Boiling Point of Oxygen: Uses & Safety Tips
Oxygen, a vital element for respiration and combustion, undergoes a phase transition from liquid to gas at its boiling point. This critical temperature, approximately -183 degrees Celsius (-297.4 degrees Fahrenheit), is essential for various industrial and scientific applications. For example, Linde Group, a leading gas and engineering company, uses the principles of cryogenics to liquefy and transport oxygen for medical and manufacturing purposes. Understanding the boiling point of oxygen is particularly important when using equipment such as a cryogenic Dewar flask, designed specifically for storing and handling liquefied gases at extremely low temperatures. Correct handling and storage based on established safety protocols are paramount to prevent hazards associated with liquid oxygen, underlining the importance of comprehensive safety measures in environments where liquid oxygen is used.
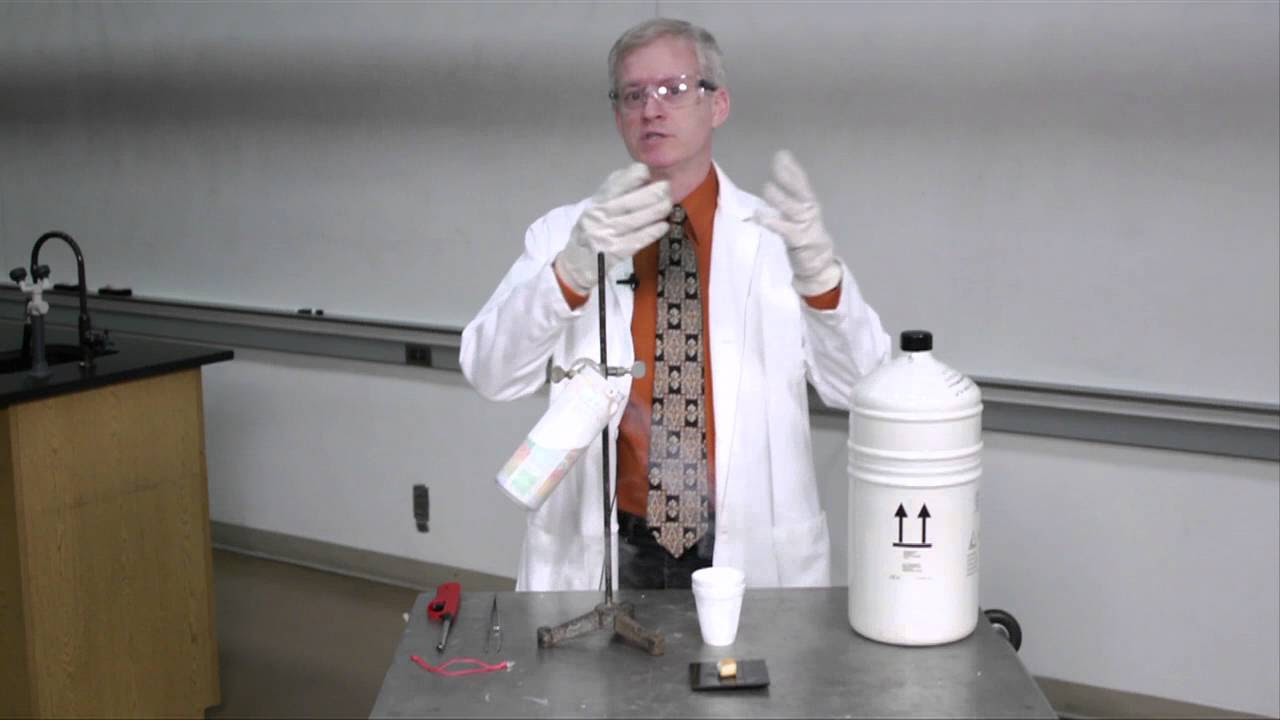
Image taken from the YouTube channel Chris Cramer , from the video titled Liquid Oxygen .
Unveiling the Science Behind Oxygen's Boiling Point
The boiling point of a substance is a fundamental physical property that dictates its behavior across a wide range of conditions. This critical temperature marks the point at which a liquid transforms into a gas, representing a dynamic equilibrium between the liquid and gaseous phases. Understanding this point is essential for numerous scientific and industrial applications.
