Ethyl Methyl Carbonate: Uses, Safety, Guide
Ethyl methyl carbonate (EMC), a versatile aliphatic carbonate, is garnering attention across various sectors due to its unique properties and applications. As an environmentally conscious alternative, ethyl methyl carbonate serves as a key component in lithium-ion batteries, enhancing electrolyte conductivity and overall battery performance. Regulatory bodies, such as the Environmental Protection Agency (EPA), closely monitor the production and use of ethyl methyl carbonate to ensure compliance with safety and environmental standards. Its chemical structure, C4H8O3, dictates its solvent properties, making it suitable for use in organic synthesis and as a solvent in industrial processes.
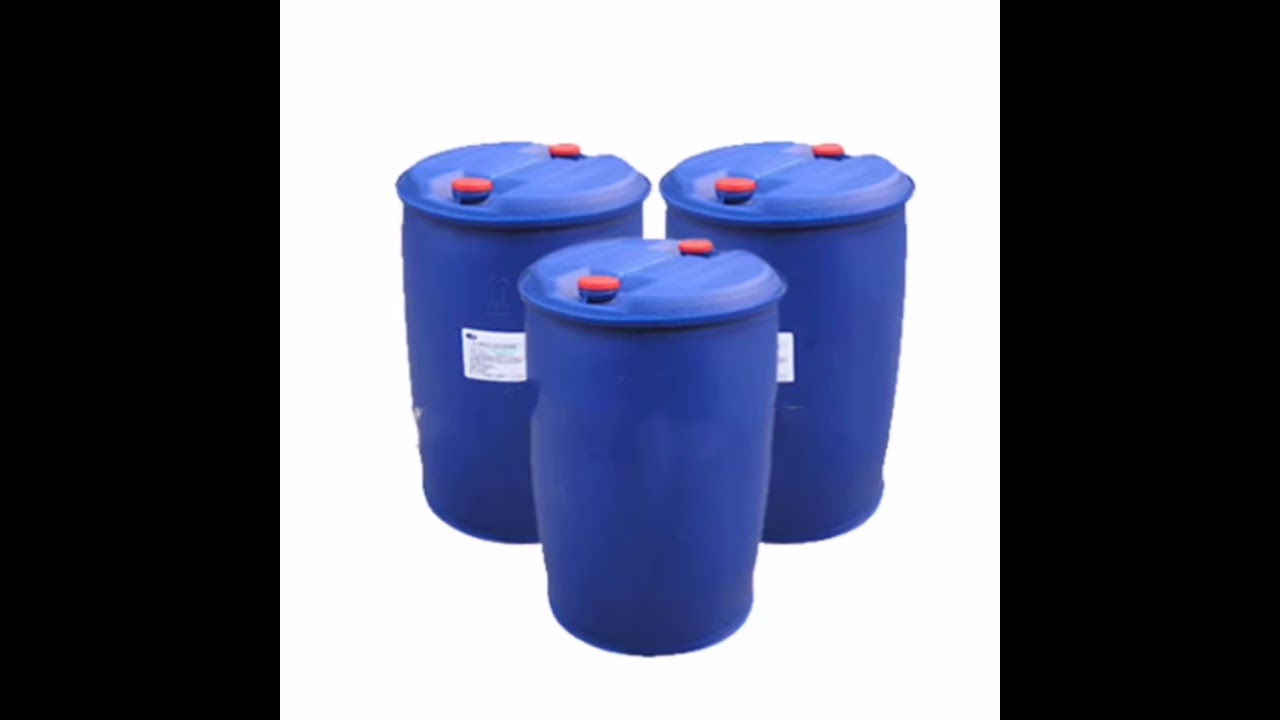
Image taken from the YouTube channel Dong Ke , from the video titled Ethyl Methyl Carbonate(EMC) Diethyl Carbonate(DEC) Dimethyl Carbonate .
Ethyl Methyl Carbonate (EMC) is an organic compound of significant industrial importance, primarily recognized for its pivotal role in modern battery technology.
Its unique chemical structure and physicochemical properties render it indispensable in a variety of applications, particularly in the optimization of lithium-ion battery performance.
Defining Ethyl Methyl Carbonate
EMC is a dialkyl carbonate, meaning it features a carbonyl group flanked by two alkoxy groups. This structure endows it with specific characteristics crucial for its applications.
The chemical formula of Ethyl Methyl Carbonate is C4H8O3, which can also be represented structurally as CH3OC(O)OCH2CH3.
