Flexural Modulus: Material Selection Guide
Flexural modulus, a critical property in material science, dictates a material's resistance to bending under load. Engineers at institutions like ASTM International rely heavily on flexural modulus data when selecting materials for diverse applications. Finite Element Analysis (FEA) software uses flexural modulus as a key input parameter for simulating structural behavior under bending stresses. Material selection charts, often consulted by designers, compare the flexural modulus of various substances, from polymers like Polyethylene (PE) to metals like Aluminum Alloy 6061, to meet specific performance requirements.
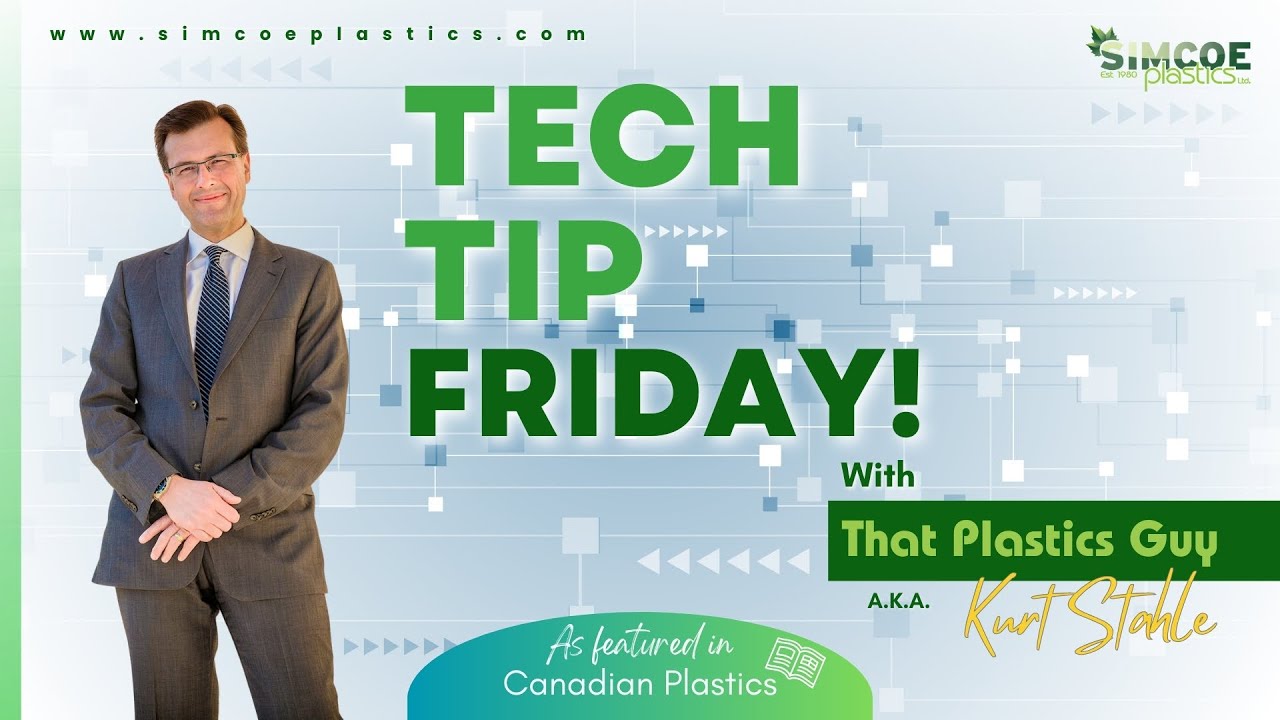
Image taken from the YouTube channel Kurt Stahle - "That Plastics Guy" , from the video titled Tech Tip Friday - What is Flexural Modulus .
Flexure, often referred to as bending, is a fundamental concept in engineering mechanics. It describes the behavior of a structural element subjected to an external load that causes it to deform along its axis. This deformation results in internal stresses and strains within the material. Understanding flexural behavior is crucial for engineers in designing safe, reliable, and efficient structures and components.
Defining Flexure and Bending
Flexure occurs when a moment is applied to a structural member. This moment causes one part of the member to experience tensile stresses (stretching), while another part experiences compressive stresses (squeezing).
The neutral axis is the line within the member where there is neither tension nor compression. A simple example of flexure is a beam supported at both ends and subjected to a load in the middle.
The beam will bend downwards, with the top surface experiencing compression and the bottom surface experiencing tension. The amount of bending and the resulting stresses depend on the material properties, the geometry of the beam, and the magnitude and location of the applied load.
Importance in Engineering Applications
Understanding flexural behavior is paramount across numerous engineering disciplines.
