Bell Cranks: Types, Use & Care for Top Performance
Bell cranks, pivotal mechanical linkages, are indispensable components in systems demanding directional changes in force or motion, such as those frequently encountered in automotive steering systems and aircraft control surfaces. Manufacturers like Thomson Industries produce an array of bell cranks, each designed to meet specific operational demands across diverse applications. Engineers frequently consult Finite Element Analysis (FEA) during the design phase to optimize the performance and longevity of bell crank systems. Precision maintenance, incorporating specialized tools like torque wrenches, is crucial for ensuring the continued optimal performance of bell cranks within these critical systems.
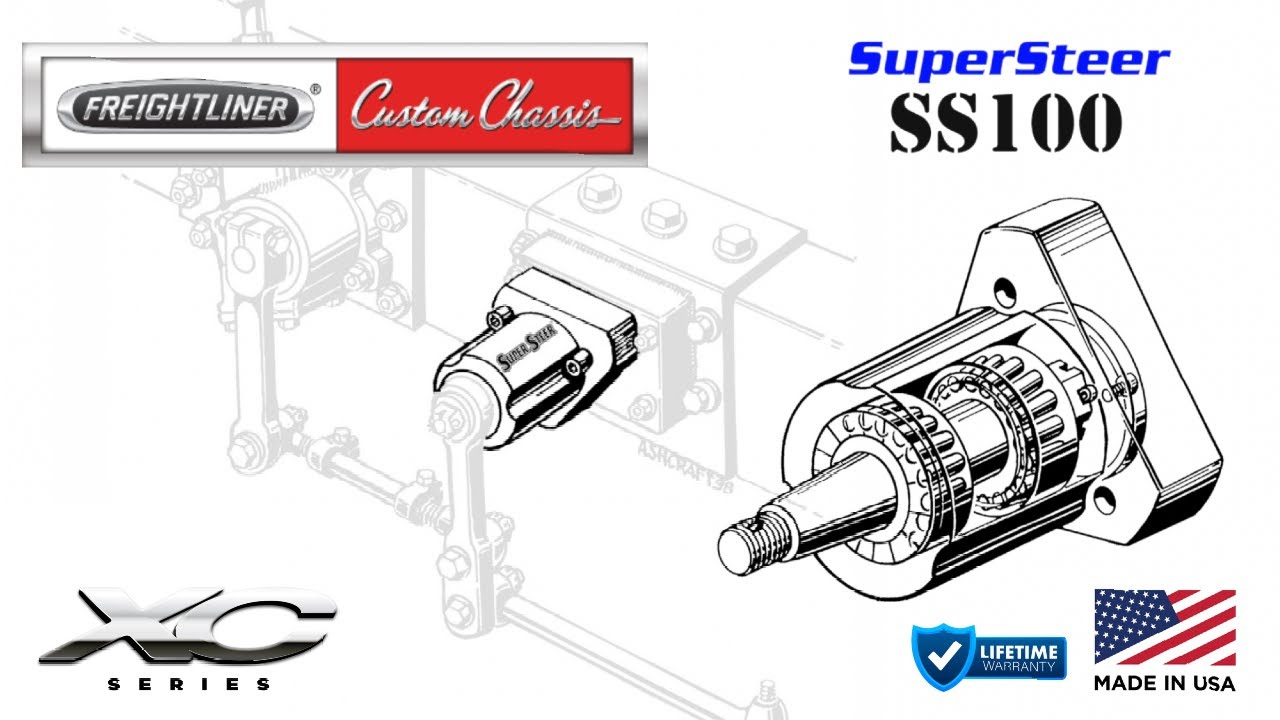
Image taken from the YouTube channel SuperSteer , from the video titled Upgrade Your RV's Steering: SuperSteer® SS100 Bell Crank Explained by Tommy Henderson .
Bell crank mechanisms represent a cornerstone in mechanical engineering, serving as essential components in a vast array of systems.
Their primary function is to act as a mechanical linkage, adept at altering the direction of motion and force.