For unambiguous identification, the Chemical Abstracts Service (CAS) registry number for EMC is 623-53-0. This number serves as a unique identifier in chemical databases and literature.
Significance and Diverse Applications
EMC's primary significance stems from its application in lithium-ion batteries, where it functions as a co-solvent in electrolyte formulations.
However, its utility extends beyond battery technology.
EMC finds applications as a solvent in organic synthesis, as a chemical intermediate, and in various specialty chemical applications.
Role in Lithium-ion Batteries
The increasing demand for high-performance energy storage solutions has amplified the importance of EMC.
In lithium-ion batteries, EMC is typically used in combination with other carbonates, such as ethylene carbonate (EC), propylene carbonate (PC), dimethyl carbonate (DMC), and diethyl carbonate (DEC).
The strategic incorporation of EMC into electrolyte formulations offers several advantages:
- Enhanced Ionic Conductivity
- Improved Low-Temperature Performance
- Optimized Electrolyte Viscosity
These improvements contribute to the overall efficiency, lifespan, and safety of lithium-ion batteries, making EMC a critical component in the advancement of battery technology for electric vehicles, portable electronics, and grid-scale energy storage.
Chemical and Physical Properties of EMC
Ethyl Methyl Carbonate (EMC) is an organic compound of significant industrial importance, primarily recognized for its pivotal role in modern battery technology. Its unique chemical structure and physicochemical properties render it indispensable in a variety of applications, particularly in the optimization of lithium-ion battery performance. Delving into these properties is crucial for understanding its effectiveness and safety considerations.
Physical Properties: Foundations of Functionality
The physical properties of EMC dictate its behavior in different environments and applications. Understanding these characteristics is essential for safe handling and optimal utilization.
Flash Point and Autoignition Temperature: Core Safety Metrics
Flash point is defined as the lowest temperature at which a liquid forms an ignitable mixture in air near the surface of the liquid. EMC's flash point is a critical safety parameter, dictating the conditions under which it can ignite and cause a fire hazard.
The autoignition temperature is the minimum temperature required to cause spontaneous ignition in air without an external ignition source. These values are paramount for assessing fire risks and implementing appropriate safety measures in storage and handling.
Vapor Pressure: Evaporation and Hazard Assessment
Vapor pressure measures the tendency of a substance to evaporate. A higher vapor pressure indicates a higher rate of evaporation, which can lead to increased concentration of the substance in the air.
This is vital for assessing potential inhalation hazards and designing proper ventilation systems in work environments where EMC is used.
Solubility: Implications for Formulation and Use
EMC’s solubility in various solvents—both polar and non-polar—determines its utility in diverse chemical processes and formulations. This property influences its compatibility with other electrolyte components in lithium-ion batteries.
Understanding its solubility allows for optimized electrolyte mixtures, improving battery performance and stability.
Viscosity: Impact on Electrolyte Performance
Viscosity, a measure of a fluid's resistance to flow, affects the ion transport within battery electrolytes. Lower viscosity generally promotes faster ion movement, which is crucial for achieving high battery performance.
EMC's viscosity is an important factor in determining the overall efficiency and power output of lithium-ion batteries.
Thermal Stability: Behavior Under Heat
The thermal stability of EMC refers to its ability to resist decomposition or degradation at elevated temperatures. In battery applications, EMC is subjected to varying thermal conditions, and its stability is essential for maintaining electrolyte integrity and battery lifespan.
Understanding its decomposition pathways helps in designing safer and more robust battery systems.
Electrochemical Stability: Crucial for Battery Performance
Electrochemical stability dictates how well EMC resists oxidation and reduction reactions during battery operation. High electrochemical stability ensures that the electrolyte remains intact during charging and discharging, preventing unwanted side reactions that can degrade battery performance.
This property is pivotal for achieving long cycle life and high efficiency in lithium-ion batteries.
Conductivity: Enabling Ion Transport
The conductivity of EMC is essential for facilitating the movement of lithium ions within the electrolyte. Higher conductivity translates to lower internal resistance in the battery, enabling faster charging and discharging rates.
Enhancing the conductivity of EMC-based electrolytes is a key focus in battery research to improve overall performance.