In civil engineering, flexural analysis is essential for designing bridges, buildings, and other infrastructure to withstand various loads, including their own weight, traffic, and environmental factors.
Aerospace engineers rely on flexural analysis to design aircraft wings and fuselages that can withstand aerodynamic forces during flight.
In mechanical engineering, flexural analysis is used to design machine components such as shafts, beams, and frames that can withstand operating loads without failure.
Automotive engineers employ flexural analysis in the design of car chassis and body panels to ensure structural integrity and passenger safety during collisions and normal use.
Factors Influencing Flexural Performance
Several factors influence a material's flexural performance.
Material properties play a critical role, with Young's modulus (E) being a key indicator of stiffness. A higher Young's modulus indicates a stiffer material that will deflect less under a given load.
The geometry of the structural element is also crucial. The second moment of area (I), also known as the area moment of inertia, quantifies a shape's resistance to bending. A larger second moment of area indicates a greater resistance to bending.
Loading conditions also significantly impact flexural behavior. The magnitude, type (e.g., concentrated, distributed), and location of the applied load will determine the resulting stresses, strains, and deflections in the structure. Proper understanding and consideration of these factors is therefore essential for accurate design and analysis.
Key Material Properties Affecting Flexure
Flexure, often referred to as bending, is a fundamental concept in engineering mechanics. It describes the behavior of a structural element subjected to an external load that causes it to deform along its axis. This deformation results in internal stresses and strains within the material. Understanding flexural behavior is crucial for engineers in designing safe and reliable structures. Material properties play a vital role in determining how a component responds to bending forces.
This section explores the crucial material properties that govern a material's behavior under flexural loading. These properties are essential for predicting and controlling bending performance.
Elasticity and Elastic Deformation
Elasticity is the ability of a material to return to its original shape after the removal of an applied load. This is crucial in flexure, as many structural components are designed to operate within their elastic range to avoid permanent deformation.
Elastic deformation is the temporary change in shape that occurs when a stress is applied. The extent of elastic deformation dictates the degree of bending a material can withstand before permanent changes occur.
Young's Modulus (E): A Measure of Stiffness
Young's Modulus (E), also known as the modulus of elasticity, is a fundamental material property that quantifies its stiffness or resistance to elastic deformation under tensile or compressive stress. In the context of flexure, a higher Young's Modulus indicates a stiffer material that will exhibit less deflection under a given bending load.
Typical values for common materials include:
- Steel: ~200 GPa
- Aluminum: ~70 GPa
- Concrete: ~30 GPa
- Wood: Varies greatly with species and grain direction, typically 10-15 GPa
Hooke's Law and Linear Elasticity
Hooke's Law describes the linear relationship between stress and strain within the elastic limit of a material. It states that stress is directly proportional to strain, with Young's Modulus (E) as the constant of proportionality (σ = Eε). This relationship is fundamental to flexural analysis as it allows us to predict the stress and strain distribution within a bending element, provided the material remains within its elastic range.
Defining the Elastic Limit
The elastic limit is the maximum stress a material can withstand before permanent deformation occurs. Beyond this point, the material will no longer return to its original shape upon unloading.
In flexural design, it's essential to ensure that the applied stresses remain below the elastic limit to prevent permanent bending or failure.
Interpreting the Stress-Strain Curve
The stress-strain curve provides a comprehensive overview of a material's mechanical behavior under loading.
For flexural analysis, key points on the curve include:
- Yield Strength: The stress at which the material begins to exhibit permanent deformation.
- Tensile Strength: The maximum stress the material can withstand before failure.
- Fracture Point: The point at which the material breaks.
Analyzing the stress-strain curve helps engineers understand a material's ductility, brittleness, and overall suitability for flexural applications.
Material Stiffness and Deflection
Material stiffness, directly related to Young's Modulus, significantly impacts the amount of deflection a structural element experiences under a given load.
A stiffer material (higher E) will exhibit less deflection compared to a more flexible material (lower E) under the same load and geometric conditions.
Isotropy vs. Anisotropy: Directional Dependence
Isotropic materials exhibit uniform properties in all directions. Examples include steel and aluminum. Anisotropic materials, on the other hand, possess properties that vary with direction. Wood and fiber-reinforced composites are examples of anisotropic materials.
Understanding a material's isotropy or anisotropy is crucial in flexural analysis, as it affects how stresses and strains are distributed within the element.
Yield Strength: Onset of Permanent Deformation
The yield strength is the stress level at which a material begins to deform permanently. In flexural applications, exceeding the yield strength can lead to undesirable bending and structural instability.