This seemingly simple capability belies a profound impact on the design and functionality of countless machines and devices.
Defining the Bell Crank
At its core, a bell crank mechanism is a pivoting lever, typically L-shaped or angled, designed to translate force and motion through an angle, often 90 degrees.
The primary function is directional change, but it also often involves manipulating the magnitude of the applied force.
This is done either by amplifying it (increasing the output force relative to the input) or reducing it (decreasing the output force relative to the input).
This makes them invaluable for applications requiring precise control and efficient force transmission.
Significance in Mechanical Systems
The ubiquity of bell cranks stems from their ability to solve fundamental mechanical challenges.
They enable designers to re-orient forces, allowing for mechanisms to operate in confined spaces or to connect disparate parts of a system.
Consider scenarios where a linear force needs to be converted into a rotational movement, or vice versa.
Bell cranks provide a simple and effective solution.
From automotive steering linkages to aircraft control surfaces, their role is often critical to the overall performance and safety of these systems.
Scope of Exploration
This article aims to provide a comprehensive overview of bell crank mechanisms, delving into the core principles that govern their operation.
We will examine different types of bell cranks, exploring their unique configurations and applications.
A critical look at material selection and manufacturing considerations will also be covered.
Finally, we will discuss essential maintenance practices to ensure the longevity and reliability of these crucial mechanical components.
Fundamental Principles of Bell Crank Operation
[ Bell crank mechanisms represent a cornerstone in mechanical engineering, serving as essential components in a vast array of systems. Their primary function is to act as a mechanical linkage, adept at altering the direction of motion and force. This seemingly simple capability belies a profound impact on the design and functionality of countless machines and applications. The following explores the principles governing their operation, including mechanical advantage, leverage, torque, and the critical role of the transmission angle.]
Mechanical Advantage in Bell Cranks
Mechanical advantage (MA) is a critical parameter in bell crank design, defining its ability to amplify force. It represents the ratio of the output force to the input force. A higher MA means the bell crank can exert a greater output force than the input force applied.
The calculation of MA in a bell crank hinges on the lengths of the input and output lever arms. Specifically, it is the ratio of the output lever arm length to the input lever arm length. MA = Output Lever Arm Length / Input Lever Arm Length. Understanding this relationship is paramount for designing bell cranks that meet specific force requirements.
Leverage: Force Multiplication and Motion Redirection
Leverage is intrinsically linked to mechanical advantage. It describes how a bell crank uses the principle of levers to multiply force or redirect motion. By applying force at a certain distance from the fulcrum (pivot point), a greater force can be exerted at a different distance on the opposite side.
This capability of force multiplication allows for the actuation of heavy loads with relatively small input forces. Motion redirection is equally important, enabling changes in the direction of movement, crucial in many mechanical systems. The interplay between force and distance is key to understanding how leverage operates within a bell crank.
Torque and Lever Arm Length
Torque, the rotational force, plays a fundamental role in bell crank operation. It’s the product of the applied force and the perpendicular distance from the fulcrum to the line of action of the force (lever arm length). Torque = Force × Lever Arm Length.
The torque generated by the input force must be balanced by the torque produced by the output force for the bell crank to be in static equilibrium. This relationship dictates the force that can be exerted at the output, given the input force and the respective lever arm lengths. Precise calculation of torque is essential for efficient and predictable performance.
The Significance of the Transmission Angle
The transmission angle, the angle between the direction of the force applied to the output link and the output link itself, significantly impacts force transfer efficiency.
Ideal Transmission Angle
An ideal transmission angle, typically close to 90 degrees, ensures maximum force transfer from the bell crank to the output link. At this angle, the majority of the force is effectively used to move the output link, minimizing energy loss due to friction or binding.
Effects of Non-Ideal Angles
Deviations from the ideal transmission angle can lead to reduced efficiency and increased stress on the mechanism. Small transmission angles result in a larger component of force acting perpendicular to the desired direction of motion. This can cause binding, increased friction, and ultimately, reduced output force. Careful consideration of the transmission angle is therefore crucial for optimal bell crank performance.
