Minimum Temperature Approach: The Ultimate Guide You Need!
Process Integration, a crucial methodology in chemical engineering, heavily relies on the minimum temperature approach, a key concept often associated with Linnhoff March, pioneers in the field. This approach significantly impacts the design of Heat Exchanger Networks (HENs), influencing both capital investment and operational costs. Understanding the nuances of the minimum temperature approach, therefore, is vital for optimizing energy recovery within a plant and reducing reliance on external utilities. This guide will provide a comprehensive overview, exploring how Pinch Technology implements the minimum temperature approach to achieve substantial energy savings in various industrial processes.
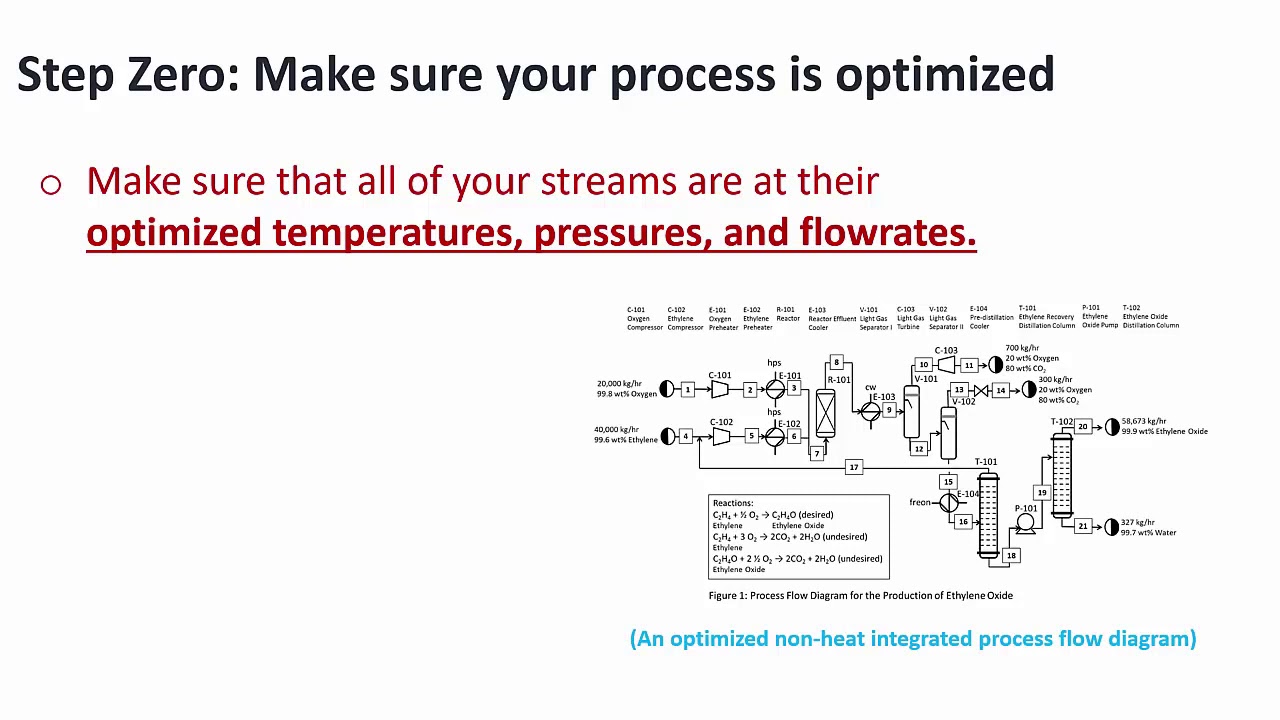
Image taken from the YouTube channel Chemical Engineering U , from the video titled Heat Integration Part 1/5: Introduction and Selecting a Minimum Approach Temperature .
In the landscape of modern process industries, the relentless pursuit of enhanced efficiency and reduced operational costs has become paramount. Amidst evolving environmental regulations and fluctuating energy prices, businesses are compelled to explore innovative methodologies that can significantly impact their bottom line while minimizing their environmental footprint.
The Minimum Temperature Approach (MTA) emerges as a powerful strategy to meet these demands, offering a systematic framework for optimizing energy consumption and maximizing heat recovery within complex industrial processes.