Tensile Strength: Resistance to Pulling Forces
Tensile strength is the maximum tensile stress a material can withstand before it starts to fracture or break. In bending, the convex (outer) surface of the beam experiences tensile stress. A material with high tensile strength is crucial for resisting cracking or failure on this surface.
Compressive Strength: Resistance to Squeezing Forces
Compressive strength is the capacity of a material to withstand axially directed pushing forces. When a beam is subjected to flexure, the concave (inner) surface experiences compressive stresses. Therefore, the compressive strength of the material is vital in preventing crushing or buckling on this surface.
Poisson's Ratio: Lateral Strain Effects
Poisson's Ratio (ν) describes the ratio of lateral strain to axial strain in a material subjected to stress. In bending, Poisson's Ratio influences the change in cross-sectional shape. When a beam bends, it not only deflects downwards but also undergoes a slight change in width due to this phenomenon.
Second Moment of Area (Area Moment of Inertia): Resisting Bending
The Second Moment of Area (I), also known as the Area Moment of Inertia, quantifies a shape's resistance to bending. It depends on the cross-sectional geometry of the structural element.
A larger Second Moment of Area indicates a greater resistance to bending.
For example:
- A beam with a rectangular cross-section has a Second Moment of Area of (bh3)/12, where b is the width and h is the height.
- Increasing the height (h) has a much more significant impact on the Second Moment of Area and bending resistance than increasing the width (b).
Engineers strategically choose cross-sectional shapes to optimize the Second Moment of Area and enhance bending performance.
Materials Commonly Subjected to Flexural Loads
Having established the fundamental material properties that govern flexural behavior, it is crucial to examine the materials that are most frequently employed in scenarios where bending is a primary concern. Understanding why certain materials are chosen over others for flexural applications requires a nuanced consideration of their inherent properties and performance characteristics. This section will explore the suitability of polymers, metals, and composites in resisting flexural loads, focusing on their unique attributes and common uses.
Polymers/Plastics
Polymers, also known as plastics, constitute a broad class of materials with widely varying properties. Their versatility makes them suitable for a multitude of applications, including those involving flexural loading. The specific type of polymer dictates its performance under bending forces.
Polypropylene (PP)
Polypropylene is known for its low cost, good chemical resistance, and moderate strength. It is commonly used in applications where flexibility and resistance to degradation are important.
Examples include hinges, containers, and certain automotive components. However, its relatively low stiffness limits its use in high-load flexural applications.
Polyethylene (PE)
Polyethylene is another widely used polymer, available in several grades with different densities and properties. High-Density Polyethylene (HDPE) offers greater strength and stiffness compared to Low-Density Polyethylene (LDPE).
HDPE is often found in pipes, containers, and structural components where moderate flexural strength is required. LDPE is more flexible and used in applications such as films and flexible packaging.
Polyvinyl Chloride (PVC)
Polyvinyl Chloride is a rigid polymer known for its excellent chemical resistance and durability. It is frequently used in piping systems and construction materials.
PVC exhibits good flexural strength, making it suitable for applications where structural integrity is important. Its inherent rigidity, however, can be a limitation in applications requiring flexibility.
Polystyrene (PS)
Polystyrene is a versatile polymer available in both general-purpose (GPPS) and high-impact (HIPS) grades. GPPS is brittle and has limited flexural strength.
HIPS, on the other hand, incorporates rubber additives to improve its impact resistance. Polystyrene is often used in disposable products and packaging.
Acrylonitrile Butadiene Styrene (ABS)
Acrylonitrile Butadiene Styrene is a thermoplastic polymer known for its toughness and impact resistance. It offers a good balance of properties, including moderate flexural strength.
ABS is commonly used in automotive components, consumer electronics, and protective housings. Its ability to withstand bending stresses makes it suitable for applications requiring durability.
Polycarbonate (PC)
Polycarbonate is characterized by its high impact strength and optical clarity. It exhibits good flexural strength and stiffness, making it suitable for demanding applications.
PC is often used in safety eyewear, automotive lenses, and electronic enclosures. Its ability to resist deformation under bending forces is essential in these applications.
Polyamide (Nylon)
Polyamides, commonly known as nylons, are a family of polymers with high strength, wear resistance, and good chemical resistance. They exhibit excellent flexural properties, making them suitable for structural applications.
Nylon is used in gears, bearings, and automotive components. Its ability to withstand repeated bending stresses makes it ideal for high-performance applications.
Polyurethane (PU)
Polyurethane is a versatile polymer that can be formulated to be either flexible or rigid. It is commonly used in foams, coatings, and elastomers.