Defining Forces and the Fulcrum
Input Force: The force applied to the bell crank to initiate movement.
Output Force: The force exerted by the bell crank on another component in the system.
Fulcrum: The pivot point around which the bell crank rotates, serving as the center of rotation.
Exploring Different Types of Bell Crank Mechanisms
Bell crank mechanisms represent a cornerstone in mechanical engineering, serving as essential components in a vast array of systems.
Their primary function is to act as a mechanical linkage, adept at altering the direction of motion and force.
This seemingly simple capability belies a profound impact, making them indispensable in numerous applications. To fully appreciate the versatility of bell cranks, it is essential to examine the various types available, each tailored to specific operational requirements.
Simple Bell Cranks: The Foundation of Motion Redirection
The simple bell crank stands as the most basic configuration, characterized by its distinctive L-shape.
This design typically consists of two levers connected at a fixed pivot point, or fulcrum, usually forming a 90-degree angle, although other angles are possible depending on the specific application.
The primary function of a simple bell crank is to convert a linear input motion into a linear output motion at a different angle, most commonly redirecting force by 90 degrees.
This makes it an ideal solution for scenarios where a change in direction is paramount.
Applications range from operating valves in fluid control systems to actuating mechanical linkages in automotive braking systems.
Its straightforward design ensures reliability and ease of maintenance, making it a staple in many mechanical designs.
Compound Bell Cranks: Amplifying Complexity for Specialized Tasks
When a single bell crank cannot achieve the desired motion or force transformation, a compound bell crank becomes the solution.
This type integrates multiple bell cranks in series, connected by linkages.
This configuration enables more complex motion profiles and greater mechanical advantage.
By combining several bell cranks, engineers can achieve intricate movements that would be impossible with a single unit.
A compound bell crank might be used in robotics, where precise, multi-directional movements are necessary.
It's also useful in aircraft control systems, or any setting demanding intricate and amplified mechanical actions.
While offering enhanced capabilities, compound bell cranks also present increased complexity in design and maintenance.
Offset Bell Cranks: Adapting to Non-Perpendicular Alignments
In situations where input and output axes are not perpendicular, an offset bell crank is employed.
Unlike the simple bell crank, the offset variant features input and output arms that are not aligned at a right angle.
This design is particularly useful when spatial constraints dictate a non-orthogonal arrangement.
Applications often include scenarios where the input and output forces must be applied at specific, non-perpendicular angles to avoid obstacles or to interface with existing machinery.
Offset bell cranks are frequently found in specialized machinery and custom mechanical setups, where standard configurations are unsuitable.
Rotating Bell Cranks: Enabling Continuous Motion Transformation
The rotating bell crank is designed to translate continuous rotational motion into another form of motion.
This type typically features a rotating arm that drives a connecting rod or linkage, thereby converting the rotary input into oscillating or reciprocating output.
This is used in converting rotary motion into linear motion, or vice versa.
Applications include converting the continuous rotation of an engine crankshaft into the reciprocating motion of a piston.
These are also useful in systems that require continuous or repetitive motion transformation.
The rotating bell crank is particularly advantageous in machinery where cyclic operations are fundamental to the process.
Materials and Manufacturing Considerations for Bell Cranks
Bell crank mechanisms represent a cornerstone in mechanical engineering, serving as essential components in a vast array of systems. Their primary function is to act as a mechanical linkage, adept at altering the direction of motion and force. This seemingly simple capability belies a profound impact, requiring careful consideration of materials and manufacturing processes to ensure optimal performance and longevity. The selection of appropriate materials and manufacturing techniques is paramount, directly influencing the bell crank's strength, weight, durability, and overall effectiveness in its intended application.
The Critical Role of Material Selection
The choice of material for a bell crank is not arbitrary; it is a carefully considered decision driven by the specific demands of the application. Factors such as required strength, operating temperature, environmental conditions, and weight constraints all play crucial roles in the selection process. A bell crank designed for a high-stress environment will necessitate a material with superior tensile strength and fatigue resistance, while one intended for aerospace applications may prioritize lightweight properties.