Defining the Minimum Temperature Approach (MTA)
At its core, the Minimum Temperature Approach (MTA) is a thermodynamic design principle focused on minimizing the temperature difference (ΔT) between hot and cold streams in heat exchange processes. By carefully analyzing and optimizing this temperature difference, MTA aims to reduce energy consumption, increase heat recovery, and ultimately improve the overall efficiency of a process.
The core principle revolves around identifying the "pinch point," the location within the process where the temperature difference between the hot and cold streams is at its minimum.
The Indispensable Role of MTA in Energy Efficiency
Energy efficiency is no longer a mere buzzword but a fundamental necessity for sustainable industrial operations. MTA plays a crucial role in achieving optimal energy efficiency by:
- Reducing the amount of energy required to heat or cool process streams.
- Maximizing the recovery and reuse of waste heat, minimizing the need for external energy inputs.
- Optimizing heat exchanger network design to ensure efficient heat transfer.
By strategically implementing MTA, companies can significantly reduce their energy consumption, leading to substantial cost savings and a reduced environmental impact.
Guide Objectives: A Comprehensive Understanding of MTA
This guide is designed to provide a comprehensive understanding of the Minimum Temperature Approach, catering to both newcomers and seasoned professionals in the field. It aims to equip readers with the knowledge and tools necessary to effectively implement MTA in their own industrial processes.
Specifically, this guide will:
- Provide a clear definition of MTA and its underlying principles.
- Illustrate the applications of MTA across various industries and processes.
- Highlight the economic, environmental, and operational advantages of MTA implementation.
- Offer practical strategies for implementing MTA, including Pinch Analysis and heat exchanger selection.
- Present real-world case studies demonstrating the successful application of MTA.
Ultimately, this guide seeks to empower readers to unlock the full potential of the Minimum Temperature Approach, driving towards more sustainable and efficient industrial operations.
In the landscape of modern process industries, the relentless pursuit of enhanced efficiency and reduced operational costs has become paramount. Amidst evolving environmental regulations and fluctuating energy prices, businesses are compelled to explore innovative methodologies that can significantly impact their bottom line while minimizing their environmental footprint.
The Minimum Temperature Approach (MTA) emerges as a powerful strategy to meet these demands, offering a systematic framework for optimizing energy consumption and maximizing heat recovery within complex industrial processes.
With the understanding of MTA now established, it becomes crucial to delve into the scientific underpinnings that justify its effectiveness. A firm grasp of the relevant thermodynamic principles and heat transfer concepts is essential for anyone seeking to implement and optimize MTA successfully.
The Foundation: Thermodynamics and Heat Transfer in MTA
The Minimum Temperature Approach isn't merely a practical technique; it is firmly rooted in the fundamental laws of thermodynamics and the principles of heat transfer. Understanding these scientific underpinnings is crucial for appreciating MTA's effectiveness and applying it optimally.
This section elucidates those principles. It establishes the scientific basis upon which MTA's value proposition rests.
Laws of Thermodynamics and Heat Exchange
Thermodynamics governs the behavior of energy and its transformations, providing the theoretical framework for understanding heat exchange processes. Several of its laws are particularly relevant to MTA.
The First Law: Conservation of Energy
The First Law, also known as the Law of Conservation of Energy, dictates that energy cannot be created or destroyed, only transformed from one form to another. In heat exchange, this means that the total energy entering a system must equal the total energy leaving it.
MTA leverages this principle by aiming to minimize energy losses during heat transfer. This is done by maximizing heat recovery and reducing the need for external heating or cooling.
The Second Law: Entropy and the Direction of Heat Flow
The Second Law of Thermodynamics introduces the concept of entropy, a measure of the disorder or randomness within a system. It states that the total entropy of an isolated system can only increase over time.
In the context of heat transfer, the Second Law dictates that heat naturally flows from a hotter body to a colder one. However, this transfer is always accompanied by an increase in entropy, representing a loss of available energy.
MTA strives to minimize this entropy generation by reducing the temperature difference between hot and cold streams, thereby making the heat transfer process more efficient.