Defining the Boiling Point
The boiling point is defined as the temperature at which the vapor pressure of a liquid equals the surrounding atmospheric pressure. At this temperature, the liquid's molecules possess sufficient kinetic energy to overcome intermolecular forces and escape into the gaseous phase.
It's a transition that impacts everything from weather patterns to chemical reactions, and industrial processes. Its importance cannot be overstated.
Introducing Oxygen (O₂) and Liquid Oxygen (LOX)
Oxygen, in its diatomic form (O₂), is a colorless, odorless, and tasteless gas vital for respiration and combustion. It makes up approximately 21% of Earth's atmosphere.
When cooled to extremely low temperatures, oxygen transitions into its liquid state, known as Liquid Oxygen (LOX). LOX is a cryogenic liquid with a boiling point of approximately -183°C (-297°F).
Liquid oxygen is characterized by its pale blue color.
LOX finds extensive use in various applications, including rocket propellant, medical respiratory support, and industrial processes. Its high density and purity make it a highly efficient source of oxygen.
Temperature, Pressure, and Oxygen's Boiling Point
The boiling point of oxygen, like any liquid, is highly dependent on pressure.
The standard boiling point, -183°C, is defined at standard atmospheric pressure (1 atm or 101.325 kPa). As pressure increases, the boiling point also increases; conversely, decreasing the pressure lowers the boiling point.
This relationship is described by the Clausius-Clapeyron equation, which mathematically relates the vapor pressure of a liquid to its temperature and enthalpy of vaporization.
The relationship between temperature, pressure, and boiling point is not just academic. It dictates the storage, handling, and applications of liquid oxygen in real-world scenarios. For example, in high-altitude environments where atmospheric pressure is lower, liquid oxygen will boil at a lower temperature.
Understanding the Core Principles: Thermodynamics and Phase Transition
[Unveiling the Science Behind Oxygen's Boiling Point The boiling point of a substance is a fundamental physical property that dictates its behavior across a wide range of conditions. This critical temperature marks the point at which a liquid transforms into a gas, representing a dynamic equilibrium between the liquid and gaseous phases. Understandi...] A deeper dive into the science behind oxygen's boiling point requires an understanding of the thermodynamic principles governing phase transitions. From the concept of latent heat to the influence of pressure, these factors dictate the conditions under which oxygen transitions from a liquid to a gaseous state.
Thermodynamics of Phase Transition: Liquid to Gas
The transition of oxygen from a liquid to a gaseous state is governed by the laws of thermodynamics, specifically the principles related to phase transitions. At a given pressure, a substance will undergo a phase transition at a specific temperature, which is its boiling point.
This transition requires energy, as the molecules must overcome the intermolecular forces holding them in the liquid phase. The driving force behind this transition is the increase in entropy (disorder) as the substance moves from a more ordered liquid state to a less ordered gaseous state.
Latent Heat of Vaporization: The Energy of Transformation
The energy required for a substance to undergo a phase change from liquid to gas at its boiling point is known as the latent heat of vaporization. For oxygen, this is the amount of heat needed to convert one mole (or kilogram) of liquid oxygen into gaseous oxygen, without changing its temperature.
This energy is used to break the intermolecular bonds between oxygen molecules in the liquid state, allowing them to escape into the gaseous phase. The latent heat of vaporization is a crucial factor in understanding the energy requirements for processes involving liquid oxygen, such as its use in rocket propulsion or industrial applications.
The Influence of Pressure: Modulating Oxygen's Boiling Point
The boiling point of oxygen, like any substance, is heavily influenced by pressure. At standard atmospheric pressure (1 atm), oxygen boils at approximately -183°C (90.2 K). However, as pressure increases, the boiling point also increases.
This relationship is described by the Clausius-Clapeyron equation, which mathematically relates the vapor pressure of a substance to its temperature and enthalpy of vaporization. In practical terms, this means that liquid oxygen can exist at higher temperatures if it is kept under increased pressure.
