Faying Surface Secrets: Master Joining Techniques!
The strength of any structure often relies on the integrity of its connections, and a critical component in achieving robust joints is understanding the faying surface. The aerospace industry, with its stringent demands for safety and reliability, heavily emphasizes proper faying surface preparation. Specifically, surface treatment is crucial for a strong joint. Bolting, welding, and riveting are often used, but surface needs to be treated to create a strong bond. It's all about the details when it comes to creating a structure to last, particularly with a good faying surface.
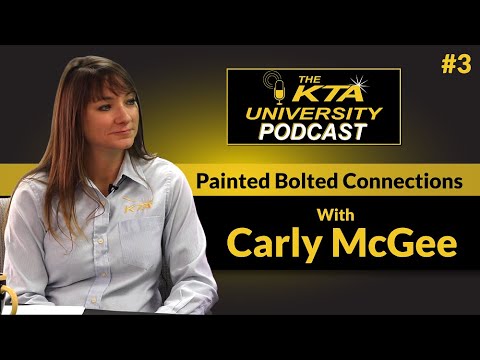
Image taken from the YouTube channel KTATator , from the video titled Podcast #3: Slip-Critical Painted Bolted Connections .
The world around us is held together, quite literally, by joints. From the complex structures of aircraft to the humble automobile and towering skyscrapers, faying surfaces play a critical, albeit often unseen, role. Understanding these surfaces and the principles governing their behavior is paramount to ensuring structural integrity, safety, and longevity across a multitude of engineering applications.
Defining the Faying Surface
A faying surface is defined as the contact area between two or more surfaces that are joined together by a fastener or adhesive. It is the interface through which load is transferred between the connected components.
The integrity of this interface directly impacts the overall strength and stability of the entire structure. In essence, the faying surface is where the action happens.
The Importance of Proper Joining Techniques
The success of any assembly that relies on faying surfaces hinges on the quality of the joining technique employed. Poorly executed joints can lead to a cascade of problems. These problems can include:
- Premature failure due to stress concentrations.
- Corrosion caused by trapped moisture.
- Reduced fatigue life due to fretting.
- Ultimately, structural collapse.
Therefore, meticulous attention to detail in the design, preparation, and execution of faying surface joints is not merely a best practice, but an absolute necessity.
Applications Across Industries
Faying surfaces are ubiquitous, finding application in virtually every industry that relies on assembled components.
Aerospace
In aerospace, where weight is a critical factor, faying surfaces are extensively used in aircraft structures. These aircraft structures include wing assemblies and fuselage sections. Here, reliable joining is non-negotiable for flight safety.
Automotive
The automotive industry relies on faying surfaces in car body construction, chassis assembly, and engine components. The reliable joining is crucial for vehicle performance and passenger safety.
Civil Engineering
From steel bridges to high-rise buildings, civil engineering relies heavily on bolted and riveted connections. Bolted and riveted connections are critical for ensuring the stability and durability of infrastructure. The cost of failure can be catastrophic, highlighting the immense importance of properly designed and executed faying surface joints.
The ubiquitous nature of faying surfaces across diverse industries underscores the critical need for robust joining techniques. But impeccable execution isn't simply about following a manual; it demands a comprehensive understanding of the principles that govern these interfaces. Therefore, let's explore the foundational design considerations that ensure effective and reliable faying surface joints.
The Foundation: Understanding Faying Surface Design Principles
The integrity of a faying surface joint is intrinsically linked to its design. A well-conceived joint not only facilitates efficient load transfer but also mitigates the risks of premature failure. Conversely, a poorly designed joint can become a point of vulnerability, undermining the structural integrity of the entire assembly.
Joint Design and Load Transfer
The primary objective of any faying surface joint is to effectively transfer loads between the connected components. The joint design dictates how this load is distributed across the faying surfaces.
Optimal design seeks to minimize stress concentrations, which are localized areas of high stress that can initiate cracks and lead to failure. Several factors influence load distribution, including:
-
Joint Geometry: The shape and dimensions of the faying surfaces significantly impact load transfer. Overlapping joints, for instance, offer greater surface area for load distribution compared to butt joints.
-
Fastener Placement: The location and spacing of fasteners (bolts, rivets, adhesives) play a crucial role in distributing the load evenly across the joint. Improper fastener placement can create stress concentrations around the fasteners.