Depending on its formulation, PU can exhibit a wide range of flexural properties. Flexible PU is used in cushioning and sealing applications, while rigid PU is used in structural components.
Thermoplastics
Thermoplastics are polymers that soften upon heating and can be repeatedly melted and reshaped. Their flexural properties vary depending on the specific polymer.
Thermoplastics are widely used in injection molding and extrusion processes. Understanding their behavior under flexural loads is critical for designing durable and reliable products.
Thermosets
Thermosets are polymers that undergo an irreversible chemical change during curing, resulting in a rigid, cross-linked structure. They typically exhibit higher strength and stiffness compared to thermoplastics.
Thermosets are commonly used in structural composites and adhesives. Their ability to maintain their shape under bending stresses makes them suitable for demanding applications.
Elastomers
Elastomers are polymers that exhibit high elasticity and can undergo large deformations. They are commonly used in seals, gaskets, and vibration dampers.
While elastomers are not typically used in structural applications, their ability to deform under bending forces is essential in certain applications. Their flexibility allows them to conform to irregular surfaces and absorb energy.
Metals
Metals are extensively utilized in flexural applications due to their high strength, stiffness, and durability. The choice of metal depends on the specific requirements of the application, including load, environment, and cost considerations.
Aluminum
Aluminum is a lightweight metal known for its good corrosion resistance. It offers moderate strength and stiffness, making it suitable for applications where weight is a concern.
Aluminum is commonly used in aerospace structures, automotive components, and construction materials. Its ability to resist bending stresses while minimizing weight is a key advantage.
Steel
Steel is a widely used metal known for its high strength and stiffness. It offers excellent flexural properties, making it suitable for structural applications.
Steel is used in bridges, buildings, and machinery. Its ability to withstand high bending loads is essential for ensuring the safety and reliability of these structures.
Titanium
Titanium is a high-performance metal characterized by its high strength-to-weight ratio and exceptional corrosion resistance. It exhibits excellent flexural properties, making it suitable for demanding applications.
Titanium is used in aerospace structures, medical implants, and high-performance sports equipment. Its ability to resist bending stresses while minimizing weight is a key advantage in these applications.
Composites
Composite materials combine two or more distinct materials to achieve properties that are superior to those of the individual components. Fiber-reinforced polymers (FRPs) are a common type of composite used in flexural applications.
Fiber-Reinforced Polymers (FRP)
Fiber-reinforced polymers consist of a polymer matrix reinforced with high-strength fibers such as carbon, glass, or aramid. The fibers provide high strength and stiffness, while the polymer matrix binds the fibers together and distributes the load.
FRPs offer several advantages over traditional materials, including high strength-to-weight ratio, corrosion resistance, and design flexibility. They are commonly used in aerospace structures, automotive components, and sporting goods.
Carbon Fiber Reinforced Polymers (CFRP)
Carbon fiber reinforced polymers utilize carbon fibers as the reinforcing material. CFRPs offer exceptional strength and stiffness, making them suitable for high-performance flexural applications.
They are used in aerospace structures, racing cars, and high-end sporting equipment. Their ability to withstand extreme bending stresses while minimizing weight is a key advantage.
Glass Fiber Reinforced Polymers (GFRP)
Glass fiber reinforced polymers utilize glass fibers as the reinforcing material. GFRPs offer a good balance of properties at a lower cost compared to CFRPs.
They are used in automotive components, marine structures, and construction materials. Their ability to provide adequate flexural strength at a reasonable cost makes them a popular choice for a wide range of applications.
Standard Flexural Testing Methods
Having established the fundamental material properties that govern flexural behavior, it is crucial to examine the methods that are most frequently employed to experimentally determine the flexural properties of materials. Understanding these tests is key to validating material models and ensuring structural integrity. This section details common experimental approaches, providing insights into their principles, setups, and data analysis techniques.
Three-Point Bending Test
The three-point bending test is a widely used method for characterizing the flexural behavior of materials.
It is particularly suitable for brittle materials or when a simple and quick assessment of flexural strength is required.
Principles and Setup
In a three-point bending test, a specimen is supported at two points, and a load is applied at the midpoint between the supports. This creates a bending moment that induces tensile stress on the convex side of the specimen and compressive stress on the concave side. The test continues until the specimen fractures or reaches a predetermined deflection limit.
The test setup involves a Universal Testing Machine (UTM) equipped with a three-point bending fixture. The fixture typically consists of two support rollers and a loading nose, all of which are carefully aligned to ensure accurate and consistent loading.