Conversely, reducing the pressure lowers the boiling point. This principle is utilized in various cryogenic applications, where maintaining low pressures is crucial for keeping oxygen in its liquid state at desired temperatures.
Describing the Phase Transition: From Liquid to Gaseous Oxygen
The phase transition from liquid to gaseous oxygen is characterized by a distinct change in physical properties. Liquid oxygen is a pale blue, cryogenic liquid with a high density compared to gaseous oxygen. As it absorbs heat at its boiling point, the liquid begins to vaporize, forming gaseous oxygen.
This gaseous oxygen is colorless and odorless at room temperature. The transition involves a significant increase in volume, as the molecules spread out and occupy a much larger space in the gaseous phase. This expansion is an essential consideration in the design of storage and handling systems for liquid oxygen, as it can generate high pressures if not properly managed.
Safety First: Handling and Storing Liquid Oxygen Safely
Transitioning from understanding the science behind oxygen's boiling point, we must address the paramount importance of safety when handling and storing liquid oxygen. Given its cryogenic nature and powerful oxidizing properties, liquid oxygen demands meticulous adherence to safety protocols to prevent accidents and ensure operational integrity.
Cryogenic Storage Tanks and Safety Features
Liquid oxygen is typically stored in specialized cryogenic storage tanks, designed to maintain extremely low temperatures. These tanks often consist of a double-walled construction with a vacuum insulation layer to minimize heat transfer from the environment.
Safety features include:
- Pressure relief valves: To prevent over-pressurization.
- Rupture discs: Acting as a backup pressure relief mechanism.
- Liquid level indicators: For accurate monitoring of the oxygen level.
- Temperature sensors: To ensure stable cryogenic conditions.
Regular inspection and maintenance of these tanks are critical to identify and address any potential issues before they escalate into safety hazards.
Essential Personal Protective Equipment (PPE)
Personnel handling liquid oxygen must wear appropriate Personal Protective Equipment (PPE) to mitigate the risks of cold burns, frostbite, and other injuries.
Essential PPE includes:
- Cryogenic gloves: Insulated gloves designed to protect hands from extreme cold.
- Safety glasses or face shields: To shield the eyes from splashes or vapor exposure.
- Cryogenic aprons or suits: Providing insulation and protection against cryogenic liquid exposure.
- Long-sleeved shirts and pants: To minimize skin exposure.
- Closed-toe shoes: Protecting feet from potential spills.
Ensuring that PPE is in good condition and used correctly is paramount.
Risks of Oxygen Enrichment and Prevention Measures
One of the most significant hazards associated with liquid oxygen is the risk of oxygen enrichment. Oxygen enrichment occurs when the concentration of oxygen in the air exceeds normal levels (approximately 21%).
This can dramatically increase the flammability of materials, making them easier to ignite and causing fires to burn hotter and faster.
Prevention measures include:
- Ventilation: Ensuring adequate ventilation in areas where liquid oxygen is handled or stored.
- Leak detection: Implementing systems to detect and address leaks promptly.
- Material control: Restricting the use of flammable materials in oxygen-rich environments.
Oxygen’s Role in Combustibility and Fire Safety Protocols
Oxygen itself is non-flammable, but it vigorously supports combustion. Elevated oxygen concentrations can render normally non-combustible materials flammable and significantly intensify any existing fire.
Fire safety protocols must include:
- Fire suppression systems: Installed and maintained to extinguish potential fires rapidly.
- Emergency response plans: Clearly defined procedures for responding to fires or oxygen leaks.
- Regular training: Ensuring that personnel are trained in fire safety and emergency response.
Material Compatibility for Oxygen Storage and Handling
Material compatibility is another critical consideration. Certain materials can react violently with liquid or gaseous oxygen, leading to explosions or other hazardous events.
Materials commonly used in oxygen systems include:
- Stainless steel: Known for its resistance to oxidation and compatibility with oxygen.
- Copper alloys: Suitable for certain applications, but must be carefully selected.
- Certain plastics: Such as PTFE (Teflon), which are compatible with oxygen under specific conditions.