The Third Law: Absolute Zero
While less directly applicable, the Third Law establishes that the entropy of a perfect crystal approaches zero as the temperature approaches absolute zero. It provides a theoretical lower limit for temperature and has implications for the efficiency of processes operating at cryogenic conditions.
Temperature Difference (ΔT) and Heat Exchanger Efficiency
The temperature difference (ΔT) between hot and cold streams is a critical parameter in heat exchanger design and operation. It directly impacts the rate of heat transfer and the overall efficiency of the process.
A larger ΔT drives a faster rate of heat transfer, enabling a smaller heat exchanger surface area for a given heat duty. However, as discussed with the Second Law, a larger ΔT also leads to greater irreversibility and entropy generation, resulting in a lower thermodynamic efficiency.
Conversely, a smaller ΔT reduces irreversibility and enhances efficiency. However, it necessitates a larger heat exchanger surface area, increasing capital costs.
MTA seeks to find the optimal balance between these competing factors by carefully selecting the minimum allowable ΔT. This maximizes heat recovery without incurring excessive capital expenditures.
Irreversibility and Energy Consumption
Irreversibility refers to processes that cannot be reversed without external energy input. These processes are inherently inefficient.
In heat transfer, irreversibility arises from factors such as:
- Temperature gradients
- Fluid friction
- Mixing of streams at different temperatures
These irreversible processes consume energy without producing useful work, leading to higher energy consumption and increased operating costs.
MTA directly addresses this issue by minimizing temperature differences and optimizing heat exchanger design. This reduces the degree of irreversibility and enhances the overall energy efficiency of the process. By understanding and mitigating irreversibility, MTA provides a pathway to more sustainable and cost-effective industrial operations.
In the landscape of modern process industries, the relentless pursuit of enhanced efficiency and reduced operational costs has become paramount. Amidst evolving environmental regulations and fluctuating energy prices, businesses are compelled to explore innovative methodologies that can significantly impact their bottom line while minimizing their environmental footprint.
The Minimum Temperature Approach (MTA) emerges as a powerful strategy to meet these demands, offering a systematic framework for optimizing energy consumption and maximizing heat recovery within complex industrial processes.
With the understanding of MTA now established, it becomes crucial to delve into the scientific underpinnings that justify its effectiveness. A firm grasp of the relevant thermodynamic principles and heat transfer concepts is essential for anyone seeking to implement and optimize MTA successfully.
Pinch Analysis: The Cornerstone of MTA Optimization
While understanding the thermodynamic foundation is crucial, the true power of MTA lies in its practical application through Pinch Analysis. This methodology provides a structured approach to identify opportunities for energy recovery and process optimization, making it the cornerstone of effective MTA implementation. It allows engineers to visualize energy flows, identify bottlenecks, and design heat exchanger networks that minimize energy consumption.
Understanding the Fundamentals of Pinch Analysis
Pinch Analysis is a powerful technique used to minimize energy consumption in chemical processes by identifying the thermodynamically optimal energy targets. It achieves this by analyzing the heat flows within a process and determining the minimum amount of external heating and cooling required.
The primary objectives of Pinch Analysis include:
-
Setting Realistic Energy Targets: Determining the theoretical minimum energy requirements for a process.
-
Designing Efficient Heat Exchanger Networks: Creating networks that maximize heat recovery and minimize external utility usage.
-
Identifying Process Modifications: Revealing opportunities to alter process conditions and improve overall energy efficiency.
The Step-by-Step Methodology
The Pinch Analysis methodology typically involves the following key steps:
-
Data Extraction: Gathering detailed data on all hot and cold streams within the process, including their temperatures, flow rates, and heat capacities.
-
Composite Curve Construction: Creating composite curves that represent the overall heating and cooling requirements of the process. This visualization allows for an understanding of the temperature ranges where heat is available and needed.
-
Pinch Point Identification: Determining the "Pinch Point," which is the point of closest approach between the hot and cold composite curves. This point represents the greatest thermodynamic constraint on heat recovery.
-
Target Setting: Establishing the minimum heating and cooling requirements based on the Pinch Point location.
-
Heat Exchanger Network Design: Designing a heat exchanger network that maximizes heat recovery while respecting the temperature constraints imposed by the Pinch Point.