Steel: Strength and Durability Paramount
Steel alloys, renowned for their high strength and durability, are frequently employed in bell crank manufacturing. Steel's ability to withstand significant loads and resist deformation makes it an ideal choice for applications where structural integrity is paramount.
High-Stress Applications
In automotive steering linkages, heavy machinery, and industrial valve actuation systems, steel bell cranks provide the necessary robustness to endure constant stress and repetitive motion. The inherent strength of steel ensures reliable operation even under demanding conditions, making it a preferred material in safety-critical applications.
Manufacturing Processes for Steel Bell Cranks
Steel bell cranks are commonly manufactured through processes such as forging, casting, and machining. Forging, in particular, enhances the material's strength and grain structure, further increasing its durability and resistance to fatigue.
Aluminum: Lightweight and Corrosion-Resistant
Aluminum alloys offer a compelling alternative to steel, particularly in applications where weight is a critical factor. Aluminum's significantly lower density compared to steel makes it an attractive choice for aerospace, automotive, and robotics applications where minimizing weight is essential for performance and efficiency.
Weight-Sensitive Applications
In aircraft control surfaces, drone mechanisms, and high-performance vehicles, aluminum bell cranks contribute to overall weight reduction, improving fuel efficiency, maneuverability, and system responsiveness. The reduction of weight enhances the efficiency.
Corrosion Resistance
Furthermore, aluminum exhibits excellent corrosion resistance, making it suitable for applications exposed to harsh environmental conditions.
Manufacturing Aluminum Bell Cranks
Aluminum bell cranks can be manufactured through processes such as die-casting, extrusion, and machining. These methods allow for the creation of complex shapes with tight tolerances, ensuring precise fit and functionality.
Material Selection Criteria: A Holistic Approach
Selecting the optimal material for a bell crank involves a comprehensive assessment of various factors.
Strength and Stiffness
The material must possess adequate strength to withstand the applied loads without failure and sufficient stiffness to prevent excessive deformation.
Weight Considerations
In applications where weight is critical, lightweight materials such as aluminum or composite materials may be preferred.
Environmental Factors
Exposure to corrosive environments, extreme temperatures, or other harsh conditions may necessitate the use of corrosion-resistant or heat-resistant materials.
Manufacturing Feasibility
The ease of manufacturing, including machining, forming, and joining processes, can significantly impact the overall cost and lead time.
Cost-Effectiveness
The material cost and availability must be considered to ensure a cost-effective solution without compromising performance or reliability. By carefully evaluating these criteria, engineers can select the most appropriate material for a given bell crank application, ensuring optimal performance, durability, and cost-effectiveness.
Diverse Applications of Bell Crank Mechanisms Across Industries
Bell crank mechanisms represent a cornerstone in mechanical engineering, serving as essential components in a vast array of systems. Their primary function is to act as a mechanical linkage, adept at altering the direction of motion and force. This seemingly simple capability belies a profound impact across diverse industries, from automotive to aerospace, each leveraging the bell crank's unique attributes for specific applications. Let's explore these applications in greater detail, highlighting the critical roles bell crank mechanisms play in each sector.
Automotive Industry Applications
The automotive industry relies heavily on bell crank mechanisms for various functions, all critical to vehicle operation and control. These applications predominantly revolve around translating driver input into mechanical action.
Bell cranks are crucial components within steering linkages. They translate the rotational motion of the steering wheel into the linear motion required to turn the vehicle's wheels.
Throttle linkages often employ bell cranks to convert the driver's pedal input into precise control over the engine's airflow, directly affecting acceleration.
Brake linkages similarly utilize bell cranks to amplify and redirect the force applied to the brake pedal, ensuring effective deceleration.
Clutch linkages, particularly in manual transmission vehicles, frequently incorporate bell cranks to facilitate smooth engagement and disengagement of the clutch.
Aerospace Industry Applications
The aerospace sector presents a unique set of challenges, demanding high precision, reliability, and often lightweight construction. Bell crank mechanisms are invaluable in meeting these stringent requirements.