EMC as an Electrolyte Component in Lithium-ion Batteries
Ethyl Methyl Carbonate (EMC) is an organic compound of significant industrial importance, primarily recognized for its pivotal role in modern battery technology. Its unique chemical structure and physicochemical properties render it indispensable in a variety of applications, particularly in the optimization of lithium-ion battery performance. In this section, we will explore the multifaceted functions of EMC as an electrolyte component, focusing on its contributions to battery performance and compatibility within diverse electrochemical environments.
The Role of EMC in Electrolyte Composition
The electrolyte serves as the lifeblood of a lithium-ion battery, facilitating the movement of lithium ions between the cathode and anode during charge and discharge cycles. EMC, with its specific molecular architecture, acts as a crucial component within these electrolyte solutions. Its primary function is to act as a solvent, dissolving lithium salts and enabling ionic conductivity.
Enhancement of Battery Performance Through Specialized Electrolyte Formulations
EMC is strategically integrated into electrolyte formulations to achieve specific enhancements in battery performance metrics.
Improving Conductivity and Low-Temperature Performance
One of the key advantages of EMC is its ability to improve ionic conductivity, particularly at lower temperatures. Compared to other solvents, EMC exhibits a lower melting point and viscosity, which translates to better ion mobility even in sub-optimal operating conditions.
This characteristic is vital for applications where batteries are subjected to cold environments, such as in electric vehicles operating in winter climates.
Enhancing Safety Features
Beyond performance, EMC also plays a role in enhancing the safety features of lithium-ion batteries. Its chemical structure contributes to the formation of a stable solid electrolyte interphase (SEI) layer on the anode surface.
This layer protects the anode from further electrolyte decomposition and lithium plating, both of which can lead to reduced battery life and increased safety risks. By promoting a robust SEI layer, EMC helps to mitigate these issues.
Interactions with Lithium Salts and Polymers
The effectiveness of EMC is also contingent on its compatibility with other electrolyte components, notably lithium salts and polymer separators.
Compatibility with Lithium Salts
EMC exhibits excellent miscibility with common lithium salts such as LiPF6 and LiBF4, ensuring their proper dissolution and ionization within the electrolyte. The resulting ionic conductivity is directly proportional to the salt concentration and the solvent's ability to effectively solvate the lithium ions.
Compatibility with Battery Separators
EMC is also compatible with a range of polymer separators commonly used in lithium-ion batteries, such as polyethylene (PE) and polypropylene (PP). The solvent should not degrade or dissolve the separator material, maintaining its structural integrity and preventing short circuits.
Comparison with Other Battery Electrolytes
EMC is often used in combination with other solvents to fine-tune the properties of the electrolyte. A comparative analysis with other common solvents provides insights into its strengths and limitations.
Ethylene Carbonate (EC)
EC is known for its high dielectric constant, which promotes better lithium salt dissociation. However, it has a high melting point, limiting its low-temperature performance. EMC is often added to EC-based electrolytes to improve low-temperature operation.
Dimethyl Carbonate (DMC)
DMC has a low viscosity and improves conductivity, but its high volatility can pose safety concerns. EMC offers a balance between conductivity and safety compared to DMC.
Diethyl Carbonate (DEC)
DEC shares similar properties with EMC but may not perform as well in forming a stable SEI layer. EMC can be preferred when SEI formation is critical.
Propylene Carbonate (PC)
PC can cause graphite exfoliation in some battery designs. EMC is a safer alternative in these scenarios, as it does not have the same exfoliation issues.
In summary, EMC's unique blend of properties makes it an invaluable component in lithium-ion battery electrolytes. Its contribution to conductivity, low-temperature performance, and safety features makes it a key enabler for high-performance and reliable battery systems. While other solvents offer certain advantages, EMC provides a balanced profile that is essential for meeting the demands of modern battery applications.
Regulatory and Safety Information for Ethyl Methyl Carbonate (EMC)
Ethyl Methyl Carbonate (EMC) is an organic compound of significant industrial importance, primarily recognized for its pivotal role in modern battery technology. Its unique chemical structure and physicochemical properties render it indispensable in a variety of applications, particularly in lithium-ion batteries. However, with such widespread usage, adherence to stringent regulatory and safety standards is paramount to mitigate potential risks and ensure responsible handling throughout its lifecycle.
Globally Harmonized System (GHS) Compliance
The Globally Harmonized System of Classification and Labelling of Chemicals (GHS) provides a standardized framework for classifying and communicating chemical hazards.
Adherence to GHS is essential for EMC, ensuring that all safety information, including hazard pictograms, signal words, and hazard statements, are consistently displayed on product labels and Safety Data Sheets (SDS).