Data Analysis
The data obtained from a three-point bending test includes the applied load and the corresponding deflection of the specimen. This data is used to calculate the flexural stress and strain, which are then plotted to generate a stress-strain curve.
The flexural modulus, a measure of the material's stiffness in bending, can be determined from the slope of the initial linear portion of the stress-strain curve.
The flexural strength, which represents the material's resistance to bending, is defined as the maximum stress the material can withstand before failure. This is calculated using the formula:
σ = (3FL) / (2bh2)
Where:
- σ is the flexural stress
- F is the applied force
- L is the support span
- b is the width of the specimen
- h is the thickness of the specimen
Four-Point Bending Test
The four-point bending test offers advantages over the three-point bending test, particularly for materials that exhibit non-uniform stress distribution.
Principles and Setup
In a four-point bending test, the specimen is supported at two points, similar to the three-point test. However, the load is applied at two points equidistant from the supports.
This creates a region of uniform bending moment between the loading points, which eliminates the stress concentration that occurs directly under the loading nose in the three-point test.
The setup for a four-point bending test also involves a UTM equipped with a specialized fixture. The fixture consists of two support rollers and two loading rollers, carefully aligned to ensure consistent loading.
Advantages over Three-Point Bending
The main advantage of the four-point bending test is the presence of a uniform bending moment in the central region of the specimen. This allows for a more accurate determination of the material's flexural properties, especially for materials that are sensitive to stress concentrations.
Additionally, the four-point bending test provides a larger area of constant moment, which can be beneficial when evaluating the effects of surface treatments or defects on the flexural performance of materials.
Universal Testing Machine (UTM)
The Universal Testing Machine (UTM) is the primary equipment used in both three-point and four-point bending tests. It provides controlled application of force and precise measurement of displacement.
Function and Components
The UTM is a versatile machine capable of performing a wide range of mechanical tests, including tensile, compressive, and flexural tests.
It consists of several key components:
- Load Cell: Measures the applied force.
- Crosshead: Applies the force to the specimen.
- Grips or Fixtures: Hold the specimen in place.
- Displacement Transducer: Measures the displacement of the crosshead.
- Control System: Controls the movement of the crosshead and acquires data from the load cell and displacement transducer.
During a flexural test, the specimen is placed in the appropriate bending fixture, and the crosshead is moved at a constant rate, applying a load to the specimen. The UTM continuously records the applied load and the corresponding displacement, providing the data needed to calculate the flexural properties of the material.
Strain Gauges
Strain gauges are essential tools for measuring the strain experienced by a material during flexural testing.
Working Principle
A strain gauge is a sensor whose resistance varies with applied force. It converts force, pressure, tension, etc., into a change in electrical resistance which can then be measured. When an external force is applied to a stationary object, stress and strain are the result.
Stress is defined as the object's internal resisting forces, and strain is defined as the deformation of the object.
Placement on the Specimen
In a flexural test, strain gauges are typically applied to the surface of the specimen in the region of maximum bending moment. For example, in a three-point bending test, strain gauges would be placed on the top and bottom surfaces of the specimen at the midpoint between the supports.
By measuring the strain at these locations, it is possible to determine the stress distribution within the specimen and to validate the assumptions used in the flexural analysis.
Extensometers
Extensometers are devices used for precise measurement of the change in length (extension or compression) of a material under stress.
Accuracy Comparison to Strain Gauges
While strain gauges are useful for measuring strain at specific points, extensometers offer higher accuracy and can measure strain over a larger gauge length. They are particularly valuable in determining the elastic modulus of materials, as they provide a more precise measurement of the initial linear portion of the stress-strain curve.
However, extensometers can be more cumbersome to use than strain gauges, and they may not be suitable for all types of flexural tests.
Relevant Standards and Simulation Software
Having established the fundamental material properties that govern flexural behavior, it is crucial to examine the methods that are most frequently employed to experimentally determine the flexural properties of materials. Understanding these tests is key to validating material models and ensuring structural integrity. This requires adherence to established industry standards and often involves the use of sophisticated simulation software. This section provides an overview of these resources, emphasizing their role in flexural analysis and design.
The Role of Standards in Flexural Testing
Standards play a critical role in ensuring consistency and reliability in flexural testing. By adhering to recognized standards, engineers can ensure that test results are comparable across different laboratories and that materials meet specified performance criteria. These standards provide detailed procedures for specimen preparation, test setup, and data analysis, minimizing variability and promoting accuracy.
ASTM Standards for Flexural Testing
The American Society for Testing and Materials (ASTM) offers a range of standards relevant to flexural testing of materials.