Aircraft control systems, such as those governing ailerons, elevators, and rudders, depend on bell cranks to transmit pilot commands to the control surfaces. The precision and responsiveness of these systems are paramount to flight safety.
Landing gear mechanisms often incorporate bell cranks to facilitate the complex deployment and retraction sequences. These mechanisms must operate flawlessly under demanding conditions.
Model Engineering
Bell crank mechanisms find extensive use in model engineering. They can be seen in remote controlled cars, airplanes, and boats.
In radio-controlled (RC) cars, they often translate the servo motor's rotational motion into linear steering action.
Model airplanes use them to control the ailerons, elevators, and rudders.
Similarly, RC boats may use bell cranks to control the rudder for precise maneuvering.
Linkages
Bell crank mechanisms are employed where redirection of motion is required. They can be used to translate linear motion into rotational motion, or vice versa.
Bell cranks are useful in connecting components that are at 90° to each other, where direct connections are not viable.
Valve Actuation
Bell cranks can be used to actuate and control the opening and closing of valves. The linear motion of an actuator can be translated into the rotational motion needed to operate a valve.
Bell cranks can adjust the timing and stroke of valve movements.
Robotics
The field of robotics leverages bell crank mechanisms to achieve precise and controlled movements in manipulators and other robotic mechanisms.
Bell cranks are useful in robotic arms to actuate joints that need to move in different planes. Their ability to change the direction of force makes them invaluable for designing compact and efficient robotic systems.
In robotic mechanisms, bell cranks can be used to synchronize movements or to amplify force, allowing robots to perform complex tasks with greater precision and power.
Essential Components and System Integration for Bell Cranks
Diverse Applications of Bell Crank Mechanisms Across Industries Bell crank mechanisms represent a cornerstone in mechanical engineering, serving as essential components in a vast array of systems. Their primary function is to act as a mechanical linkage, adept at altering the direction of motion and force. This seemingly simple capability belies a complex integration process, requiring careful consideration of various supporting components to ensure optimal functionality and longevity.
The successful integration of a bell crank mechanism hinges not only on its design but also on the selection and implementation of associated elements. These elements, including bearings, bushings, linkages, and fasteners, each play a crucial role in facilitating smooth operation, minimizing wear, and ensuring secure assembly within the overall mechanical system.
Bearings: Minimizing Friction and Maximizing Efficiency
Bearings are paramount in reducing friction within a bell crank mechanism, allowing for smoother and more efficient operation. The choice of bearing type is often dictated by the specific application's demands regarding load, speed, and precision.
Ball bearings, with their low rolling friction, are suitable for high-speed and high-precision applications. Roller bearings, offering a greater load-bearing capacity, are preferred in scenarios where the bell crank is subjected to substantial forces. Sleeve bearings, also known as journal bearings, provide a cost-effective solution for lower-speed applications where minimal maintenance is desired.
Bushings: A Cost-Effective Alternative
Bushings serve as a simpler and more economical alternative to bearings, particularly in low-speed or lightly loaded applications. Typically made from materials like bronze, nylon, or polymers, bushings offer self-lubricating properties, reducing the need for frequent maintenance.
However, it is crucial to recognize that bushings generally exhibit higher friction coefficients compared to bearings. Therefore, their application is best suited for systems where efficiency is not a primary concern and where the cost savings outweigh the performance trade-offs.
Linkages: Connecting the Bell Crank
Linkages, such as connecting rods and tie rods, form the critical interface between the bell crank and other components within the mechanical system. These linkages transmit force and motion from the bell crank to the desired output location.
The design and material selection for linkages are crucial to ensuring accurate and reliable performance. Factors such as length, cross-sectional area, and material stiffness must be carefully considered to minimize deflection and maintain precise motion transfer.
Fasteners: Ensuring Secure Assembly
The integrity of a bell crank mechanism relies heavily on the quality and proper application of fasteners. Bolts, nuts, screws, and rivets are commonly employed to securely connect the bell crank to its supporting structure and associated linkages.