This standardized approach facilitates clear communication of potential hazards to workers, consumers, and emergency responders, regardless of geographical location or industry.
The Indispensable Role of Safety Data Sheets (SDS)
The Safety Data Sheet (SDS) is a comprehensive document that provides detailed information about the properties, hazards, and safe handling procedures for a chemical substance.
For EMC, the SDS serves as a critical resource for outlining potential health effects, flammability risks, reactivity hazards, and environmental impacts.
It is imperative that all individuals involved in the handling, storage, and transportation of EMC have access to and thoroughly understand the information contained within the SDS. This includes detailed guidance on personal protective equipment (PPE), first aid measures, spill response procedures, and proper disposal methods.
NFPA 704 Hazard Ratings
The National Fire Protection Association (NFPA) 704 standard provides a visual system for quickly identifying the hazards associated with a chemical substance in the event of a fire or other emergency.
This system utilizes a diamond-shaped symbol with four colored sections: red (flammability), blue (health), yellow (reactivity), and white (specific hazard).
Each section is assigned a numerical rating from 0 to 4, with 0 indicating minimal hazard and 4 indicating severe hazard. The NFPA 704 rating for EMC should be prominently displayed on storage containers and in areas where it is handled, enabling emergency responders to quickly assess the risks and take appropriate action.
Regulatory Oversight
Several regulatory agencies play a crucial role in ensuring the safe handling and use of EMC. These agencies establish and enforce standards related to workplace safety, environmental protection, and chemical registration.
Occupational Safety and Health Administration (OSHA)
The Occupational Safety and Health Administration (OSHA) is responsible for protecting the health and safety of workers in the United States.
OSHA sets permissible exposure limits (PELs) for hazardous substances, including EMC, and enforces regulations related to workplace safety practices, such as the use of PPE, proper ventilation, and hazard communication.
Environmental Protection Agency (EPA)
The Environmental Protection Agency (EPA) is responsible for protecting human health and the environment in the United States.
The EPA regulates the production, use, and disposal of chemicals, including EMC, to prevent pollution and minimize environmental impacts. This includes setting standards for air and water quality, as well as regulations related to waste management and hazardous waste disposal.
REACH (European Union)
REACH (Registration, Evaluation, Authorisation and Restriction of Chemicals) is a European Union regulation that requires companies to register all chemical substances manufactured or imported into the EU in quantities of one ton or more per year.
REACH aims to improve the protection of human health and the environment from the risks that can be posed by chemicals. Compliance with REACH is essential for companies that manufacture, import, or use EMC in the EU.
Local Regulatory Agencies
In addition to national and international regulations, local regulatory agencies may also have specific requirements related to the handling and use of EMC.
These requirements may vary depending on the jurisdiction and may address issues such as air emissions, wastewater discharge, and community right-to-know. It is important to consult with local authorities to ensure compliance with all applicable regulations.
Safe Handling, Storage, and Disposal of Ethyl Methyl Carbonate (EMC)
Ethyl Methyl Carbonate (EMC) presents specific handling, storage, and disposal challenges that necessitate adherence to stringent safety protocols. Neglecting these guidelines can lead to significant safety hazards and environmental damage. This section outlines essential practices to ensure the responsible management of EMC throughout its lifecycle.
Storage and Handling Best Practices
Proper storage and handling are paramount to preventing accidents and maintaining the integrity of EMC. Specific guidelines must be followed to minimize risks associated with its chemical properties.
-
Ventilation and Temperature Control: EMC should be stored in a well-ventilated area, away from direct sunlight and sources of ignition. Maintaining a consistent temperature below 30°C (86°F) is crucial to prevent degradation and vapor buildup.
This minimizes the risk of fire and maintains the chemical's stability over time.
- Container Integrity: Use only approved, tightly sealed containers made of compatible materials such as stainless steel or certain plastics like PTFE (Teflon). Regularly inspect containers for signs of damage or leaks.
-
Inert Atmosphere: When handling large quantities or transferring EMC, consider using an inert atmosphere (e.g., nitrogen or argon) to prevent contact with moisture and air.
This reduces the likelihood of unwanted reactions and maintains purity.
- Personal Protective Equipment (PPE): Always wear appropriate PPE, including chemical-resistant gloves, safety goggles, and a lab coat, when handling EMC. In situations where vapor concentrations may be high, respiratory protection is essential.