Materials to avoid include:
- Oils, greases, and lubricants: These can react violently with oxygen.
- Carbon steel: Susceptible to corrosion in oxygen-rich environments.
- Aluminum: Can form flammable aluminum oxide.
Importance of Proper Ventilation
Proper ventilation is essential to prevent oxygen enrichment and maintain a safe working environment. Ventilation systems should be designed to effectively remove any leaked oxygen and maintain normal oxygen concentrations in the air.
Leak Detection Methods
Leak detection is a crucial aspect of safety management. Early detection of leaks can prevent oxygen enrichment, material damage, and potential fires.
Common methods include:
- Oxygen sensors: Continuously monitoring oxygen concentrations in the air.
- Soap bubble tests: Applying a soap solution to joints and connections to identify leaks.
- Ultrasonic leak detectors: Detecting leaks by listening for the sound of escaping gas.
Emergency Procedures for Leaks or Fires
Emergency procedures must be in place to address leaks or fires involving liquid oxygen. These procedures should include:
- Evacuation: Immediately evacuating the area.
- Shutting off the oxygen supply: Isolating the source of the leak or fire.
- Activating fire suppression systems: Extinguishing any fires.
- Contacting emergency services: Notifying the appropriate authorities.
Safe Storage Practices and Regulations
Safe storage practices are dictated by regulations.
Regulations are set by organizations:
- OSHA: Mandates safety standards for workplaces.
- NFPA: Provides codes and standards for fire safety.
- CGA: Develops standards for gas handling.
These regulations cover various aspects of storage, including:
- Tank design and construction: Ensuring that tanks meet specific safety requirements.
- Location: Storing tanks in well-ventilated areas away from combustible materials.
- Security: Preventing unauthorized access to storage areas.
- Signage: Clearly labeling storage areas with appropriate hazard warnings.
Compliance with these regulations is essential to ensure the safe handling and storage of liquid oxygen, protecting personnel, property, and the environment.
Essential Equipment for Oxygen Handling: A Detailed Overview
Transitioning from the crucial safety considerations surrounding liquid oxygen, it's essential to delve into the specific equipment required for its safe and efficient handling. Understanding the purpose, materials, and maintenance of each piece of equipment is vital for anyone working with this cryogenic substance.
This section provides a comprehensive overview of the essential equipment, emphasizing their role in maintaining safety and operational integrity.
Cryogenic Gloves: Protecting Against Extreme Cold
Cryogenic gloves are indispensable for protecting hands from the extreme cold of liquid oxygen. These gloves are engineered to withstand temperatures as low as -196°C (-320°F), preventing frostbite and cold burns.
They are typically constructed from multiple layers of insulating materials, such as:
- A waterproof outer layer.
- An insulating mid-layer of synthetic fibers or aerogels.
- A comfortable inner lining.
It's imperative to regularly inspect cryogenic gloves for any signs of damage, such as tears or punctures, as compromised gloves offer inadequate protection.
Gloves should be sized appropriately to ensure dexterity and a secure grip. Never handle liquid oxygen directly without proper cryogenic gloves.
Safety Glasses/Face Shields: Shielding Eyes from Splashes
Safety glasses or face shields provide crucial protection for the eyes and face from potential splashes or sprays of liquid oxygen. Even brief exposure can cause severe eye damage or frostbite.
Safety glasses should meet ANSI Z87.1 standards, ensuring they can withstand impacts and provide adequate coverage.
Face shields offer broader protection, safeguarding the entire face from splashes and vapor exposure. When handling liquid oxygen, always wear appropriate eye and face protection.
Pressure Gauges: Monitoring Oxygen Pressure
Pressure gauges are critical for monitoring the pressure within oxygen storage vessels and delivery systems. Accurate pressure readings are essential for safe operation and preventing over-pressurization.
Gauges used with oxygen systems must be specifically designed for oxygen service, constructed from materials compatible with oxygen, such as:
- Stainless steel.
- Brass.
- Copper.
Regular calibration of pressure gauges is necessary to ensure accuracy. Always verify the pressure is within the safe operating range before and during any oxygen handling procedure.