ASTM D790 is a widely used standard that specifies the test methods for flexural properties of unreinforced and reinforced plastics and electrical insulating materials. It outlines procedures for both three-point and four-point bending tests. The standard covers specimen dimensions, test speeds, and calculations for flexural modulus and flexural strength.
ASTM D6272 is another important standard that describes a four-point bending test method specifically designed for determining the flexural properties of plastics and composite materials. This standard is particularly useful for materials that exhibit non-linear behavior or for specimens where a uniform stress distribution is desired over a larger portion of the sample.
ISO Standards for Flexural Testing
The International Organization for Standardization (ISO) also provides globally recognized standards for flexural testing.
ISO 178 specifies the method for determining the flexural properties of plastics. It is broadly similar to ASTM D790 but may contain slight variations in test parameters and calculation methods. Adherence to ISO 178 is crucial for ensuring compliance with international regulations and for facilitating global trade of materials and products.
Finite Element Analysis (FEA) Software for Flexural Simulation
Finite Element Analysis (FEA) software has become an indispensable tool for simulating bending behavior in engineering design. FEA allows engineers to predict how a structure will respond to flexural loads. This reduces the need for extensive physical testing and accelerates the product development cycle.
Capabilities of FEA Software
FEA software utilizes numerical methods to solve complex structural problems. It can accurately model the stress and strain distribution within a component subjected to bending. FEA can also simulate the effects of various factors, such as material properties, geometry, and loading conditions, on the flexural performance of a structure.
Popular FEA Software Packages
Several powerful FEA software packages are widely used in industry and academia. These include:
ANSYS is a comprehensive FEA software suite capable of handling a wide range of structural analysis problems, including flexural analysis.
Abaqus is another popular FEA package. It is known for its advanced material modeling capabilities.
COMSOL Multiphysics is a versatile simulation platform that can be used for both structural and multiphysics analysis.
SolidWorks Simulation is an integrated FEA tool that is easy to use and well-suited for design engineers.
By integrating standards compliance and FEA simulations into the design process, engineers can ensure the structural integrity and reliability of products subjected to flexural loads. This approach not only enhances product performance but also minimizes the risks associated with structural failure.
Real-World Applications of Flexural Analysis
Having established the fundamental material properties that govern flexural behavior, it is crucial to examine the methods that are most frequently employed to experimentally determine the flexural properties of materials. Understanding these tests is key to validating material models and ensuring structural integrity. The application of these principles extends across diverse engineering disciplines, where understanding and managing flexural behavior is paramount for creating safe, reliable, and efficient designs.
Flexural Analysis in Civil Engineering
Civil engineering relies heavily on understanding flexure, primarily in the design of beams, bridges, and various structural components. The flexural strength of these elements directly impacts the integrity and safety of structures intended for public use.
Consider a simple bridge design: the deck must withstand the bending forces induced by vehicular traffic. Engineers use flexural analysis to determine the required thickness and material properties of the deck to prevent failure under maximum load.
Similarly, in high-rise buildings, beams and columns are subjected to substantial bending moments due to gravity and wind loads. Sophisticated flexural analysis techniques, often incorporating finite element methods, are essential to ensure these components can withstand anticipated stresses without exceeding allowable deflection limits. This involves not only selecting appropriate materials, but also optimizing the geometry of structural members to enhance their resistance to bending.
Flexural Analysis in Aerospace Engineering
In aerospace engineering, the performance and safety of aircraft are intricately tied to the flexural characteristics of their structural components, particularly wings and fuselages. Aircraft wings, for example, are designed to withstand significant bending loads during flight, resulting from lift and aerodynamic forces.
Flexural analysis allows engineers to optimize the wing's shape and internal structure to minimize weight while maintaining adequate stiffness and strength. The design must account for various flight conditions, including turbulence and abrupt maneuvers, which can induce extreme bending moments.
The fuselage also experiences flexural stresses, especially during takeoff and landing, where the aircraft is subjected to high accelerations and ground reaction forces. Analyzing the flexural behavior of the fuselage helps ensure structural integrity and passenger safety under these demanding conditions. Composite materials, like carbon fiber reinforced polymers, are increasingly used in aircraft construction because of their high strength-to-weight ratio, which enhances flexural performance while reducing overall aircraft weight.
Flexural Analysis in Mechanical Engineering
Mechanical engineers frequently encounter flexural loads in the design of machine components and structural elements. Shafts, gears, and frames are prime examples where understanding flexural behavior is critical.
A rotating shaft, for instance, experiences bending due to its own weight and the forces transmitted by connected components. Flexural analysis is employed to determine the shaft's diameter and material properties to prevent excessive deflection or fatigue failure.