The Significance of the "Pinch Point"
The "Pinch Point" is arguably the most critical element in Pinch Analysis. It represents the temperature at which heat transfer is most constrained within the process. Understanding its significance is paramount.
This point effectively divides the process into two distinct regions:
-
Above the Pinch: Where heat is required and should be supplied by external heating utilities.
-
Below the Pinch: Where heat needs to be rejected and should be removed by external cooling utilities.
By identifying the Pinch Point, engineers can avoid transferring heat across the pinch, a practice that would violate the Second Law of Thermodynamics and lead to increased energy consumption.
Establishing the Minimum Allowable Temperature Difference (ΔT)
Pinch Analysis also plays a crucial role in establishing the minimum allowable temperature difference (ΔT) for optimal efficiency. The ΔT is the temperature difference between the hot and cold streams in a heat exchanger.
-
A smaller ΔT leads to greater heat recovery but requires larger and more expensive heat exchangers.
-
A larger ΔT results in lower capital costs but increases energy consumption.
Pinch Analysis helps to determine the optimal balance between these two factors, identifying the ΔT that minimizes the total cost of the heat exchanger network, considering both capital and operating expenses.
Real-World Applications of Pinch Analysis
Pinch Analysis has found widespread application across various industries, demonstrating its versatility and effectiveness in optimizing energy consumption.
Examples include:
-
Chemical Industry: Optimizing heat recovery in distillation columns, reactors, and other chemical processes.
-
Petroleum Refining: Reducing energy consumption in crude oil distillation units and other refining operations.
-
Food and Beverage Industry: Improving energy efficiency in evaporation, drying, and pasteurization processes.
-
Power Generation: Optimizing heat recovery in combined heat and power (CHP) systems.
These case studies demonstrate that Pinch Analysis can lead to significant energy savings, reduced operating costs, and improved environmental performance across a wide range of industrial applications. The systematic approach of Pinch Analysis empowers engineers to make informed decisions about heat exchanger network design and process optimization, ultimately leading to more sustainable and efficient operations.
Pinch Analysis, in essence, illuminates pathways to achieve greater energy efficiency and highlights areas where heat exchange can be optimized.
The identification of the "Pinch Point" and subsequent design modifications pave the way for considerable savings. But the benefits of meticulously optimizing the Minimum Temperature Approach extend far beyond mere energy conservation.
The Multifaceted Benefits of Optimizing the MTA
The strategic optimization of the Minimum Temperature Approach (MTA) unleashes a cascade of benefits that resonate across economic, environmental, and operational dimensions. It is not simply about saving energy; it's about transforming industrial processes into more efficient, sustainable, and profitable endeavors.
Enhancing Energy Efficiency
At its core, MTA optimization is fundamentally about enhancing energy efficiency. By meticulously analyzing heat flows and identifying opportunities for heat recovery, MTA drastically reduces energy consumption. This reduction stems from minimizing waste heat, ensuring that energy input is utilized with maximum effectiveness.
Optimizing the MTA means achieving a higher output with the same or lower energy input, which results in significant improvements in overall energy efficiency.
Improving Heat Recovery
The ability to efficiently recover and reuse waste heat is a hallmark of MTA optimization. Instead of simply dissipating excess heat into the environment, MTA strategies focus on channeling this energy back into the process.
This is achieved through the implementation of optimized Heat Exchanger Networks (HENs).
Improved heat recovery translates directly into reduced demand for external heating sources, thereby lessening reliance on fossil fuels and other energy-intensive resources.
Reducing Operating Costs
The economic advantages of MTA optimization are compelling. Reduced energy consumption directly translates into lower energy bills, leading to substantial cost savings over time.
Moreover, optimizing MTA can lead to decreased raw material usage. More efficient energy usage often correlates with reduced waste and improved yields.
Streamlined production expenses further contribute to the economic benefits, creating a more financially sustainable operation.
Streamlining Process Integration
MTA facilitates improved Process Integration by promoting a more holistic and interconnected approach to process design. By considering energy flows and heat exchange opportunities early in the design phase, MTA helps to create more efficient and streamlined operations.
This integrated approach results in optimal energy utilization throughout the entire process, minimizing energy waste and maximizing productivity.
