is generally taken as the melting point (Tm) of the material.
For crystalline polymers, the DSC curve typically exhibits a sharp and well-defined melting peak. This sharp peak indicates a relatively narrow melting range, reflecting the highly ordered structure of the crystalline regions.
In contrast, amorphous polymers do not exhibit a distinct melting point. Instead, they show a glass transition temperature (Tg), which is a second-order transition representing the temperature at which the polymer transitions from a glassy, brittle state to a rubbery state. The Tg appears on the DSC curve as a step change in the heat flow.
Other Methods for Measuring Melting Points
While DSC is the most prevalent technique, other methods can be employed to estimate melting points, though often with lower accuracy or for specific applications:
-
Hot Stage Microscopy: This technique involves observing the sample under a microscope while heating it on a hot stage. The melting point is determined visually as the temperature at which the first signs of melting are observed. This method is useful for qualitative analysis and for observing the morphology of the melting process.
-
Melt Flow Index (MFI): Although primarily used to assess the flow properties of molten plastics, the MFI test can provide an indirect indication of the processing temperature range, which is related to the melting point. However, it doesn't directly measure the melting point.
-
Thermal Mechanical Analysis (TMA): TMA measures the dimensional changes of a material as a function of temperature. The softening point or the temperature at which significant deformation occurs can be correlated to the melting point, especially for amorphous polymers.
Factors Affecting Accuracy of Melting Point Measurements
Several factors can influence the accuracy and reproducibility of melting point measurements. These factors need to be carefully controlled to obtain reliable data:
-
Sample Preparation: The sample's purity, size, and thermal history can all affect the melting point. Ensure the sample is representative of the material and free from contaminants.
-
Heating Rate: The heating rate used during DSC measurements can influence the observed melting point. Slower heating rates generally provide more accurate results, as they allow for better thermal equilibrium within the sample.
-
Calibration of the Instrument: Regular calibration of the DSC instrument using standard materials with known melting points is crucial for ensuring accurate temperature readings.
-
Atmosphere: The atmosphere surrounding the sample during the measurement can also affect the results. For example, oxidative degradation can occur at elevated temperatures in the presence of oxygen, which can alter the melting behavior.
-
Polymer Composition: Factors such as the molecular weight distribution, copolymer ratios, and the presence of additives can influence a polymers melting points, making it vital to understanding its composition during analysis.
By carefully considering these factors and adhering to standardized testing procedures, accurate and reliable melting point measurements can be obtained, leading to better material selection, processing, and product performance.
Having understood how melting points are measured, it's time to turn our attention to the factors that govern them. The melting point of a plastic is not a fixed, immutable property. Instead, it's a dynamic characteristic influenced by a variety of factors, each playing a crucial role in determining the temperature at which a plastic transitions from solid to liquid. Understanding these influences is key to manipulating material properties for specific applications.
Factors Influencing Plastic Melting Point: A Deeper Dive
The melting point of a plastic material is a complex property dictated by a confluence of factors. These include intrinsic characteristics of the polymer itself, such as molecular weight and chain structure, as well as extrinsic influences like additives and external pressure. Let's delve into each of these factors to understand their individual and collective impact.
Molecular Weight and Its Effect
Molecular weight refers to the size of the polymer chains. It's a crucial determinant of a plastic's melting point.
Generally, as the molecular weight of a polymer increases, its melting point also increases. Longer chains have more intermolecular forces acting between them.
These stronger forces require more energy (higher temperature) to overcome, resulting in a higher melting point. However, this relationship isn't always linear.
After a certain molecular weight threshold, the increase in melting point becomes less pronounced.
The Role of Polymer Branching
Polymer branching refers to the presence of side chains extending from the main polymer backbone. Branching significantly affects the ability of polymer chains to pack closely together.
Increased branching generally leads to a lower melting point. Branches disrupt the regularity of the polymer structure, reducing crystallinity.
This reduction in crystallinity weakens intermolecular forces and lowers the energy required for melting. Linear polymers, with minimal branching, tend to have higher melting points.
Additives: Modifiers of Melting Behavior
Additives are substances incorporated into plastics to modify their properties.
Plasticizers, for example, are often added to increase flexibility and reduce brittleness. They achieve this by increasing the space between polymer chains, thus lowering the glass transition temperature (Tg) and, in some cases, the melting point.