Cryogenic Storage Vessels: Maintaining Low Temperatures
Cryogenic storage vessels, such as Dewar flasks and larger storage tanks, are designed to maintain the extremely low temperatures required to keep oxygen in its liquid state. These vessels utilize vacuum insulation to minimize heat transfer from the surrounding environment.
Dewar flasks are smaller, portable containers often used in laboratories. Larger storage tanks, used in industrial settings, may incorporate additional features, such as:
- Pressure relief valves.
- Level indicators.
- Temperature sensors.
Regular inspections are essential to identify any signs of damage or deterioration, which could compromise the vessel's insulation and lead to oxygen loss.
Vaporizers: Converting Liquid to Gaseous Oxygen
Vaporizers are used to convert liquid oxygen into gaseous oxygen, providing a continuous supply for various applications. These devices use heat to raise the temperature of liquid oxygen above its boiling point, causing it to vaporize.
Vaporizers can be:
- Ambient air vaporizers.
- Electrically heated vaporizers.
- Steam-heated vaporizers.
The choice of vaporizer depends on the required flow rate and the available heat source. Ensure the vaporizer is properly sized and maintained to prevent icing or other malfunctions that could disrupt the oxygen supply.
Regulators: Controlling Oxygen Pressure
Regulators are essential for controlling the pressure of gaseous oxygen delivered from storage vessels or vaporizers. They reduce high-pressure oxygen to a safe and usable level for specific applications.
Oxygen regulators must be:
- Compatible with oxygen service.
- Equipped with pressure gauges.
- Designed to maintain a stable outlet pressure.
Regularly inspect regulators for leaks or damage and replace them as needed to ensure accurate pressure control. Never use regulators designed for other gases with oxygen, as this could create a fire hazard.
Oxygen Analyzers: Measuring Oxygen Concentration
Oxygen analyzers are used to measure the concentration of oxygen in a gaseous environment. This is critical for monitoring oxygen levels in:
- Confined spaces.
- Medical facilities.
- Industrial processes.
Analyzers employ various sensing technologies, such as:
- Electrochemical sensors.
- Paramagnetic sensors.
Regular calibration of oxygen analyzers is essential to ensure accurate readings. Monitoring oxygen concentration is crucial to prevent oxygen enrichment or deficiency, both of which pose significant safety risks.
Navigating Regulations: OSHA and NFPA Safety Standards
Transitioning from the crucial safety considerations surrounding liquid oxygen, it's essential to delve into the specific equipment required for its safe and efficient handling. Understanding the purpose, materials, and maintenance of each piece of equipment is vital for anyone working with liquid oxygen. However, equally important is adhering to the regulatory landscape established by organizations like OSHA and NFPA. These standards ensure that the handling of oxygen, particularly in its liquid form, is conducted with the utmost safety and diligence, minimizing risks across various industries and laboratories.
OSHA's Comprehensive Safety Standards for Oxygen Handling
The Occupational Safety and Health Administration (OSHA) plays a pivotal role in setting and enforcing workplace safety standards across the United States. Its regulations concerning oxygen handling are designed to protect employees from potential hazards associated with its use and storage.
Compressed Gases: A Foundational OSHA Standard
A cornerstone of OSHA's regulatory framework is the standard for compressed gases, outlined in 29 CFR 1910.101. This regulation covers the safe handling, storage, and utilization of compressed gases, including oxygen.
It mandates that cylinders be properly marked, stored in well-ventilated areas away from combustible materials, and secured to prevent tipping. This standard also addresses the proper use of regulators and other equipment to control the flow of oxygen.
Welding, Cutting, and Brazing: Specific Oxygen Use Guidelines
OSHA also provides specific guidelines for oxygen use in welding, cutting, and brazing operations under 29 CFR 1910.253. These regulations emphasize the safe use of oxygen-fuel gas systems.
They require that equipment be regularly inspected, hoses be properly maintained, and workers be trained in the safe operation of these systems. Moreover, they stipulate the separation of oxygen and fuel gas cylinders to prevent accidental mixing and potential explosions.