First Aid Measures for Accidental Exposure
Despite preventative measures, accidental exposure to EMC can occur. Immediate and appropriate first aid is critical to minimize potential health effects.
- Inhalation: If inhaled, move the affected individual to fresh air immediately. Provide oxygen if breathing is difficult. Seek medical attention promptly.
- Skin Contact: Immediately flush the affected area with copious amounts of water for at least 15 minutes. Remove contaminated clothing and shoes. Seek medical attention if irritation persists.
- Eye Contact: Immediately flush the eyes with a gentle, steady stream of water for at least 20 minutes, holding the eyelids open to ensure thorough rinsing. Seek immediate medical attention.
- Ingestion: Do not induce vomiting. Rinse the mouth with water and seek immediate medical attention. Provide the SDS to medical personnel.
Proper Waste Disposal Methods
Improper disposal of EMC and EMC-containing waste can pose serious environmental risks. Strict adherence to regulatory guidelines and best practices is essential.
- Hazardous Waste Classification: EMC is typically classified as a hazardous waste due to its flammability and potential toxicity. Dispose of it in accordance with local, regional, and national regulations.
- Incineration: Incineration in a licensed hazardous waste incinerator is the preferred method for disposing of EMC. Ensure the incinerator is equipped to handle volatile organic compounds (VOCs) and prevent the release of harmful emissions.
-
Chemical Treatment: Certain chemical treatment methods may be suitable for neutralizing or detoxifying EMC prior to disposal. Consult with a qualified environmental waste management specialist to determine the appropriate method.
Always verify compliance with all applicable regulations.
- Prohibition of Drain Disposal: Never dispose of EMC down drains or into the environment. Such actions can contaminate water sources and ecosystems, leading to severe environmental consequences.
Recycling Lithium-ion Batteries and EMC Recovery
Given the increasing prevalence of lithium-ion batteries and the environmental impact of their disposal, recycling and material recovery are becoming increasingly important. The recovery of EMC from spent batteries offers both economic and environmental benefits.
- Battery Recycling Infrastructure: Support and promote the development of robust lithium-ion battery recycling infrastructure. This includes collection programs, dismantling facilities, and material recovery processes.
-
EMC Recovery Techniques: Invest in research and development of efficient and cost-effective technologies for recovering EMC from spent lithium-ion batteries. Techniques such as solvent extraction, distillation, and supercritical fluid extraction show promise.
These processes contribute to resource conservation.
- Closed-Loop Systems: Encourage the establishment of closed-loop systems where recovered EMC can be purified and reused in new battery manufacturing. This reduces the reliance on virgin materials and minimizes waste.
- Life Cycle Assessment: Conduct comprehensive life cycle assessments (LCAs) to evaluate the environmental benefits of EMC recovery and recycling. These assessments should consider energy consumption, emissions, and resource utilization.
Potential Hazards and Mitigation Strategies for Ethyl Methyl Carbonate (EMC)
Ethyl Methyl Carbonate (EMC), while valuable in lithium-ion battery technology and other applications, is not without its inherent hazards. A thorough understanding of these risks, coupled with proactive mitigation strategies, is crucial to ensure safe and responsible handling. This section examines the potential toxicity of EMC, the detrimental impact of water contamination, and the formation of carbon dioxide as a degradation product, providing actionable strategies to minimize these risks.
Toxicity Considerations
While EMC is generally considered to have low acute toxicity, its potential for chronic effects and environmental impact necessitates careful consideration. Direct exposure can cause skin and eye irritation, and prolonged or repeated exposure may lead to more severe health concerns.
It is imperative to consult the Safety Data Sheet (SDS) for detailed toxicological information and to implement appropriate personal protective equipment (PPE) during handling.
Environmental Impact
The environmental fate of EMC is a critical consideration. While data on its biodegradability are limited, its potential persistence in the environment and its impact on aquatic ecosystems warrant careful management.
Spills should be contained and cleaned up promptly using appropriate methods, and waste disposal must adhere to strict regulatory guidelines to prevent environmental contamination.
Impact of Water Contamination
The presence of water in EMC can have a significant detrimental impact on its performance and stability, particularly in lithium-ion battery applications.
Even trace amounts of water can react with the lithium salts in the electrolyte, leading to the formation of unwanted byproducts such as hydrofluoric acid (HF) in LiPF6-based electrolytes.
Effects on Electrolyte Performance
Water contamination drastically reduces the ionic conductivity of the electrolyte, hindering battery performance and lifespan.