Achieving Environmental Benefits
Beyond the economic gains, MTA optimization offers significant environmental benefits. The reduction in energy consumption inevitably leads to a decrease in greenhouse gas emissions, contributing to a smaller carbon footprint.
By promoting sustainable practices, MTA enables companies to meet increasingly stringent environmental regulations and demonstrate a commitment to environmental stewardship. This proactive approach enhances brand reputation and ensures long-term sustainability.
Practical Implementation: Integrating MTA into Industrial Processes
Having explored the profound benefits of optimizing the Minimum Temperature Approach, the question naturally arises: how does one translate these theoretical advantages into tangible improvements within a real-world industrial setting? The practical implementation of MTA requires a systematic, phased approach, encompassing thorough audits, rigorous analysis, and informed equipment selection. This section provides a step-by-step guide to navigate this process effectively.
Conducting a Comprehensive Energy Audit
The first step towards integrating MTA is to conduct a comprehensive energy audit of the existing processes. This audit serves as a crucial diagnostic tool, pinpointing areas where energy is being wasted or underutilized.
The process begins with a detailed mapping of all energy inputs and outputs within the system.
This includes quantifying energy consumption by individual unit operations, identifying sources of waste heat, and assessing the overall energy efficiency of the plant.
Data collection is paramount. Accurate measurements of temperature, flow rates, pressure, and other relevant parameters are essential for a reliable analysis.
This data can then be used to construct a composite curve, visually representing the heating and cooling requirements of the process.
Leveraging Pinch Analysis for Targeted Heat Recovery
Once the energy audit is complete, the next step involves utilizing Pinch Analysis results to identify specific opportunities for heat recovery. Pinch Analysis, as previously discussed, reveals the Pinch Point, the temperature at which heat transfer is most constrained.
Understanding the Pinch Point is critical for designing effective Heat Exchanger Networks (HENs).
Heat should be recovered across the pinch, preheating cold streams with hot streams, to reduce external energy demands.
By strategically placing heat exchangers to maximize heat recovery around the Pinch Point, significant reductions in energy consumption can be achieved.
Selecting Appropriate Heat Exchangers
Selecting the appropriate Heat Exchangers is a crucial step in the MTA implementation process. The choice of heat exchanger depends on a variety of factors, including process requirements, fluid properties, operating conditions, and cost considerations.
The Temperature Difference (ΔT) is a key parameter in heat exchanger selection.
A smaller ΔT generally leads to a larger, more expensive heat exchanger, but it also results in greater energy recovery.
Different types of heat exchangers, such as shell-and-tube, plate-and-frame, and compact heat exchangers, offer varying performance characteristics and are suited for different applications.
Careful consideration must be given to factors such as fouling potential, pressure drop, and material compatibility to ensure the selected heat exchanger will operate reliably and efficiently over its lifespan.
Integrating MTA into Process Design Workflow
Integrating the Minimum Temperature Approach into the overall Process Design workflow is essential for realizing its full potential.
MTA should not be treated as an afterthought but rather as an integral part of the design process from the outset.
This requires close collaboration between process engineers, heat transfer specialists, and other relevant stakeholders.
By incorporating MTA principles into the design phase, opportunities for energy optimization can be identified early on, leading to more efficient and sustainable processes.
This proactive approach can also help avoid costly retrofits and modifications later in the project lifecycle.
Addressing Challenges, Limitations, and Considerations
Implementing MTA is not without its challenges. Potential obstacles include high capital costs, complex process interactions, and limitations in available technology.
It is important to carefully consider these challenges and develop strategies to mitigate them.
Sensitivity analysis can be used to assess the impact of uncertainties in process parameters on the performance of the MTA implementation.
Furthermore, the economic feasibility of MTA projects should be carefully evaluated, taking into account factors such as energy prices, equipment costs, and potential savings.
By proactively addressing these challenges and limitations, it is possible to successfully implement MTA and achieve significant improvements in energy efficiency and sustainability.
Having explored the profound benefits of optimizing the Minimum Temperature Approach, the question naturally arises: how does one translate these theoretical advantages into tangible improvements within a real-world industrial setting? The practical implementation of MTA requires a systematic, phased approach, encompassing thorough audits, rigorous analysis, and informed equipment selection.