It is imperative to select fasteners with adequate strength and corrosion resistance for the intended application environment. Furthermore, proper tightening torques must be applied to ensure that the connections remain secure under operational loads and vibrations. Regular inspection and tightening of fasteners are essential for maintaining the overall reliability of the bell crank mechanism.
Underlying Physics Principles
Bell crank mechanisms represent a cornerstone in mechanical engineering, serving as essential components in a vast array of systems. Their primary function is to act as a mechanical linkage, adept at altering the direction of forces and motion. Grasping the underlying physics is paramount to understanding how bell cranks achieve their functionality and how to optimize their design for specific applications. This section delves into the foundational principles of statics and dynamics that govern bell crank operation.
Statics: Equilibrium and Force Analysis
Statics, in the context of bell crank mechanisms, focuses on the conditions under which the system is in a state of equilibrium. Equilibrium implies that the bell crank is neither accelerating linearly nor rotating. This condition is crucial for predictable and controlled operation.
Achieving static equilibrium requires that the sum of all forces and moments acting on the bell crank is equal to zero. In simpler terms, the forces and moments must balance each other out.
Force Analysis
Force analysis involves determining the magnitude and direction of all forces acting on the bell crank. This includes input forces, output forces, reaction forces at the pivot (fulcrum), and any external forces such as gravity or friction.
Free Body Diagrams (FBDs) are indispensable tools in force analysis. An FBD isolates the bell crank and represents all external forces acting upon it as vectors. By applying the equations of static equilibrium (ΣF = 0 and ΣM = 0), we can solve for unknown forces or moments.
This process often involves resolving forces into their x and y components. Taking moments about a convenient point (typically the fulcrum) simplifies the equations and allows for easier determination of unknown variables.
Understanding Equilibrium Equations
The equations of equilibrium are the mathematical expressions of the conditions for static equilibrium.
- ΣF = 0: The vector sum of all forces acting on the bell crank must be zero.
- ΣM = 0: The sum of all moments about any point must be zero.
Solving these equations allows engineers to determine the forces required to maintain equilibrium under various loading conditions.
Dynamics: Motion and Force
While statics deals with systems at rest, dynamics explores the behavior of bell crank mechanisms in motion. This involves analyzing the relationships between forces, mass, and acceleration. Newton's Second Law of Motion (F = ma) is the cornerstone of dynamic analysis.
Analyzing Motion
Dynamic analysis considers the inertia of the bell crank and the accelerations of its various parts. The moment of inertia of the bell crank plays a significant role in determining its rotational behavior.
External forces acting on the bell crank cause it to accelerate, and the resulting motion depends on the magnitude and direction of these forces as well as the bell crank's inertial properties.
Force and Acceleration
Newton's Second Law (F = ma) directly relates the net force acting on a body to its acceleration. In the context of bell cranks, this law applies both to linear and angular motion.
For rotational motion, the equivalent equation is τ = Iα, where τ is the net torque, I is the moment of inertia, and α is the angular acceleration. These equations are crucial for predicting the dynamic response of a bell crank mechanism under varying loads and speeds.
Practical Applications of Dynamic Analysis
Dynamic analysis is essential for designing bell crank mechanisms that operate at high speeds or experience rapidly changing loads. It helps to predict the dynamic stresses within the mechanism and to ensure that it can withstand these stresses without failure.
Understanding the dynamics of a bell crank is also crucial for optimizing its performance. For instance, minimizing the moment of inertia can reduce the force required to accelerate the mechanism, leading to faster response times and improved efficiency.
Maintenance, Reliability, and Troubleshooting of Bell Crank Mechanisms
Underlying Physics Principles
Bell crank mechanisms represent a cornerstone in mechanical engineering, serving as essential components in a vast array of systems. Their primary function is to act as a mechanical linkage, adept at altering the direction of forces and motion. Grasping the underlying physics is paramount to understanding how bell cranks operate. The following section addresses maintenance, reliability, and troubleshooting to ensure the longevity and effectiveness of bell crank mechanisms.