The formation of HF can also corrode the battery's internal components, further accelerating degradation.
Mitigation Strategies
Preventing water contamination requires meticulous handling and storage procedures. EMC should be stored in airtight containers under dry conditions, and exposure to humid environments should be minimized.
Regular quality control testing should be performed to monitor water content, and desiccants such as molecular sieves can be used to remove any residual water.
Carbon Dioxide (CO2) Formation
The degradation of EMC can lead to the formation of carbon dioxide (CO2), particularly under elevated temperatures or electrochemical stress.
CO2 formation can increase the internal pressure of battery cells, leading to swelling and potentially compromising safety.
Degradation Pathways
The precise degradation pathways leading to CO2 formation are complex and can vary depending on the specific electrolyte composition and operating conditions. However, electrochemical oxidation and thermal decomposition are key contributors.
Minimizing CO2 Formation
Strategies to minimize CO2 formation include:
- Using high-purity EMC: Minimizing impurities that can catalyze degradation reactions.
- Adding Stabilizers: Incorporating electrolyte additives that can scavenge free radicals or stabilize the EMC molecule.
- Optimizing Operating Conditions: Avoiding extreme temperatures and overcharging, which can accelerate degradation.
By understanding the potential hazards associated with EMC and implementing appropriate mitigation strategies, we can ensure its safe and responsible use across various applications, particularly in the critical field of energy storage.
Applications of Ethyl Methyl Carbonate (EMC) Beyond Battery Technology
Ethyl Methyl Carbonate (EMC), while valuable in lithium-ion battery technology and other applications, is not without its inherent hazards. A thorough understanding of these risks, coupled with proactive mitigation strategies, is crucial to ensure safe and responsible handling. Beyond its significant role as a crucial component in lithium-ion battery electrolytes, EMC's solvent properties unlock a range of applications across diverse industrial sectors.
This section explores these alternative uses, emphasizing the versatility of EMC and detailing advanced applications within the context of battery technology.
EMC as a Solvent in Diverse Industries
EMC's unique solvency characteristics render it a valuable asset in various chemical processes and applications beyond the realm of battery technology. Its ability to dissolve a range of organic compounds, combined with its relatively low toxicity compared to some traditional solvents, makes it an attractive alternative in several sectors.
-
Pharmaceutical Industry: EMC can serve as a solvent in the synthesis of pharmaceutical intermediates and active pharmaceutical ingredients (APIs). Its favorable solvency profile helps ensure efficient reaction yields and product purity.
-
Cosmetics and Personal Care: The cosmetics industry utilizes EMC in the formulation of certain products where its solvency power aids in blending various ingredients. This helps improve product texture and stability.
-
Specialty Chemicals: EMC is utilized in the synthesis and processing of specialty chemicals, where its capacity to dissolve various organic compounds is essential. It facilitates complex chemical reactions and purification processes.
-
Cleaning and Coating Applications: EMC finds use in certain cleaning formulations and coatings, especially where a solvent with moderate polarity is needed. It can remove residues and improve surface finish in various applications.
Advanced Applications in Lithium-ion Batteries
Beyond its standard role as a co-solvent in electrolyte formulations, further applications of EMC within lithium-ion batteries are being explored to improve battery performance and safety.
-
SEI Layer Modification: EMC can be strategically used to modify the Solid Electrolyte Interphase (SEI) layer formed on the electrode surfaces. Optimization of this layer improves ion transport and long-term cycling stability.
-
High-Voltage Electrolytes: Research is exploring the use of EMC in high-voltage electrolytes where its electrochemical stability is critical. This allows for higher energy density battery designs.
-
Electrolyte Additives: Beyond its primary role, EMC can function as an electrolyte additive to enhance specific battery characteristics. Its integration helps fine-tune the electrolyte's performance under different operational conditions.
-
Next-Generation Battery Chemistries: EMC is being evaluated in novel battery chemistries, such as lithium-sulfur and solid-state batteries. Its solvent properties may prove crucial in these emerging technologies.
Key Stakeholders and Industry Involvement in EMC Production and Use
Ethyl Methyl Carbonate (EMC), while valuable in lithium-ion battery technology and other applications, exists within a complex ecosystem of stakeholders. A comprehensive understanding of their respective roles and involvement is critical to grasp the full picture of EMC production, use, and impact. This section identifies key players, from chemical manufacturers to emergency responders, and examines their specific contributions to the EMC lifecycle.