Fillers, on the other hand, are added to enhance strength, reduce cost, or improve other properties. Fillers can have a varied effect on the melting point depending on their type and concentration.
Some fillers may increase the melting point by restricting chain movement, while others may have a negligible effect.
Crystallinity: Order and Melting Temperature
Crystallinity refers to the degree of structural order within a polymer. Crystalline polymers have highly ordered regions where the chains are tightly packed.
Amorphous polymers lack this long-range order. Higher crystallinity generally leads to a higher melting point.
The ordered structure of crystalline regions requires more energy to disrupt, resulting in a higher melting point. Amorphous polymers, lacking this ordered structure, soften over a broader temperature range.
Semi-crystalline polymers, which contain both crystalline and amorphous regions, exhibit a melting point influenced by the proportion and perfection of their crystalline domains.
External Pressure: A Less Obvious Influence
While less commonly considered, external pressure can also influence the melting point of a plastic. Increasing the pressure applied to a plastic material generally increases its melting point.
This is because increased pressure forces the molecules closer together, increasing the intermolecular forces that must be overcome for melting to occur.
The effect of pressure is more pronounced in some plastics than others, depending on their compressibility and molecular structure. In specialized applications involving high pressures, this effect becomes a significant consideration.
Having understood how melting points are measured, it's time to turn our attention to the factors that govern them. The melting point of a plastic is not a fixed, immutable property. Instead, it's a dynamic characteristic influenced by a variety of factors, each playing a crucial role in determining the temperature at which a plastic transitions from solid to liquid. Understanding these influences is key to manipulating material properties for specific applications.
Practical Implications: Melting Point in Real-World Applications
The melting point of a plastic is more than just a scientific data point. It's a critical parameter that dictates its suitability for various real-world applications.
From selecting the right material for a high-temperature automotive component to optimizing the settings for an injection molding process, an understanding of melting point is paramount.
This section explores the practical implications of melting points, focusing on heat resistance, polymer degradation, thermal conductivity, and processing techniques.
Heat Resistance and Material Selection
One of the most direct implications of a plastic's melting point is its heat resistance. This characteristic dictates whether a particular plastic can withstand high-temperature environments without deforming or failing.
For applications involving exposure to elevated temperatures, selecting a plastic with a sufficiently high melting point is critical.
For example, under-the-hood automotive parts, like coolant reservoirs or electrical connectors, require plastics with excellent heat resistance.
Materials like polypropylene (PP) or polyamide (PA) are often chosen for these applications due to their relatively high melting points compared to plastics like polyethylene (PE).
Similarly, in cookware or food packaging designed for microwave use, plastics like copolyester (PETG) are preferred for their ability to withstand microwave temperatures without melting or leaching harmful chemicals.
Conversely, using a plastic with a low melting point in a high-temperature application can lead to catastrophic failure.
Imagine using low-density polyethylene (LDPE) for a component in a hot water system. The material would quickly soften, deform, and potentially rupture, leading to leaks and system failure.
Polymer Degradation and Heat Exposure
The melting point is closely related to the temperature at which polymer degradation becomes a significant concern.
While a plastic may not melt immediately upon reaching its melting point, prolonged exposure to high temperatures below the melting point can still induce degradation.
Polymer degradation refers to changes in the chemical structure and physical properties of the plastic, leading to weakening, discoloration, and embrittlement.
For instance, prolonged exposure to UV radiation and heat can cause the chains of PVC to break down, leading to a yellowing appearance and reduced flexibility.
Understanding the relationship between melting point and degradation temperature is crucial for predicting the long-term performance of plastic products.
Engineers often use accelerated aging tests to simulate years of exposure to high temperatures and assess the degradation behavior of different plastics.
These tests help determine the service life of a product and identify potential failure modes.
To mitigate polymer degradation, additives like heat stabilizers and antioxidants are often incorporated into plastic formulations.
These additives can slow down the degradation process and extend the lifespan of the plastic product.
Thermal Conductivity and Melting Temperature
Thermal conductivity, the ability of a material to conduct heat, is indirectly related to the melting temperature of a plastic.
Generally, plastics are known for their low thermal conductivity compared to metals.