-
Edge Distance: The distance from the edge of the component to the nearest fastener is also critical. Insufficient edge distance can lead to tear-out failure.
Finite element analysis (FEA) is a powerful tool for simulating load distribution in faying surface joints. FEA allows engineers to identify areas of high stress concentration and optimize the joint design to achieve more uniform load transfer.
Material Selection: Compatibility and Performance
The selection of appropriate materials for the faying surfaces is as crucial as the joint design itself. Material compatibility and performance characteristics directly impact the long-term reliability of the joint.
Compatibility refers to the ability of the materials to interact favorably with each other in the given environment.
-
Galvanic Corrosion: A major concern is galvanic corrosion, which occurs when dissimilar metals are in contact in the presence of an electrolyte (e.g., moisture). The more active metal corrodes preferentially, weakening the joint. Careful selection of compatible metals or the use of protective coatings can prevent galvanic corrosion.
-
Coefficient of Thermal Expansion (CTE): Differences in CTE between the joined materials can induce stress in the joint due to thermal expansion and contraction. Selecting materials with similar CTEs can minimize these stresses.
Beyond compatibility, the performance characteristics of the materials must also be considered.
-
Strength and Stiffness: The materials must possess adequate strength and stiffness to withstand the applied loads without yielding or fracturing.
-
Fatigue Resistance: For joints subjected to cyclic loading, the materials must exhibit good fatigue resistance to prevent crack initiation and propagation.
-
Corrosion Resistance: The materials must be resistant to corrosion in the intended operating environment.
Common Challenges and Failure Modes
Despite careful design and material selection, faying surface joints are susceptible to various challenges that can lead to failure. Understanding these challenges is critical for implementing preventative measures.
Load Distribution Issues:
-
Uneven Load Sharing: In multi-fastener joints, uneven load sharing can occur due to variations in fastener preload or manufacturing tolerances. This can lead to overloading of certain fasteners and premature failure.
-
Peeling Stresses: In adhesive joints, peeling stresses can occur at the edges of the joint, leading to debonding.
Potential Failure Modes:
-
Tensile Failure: This occurs when the applied tensile stress exceeds the tensile strength of the material.
-
Shear Failure: This occurs when the applied shear stress exceeds the shear strength of the material.
-
Bearing Failure: This occurs when the fasteners crush the material around the fastener holes.
-
Fatigue Failure: This occurs due to repeated cyclic loading, leading to crack initiation and propagation.
-
Corrosion Failure: This occurs when corrosion weakens the joint, reducing its strength and load-carrying capacity.
Preventative Measures:
To mitigate these challenges, several preventative measures can be implemented:
-
Proper Fastener Preload: Ensuring proper fastener preload is essential for achieving uniform load sharing in bolted joints. Torque control or direct tension indicators can be used to verify preload.
-
Surface Preparation: Proper surface preparation, including cleaning and roughening, is crucial for ensuring good adhesion in adhesive joints.
-
Protective Coatings: Applying protective coatings can prevent corrosion and extend the service life of the joint.
-
Regular Inspection: Regular inspection of the joint can help detect early signs of failure, allowing for timely repairs or replacements.
By carefully considering joint design, material selection, and potential failure modes, engineers can create robust and reliable faying surface joints that ensure the structural integrity and longevity of assembled components.
Preparation is Paramount: The Importance of Surface Treatment
Even the most meticulously designed joint, employing the highest-grade materials and fasteners, can be rendered ineffective if the faying surfaces are improperly prepared. Surface treatment is not merely a preliminary step; it is a fundamental prerequisite for achieving strong, durable, and reliable joints. Neglecting this critical stage can lead to premature failure, compromised structural integrity, and ultimately, significant financial repercussions.
Why Surface Preparation Matters
Surface preparation addresses two primary concerns: ensuring proper adhesion and preventing corrosion.
Enhancing Adhesion
Adhesion, whether achieved through mechanical interlocking or chemical bonding, is paramount in load transfer. Contaminants such as dirt, oil, grease, and loose particles act as barriers, preventing intimate contact between the faying surfaces and the joining medium (adhesive, fastener, or direct metal-to-metal contact).
These contaminants compromise the strength and integrity of the joint. Effective surface preparation removes these barriers, creating a clean and receptive surface that allows for optimal adhesion.