Battery Manufacturers: The Primary Consumers
Battery manufacturers stand as primary consumers of EMC. They incorporate it as a crucial component in electrolyte formulations. This incorporation directly influences battery performance and safety. The exact formulations and EMC ratios used are often proprietary. They are closely guarded secrets to maintain a competitive advantage.
The demands of these manufacturers drive innovation and production in the EMC market. Their choices have a cascading effect throughout the entire supply chain. Factors such as energy density, cycle life, and thermal stability push manufacturers to optimize their electrolyte compositions. This often involves a careful balance between EMC and other solvents and additives.
Electrolyte Suppliers: Formulating for Performance
Electrolyte suppliers play a vital intermediary role, often bridging the gap between chemical manufacturers and battery producers. They specialize in formulating customized electrolyte solutions. These solutions are tailored to the specific needs of diverse battery applications.
These suppliers possess expertise in optimizing electrolyte blends for conductivity, stability, and compatibility. Electrolyte suppliers perform extensive testing. This ensures that their formulations meet stringent performance and safety standards. They also work closely with battery manufacturers to fine-tune electrolyte composition. The composition needs to be optimized for specific battery chemistries and operating conditions.
Chemical Manufacturers: The Foundation of Supply
Chemical manufacturers are at the base of the EMC supply chain. They are responsible for the production and purification of EMC at an industrial scale. These companies employ sophisticated chemical processes to synthesize EMC from raw materials. The process requires precise control to ensure high purity and minimal impurities.
Maintaining a reliable supply of high-quality EMC is critical for supporting the growing demand for lithium-ion batteries. Chemical manufacturers continuously invest in process optimization and capacity expansion. The investment allows them to meet the increasing needs of the battery industry. These investments may also have a cascading impact on material science.
Researchers in Battery Technology: Driving Innovation
Researchers in battery technology are instrumental in pushing the boundaries of EMC application and performance. They investigate new electrolyte formulations. They study the impact of EMC on battery characteristics. The researchers are looking for ways to improve overall battery technology.
Their work often involves:
- Conducting fundamental studies of EMC's electrochemical behavior.
- Developing novel additives to enhance its properties.
- Exploring new battery chemistries that leverage EMC's unique characteristics.
Their findings inform both chemical manufacturers and electrolyte suppliers. The findings can lead to the development of next-generation battery technologies. The battery technology needs to be safer and more efficient.
Analytical Chemistry Laboratories: Ensuring Quality Control
Analytical chemistry laboratories provide essential quality control services throughout the EMC lifecycle. They employ sophisticated analytical techniques to characterize EMC. They need to verify the purity of the EMC and detect any trace impurities.
This rigorous testing is critical for ensuring that EMC meets the stringent specifications required for battery applications. These laboratories support both chemical manufacturers and battery producers. The laboratories provide data-driven insights that enable them to optimize their processes. The laboratory work mitigates potential risks associated with substandard materials.
Material Safety Professionals: Promoting Safe Handling
Material safety professionals play a critical role in ensuring the safe handling of EMC across its entire lifecycle. They are responsible for developing and implementing safety protocols. The safety protocols need to minimize the risks associated with EMC production, transportation, and use.
This includes:
- Developing comprehensive safety data sheets (SDS).
- Conducting risk assessments.
- Providing training to workers on safe handling procedures.
Their expertise is crucial for protecting workers, the environment, and the public from potential hazards. Material Safety Professionals often work closely with regulatory agencies. This ensures compliance with all applicable safety standards and regulations.
Electric Vehicle (EV) Manufacturers: Relying on EMC Performance
Electric vehicle (EV) manufacturers are indirect stakeholders. They rely on the performance and safety of lithium-ion batteries that incorporate EMC. The electrolyte blend influences the EV's range, charging time, and overall reliability.
The demand for high-performance EVs is driving innovation in battery technology and pushing the boundaries of what is possible with EMC-based electrolytes. EV manufacturers are increasingly focused on sourcing sustainable and ethically produced battery materials. This influences the entire EMC supply chain.
Emergency Responders: Preparing for Contingencies
Emergency responders, including firefighters and hazmat teams, represent a final critical line of defense. They respond to incidents involving EMC, such as spills or fires. Effective emergency response requires specialized knowledge of EMC's properties. They require clear protocols for handling potential hazards.