Similarly, gears are subjected to bending stresses at the point of contact between teeth. Engineers use flexural analysis to optimize gear tooth geometry and material selection, ensuring the gear can transmit torque without tooth breakage or excessive wear.
Frames, which provide structural support for machinery, also experience bending moments due to applied loads. Flexural analysis aids in designing frame members with sufficient stiffness and strength to maintain machine alignment and prevent structural instability.
Flexural Analysis in Automotive Engineering
In automotive engineering, flexural analysis plays a crucial role in designing car body panels and chassis components that provide both structural integrity and occupant safety. Car body panels, such as doors, hoods, and roofs, are subjected to bending loads during normal use and, more importantly, during collisions.
Flexural analysis helps engineers optimize the panel's shape and material thickness to absorb impact energy and protect occupants in the event of a crash. The chassis, which serves as the vehicle's structural backbone, also experiences significant bending stresses due to road irregularities and dynamic loads.
Flexural analysis ensures the chassis can withstand these stresses without undergoing permanent deformation or failure. Advanced materials, such as high-strength steels and aluminum alloys, are often used in automotive construction to enhance flexural performance while minimizing vehicle weight, improving fuel efficiency and handling. By carefully analyzing flexural behavior, automotive engineers can design safer and more efficient vehicles.
Material Selection Software for Flexural Applications
Having established the fundamental material properties that govern flexural behavior and standard flexural testing methods, this section explores how material selection software can be effectively utilized for choosing the optimal materials in flexural applications. The features and benefits of such software are discussed, along with a curated list of relevant software packages available to engineers and designers.
Streamlining Material Selection with Dedicated Software
Material selection is a critical aspect of engineering design, directly impacting the performance, durability, and cost-effectiveness of the final product. Traditionally, this process involved manually sifting through material datasheets, comparing properties, and considering various design constraints.
However, with the advent of sophisticated material selection software, this process has been significantly streamlined and enhanced. These software tools provide engineers with a comprehensive and efficient means of identifying materials that meet specific performance requirements, including those related to flexural behavior.
Key Features and Benefits
Material selection software offers a multitude of features that simplify the material selection process.
Comprehensive Material Databases
These tools typically incorporate vast databases containing detailed information on thousands of materials, including their mechanical, thermal, and chemical properties. This allows engineers to readily access and compare material properties relevant to flexural performance, such as Young's modulus, yield strength, and flexural strength.
Property Filtering and Screening
Material selection software enables users to define specific performance criteria and filter materials based on these requirements. This feature significantly reduces the number of potential materials to consider, saving time and effort in the selection process. For example, engineers can specify minimum values for flexural strength and stiffness to identify materials suitable for a bending application.
Performance Simulation and Analysis
Some advanced material selection software packages offer integrated simulation capabilities, allowing users to predict the flexural behavior of different materials under various loading conditions. This feature enables engineers to assess the performance of candidate materials before committing to physical prototyping, reducing development costs and time.
Environmental and Cost Considerations
Modern material selection software often incorporates environmental impact and cost data, enabling engineers to make informed decisions about sustainability and affordability. This is particularly important in today's world, where minimizing environmental footprint and optimizing costs are key considerations.
Relevant Software Packages
Several material selection software packages are available on the market, each offering unique features and capabilities.
CES Edupack
CES Edupack by Granta Design (now Ansys) is a widely used software suite in engineering education and design. It provides access to a comprehensive material database and offers tools for property charting, material selection, and eco-auditing.
Ansys Granta MI
Ansys Granta MI is a material intelligence software that helps organizations manage and utilize their materials data effectively. It offers tools for material selection, simulation, and traceability, supporting data-driven decision-making across the product lifecycle.
MatWeb
MatWeb is a free online database of material properties that provides access to information on thousands of materials. While it does not offer the advanced features of commercial software packages, it is a valuable resource for engineers and designers seeking material property data.
Total Materia
Total Materia is a comprehensive materials database that combines data from international standards, material manufacturers, and research institutions. It offers tools for material comparison, property prediction, and heat treatment simulation.
By leveraging the capabilities of material selection software, engineers can make more informed and efficient decisions regarding material choices in flexural applications, leading to improved product performance, reduced development costs, and enhanced sustainability.
Key Concepts in Flexural Analysis: Stress, Strain, and Deflection
Having established the fundamental material properties that govern flexural behavior and standard flexural testing methods, this section revisits the core principles of stress, strain, and deflection in the context of flexural analysis.
A thorough understanding of these concepts is crucial for accurately predicting a material's response to bending loads and ensuring structural integrity. This section serves as a refresher, reinforcing the theoretical foundation necessary for practical applications.