However, variations exist among different types of plastics. Crystalline plastics tend to have slightly higher thermal conductivity than amorphous plastics.
The rate at which heat is conducted through a plastic can influence how quickly it reaches its melting point when exposed to a heat source.
For instance, if two plastics with similar melting points are exposed to the same heat source, the one with higher thermal conductivity will heat up faster and potentially reach its melting point sooner.
The thermal conductivity of a plastic also plays a role in applications involving heat dissipation.
In electronic devices, plastics are used to encase components and provide insulation.
Choosing a plastic with a slightly higher thermal conductivity can help dissipate heat generated by the components and prevent overheating.
Fillers are sometimes added to plastic compounds to increase their thermal conductivity.
Melting Point and Plastic Processing Techniques
The melting point of a plastic is a critical parameter in various processing techniques, including:
- Injection Molding
- Extrusion
- Thermoforming
These manufacturing processes rely on heating the plastic to a molten state so that it can be shaped and molded into the desired form.
Each processing technique has an optimal temperature range that is closely related to the plastic's melting point.
In injection molding, plastic pellets are heated until molten and then injected into a mold cavity.
The temperature must be high enough to ensure that the plastic flows easily into the mold but not so high that it degrades or decomposes.
Extrusion involves forcing molten plastic through a die to create continuous shapes, such as pipes, films, or profiles.
The extrusion temperature must be carefully controlled to ensure consistent product dimensions and properties.
Thermoforming involves heating a plastic sheet until it is pliable and then shaping it over a mold using vacuum or pressure.
The heating temperature must be sufficient to soften the plastic without causing it to melt or sag excessively.
Understanding the melting point and thermal behavior of a plastic is essential for optimizing processing parameters and achieving high-quality, consistent results.
Careful control of temperature, pressure, and cooling rates is crucial to avoid defects such as warping, cracking, or surface imperfections.
Having understood how melting points are measured, it's time to turn our attention to the factors that govern them. The melting point of a plastic is not a fixed, immutable property. Instead, it's a dynamic characteristic influenced by a variety of factors, each playing a crucial role in determining the temperature at which a plastic transitions from solid to liquid. Understanding these influences is key to manipulating material properties for specific applications.
Practical Implications: Melting Point in Real-World Applications The melting point of a plastic is more than just a scientific data point. It's a critical parameter that dictates its suitability for various real-world applications. From selecting the right material for a high-temperature automotive component to optimizing the settings for an injection molding process, an understanding of melting point is paramount. This section explores the practical implications of melting points, focusing on heat resistance, polymer degradation, thermal conductivity, and processing techniques.
Now, let's delve into one of the most concerning consequences of exceeding a plastic's thermal limits: polymer degradation. While a plastic's melting point represents the temperature at which it transitions to a liquid state, significant and often irreversible damage can occur well before this point. Understanding the mechanisms and mitigation strategies for polymer degradation is crucial for ensuring the longevity and reliability of plastic components in demanding environments.
Polymer Degradation at High Temperatures: Minimizing the Damage
High temperatures, while sometimes necessary for processing or unavoidable in certain applications, can initiate a cascade of detrimental effects on polymers. This degradation compromises the structural integrity, appearance, and functionality of the plastic material. Understanding the types of degradation and how to combat them is vital for extending the lifespan of plastic products.
The Onset of Polymer Degradation
The vulnerability of polymers to heat stems from the nature of their chemical bonds. While strong, these bonds are not impervious to the disruptive effects of thermal energy.
As temperatures rise, the energy input can cause these bonds to break, leading to chain scission, cross-linking, and the formation of volatile byproducts.
These changes manifest as discoloration, embrittlement, cracking, and a loss of mechanical strength. The degree of degradation depends on the type of polymer, the temperature, the duration of exposure, and the presence of other environmental factors.
Types of Polymer Degradation
Understanding the specific mechanisms by which polymers degrade is crucial for selecting appropriate mitigation strategies. The primary types of degradation at high temperatures include thermal, oxidative, and hydrolytic degradation.
Thermal Degradation
Thermal degradation refers to the breakdown of polymer chains due solely to heat. It is often the initial form of degradation.
At elevated temperatures, the polymer chains vibrate more vigorously, increasing the probability of bond scission. This process is exacerbated by the presence of weak links or impurities within the polymer structure.