Now, let's move beyond theoretical frameworks and delve into the realm of tangible results. The following section presents compelling case studies, demonstrating the transformative potential of MTA in diverse industrial landscapes.
Success Stories: Real-World MTA Applications and Results
The true measure of any optimization strategy lies in its demonstrated impact. Minimum Temperature Approach (MTA) is no exception. This section will showcase a collection of success stories, illustrating how innovative application of MTA principles has yielded significant energy savings, improved efficiency, and enhanced sustainability across various industries, with a particular emphasis on chemical engineering applications.
Chemical Engineering Triumphs: Energy Savings and Efficiency Gains
The chemical engineering sector, with its energy-intensive processes, stands to gain substantially from the strategic implementation of MTA. Let's examine a few compelling examples of successful MTA integration within this domain.
Case Study 1: Ethylene Production Optimization
Ethylene production, a cornerstone of the petrochemical industry, typically involves high-temperature cracking and complex separation processes. A leading chemical company implemented Pinch Analysis to optimize its ethylene plant's Heat Exchanger Network (HEN).
By strategically integrating heat exchangers and reducing the Minimum Temperature Approach, the company achieved a remarkable 15% reduction in overall energy consumption.
This translated into significant cost savings and a substantial decrease in greenhouse gas emissions. The success of this project highlighted the importance of a holistic approach, considering both process optimization and equipment selection.
Case Study 2: Ammonia Synthesis Enhancement
Ammonia synthesis, another energy-demanding process, relies heavily on the Haber-Bosch process. A fertilizer manufacturer, facing escalating energy costs, embarked on an MTA optimization project.
Through meticulous Pinch Analysis and redesign of the HEN, the manufacturer was able to significantly reduce the energy required for heating and cooling. The outcome was a 10% reduction in steam consumption and a corresponding decrease in the plant's carbon footprint.
This case underscores the value of thorough process analysis and the selection of highly efficient heat exchangers tailored to specific process requirements.
Beyond Chemical Engineering: MTA's Versatility in Other Sectors
While the chemical engineering industry provides particularly striking examples, the benefits of MTA extend far beyond this single sector. Let's explore successful implementations in other industrial settings, showcasing the approach's versatility and broad applicability.
Case Study 3: Food Processing Plant Efficiency
A large-scale food processing plant, struggling with high energy bills, implemented an MTA-driven heat recovery system. By capturing and reusing waste heat from various processes, such as cooking and sterilization, the plant significantly reduced its reliance on external energy sources.
The result was an impressive 20% reduction in overall energy consumption, leading to substantial cost savings and improved environmental performance.
This case demonstrates the potential of MTA to transform energy-intensive operations, even in sectors not traditionally associated with advanced chemical engineering principles.
Case Study 4: Pulp and Paper Mill Optimization
Pulp and paper mills are notorious for their high water and energy consumption. One mill adopted MTA to optimize its black liquor recovery process, a critical step in chemical recovery and energy generation.
By strategically integrating heat exchangers and minimizing the Minimum Temperature Approach, the mill improved the efficiency of the black liquor evaporation process. This resulted in a significant decrease in steam usage and a corresponding increase in the mill's energy self-sufficiency.
This success story illustrates how MTA can contribute to both economic and environmental sustainability within the pulp and paper industry.
Key Takeaways from Real-World Applications
These case studies collectively underscore several key takeaways regarding the successful implementation of Minimum Temperature Approach:
- Thorough process analysis is paramount for identifying opportunities for heat recovery and optimization.
- Pinch Analysis serves as a powerful tool for pinpointing the optimal Minimum Temperature Approach and designing effective Heat Exchanger Networks.
- Strategic equipment selection is crucial for maximizing heat transfer efficiency and achieving desired temperature differences.
- MTA is a versatile approach applicable across a wide range of industries, offering significant economic and environmental benefits.
By learning from these real-world examples, industries can unlock the full potential of Minimum Temperature Approach and pave the way for a more sustainable and efficient future.
Having explored the profound benefits of optimizing the Minimum Temperature Approach, the question naturally arises: how does one translate these theoretical advantages into tangible improvements within a real-world industrial setting? The practical implementation of MTA requires a systematic, phased approach, encompassing thorough audits, rigorous analysis, and informed equipment selection.