Bending Stress: Understanding Stress Distribution
Bending stress refers to the internal stresses that develop within a material when it is subjected to a bending moment. These stresses are not uniform across the cross-section of the bending element.
Instead, they vary linearly, with the maximum tensile stress occurring at the surface farthest from the neutral axis and the maximum compressive stress at the surface closest to the neutral axis.
The Neutral Axis: A Critical Reference Point
The neutral axis is an imaginary line or plane within the cross-section of a beam or bending element where the bending stress is zero. It is the point where the material transitions from tension to compression.
For symmetrical cross-sections, the neutral axis typically coincides with the centroid. However, for asymmetrical sections, its location needs to be calculated carefully.
Calculating Bending Stress
The bending stress (σ) at a point within the cross-section can be calculated using the flexure formula:
σ = (M
**y) / I
Where:
- M is the bending moment at the section.
- y is the distance from the neutral axis to the point of interest.
- I is the second moment of area (area moment of inertia) of the cross-section about the neutral axis.
This formula highlights that bending stress is directly proportional to the bending moment and the distance from the neutral axis. It is inversely proportional to the second moment of area.
Bending Strain: Quantifying Deformation
Bending strain refers to the deformation of the material under bending stress. It is the change in length per unit length of the material.
Similar to bending stress, bending strain also varies linearly across the cross-section, with the maximum tensile strain at the surface farthest from the neutral axis and the maximum compressive strain at the surface closest to the neutral axis.
Relationship Between Stress and Strain: Material Constitutive Law
The relationship between bending stress and bending strain is defined by the material's constitutive law, most commonly Hooke's Law for materials within the elastic region.
Hooke's Law states that stress is directly proportional to strain:
σ = E** ε
Where:
- σ is the bending stress.
- E is the Young's modulus (modulus of elasticity) of the material.
- ε is the bending strain.
This relationship allows us to determine the strain distribution based on the stress distribution and vice versa.
It also allows us to predict the material's behavior under bending loads as long as the stress remains within the elastic limit.
Deflection: Determining Displacement Under Load
Deflection refers to the displacement of a beam or bending element from its original position under bending load. Excessive deflection can lead to structural instability or functional problems.
Therefore, it is crucial to accurately calculate and control deflection in engineering design.
Factors Influencing Deflection
Several factors influence the amount of deflection:
- Applied load (magnitude and distribution).
- Material properties (Young's modulus).
- Beam geometry (length, cross-sectional shape, and second moment of area).
- Support conditions (fixed, simply supported, cantilever).
Common Deflection Formulas
Deflection formulas are available for various beam configurations and loading conditions. For example, the maximum deflection (δ) of a simply supported beam with a uniformly distributed load (w) is given by:
δ = (5 w L4) / (384 E I)
Where:
- w is the uniformly distributed load per unit length.
- L is the length of the beam.
- E is the Young's modulus of the material.
- I is the second moment of area of the cross-section.
Understanding and applying these formulas, as well as more complex analytical or numerical methods, is crucial for predicting and managing deflection in structural design. They enable engineers to ensure that structures meet performance criteria and safety standards.
Video: Flexural Modulus: Material Selection Guide
FAQs: Flexural Modulus Material Selection
What does a high flexural modulus indicate about a material?
A high flexural modulus indicates that a material is stiff and resistant to bending. It means the material requires a significant force to deflect or deform under bending stress. Materials with high flexural modulus are often chosen for applications where rigidity and minimal deformation are critical.
How does flexural modulus differ from tensile modulus?
Flexural modulus measures a material's resistance to bending, while tensile modulus (Young's Modulus) measures resistance to stretching or pulling. They are both moduli of elasticity but represent different types of deformation. A material can have different values for each depending on its structure.
Why is flexural modulus important for material selection?
Flexural modulus is crucial when selecting materials for applications subjected to bending forces, such as beams, supports, or housings. Choosing a material with sufficient flexural modulus ensures structural integrity and prevents excessive bending or failure under load. It helps engineers determine if a material can withstand bending stresses.
What factors influence a material's flexural modulus?
Several factors influence a material's flexural modulus, including its composition, processing method, and temperature. The type and arrangement of molecules within the material significantly impact its stiffness. Additives, manufacturing processes, and even the testing environment can also alter the measured flexural modulus.
So, the next time you're wrestling with material choices for a project needing to withstand bending, remember this guide! Understanding flexural modulus and how it relates to different materials can be a game-changer in ensuring your designs are strong, reliable, and, well, don't snap under pressure. Happy building!