These protocols outline procedures for containment, cleanup, and mitigation of risks. Emergency responders need to be trained on the specific hazards associated with EMC. They need to understand the appropriate personal protective equipment (PPE) to use. Collaboration between chemical manufacturers, transportation companies, and emergency response agencies is essential. This collaboration ensures that responders are well-prepared to handle any incidents involving EMC safely and effectively.
Environmental Considerations of EMC Use
Key Stakeholders and Industry Involvement in EMC Production and Use Ethyl Methyl Carbonate (EMC), while valuable in lithium-ion battery technology and other applications, exists within a complex ecosystem of stakeholders. A comprehensive understanding of their respective roles and involvement is critical to grasp the full picture of EMC production, use, and, crucially, its environmental consequences.
The increasing demand for lithium-ion batteries, driven by the proliferation of electric vehicles and portable electronics, has amplified the production and use of EMC.
This heightened usage necessitates a careful examination of its environmental footprint.
Assessing the Environmental Impact of Ethyl Methyl Carbonate
Understanding the environmental impact of EMC requires considering its biodegradability, toxicity, and potential for pollution throughout its lifecycle – from production and use to disposal and potential release into the environment.
A crucial consideration is the fate of EMC once it enters environmental compartments such as water, soil, and air.
Biodegradability and Persistence
Biodegradability refers to the ability of a substance to be broken down by microorganisms into less harmful compounds.
The biodegradability of EMC is a complex issue, with studies suggesting varying degrees of degradation under different environmental conditions.
If EMC is not readily biodegradable, it can persist in the environment, potentially leading to long-term ecological effects.
The rate and extent of biodegradation are influenced by factors such as temperature, pH, the presence of suitable microorganisms, and the concentration of EMC.
Toxicity and Ecotoxicity
The toxicity of EMC to aquatic organisms, terrestrial plants, and other wildlife is an important factor in assessing its environmental risk.
Studies are needed to evaluate the potential ecotoxicological effects of EMC on various species at different trophic levels.
These studies should consider both acute and chronic exposure scenarios to provide a comprehensive understanding of the potential harm posed by EMC.
If EMC exhibits significant toxicity to key environmental species, it could disrupt ecosystems and impact biodiversity.
Potential for Pollution and Mitigation Strategies
The potential for pollution arises from leaks, spills, and improper disposal of EMC during manufacturing, transportation, and use.
Volatile organic compounds (VOCs) can contribute to air pollution and the formation of ground-level ozone.
Mitigation strategies include implementing stringent containment measures, improving waste management practices, and developing closed-loop systems to minimize EMC release into the environment.
Employing advanced wastewater treatment technologies can also reduce the concentration of EMC in industrial effluents.
Life Cycle Assessment (LCA)
A comprehensive Life Cycle Assessment (LCA) is essential to evaluate the environmental impacts associated with the entire EMC lifecycle, from raw material extraction to end-of-life management.
This assessment should consider energy consumption, greenhouse gas emissions, water usage, and waste generation at each stage.
The results of the LCA can identify areas for improvement and guide the development of more sustainable practices in the production, use, and disposal of EMC.
Video: Ethyl Methyl Carbonate: Uses, Safety, Guide
Frequently Asked Questions
What is ethyl methyl carbonate primarily used for?
Ethyl methyl carbonate (EMC) is mainly utilized as an electrolyte solvent in lithium-ion batteries. Its properties enhance battery performance, stability, and lifespan. It's also used as a solvent in organic synthesis.
Is ethyl methyl carbonate flammable?
Yes, ethyl methyl carbonate is a flammable liquid. It should be handled with appropriate precautions, including keeping it away from open flames and sources of ignition. Adequate ventilation is crucial when working with it.
What are the safety precautions for handling ethyl methyl carbonate?
When handling ethyl methyl carbonate, wear appropriate personal protective equipment (PPE) like gloves, eye protection, and a lab coat. Avoid inhalation of vapors and ensure good ventilation. Refer to the Safety Data Sheet (SDS) for detailed safety information.
How does ethyl methyl carbonate contribute to lithium-ion battery performance?
Ethyl methyl carbonate acts as a solvent to dissolve lithium salts in the electrolyte of lithium-ion batteries. It helps to improve the ionic conductivity and electrochemical stability of the battery, leading to better charging efficiency and overall performance.
So, there you have it! Ethyl methyl carbonate might sound complex, but hopefully, this guide has cleared things up. Whether you're a seasoned chemist or just curious, understanding the uses and safety precautions of ethyl methyl carbonate is key. Now you're armed with the knowledge to navigate the world of EMC a little more confidently.