Preventing Corrosion
Corrosion is the insidious enemy of any metallic joint. The faying surfaces, being in close proximity and often exposed to environmental elements, are particularly susceptible.
Surface preparation removes existing corrosion products, such as oxides and hydroxides, which can accelerate further corrosion. It also creates a clean surface that allows for the application of protective coatings or treatments, providing a barrier against moisture, chemicals, and other corrosive agents.
Cleaning Techniques for Faying Surfaces
Various cleaning techniques are employed to remove contaminants and oxides, each with its strengths and limitations. The choice of method depends on the materials involved, the type and extent of contamination, and the required level of cleanliness.
Solvent Cleaning
Solvent cleaning involves using organic solvents to dissolve and remove oils, grease, and other organic contaminants. This method is effective for removing light to moderate contamination.
Common solvents include acetone, isopropyl alcohol, and mineral spirits. It is crucial to select a solvent that is compatible with the materials being cleaned and to ensure proper ventilation during use.
Chemical Cleaning
Chemical cleaning utilizes acidic or alkaline solutions to remove oxides, scale, and other inorganic contaminants. This method is more aggressive than solvent cleaning and requires careful control to avoid damaging the base materials.
Common chemical cleaning processes include pickling (using acid solutions) and etching (using alkaline solutions). Appropriate safety precautions and waste disposal procedures must be followed.
Mechanical Cleaning
Mechanical cleaning involves using abrasive methods to remove contaminants and oxides. This includes techniques such as sanding, grinding, wire brushing, and abrasive blasting.
Mechanical cleaning is effective for removing heavy contamination and creating a rough surface profile for enhanced adhesion. The choice of abrasive material and cleaning parameters must be carefully considered to avoid excessive material removal or surface damage.
Roughening Techniques for Enhanced Bonding
Creating a suitable surface profile is crucial for maximizing adhesion, particularly when using adhesives. A rough surface increases the surface area available for bonding, promoting mechanical interlocking and improving the overall joint strength.
Abrasive Blasting
Abrasive blasting, also known as sandblasting or media blasting, uses a stream of abrasive particles propelled by compressed air to roughen the surface. This technique is highly effective for creating a uniform and controlled surface profile.
The choice of abrasive media (e.g., sand, aluminum oxide, glass beads) depends on the materials being treated and the desired level of roughness.
Grit Blasting
Grit blasting is a specific type of abrasive blasting that uses coarser abrasive particles to create a more aggressive surface profile. This technique is often used for preparing surfaces for structural adhesives.
Chemical Etching
Chemical etching can also be used to roughen the surface, creating microscopic irregularities that enhance adhesion. This method is particularly useful for preparing aluminum and other non-ferrous metals for bonding.
Surface Profilometry
Surface profilometry is a critical aspect of surface preparation, regardless of which cleaning and roughening methods are used. This technique provides quantitative measurements of the surface roughness, which helps to ensure that the surface is properly prepared for bonding. Surface profilometry can also be used to detect surface defects, such as scratches and cracks, which can compromise the strength and durability of the joint.
Preparation, as we've established, lays the groundwork for success. However, the selection and implementation of the actual joining method are equally crucial. The means by which faying surfaces are brought together and held in intimate contact dictates the joint's ultimate strength, durability, and performance characteristics. Understanding the nuances of each fastening option allows engineers and technicians to make informed decisions, optimizing joint integrity for specific applications and service conditions.
Joining Forces: Exploring Fastening Methods for Faying Surfaces
The selection of a fastening method for faying surfaces is a pivotal decision in engineering design. It directly impacts the structural integrity, longevity, and overall performance of the assembled components. This section delves into a comprehensive exploration of various fastening options, analyzing their advantages, disadvantages, and suitability for different applications. We'll examine adhesives, riveting, and bolting techniques, providing a detailed understanding of their principles and practical considerations.
A Spectrum of Fastening Options: An Overview
Numerous methods exist for joining faying surfaces, each possessing unique characteristics that make it appropriate for specific scenarios. Among the most common are:
-
Adhesives: Offering uniform stress distribution and the ability to bond dissimilar materials.
-
Riveting: Providing a robust and reliable mechanical interlock, particularly suited for high-shear applications.
-
Bolting: Allowing for disassembly and reassembly, making it ideal for applications requiring maintenance or adjustments.
Each method offers a unique set of benefits and drawbacks. Careful consideration of the application's requirements is critical for selecting the optimal fastening solution.