The Imperative of Lubrication
Lubrication is not merely an ancillary process; it is fundamental to the sustained operation of bell crank mechanisms. By introducing a lubricant between moving surfaces, friction is significantly reduced, thereby minimizing wear. The selection of an appropriate lubricant is contingent upon several factors, including operating temperature, load conditions, and environmental exposure. Regular lubrication extends the lifespan of components and maintains operational efficiency.
Systematic Inspection Protocols
Inspection should be conducted methodically and regularly. This includes visually examining the bell crank for signs of wear, such as pitting, scoring, or deformation. Pay close attention to areas subject to high stress or repeated motion. Cracks, particularly around stress concentrations, are indicative of potential failure and warrant immediate attention. Additionally, verify the integrity and tightness of all fasteners.
The Significance of Proper Tightening Torques
The application of correct tightening torques is crucial. Over-tightening can lead to fastener failure or damage to the bell crank itself, while under-tightening can result in loosening and subsequent instability. Consult the manufacturer's specifications or relevant engineering standards to determine the appropriate torque values.
Use a calibrated torque wrench to ensure accurate and consistent results.
Ensuring Proper Alignment
Misalignment introduces undue stress on the bell crank and its connecting linkages. Ensure that all components are properly aligned according to the design specifications. This may involve using shims or other adjustment methods to correct any discrepancies.
Adherence to Load Limits
Every bell crank mechanism is designed to operate within specific load limits. Exceeding these limits can lead to premature failure. Understand the operational parameters of the system and implement safeguards to prevent overloading. Regular monitoring and load testing may be necessary in critical applications.
Environmental Considerations
The operating environment significantly impacts the longevity of bell crank mechanisms. Temperature fluctuations, humidity, and exposure to corrosive substances can accelerate degradation. Implement protective measures, such as coatings or enclosures, to mitigate these effects.
Maintenance Schedules: A Proactive Approach
Establishing and adhering to a rigorous maintenance schedule is vital for ensuring the long-term reliability of bell crank mechanisms. This schedule should encompass regular lubrication, inspection, and adjustment procedures. The frequency of these tasks should be tailored to the specific application and operating conditions.
Preventative Maintenance: Avoiding Failures Before They Occur
Preventative maintenance goes beyond routine tasks. It involves proactively identifying and addressing potential issues before they escalate into failures. This may include replacing worn components, upgrading outdated designs, or implementing improved lubrication systems.
Failure Analysis: Understanding the Root Cause
When a bell crank mechanism fails, it is imperative to conduct a thorough failure analysis. This involves investigating the circumstances surrounding the failure, examining the failed components, and determining the root cause. Understanding why a failure occurred is essential for preventing similar incidents in the future. This process may involve metallurgical analysis, stress testing, and finite element analysis (FEA).
Video: Bell Cranks: Types, Use & Care for Top Performance
FAQs: Bell Cranks - Types, Use & Care
What are the main types of bell cranks?
Bell cranks are generally categorized by their arm arrangement. Common types include 90-degree bell cranks, T-shaped bell cranks, and variations that address specific angular transmission needs. Each type directs force differently.
Where are bell cranks commonly used?
You'll find bell cranks in mechanical systems requiring a change in direction or a modification of force. Typical applications include linkages in automotive steering, throttle controls in engines, and various mechanical devices requiring precise movement.
What maintenance ensures bell cranks perform optimally?
Regular lubrication is critical to prevent friction and wear. Inspecting for looseness in the pivot points and damage to the arms ensures proper function. Replace worn or damaged bell cranks immediately.
How do I choose the right bell crank for my application?
Consider the load requirements, desired angle of motion change, and space constraints. Selecting a bell crank with appropriate material strength and dimensions is essential for reliable and safe operation. Also, proper kinematic calculations are vital.
So, there you have it! Everything you need to know to understand, utilize, and maintain your bell cranks for optimal performance. Whether you're tweaking a classic car or designing a complex machine, keep these tips in mind, and your bell cranks should give you years of reliable service. Now get out there and put that knowledge to good use!