Now, let's move beyond theoretical frameworks and delve into the realm of tangible results. The following section presents compelling case studies, demonstrating the transformative potential of MTA in diverse industrial landscapes.
The Future of MTA: Emerging Trends and Advancements
The Minimum Temperature Approach, while already a powerful tool, is not static. Its future promises exciting developments, driven by technological innovation and a growing imperative for sustainable industrial practices. These advancements will further refine MTA methodologies, enhance equipment performance, and broaden its scope of application.
Refining Pinch Analysis with Advanced Technologies
Pinch Analysis forms the cornerstone of MTA optimization. Emerging technologies are poised to enhance its precision and effectiveness.
Advanced software tools, incorporating sophisticated algorithms and computational power, are enabling more detailed and accurate process simulations. This allows engineers to model complex systems with greater fidelity, identifying subtle opportunities for energy recovery that might be missed by traditional methods.
Furthermore, developments in sensor technology and real-time data analytics are facilitating dynamic Pinch Analysis. This involves continuously monitoring process conditions and adjusting operating parameters to maintain optimal energy efficiency, even as external factors change.
The Role of Advanced Materials in Heat Exchangers
The performance and durability of Heat Exchangers are critical to the success of any MTA implementation. Advanced materials are playing an increasingly important role in this area.
New alloys and composite materials are being developed that offer superior thermal conductivity, allowing for more efficient heat transfer. These materials can also withstand higher temperatures and pressures, expanding the range of applications for MTA.
Moreover, research is focused on materials with enhanced corrosion resistance, reducing maintenance costs and extending the lifespan of Heat Exchangers. Self-cleaning surfaces and coatings are also gaining traction, minimizing fouling and maintaining optimal performance over time.
Integrating MTA with Complementary Energy-Saving Initiatives
While MTA focuses specifically on optimizing heat exchange, it is most effective when integrated with other energy-saving strategies.
A holistic approach to process optimization involves combining MTA with initiatives such as:
- Waste Heat Recovery (WHR): Capturing and reusing waste heat for various purposes, such as electricity generation or district heating.
- Process Intensification: Designing more compact and efficient processes that require less energy and resources.
- Renewable Energy Integration: Incorporating renewable energy sources, such as solar or geothermal, to reduce reliance on fossil fuels.
By seamlessly integrating MTA with these complementary initiatives, industries can achieve significant reductions in energy consumption, greenhouse gas emissions, and operating costs, contributing to a more sustainable future. The synergy created through this integration amplifies the impact of each individual strategy, resulting in a truly optimized and environmentally responsible operation.
Video: Minimum Temperature Approach: The Ultimate Guide You Need!
FAQs about the Minimum Temperature Approach
Here are some frequently asked questions about the minimum temperature approach and how it can benefit your thermal management design.
What exactly is the minimum temperature approach?
The minimum temperature approach (MTA) is the smallest allowable temperature difference between two fluids exchanging heat. It's a crucial parameter in designing heat exchangers and cooling systems. A smaller MTA typically means a larger, more expensive exchanger, but it can lead to higher overall system efficiency.
Why is the minimum temperature approach important in heat exchanger design?
The MTA directly impacts the heat exchanger size, cost, and efficiency. Choosing an appropriate minimum temperature approach involves a trade-off. A lower MTA can improve energy recovery but requires a larger surface area for heat transfer, which translates to a more expensive heat exchanger. Conversely, a higher MTA lowers capital costs but can lead to increased operating expenses due to reduced energy efficiency.
How does the minimum temperature approach affect the overall system cost?
A lower minimum temperature approach leads to a more efficient system. This could reduce energy consumption, thereby lowering operating costs. However, it also means a larger, more expensive heat exchanger is required upfront. Finding the optimal minimum temperature approach requires a careful economic analysis that considers both capital and operating costs over the system's lifespan.
What factors influence the selection of the minimum temperature approach?
Several factors influence the choice of the minimum temperature approach. These include the fluid properties (specific heat, density, viscosity), flow rates, allowable pressure drops, and the cost of energy. Furthermore, economic factors like the equipment's capital cost and the value of the recovered heat also play a significant role in determining the most appropriate minimum temperature approach.