The Allure of Adhesives: Bonding at the Molecular Level
Adhesives represent a versatile joining solution, capable of bonding a wide array of materials. Their ability to distribute stress evenly across the faying surfaces minimizes stress concentrations, a common point of failure in mechanically fastened joints. Moreover, adhesives can join dissimilar materials, overcoming the challenges associated with welding or other fusion processes.
Types of Adhesives: A Diverse Landscape
The adhesive landscape is vast, encompassing numerous formulations tailored to specific applications. Key categories include:
-
Epoxies: Known for their high strength, chemical resistance, and excellent adhesion to various substrates.
-
Acrylics: Offering rapid curing times and good impact resistance.
-
Polyurethanes: Providing flexibility and good adhesion to plastics and elastomers.
-
Cyanoacrylates (Super Glues): Used for their rapid bonding, excellent for small components but generally not recommended for structural applications.
Applying Adhesives: Precision and Control
Proper adhesive application is paramount for achieving optimal bond strength. Surface preparation, as discussed previously, is crucial for ensuring proper adhesion. The adhesive must be applied uniformly and in the correct thickness to maximize contact area and minimize voids. Curing conditions, including temperature and pressure, must also be carefully controlled to ensure proper polymerization and bond development.
Advantages and Disadvantages of Adhesives
Advantages:
-
Uniform stress distribution.
-
Ability to bond dissimilar materials.
-
Sealing capabilities.
-
Reduced weight compared to mechanical fasteners.
Disadvantages:
-
Surface preparation is critical.
-
Curing times can be lengthy.
-
Bond strength can be affected by temperature and humidity.
-
Difficult to disassemble.
Riveting: A Time-Tested Mechanical Fastener
Riveting is a traditional joining method that creates a strong mechanical interlock between faying surfaces. A rivet is a permanent mechanical fastener. Installed, it clamps the materials together securely. It excels in applications requiring high shear strength and resistance to vibration.
Strengths of Riveting
Riveting provides a reliable and durable joint. This is especially important when dealing with thin materials.
It is a relatively simple process. This requires minimal operator skill compared to welding or adhesive bonding.
Suitable Applications
Riveting is widely used in aerospace, automotive, and construction industries. It's especially suited for applications where high strength and durability are paramount, such as aircraft structures, bridges, and sheet metal assemblies.
Bolting: The Versatile and Reversible Fastener
Bolting offers a versatile and often reversible method for joining faying surfaces. Bolts and nuts create clamping force to hold materials together. This allows for disassembly and reassembly. This makes it ideal for applications requiring maintenance, adjustments, or component replacement.
Proper Clamping Force: The Key to a Secure Joint
Achieving the correct clamping force is essential for a bolted joint's integrity. Insufficient clamping force can lead to joint slippage, loosening, and eventual failure. Conversely, excessive clamping force can damage the materials or fasteners. Torque wrenches and other specialized tools are used to ensure that bolts are tightened to the specified torque, providing the optimal clamping force.
Preventing Loosening: Maintaining Joint Integrity
Bolt loosening is a common concern in bolted joints, particularly in applications subject to vibration or thermal cycling. Several methods can be employed to prevent loosening, including:
-
Lock washers: These provide spring force to maintain tension on the bolt.
-
Lock nuts: These incorporate a locking mechanism to prevent them from backing off.
-
Thread-locking adhesives: These fill the threads with adhesive. This prevents loosening due to vibration.
Careful selection of appropriate locking mechanisms and regular inspection are crucial for maintaining the integrity of bolted joints.
By understanding the principles and practical considerations of each fastening method, engineers and technicians can make informed decisions, optimizing joint integrity for specific applications and service conditions. The right choice, combined with meticulous surface preparation and proper installation techniques, is the foundation for creating strong, durable, and reliable faying surface joints.
Preparation, as we've established, lays the groundwork for success. However, the selection and implementation of the actual joining method are equally crucial. The means by which faying surfaces are brought together and held in intimate contact dictates the joint's ultimate strength, durability, and performance characteristics. Understanding the nuances of each fastening option allows engineers and technicians to make informed decisions, optimizing joint integrity for specific applications and service conditions.