The resulting fragments can then initiate further degradation reactions, leading to a rapid decline in material properties. Polymers with poor thermal stability are particularly susceptible to this type of degradation.
Oxidative Degradation
Oxidative degradation involves the reaction of polymer chains with oxygen, accelerated by heat. This is often a chain reaction initiated by free radicals.
The presence of oxygen significantly accelerates degradation, as it readily reacts with the polymer chains, leading to chain scission, cross-linking, and the formation of carbonyl groups and other oxidized species.
This type of degradation is particularly problematic for polymers containing unsaturated bonds or those exposed to ultraviolet (UV) radiation, which can initiate the oxidation process. Antioxidants are commonly used to inhibit oxidative degradation by scavenging free radicals and interrupting the chain reaction.
Hydrolytic Degradation
Hydrolytic degradation occurs when water molecules react with the polymer chains, breaking them apart. This is particularly relevant for polymers containing ester, amide, or other hydrolyzable groups.
The rate of hydrolysis increases with temperature and humidity. Hydrolytic degradation can lead to a significant reduction in molecular weight and a corresponding loss of mechanical properties.
Polymers like polyesters (e.g., PET) and polyamides (e.g., nylon) are particularly susceptible to hydrolytic degradation.
Mitigating Polymer Degradation
Fortunately, several strategies can be employed to minimize polymer degradation in high-temperature applications. These strategies typically involve modifying the polymer composition or incorporating additives that enhance its thermal stability.
The Role of Stabilizers
Stabilizers are additives that inhibit or retard the degradation process. They are essential for extending the lifespan of plastic products exposed to heat, UV radiation, or other harsh environments.
Different types of stabilizers are effective against different degradation mechanisms. For example, antioxidants prevent oxidative degradation, while heat stabilizers inhibit thermal degradation.
Types of Stabilizers
-
Antioxidants: These scavenge free radicals, interrupting the chain reaction of oxidation. They can be primary antioxidants (e.g., hindered phenols) or secondary antioxidants (e.g., phosphites).
-
Heat Stabilizers: These prevent or slow down thermal degradation by reacting with degradation products or by neutralizing acidic species that can catalyze degradation.
-
UV Stabilizers: These absorb UV radiation, preventing it from initiating degradation reactions. They are often used in conjunction with antioxidants to provide comprehensive protection.
Other Mitigation Strategies
Beyond stabilizers, other strategies can also help to minimize polymer degradation. These include:
-
Selecting Polymers with High Thermal Stability: Choosing polymers inherently resistant to degradation is a primary defense.
-
Controlling Processing Conditions: Optimizing processing parameters like temperature and residence time can minimize thermal stress.
-
Surface Coatings: Applying protective coatings can shield the polymer from environmental factors.
By understanding the mechanisms of polymer degradation and implementing appropriate mitigation strategies, it is possible to significantly extend the lifespan and reliability of plastic components in high-temperature environments. A proactive approach to material selection and stabilization is critical for ensuring the long-term performance of plastic products.
Video: Plastic Melting Point: A Complete Guide You Need to Know
FAQs: Understanding Plastic Melting Points
Here are some common questions about the melting points of different types of plastics. This information can help you select the right plastic for your needs and understand its limitations.
What exactly does "melting point" mean for plastics?
Unlike metals, plastics often don't have a single, defined melting point. Instead, they have a softening range. Amorphous plastics gradually soften, while crystalline plastics have a sharper, but still not absolute, melting point. Knowing the plastic melting point range is crucial for manufacturing and applications.
Why do different plastics have such different melting points?
The melting point of a plastic is primarily determined by its chemical structure and the strength of the intermolecular forces between its polymer chains. Plastics with strong intermolecular forces or complex chain structures generally have higher plastic melting points.
How can I find the melting point of a specific plastic?
Refer to the manufacturer's datasheet for the specific plastic grade. These datasheets usually provide the melting point range or Vicat softening point, which is a related measurement. Online databases and material property resources can also offer estimates for the plastic melting point of common plastics.
Is it safe to heat all plastics up to their melting point?
Not all plastics are safe to heat to their melting point. Some plastics release harmful fumes or decompose before reaching their melting point. Always consult safety data sheets and follow proper ventilation guidelines when heating any plastic to near its plastic melting point.