Hazard Communication: Ensuring Awareness of Oxygen Hazards
Another critical aspect of OSHA's safety standards is hazard communication, as detailed in 29 CFR 1910.1200. This regulation requires employers to provide employees with information and training on the hazards of chemicals in the workplace, including oxygen.
Safety Data Sheets (SDSs) must be readily available. Employees must be trained on how to handle oxygen safely, understand its properties, and recognize potential hazards.
NFPA Codes and Standards for Fire Safety and Oxygen Handling
The National Fire Protection Association (NFPA) develops and publishes codes and standards aimed at minimizing the risk and effects of fire and other hazards. While NFPA standards are not laws themselves, they are widely adopted and referenced in regulations at the federal, state, and local levels.
NFPA 51: Oxygen-Fuel Gas Systems for Welding, Cutting, and Allied Processes
NFPA 51 provides detailed requirements for the safe installation and operation of oxygen-fuel gas systems used in welding, cutting, and allied processes. It covers aspects such as cylinder storage, piping systems, regulator use, and ventilation.
The standard emphasizes the importance of preventing leaks and ensuring proper ventilation to avoid oxygen enrichment, which can significantly increase the risk of fire.
NFPA 55: Compressed Gases and Cryogenic Fluids Code
NFPA 55 is a comprehensive code that addresses the safe storage, handling, and use of compressed gases and cryogenic fluids, including oxygen. It covers a wide range of topics. These include:
- Container design.
- Storage requirements.
- Ventilation.
- Emergency shutdown systems.
The code aims to prevent incidents involving compressed gases and cryogenic fluids by providing detailed guidance on safe practices.
NFPA 704: Standard System for the Identification of the Hazards of Materials for Emergency Response
NFPA 704 provides a standardized system for identifying the hazards of materials, including oxygen, during emergency response situations. This system uses a color-coded diamond with numerical ratings to indicate the health, flammability, instability, and special hazards associated with a substance.
The NFPA 704 diamond helps emergency responders quickly assess the risks involved in an incident and take appropriate actions to mitigate those risks.
Harmonizing Safety: The Interplay Between OSHA and NFPA
While OSHA and NFPA operate independently, their standards often complement each other. OSHA frequently references NFPA codes in its regulations, effectively incorporating them into enforceable workplace safety requirements.
For instance, OSHA's standards for welding and cutting often refer to NFPA 51, while its regulations for compressed gases may reference NFPA 55. This collaboration ensures that workplaces are adhering to the best practices for oxygen handling, as defined by both regulatory and industry experts.
The Importance of Training and Compliance
Ultimately, the effectiveness of OSHA and NFPA standards depends on proper training and diligent compliance. Employers must ensure that their employees are thoroughly trained in the safe handling of oxygen. They must also understand the relevant regulations and codes.
Regular audits and inspections can help identify potential hazards. They also ensure that safety protocols are being followed consistently. By prioritizing safety and adhering to regulatory guidelines, organizations can minimize the risks associated with oxygen handling and create a safer working environment.
Oxygen in Action: Diverse Applications Across Industries
Transitioning from the regulatory landscape governing oxygen handling, it is crucial to examine the diverse applications that underscore its significance across various industries. Oxygen, in its gaseous and liquid forms, plays a pivotal role in numerous processes, shaping industries ranging from manufacturing and medicine to aerospace and environmental science. This section explores these applications, highlighting the critical roles oxygen plays in each.
Industrial Applications: The Backbone of Modern Manufacturing
Oxygen's high reactivity makes it indispensable in various industrial processes. Its ability to enhance combustion and oxidation reactions is at the heart of many manufacturing techniques.
Welding, Cutting, and Steelmaking
Oxy-fuel welding and cutting are prime examples. In these processes, oxygen is mixed with a fuel gas (such as acetylene) to produce a high-temperature flame capable of melting and cutting metals. The precisely controlled flame allows for clean, efficient cuts and strong, reliable welds.
In steelmaking, oxygen is used to remove impurities from molten iron. By injecting high-purity oxygen into the furnace, elements like carbon, silicon, and phosphorus are oxidized and removed as slag, resulting in higher quality steel. This process significantly improves the efficiency and productivity of steel manufacturing.