Battling the Elements: Combating Corrosion in Faying Surfaces
Even the most meticulously designed and executed faying surface joint is vulnerable to the insidious threat of corrosion. This electrochemical degradation process can compromise structural integrity, diminish performance, and ultimately lead to catastrophic failure. Understanding the mechanisms of corrosion and implementing effective preventative strategies are, therefore, paramount.
The Corrosive Threat: Understanding the Enemy
Corrosion, at its core, is the deterioration of a material – typically a metal – through chemical reactions with its environment. This often involves oxidation, where the metal loses electrons to oxygen or other oxidizing agents.
In the context of faying surfaces, the confined space between the joined materials creates a unique microenvironment. This environment can trap moisture, contaminants, and corrosive agents. These trapped substances can then initiate and accelerate the corrosion process.
Mechanisms of Corrosion in Faying Surfaces
Several corrosion mechanisms are particularly relevant to faying surfaces:
-
Galvanic Corrosion: This occurs when two dissimilar metals are in contact in the presence of an electrolyte (e.g., moisture containing salts). The more active metal corrodes preferentially, sacrificing itself to protect the more noble metal.
-
Crevice Corrosion: This localized form of corrosion occurs within narrow crevices and shielded areas, such as those found between faying surfaces. The restricted access hinders oxygen diffusion, creating an electrochemical cell that promotes corrosion.
-
Filiform Corrosion: This type of corrosion manifests as thread-like filaments beneath a coating. Moisture and corrosive agents penetrate the coating, leading to the formation of these corrosive strands, which undermine the coating's protective ability.
The Devastating Effects of Corrosion
The consequences of corrosion in faying surface joints can be severe:
-
Reduced Structural Integrity: Corrosion weakens the joint by reducing the cross-sectional area of the metal components. This diminished area compromises its ability to withstand applied loads.
-
Joint Loosening: Corrosion products (e.g., rust) can expand and create pressure within the joint. This pressure can lead to loosening of fasteners and loss of clamping force, further weakening the joint.
-
Fatigue Failure: Corrosion can create stress concentrations that accelerate fatigue crack initiation and propagation, leading to premature failure of the joint under cyclic loading.
Surface Treatments: Fortifying Against Corrosion
Fortunately, a range of surface treatments can effectively mitigate the risk of corrosion in faying surfaces:
-
Protective Coatings: Coatings act as a barrier, preventing corrosive agents from reaching the metal surface. Common options include:
- Paints and Powder Coatings: These provide a physical barrier and can be formulated with corrosion inhibitors.
- Galvanizing: Applying a zinc coating provides sacrificial protection, as zinc corrodes preferentially to the base metal.
- Anodizing: This electrochemical process creates a protective oxide layer on aluminum surfaces.
- Conversion Coatings: These coatings, such as chromate conversion coatings, react with the metal surface to form a protective layer.
-
Corrosion Inhibitors: These chemical substances are added to coatings or adhesives to slow down the corrosion process. They work by interfering with the electrochemical reactions that drive corrosion.
-
Proper Material Selection: Choosing corrosion-resistant materials, such as stainless steel or aluminum alloys, can significantly reduce the risk of corrosion.
Mitigating Environmental Factors
Controlling the environment surrounding the faying surface is crucial for preventing corrosion:
-
Sealing: Applying sealants to the joint can prevent moisture and contaminants from entering the faying surface.
-
Drainage: Designing joints with adequate drainage allows water to escape, preventing it from accumulating and promoting corrosion.
-
Ventilation: Providing ventilation can reduce humidity levels within the joint, minimizing the risk of corrosion.
Best Practices: A Proactive Approach to Corrosion Prevention
Preventing corrosion in faying surfaces requires a proactive and multi-faceted approach:
-
Thorough Surface Preparation: Properly cleaning and preparing the faying surfaces ensures good adhesion of coatings and sealants.
-
Careful Material Selection: Choose materials that are compatible and resistant to the anticipated service environment.
-
Appropriate Surface Treatments: Apply appropriate protective coatings or corrosion inhibitors to provide a barrier against corrosion.
-
Regular Inspection and Maintenance: Periodically inspect joints for signs of corrosion and perform maintenance as needed.
By understanding the mechanisms of corrosion and implementing effective preventative measures, engineers and technicians can ensure the long-term reliability and performance of faying surface joints, even in harsh environments. Ignoring the risk of corrosion is not an option; a proactive approach is essential to safeguarding the integrity of assembled structures.