Other Significant Industrial Applications
Beyond welding and steelmaking, oxygen finds use in a wide array of industrial applications.
In the chemical industry, oxygen is a key reactant in the production of numerous chemicals, including ethylene oxide (used in antifreeze), propylene oxide (used in polyurethane foams), and various polymers. Its role in oxidation reactions is fundamental to these processes.
Oxygen is also employed in the pulp and paper industry for bleaching wood pulp, enhancing the brightness and quality of paper products.
In the environmental sector, oxygen is used in wastewater treatment plants to promote the breakdown of organic pollutants. This process, known as activated sludge treatment, relies on microorganisms that use oxygen to decompose waste, effectively cleaning wastewater before it is released back into the environment.
Medical Applications: Life Support and Beyond
In the medical field, oxygen is nothing short of essential for life support and various therapeutic applications.
Respiratory Therapy and Anesthesia
Oxygen therapy is a cornerstone of modern medicine. Patients with respiratory conditions, such as pneumonia, asthma, or chronic obstructive pulmonary disease (COPD), often require supplemental oxygen to maintain adequate blood oxygen levels. Oxygen is delivered via nasal cannula, masks, or ventilators, depending on the severity of the condition.
During surgery, oxygen is a critical component of anesthesia. Anesthesia machines deliver a controlled mixture of oxygen and anesthetic gases to keep patients unconscious and pain-free during procedures. Monitoring oxygen saturation levels is a standard practice to ensure patient safety.
Hyperbaric Oxygen Therapy
Hyperbaric oxygen therapy (HBOT) involves breathing pure oxygen in a pressurized chamber. This increases the amount of oxygen dissolved in the bloodstream, promoting faster healing of wounds, fighting infections, and treating conditions such as carbon monoxide poisoning and decompression sickness.
Aerospace Applications: Fueling Exploration
Oxygen plays a crucial role in aerospace, primarily as an oxidizer in rocket propulsion systems.
Rocket Propulsion
Liquid oxygen (LOX) is commonly used as an oxidizer in rocket engines. When combined with a fuel, such as liquid hydrogen or kerosene, LOX enables rapid and powerful combustion, generating the thrust needed to propel rockets into space. The high energy density and efficient combustion make LOX an indispensable component of space exploration.
Summary
From industrial manufacturing to medical treatments and aerospace exploration, oxygen's unique properties make it an indispensable element in modern society. Its diverse applications highlight its critical role in sustaining life, driving technological advancements, and shaping the world around us.
Video: Boiling Point of Oxygen: Uses & Safety Tips
FAQs About Oxygen's Boiling Point
What makes the boiling point of oxygen so important for industrial applications?
The very low boiling point of oxygen (-183°C or -297.3°F) allows it to be easily liquefied. This liquid form of oxygen can then be stored and transported efficiently for various uses, such as in steel production, medical applications, and rocket propulsion.
How does the boiling point of oxygen affect its use in cryogenic research?
Because of the boiling point of oxygen, it's a common cryogenic fluid for cooling materials to extremely low temperatures. Researchers use liquid oxygen to study material properties at these temperatures, exploring phenomena like superconductivity.
What are the biggest safety concerns when working with oxygen near its boiling point?
Handling liquid oxygen and gaseous oxygen near the boiling point of oxygen requires careful safety measures. The main risks are cryogenic burns from the extremely cold temperatures and the potential for rapid oxidation or combustion, especially in the presence of flammable materials.
Can changes in pressure affect the boiling point of oxygen, and why is this important?
Yes, increasing the pressure raises the boiling point of oxygen, while decreasing the pressure lowers it. Understanding this relationship is crucial in industrial processes and storage where pressure is controlled. It helps ensure oxygen remains in the desired state (liquid or gas) for its intended use.
So, there you have it! Oxygen's not just the air we breathe; it's a powerful element with some seriously cool (or, well, really cold!) applications. Just remember when you're working with it, understanding the boiling point of oxygen (-183°C or -297.4°F) and following those safety guidelines is key to keeping things safe and sound. Stay curious, and stay safe!